Einsatz der C-Technik zur Gussteilentwicklung
In den vergangenen Jahren haben sich die Randbedingungen für die Entwicklung und Produktion vieler Erzeugnisse, in denen Gussteile eingesetzt werden, entscheidend verändert:
- Der Lebenszyklus der Produkte wurde deutlich verkürzt. Nachfolgeprodukte müssen früher und schneller bei gleichzeitig erhöhter Sicherheit der Erstfertigung entwickelt werden.
- Der globale Wettbewerb und der drastische Preisverfall bei den Transportkosten sorgen dafür, dass nun auch diejenigen Länder für die Produktion und Lieferung in Frage kommen, die bisher „außen vor“ geblieben waren.
- Die wiederholten wirtschaftlichen Einbrüche im Automobil- und Maschinenbau bewirkten einen starken Personalabbau insbesondere in den Entwicklungsabteilungen (Stichwort „Outsourcing“). Mit den schlankeren Strukturen können häufig nicht alle bei einer Neuentwicklung anfallenden Aufgaben mit eigenen Ressourcen bewältigt werden
- In Vorlesungen muss die gesamte Bandbreite der Fertigungstechnik abgehandelt werden. Das Fertigungsverfahren „Gießen“ wird nicht immer ausreichend vertieft und kann mangels erforderlicher Infrastruktur auch in den meisten Praktika nicht berücksichtigt werden. Daher fehlt den Nachwuchs-Ingenieuren oftmals entscheidendes Wissen über die Möglichkeiten zur Konstruktion wirtschaftlich und funktional überzeugender Bauteile.
Hinzu kommt, dass auch die Firmen die Ausbildung von Nachwuchskräften vernachlässigt haben. Daher ist bei einer erhöhten Nachfrage der Bedarf nicht leicht wieder abzudecken. Als Folge hiervon werden Entwicklungstätigkeiten zunehmend von Zulieferern und externen Dienstleistern übernommen. Es besteht der Zwang, neue Produkte schneller als früher unter hohem Kostendruck zu entwickeln. Dieses ehrgeizige Ziel ist nur dann erreichbar, wenn völlig neue Formen der Kooperation eingeführt und angewendet werden und hierbei modernste Software- Werkzeuge zum Einsatz kommen. Der Zulieferer muss als Entwicklungspartner angesehen werden. Eine Zusammenarbeit beginnt zweckmäßigerweise nicht erst dann, wenn die Produkte fertig konstruiert sind, denn der in der Entwicklungsphase festgelegte Kostenanteil liegt bei 70 bis 80 %. Die Beratung oder weitergehende Unterstützung durch den Zulieferer in dieser Phase kann erhebliches Einsparpotential erschließen.
Inhalt dieser Seite
CAD-gestütztes Konstruieren
Mittlerweile hat sich die 3D-Konstruktion von Bauteilen auf breiter Front durchgesetzt (Bild 23).
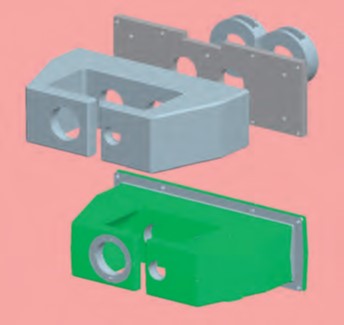
Gegenüber dem 2D-CAD ergibt sich insbesondere bei der Gussteil-Konstruktion ein höherer Nutzen durch
- Visualisieren des Bauteils, beispielsweise zur Prüfung auf kostensparende Fertigungsvereinfachungen,
- Darstellung der Baugruppe bei der Prüfung auf Integrierbarkeit von Anbauteilen,
- Festlegen der Arbeitsfolge beim Aufbauen der Form (Kerne, Formteile) in der Gießerei,
- Ermitteln von Volumina und Gewicht von Gussstück, Kernen und Form,
- Einsatz entwicklungsbegleitender Rohguss-Kalkulation,
- Beurteilung von Montage- und Fertigungsfragen zur Minimierung von Produktionsrisiken.
