Spezialschmelzofen spart Zeit und Energie mit Abwärme
Von Christine Gassel, München

Bereits seit 2003 setzt PMG Schmelzöfen von ZPF Therm ein. Die Anlagen weisen dank dicker Isolierung und spezieller Abgasführung eine hohe Energieeffizienz auf.
Erschienen in GIESSEREI 10/2012
Eine spezielle Anlagenkonstruktion mit Vorwärmkammer in der Aluminiumgießerei PMG nutzt die Abgase des Schmelzofens zum Vorwärmen der Masseln und spart damit 13 000 Euro Gaskosten pro Jahr ein.
Um rund 30 % erhöhte sich der Gaspreis 2011 im Vergleich zum Vorjahr. Für die Aluminiumindustrie, die sich inzwischen von der Krise erholt hat und wieder steigende Produktionszahlen
verzeichnet, werden die Energiekosten damit immer mehr zu einem kritischen Faktor. Der Aluminium-Druckgussspezialist Pressmetall Gunzenhausen GmbH & Co. KG (PMG), Gunzenhausen, stieg daher bereits im Mai 2011 auf ein neues Schmelzofenkonzept mit angeschlossener Vorwärmkammer um (Bild 1). Dadurch lassen sich die Masseln schneller und mit weniger Energieverbrauch schmelzen. Beheizt wird die Kammer mit Wärme aus den Abgasen des Ofens. Die ungewöhnliche Konstruktion wurde vom Schmelzofenbauer ZPF Therm, Siegelsbach, entwickelt und kommt hier zum ersten Mal in einem Druckgießbetrieb zum Einsatz.
PMG wurde1962 gegründet. 1978 kam als weiteres Geschäftsfeld die spanende Fertigung hinzu, sodass das Unternehmen in der Lage ist, Kunden während der gesamten Prozesskette von den ersten Entwürfen bis zum Serienteil zu begleiten. Die Gießerei ist auf endkonturnahes Gießen mit hoher Oberflächengüte und engen Maßtoleranzen ausgelegt. Durchschnittlich 60 t Aluminium werden täglich eingeschmolzen und verlassen das Werk wieder in Form von 30-t-Druckgusskomponenten, vornehmlich für den Automotive-Bereich. Die hochpräzise gefertigten Bauteile sind sehr gefragt. 2011 musste das Unternehmen daher seine Produktionskapazitäten aufstocken, wie Günther Rusam, Abteilungsleiter Werksgestaltung und Instandhaltung bei PMG, erzählt: „Wir benötigten zum einen zusätzliche Schmelzleistung. Zum anderen wollten wir in der Schmelzerei auch Reserven schaffen, damit wir die anderen Öfen wenn nötig für Instandhaltungsmaßnahmen abschalten können.“ Die bestehende
Schmelzerei sollte daher um einen neuen Ofen erweitert werden.
Spezialkonstruktion nutzt Wärmeenergie der Abgase
Der Druckgussbetrieb nutzt bereits seit 2003 Aluminiumschmelzöfen von ZPF Therm. Kennzeichen dieser Anlagen ist das spezielle Abgasführungssystem, das die Rauchgase lange im Ofeninneren hält. Dadurch kann deren Hitze den Schmelzprozess unterstützen, sodass weniger Brennstoff benötigt wird. Dank dieser Bauweise und der dicken Isolierung des Ofenkörpers reduziert sich der Energieverbrauch gegenüber vergleichbaren Anlagen um 20 bis 30 %. Für den neuen Ofen bei PMG sollte die Energieeffizienz durch Nutzung der Abwärme jedoch noch weiter verbessert werden. Die Ingenieure entwickelten dazu eine Vorwärmkammer für die Masseln, die über eine eigens angepasste Kaminführung mit Abwärme aus dem Ofen beheizt werden kann. Indem das Metall hier bereits auf eine höhere Temperatur gebracht wird, reduziert sich die noch nötige Hitzezufuhr beim Einschmelzen im Ofen gegenüber Aluminium mit Raumtemperatur deutlich.

„Die konkrete Energieeinsparung ist abhängig von der Verweildauer“, erklärt Norbert Feth, Vertriebsleiter bei ZPF Therm. „Bei 900 kg Schwerkraftguss und einer Umgebungstemperatur von 400 °C in der Kammer wäre die nötige Schmelzenergie nach 1 h Anwärmen bereits circa 13 % niedriger als beim untemperierten Metall.“ Nach 2 h läge die Reduktion bereits bei rund 22 %. Zusätzlich verkürzt sich auch der Zeitaufwand für das Einschmelzen der Masseln, da der Schmelzpunkt bei vorgewärmtem Aluminium schneller erreicht wird. Der Materialumsatz des Ofens lässt sich auf diese Weise je nach Intensität der vorausgehenden Erhitzung steigern.
Schmelzzeit reduziert sich durch Vorwärmen um bis zu 20 %
Bei PMG werden jeweils einzelne Masselpakete von circa 500 kg in der Kammer vortemperiert. Die umgeleiteten, etwa 350 °C heißen Abgase wärmen sie hier 2 h lang auf rund 200 °C an, bevor sie in den Schmelzofen chargiert werden. Die Dauer des Schmelzprozesses bestimmt die Anlage automatisch nach dem Gewicht des Aluminiums. Da der Schmelzmeister des Druckgießbetriebs den aktuellen Zustand des eingebrachten Materials regelmäßig kontrolliert, kann er jedoch den Prozess auch vorzeitig unterbrechen, sobald er sieht, dass sich das Metall vollständig verflüssigt hat. Im Durchschnitt
ergibt sich dadurch eine um etwa 15 bis 20 % kürzere Schmelzzeit als bei nicht vorgewärmtem Aluminium.
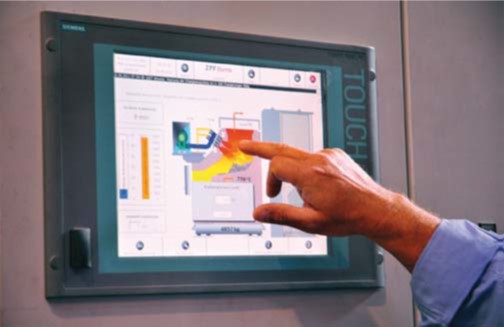
wurde bei dem neuen Schmelzofen auch die Handhabung der Steuerung dank eines Touchscreens einfacher und bequemer gestaltet.
Zum Beschicken wurde die Chargiermaschine des ZPF-Ofens eigens an die bei PMG verwendeten Behälter angepasst. Darüber hinaus verfügt das neue System über ein Touchpad, das eine bequemere Handhabung der Steuerung ermöglicht (Bild 2). Auf dem Monitor lassen sich zudem die Vorgänge im Ofen übersichtlich visualisieren. Hauptmerkmal ist jedoch die Vorwärmkammer: „Insgesamt
sparen wir durch diese Konstruktion objektiven Berechnungen zufolge in drei Jahren 40 000 Euro an Gaskosten ein“, so Rusam. „Die Vorwärmkammer hätte sich damit innerhalb dieser Zeit bereits amortisiert.“ Nach dem ersten Jahr im Einsatz sieht diese Prognose durchaus realistisch aus.