Proven energy efficiency solutions for foundries
Author: Pierre du Baret, Enertime, Puteaux
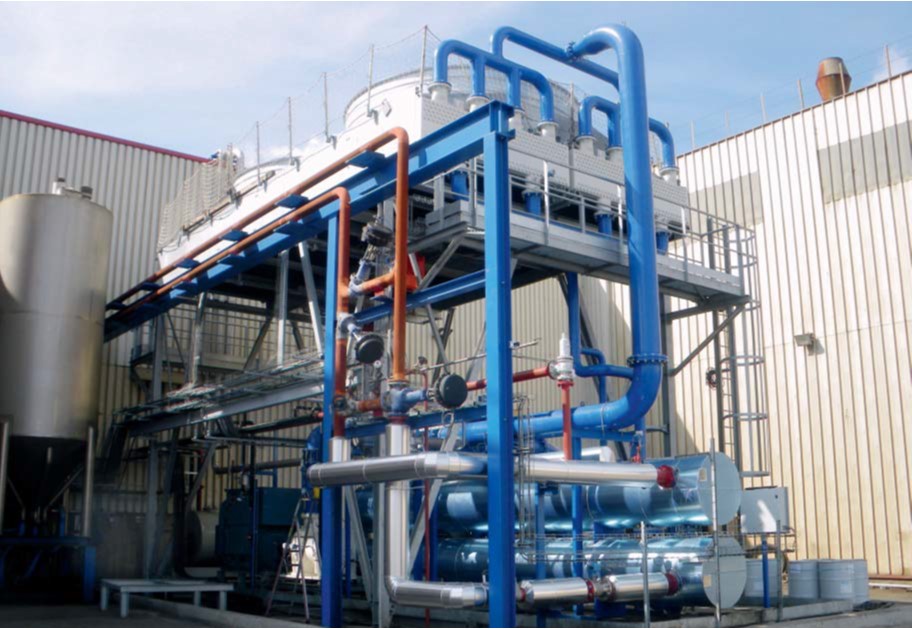
Erschienen in Casting Plant & Technology 3/2014
French company Enertime has developed an Organic Rankine Cycle system for waste heat recovery and power generation for foundries to self-produce their electricity and save up to 30% on their power bill. The pilot of this system named Orchid has been working in a foundry in France for 18 months.
Orchid is a waste-heat-to-power solution based on the Organic Rankine Cycle (ORC) principle. The system by Enertime from Puteaux in France works the same way as the steam power cycle mainly used in power production systems: heat is converted in mechanical energy, which is then transformed in electricity using an alternator. The main difference is that ORC works with organic fl uids that have a lower boiling point, therefore enabling the use of lower temperature heat sources. Organic fluids also reduce drastically operating costs while there is no need to man the power plant.
Orchid offers new perspectives for energy saving in the industry –especially for energy intensive industries such as foundries – being able to convert 200 °C heat sources into power with a 17 % effi ciency.
Enertime offers MW-size ORC systems dedicated to the industry. The company has taken into account industry specific requirements for its systems to be the more suitable to the industrial environment. The organic fluid used in Orchid is a refrigerant produced and available worldwide. The fluid is not toxic and not flammable and is kept in a closed loop, preventing any additional hazards for a plant, says Gilles David, CEO at Enertime and former head of AREVA Bio-Energy Division, Courbevoie, France.
Besides, ORC present major advantages compared to the steam cycle. “Compared to a steam power cycle, ORC systems need very low maintenance, display good part-load effi ciency, high availability and can be operated without permanent monitoring,” he said. “Daily operation and maintenance can be carried out without specific qualification.” The main reason is that there is no risk of steam condensation in the turbine in Organic Rankine Cycle systems. Water is a wetting agent so when steam is expanded in the turbine, water drops can form and damage the blades. In contrast, organic fluids used in ORC are called ‘dry’ fluids, i.e. the fl uid expanded in the turbine is always in a gaseous phase. This means the life of the turbines is increased and operational and maintenance costs are reduced.
Orchid produces between 500 and 1,000 kW of electric power depending on the available amount of heat. The unit is based on a tailor-made axial turbine and is specifi cally designed to work in an industrial environment. It is quite compact to be easily installed on site. The whole system fi ts on one skid of 40 feet, it is directly operational once installed on site and connected to the heat source, it can be installed outdoor and can work in any weather condition and fi nally it can be operated by the client staff. Enertime has remote monitoring and can control the system from a distance and intervene on site if necessary.
The ORC system can work with any kind of heat source. The unit can recover heat from a number of different sources singly or in combination. The heat can be brought to the ORC unit using steam, pressurized water or thermal oil.
For example, on the FMGC foundry site in Soudan in Western France, Orchid recovers heat form the blast cupola furnace producing cast iron (Figure 1).
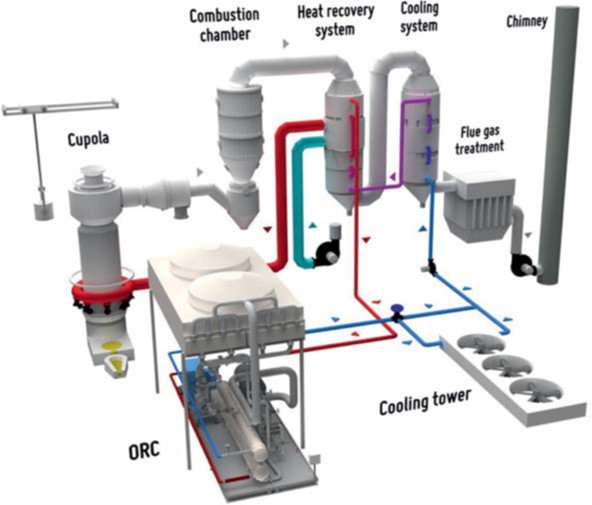
Orchid recovers waste heat from the cupola to generate electricity, which is directly used by the foundry and could also be exported to the grid. “We are seeing more and more international visitors and they are all impressed with the simplicity and compact size of our solution.” says Gilles David.
Orchid is self-reliant and causes no disturbance to the manufacturing process. Site staff just has to start the system and make basic checks which can be done by the regular maintenance team. The system also allows remote control by Enertime. Orchid covers up to 30 % of the electrical consumption of the foundry at full load. It is designed to work for 20 years and this power-plant can payback itself in five years with a MWh price of 100 euros. Orchid can work 24/7 but can also easily be started and stopped regularly. It works 5 days a week at the FMGC, following the plant activity.
Enertime takes into account the specifi cities of each client’s site and constraints to offer the most relevant solution. With power ratings from 500 kW up, foundries, steel factories and other industries can choose a customized system delivered as a turnkey solution. Orchid can also works in CHP (KWK) mode when hot water is required on site.
The Orchid system at the FMGC foundry has been installed thanks to the Total-Ademe program for energy efficiency in the industry. Enertime has sold another 600 kWel unit for combined heat and power that was commissioned in September 2014.