Die möglichst durchgängige Nutzung von 3D-CAD-Daten bringt eine erhebliche Zeitersparnis, denn diese Daten werden an mehreren Stellen benötigt. Durch den Zugriff auf ein einziges Modell sinkt auch die Fehlerwahrscheinlichkeit, vorausgesetzt, dass die einmalige Modellerstellung besonders sorgfältig durchgeführt wird, denn sonst ziehen sich vorhandene Fehler konsequent durch alle Prozesse.
Ob gussspezifische Features wie Verrundungen und Ausformschrägen bei der CAD-Modellierung berücksichtigt werden, hängt stark von der Art der späteren Modellherstellung ab. Während bei komplexen
Großgussteilen der Modellbau noch stark handwerklich geprägt ist und somit erheblicher Konstruktionsaufwand durch Verzicht auf diese Features eingespart werden kann, setzt sich das CNC-Fräsen der Modelleinrichtung nach CAD-Datensätzen bei kleineren Gussteilen zunehmend durch. Vor der Modellierung der fertigungsspezifischen Features durch den Gussabnehmer ist die Abstimmung des Formaufbaus mit der Gießerei dringend zu empfehlen.
Die auf der Bauteilgeometrie basierenden Nachfolgeprozesse (zum Beispiel Berechnung, gießtechnische Simulation und NCProgrammierung) verwenden weitestgehend das gleiche CAD-Modell und können daher im Sinne des Simultaneous Engineering parallel abgearbeitet werden.
Topologie-Optimierung
Die weiter unten beschriebene Finite-Elemente-Methode (FEM) erlaubt das sichere Auffinden konstruktiver Schwachstellen in einem CAD-Entwurf sowie eine objektive Beurteilung von Konstruktions-varianten. Mit diesem Hilfsmittel kann sich der Entwickler durch wiederholte Modifikationen im CAD-Modell iterativ an eine funktional überlegene Lösung herantasten. Insbesondere bei großen, komplexen Bauteilen mit Entsprechenden konstruktiven Freiheitsgraden ist diese Vorgehensweise zeitaufwändig. Mit der Topologie-Optimierung steht ein Werkzeug zur Verfügung, das hinsichtlich des zunehmenden Termindrucks bei der Bauteilentwicklung Entlastung schafft.
Ausgehend von dem für das zu entwickelnde Bauteil maximal verfügbaren Bauraum liefert es unter Berücksichtigung aller relevanten Lastfälle kraftflussgerechte Gestaltungsvorschläge (Bild 24). Dabei können im Lösungsvorschlag zu enthaltende Bauteilbereiche vorgegeben sowie Fertigungsrestriktionen wie Ausformrichtungen berücksichtigt werden. Inspiriert von diesen Vorschlägen ist eine treffsichere Bauteilkonstruktion ohne zeitfressende Iterationsschleifen möglich. Aufgrund der Formgebungsfreiheit ist das Fertigungsverfahren Gießen für die Umsetzung der topologisch optimierten Gestaltungsvorschläge in sowohl funktionsoptimierte als auch wirtschaftlich herstellbare Komponenten geradezu prädestiniert.
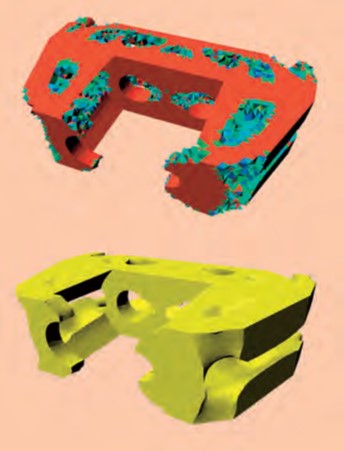
oben: massereduziertes FEM-Modell,
unten: für den CAD-Import geglättetes Volumen
FEM-Berechnung
Das Schaffen eines funktionsgerechten Bauteils sollte im Vordergrund der Gussteilentwicklung stehen. Zentrale Fragen des Konstrukteurs beim Entwurf einer Neukonstruktion sind:
- Wird das Bauteil den Belastungen standhalten?
- Sind alle kritischen Stellen ermittelt und berücksichtigt?
- Ist das Bauteil in einigen Bereichen überdimensioniert, was zu einem unnötigem Werkstoffaufwand und damit steigenden Kosten führen würde?
- Sind die im Betrieb auftretenden Verformungen tolerierbar?
Eine Antwort auf all diese Fragen allein mit Erfahrung oder analytischen Mitteln zu geben, ist bereits bei einfachen Bauteilgeometrien schwierig oder gar unmöglich. Daher hat sich nicht nur für komplexere Bauteile mit der Finite-Elemente-Methode (FEM) ein mächtiges Werkzeug zum Nachweis der funktionalen Anforderungen (zum Beispiel last- oder temperaturbedingte Verformung, Festigkeit, Schwingungsverhalten) durchgesetzt (Bild 25). Das Bauteil wird dabei im Rechner als Simulationsmodell abgebildet und mit den realen Belastungen beaufschlagt. Das Ergebnis sind die auftretenden Spannungen und Verformungen des Bauteils unter Last. Auch ist es möglich, weitere Ergebnisse zu erhalten, zum Beispiel Temperaturfelder oder Eigenfrequenzen. Durch geeignete Interpretation der Ergebnisse können auf diese Weise Bauteile unter Beachtung der Verformungs-, Gewichts- oder Kostenrestriktionen optimiert werden.
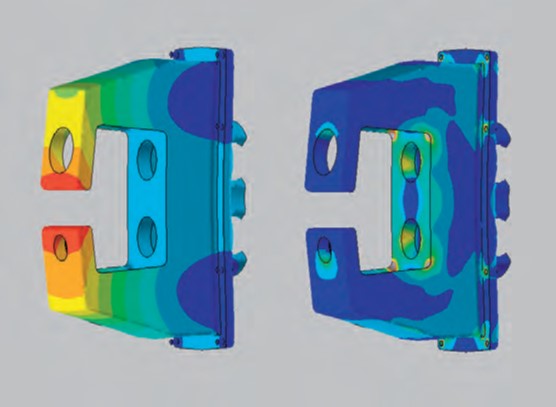
Der Nutzen des FEM-Einsatzes ist enorm, da konstruktive Schwachstellen sicher aufgedeckt und durch deren Beseitigung oft erhebliche Steifigkeitsgewinne realisiert werden können. Die großen konstruktiven Freiheiten beim Fertigungsverfahren Gießen erlauben es, dass die Kontur des Bauteils exakt an die Anforderungen angepasst werden kann. Es empfiehlt sich, für die per FEM-Analyse ermittelten hoch belasteten Bauteilbereiche gezielte Prüfanweisungen zu verfassen und so den Prüfaufwand beim Zulieferer auf das technisch Notwendige zu beschränken.
Form-Optimierung
Weist ein Gussteil Übergänge mit engen Eckenradien auf, können bei entsprechender Belastung hohe Kerbspannungen induziert werden, welche die Belastbarkeit erheblich senken. Wenn nur wenig Änderungsmöglichkeiten bezüglich Gewicht und/oder Geometrie an einem weitgehend auskonstruierten Bauteil bestehen, kann die Formoptimierung zum Erreichen der benötigten Festigkeit beitragen. Sie wertet jeweils nach einer FEMAnalyse die Spannungen an der Bauteiloberfläche aus und verschiebt iterativ solche Knoten, deren Spannungswerte oberhalb eines vorgegebenen Schwellwertes liegen, nach außen. Ähnlich den natürlichen Wachstumsvorgängen entstehen dadurch harmonische, kerbwirkungsarme Übergänge mit nahezu konstanten Oberflächenspannungen.
Wegen der relativ hohen Aufwände für das Erstellen der für die Optimierung geeigneten FEM-Modelle und die Rückführung des Optimierungsergebnisses in die CAD-Umgebung bleibt die Anwendung dieses auch als CAO (Computer Aided Optimization) bezeichneten Verfahrens noch auf Großserienteile beschränkt.
Festigkeitsnachweis
Für höher belastete Bauteile ist es Stand der Technik, die Festigkeit in Prüfstandsversuchen oder rechnerisch nachzuweisen. Aufgrund der im Allgemeinen komplexen Geometrie lassen sich die für ebene und zylindrische Körper entwickelten Nennspannungskonzepte nicht auf Gussteile anwenden. Stattdessen ist der rechnerische Festigkeitsnachweis für volumenförmige Bauteile auf Basis örtlicher Spannungen zu führen.
Die Vorgehensweise ist in der FKM-Richtlinie „Rechnerischer Festigkeitsnachweis für Maschinenbauteile“ beschrieben (Bild 26) [26]. Für die höchstbelasteten Knoten werden die per FEM-Analyse ermittelten Spannungswerte mit der von der Geometrie, dem Werkstoff und dem Belastungskollektiv abhängigen Bauteilfestigkeit verglichen. Dabei sind Sicherheitsfaktoren, die von der Art der Prüfung, dem Gefährdungspotenzial im Schadensfall und der Duktilität des Werkstoffes abhängen, zu berücksichtigen. Der sich aus dem Vergleich ergebende Auslastungsgrad darf 100 % nicht überschreiten. Zum schnelleren Einarbeiten in die Thematik sind die für Gusseisen spezifischen Inhalte in [29] verdichtet.
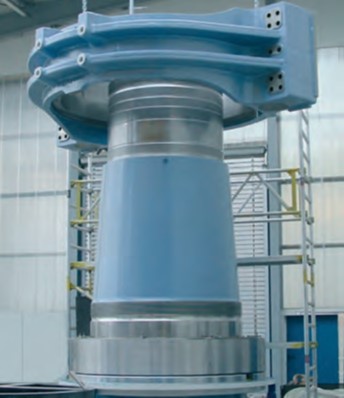
Gießtechnische Simulation
Das Konstruieren mit CAD dient der schnellen, übersichtlichen und sicheren Geometrieerzeugung. Mit Hilfe der Finite-Elemente-Methode wird geprüft, ob das Bauteil die auftretenden Lasten erträgt oder ob die auftretenden Verformungen im zulässigen Bereich liegen. Nachdem ein ausreichend dimensioniertes Bauteil vorliegt, ist der nächste Schritt, die Herstellbarkeit dieses Bauteils als Gussstück im Rechner zu simulieren und gegebenenfalls zu verbessern. Die Berechnung des Gießprozesses umfasst:
- die Formfüllung,
- das Erstarren des flüssigen Eisens,
- die Gefügeumwandlungen und Eigenschaftsverteilung im erstarrten Zustand,
- die Verformungen und Eigenspannungen des Rohgusses.
Als Ergebnisse der Simulation sind zu nennen die Strömungs- und Temperaturverteilung während der Formfüllung, potentielle Ungänzen, Erstarrungsdauer des Gussstückes, Gefügeausbildung und mechanische Eigenschaften im Gussstück. Ohne diese Simulation wären beispielsweise Informationen über die Turbulenzen und die Druckverhältnisse in der heißen Schmelze überhaupt nicht erfassbar. Mit Hilfe dieser und weiterer Ergebnisse lässt sich der Gießprozess im Rechner optimieren. Falls Problemstellen angezeigt werden, so können das Speiseund das Gießsystem verändert und die Auswirkungen nach einem erneuten Rechenlauf objektiv beurteilt werden. Seit kurzem ist für diese Aufgabenstellung eine Optimierungssoftware verfügbar, die zudem Randbedingungen wie die Minimierung des Verzuges berücksichtigen kann.
Die Programme zur Formfüllungs- und Erstarrungssimulation sind aufgrund der heute zur Verfügung stehenden Rechnertechnologien und der berücksichtigten Randbedingungen des Gießprozesses in der Lage, in relativ kurzer Zeit hervorragende Simulationsergebnisse zu liefern (Bild 28). Bei der verwendeten Software werden als Datenbasis nur physikalische und mechanisch-technologische Kennwerte der jeweils verwendeten Werkstoffe, Formstoffe und Formhilfsstoffe verwendet, so dass die Simulationsergebnisse in erster Linie von den zur Verfügung stehenden Datensätzen abhängig sind.
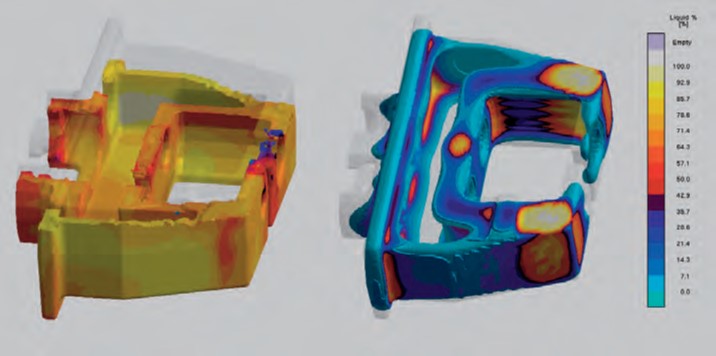
Anhand der Ergebnisse der gießtechnischen Simulation können die Wärmezentren des Gussstückes schnell erkannt werden. Diese Aussagen sind für den Gießer beim Auslegen des Gieß- und Speisesystems sehr hilfreich. Durch die Kenntnis der beim Gießen ablaufenden Prozesse können die kritischen Bereiche eines Gussstückes sehr genau lokalisiert werden. Das bietet die Möglichkeit, seine Qualität sehr viel effektiver als bisher zu beurteilen. Fertigungsrisiken werden durch die vergleichsweise schnelle und kostengünstige Überprüfung und Optimierung in der virtuellen Welt weitgehend ausgeschlossen.
Unter Zuhilfenahme der Simulationsergebnisse kann mit verringertem Aufwand eine wesentlich höhere Prüfqualität gewährleistet werden. Bei Kenntnis der kritischen Bereiche kann an diesen gezielt geprüft werden. Wenn sie fehlerlos sind, ist die Qualität des gesamten Gussstückes in Ordnung. Voraussetzung hierfür ist selbstverständlich die Prozesskontrolle und die zuverlässige Beherrschung des Gießprozesses. Sofern die kritischen Bereiche eines Bauteils dem Zulieferer nicht bekannt sind, muss es komplett geprüft werden. Aber auch dann besteht keine Sicherheit bezüglich der Problemstellenerkennung.
Bearbeitungssimulation
Der Aufwand für die Bearbeitung beeinflusst erheblich die Kosten des einbaufertigen Bauteils. Es ist daher von großem Nutzen, schon frühzeitig die für die vorgesehene Bearbeitung optimal geeignete Maschine auszuwählen. Dazu ist es notwendig zu prüfen, ob die zu bearbeitenden Flächen mit den Verfahrwegen der jeweiligen Maschine sowie mit deren Störkanten verträglich sind.
Die Auswahl der geeigneten Werkzeuge erfolgt direkt am Bildschirm im Dialog. Durch virtuelles Verfahren der Maschine in den entsprechenden Achsen wird ermittelt, ob die geplante Bearbeitung auf dieser Maschine sinnvoll und machbar ist (Bild 29). Sollte dies nicht möglich sein, dann kann das Werkstück auf einer anderen Maschine in einer weiteren Simulation getestet werden.
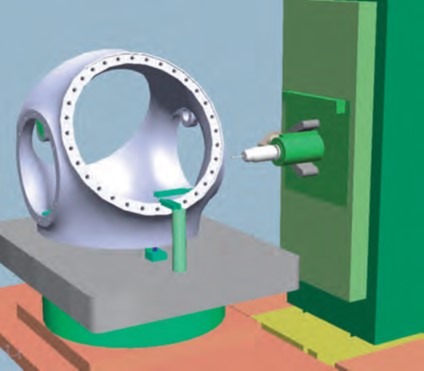
Die spätere reale Bearbeitung auf der letztendlich ausgewählten Maschine wird vor dem Start der Fertigung zusätzlich virtuell überprüft. Hierbei können sehr leicht Fehler in der Aufspannsituation und bei falschem ffestlegen des Bearbeitungsablaufs aufgedeckt werden. Weiterhin wird eine Kollisionskontrolle durchgeführt. Auch für den Bereich der mechanischen Bearbeitung führt die in der virtuellen Welt vorgenommene Fertigungssimulation zu gesteigerter Sicherheit, verringerten Einfahrzeiten und somit zu kürzeren Durchlaufzeiten und geringeren Kosten.
Rapid Prototyping
Die schnelle Marktpräsenz ist häufig von entscheidender Bedeutung für den Produkterfolg. Diese Anforderung führt bei gleichzeitig wachsenden Qualitätswünschen zu zusätzlichem Termindruck und verlangt neue Lösungsansätze. Prototypen unterstützen den Entwicklungsprozess und dienen zur Überprüfung von Design und Funktion in einer frühen Entwicklungsphase. Die schnelle Verfügbarkeit von physischen Modellen trägt zum Verkürzen der Planungsphasen und zum Optimieren der Produkteigenschaften bei. Hier kommt den Rapid-Prototyping-(RP-)-Technologien entscheidende Bedeutung zu.
Unter Rapid Prototyping versteht man solche Verfahren, mit denen Modelle, Formen und/oder Kerne schichtweise direkt aus dem 3D-CAD-Geometriedatensatz aufgebaut werden. äufig angewendete Verfahren sind die Stereolithographie, das Lasersintern von Kunststoffmodellen oder Sandformen und -kernen, Fused Deposition Modeling, Laminated Object Manufacturing, Direct Shell Production Casting und 3D-Plotting. Aufgrund der beschränkten Arbeitsräume der RP-Anlagen ist bei größeren Bauteilen das direkte Fräsen von Formen und Kernen aus Formstoffblöcken eine interessante Alternative (Bild 30).
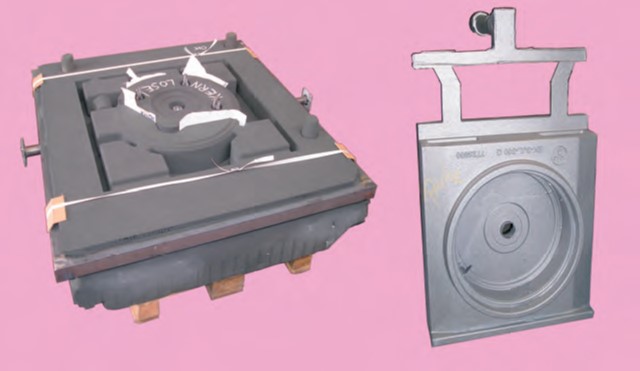
Gestaltungsfreiheit
Gegenüber konkurrierenden Verfahren besitzt das Fertigungsverfahren Gießen den Vorteil der nahezu unbegrenzten Gestaltungsfreiheit. Auch komplizierte Geometrien lassen sich in der Regel wirtschaftlich herstellen, da ein eventuell erforderlicher hoher Formgebungsaufwand nur einmalig, nämlich bei der Herstellung des Gießereimodells, anfällt. Durch Weglassen unbelasteter oder das gezielte Verstärken von stärker belasteten Bauteilbereichen sowie der Abkehr von plattenartigen, rechtwinkligen Strukturen kann die ideale Bauteilfunktion mit dem Fertigungsverfahren „Gießen“ am besten realisiert werden.
Insbesondere bei Gusseisen mit Kugelgraphit kann der gegenüber Stahlschweißkonstruktionen etwas niedrigere E-Modul durch den Nutzen der Gestaltungsfreiheit weit mehr als nur kompensiert werden. Die für ein einfaches mit einer Querkraft beaufschlagtes T-Profil dargestellten Vorteile (höhere Festigkeit dank niedriger Oberflächenspannungen sowie höhere Steifigkeit bei vergleichbarem Bauteilgewicht) lassen sich durchaus auch auf komplexe Bauteile übertragen, wenn die Möglichkeiten zur beanspruchungsgerechten Formgebung genutzt werden (Bild 31).
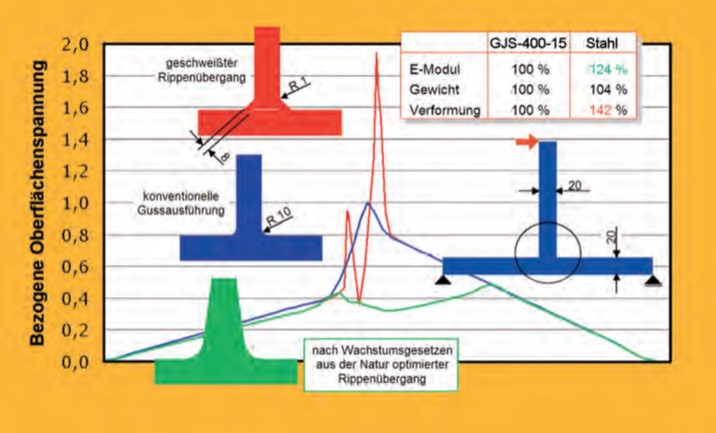
Bei anspruchsvollen Entwicklungszielen sollte die Topologieoptimierung zur Anwendung kommen, um eine Vorstellung von der Idealgestalt für die gewünschte Bauteilfunktion zu erhalten (Bild 32).
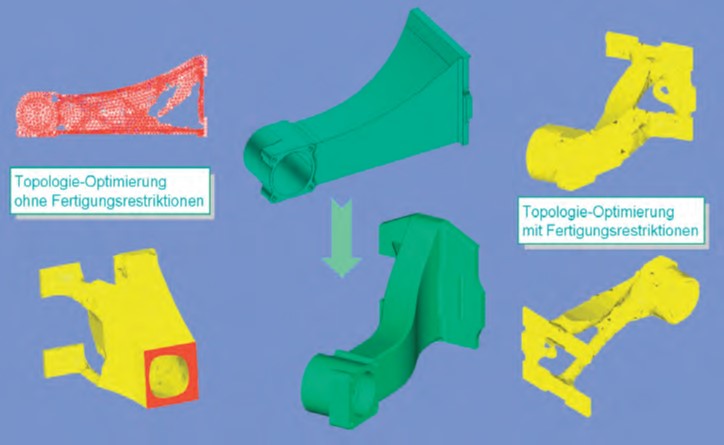
Bei der Umsetzung dieses Gestaltungsvorschlages in eine wirtschaftliche Gusskonstruktion sind dann noch fertigungstechnische Aspekte wie Gießlage, Herstellbarkeit der Werkzeuge und Kerne sowie Montierbarkeit der Form zu berücksichtigen. Letztendlich sollte auch bereits anhand des virtuellen Prototypen verifiziert werden, dass das Bauteil gieß-, strahl, putzund lackiergerecht konstruiert wurde. Als Entwicklungspartner kann die ausführende Gießerei die Gussteilentwicklung ganz oder teilweise übernehmen. Zumindest aber steht sie ihren Kunden gern beratend zur Seite, damit anspruchsvolle Bauteile wie im Bild 33 abgebildet entstehen können.
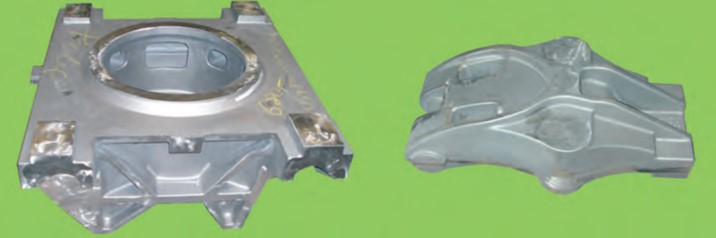
a) besonders maßhaltiges Rundtischgehäuse für eine Bearbeitungsmaschine
b) Gestalts- und gewichtsoptimierter Schließhebel für Kunststoffspritzgießmaschine
Download
Autoren und Quellen
Autoren:
Dr. Ch. Bartels, DI R. Gerhards, Prof. H. Hanselka, Prof. K. Herfurth, Dr. H. Kaufmann, DI W. Kleinkröger, Dr. M. Lampic, Dr. H. Löblich, Dr. W. Menk, Prof. G. Pusch, Dr. T. Schmidt, DI K.-H. Schütt, DI P. Tölke, Prof. E. P. Warnke