Petrolkoksstaub – ein neuer Energieträger für den Kupolofen
Von Heinz Kadelka, Düsseldorf, Ulrich Matschkewitz, Essen, Gotthard Dell, Walldürn
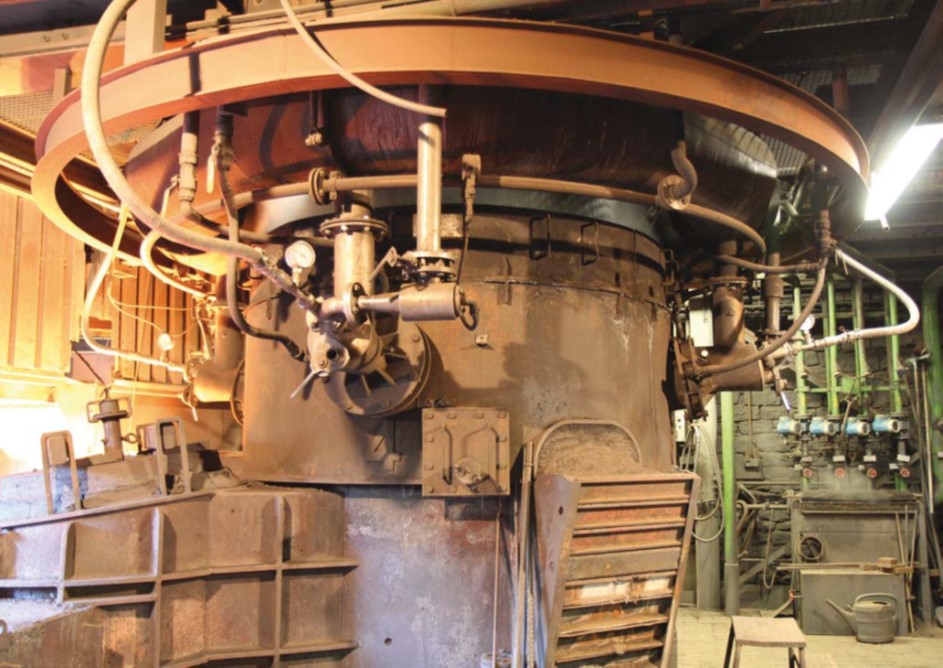
Injektion von Petrolkoksstaub in den Kupolofen als Substitution von Gießereikoks.
Erschienen in GIESSEREI 01/2013
Schon seit Anfang der 1980er Jahre wurde mit den verschiedensten Techniken versucht alternative Energieträger in den Kupolofen einzutragen um Gießereikoks zu ersetzen. Primäres Ziel war damals die Reduktion der Kokskosten, zudem erhoffte man sich weitere positive Effekte wie Prozessverbesserungen hinsichtlich der metallurgischen Beeinflussung, Flexibilität bei Legierungswechseln und Leistungsbeeinflussung. Eingesetzt wurden Stäube verschiedener Art und Zusammensetzung wie beispielsweise Anthrazitstaub (Carborat), Petrolkoks auch Elektrodengraphit sowie Staubgemische aus Reststoffen der Gießereien. Der Einsatz dieser Technologie wurde mehr oder minder erfolgreich betrieben, jedoch hat sich der dauerhafte Einsatz nicht durchgesetzt. Probleme beim Eintrag dieser Stoffe lagen sowohl im Verschleiß der Förderleitungen als auch im schlechten Ausbrand der Kohlenstoffpartikel, was zu erheblichen Problemen in der Gichtgasnachbehandlung bei Nasswäschern und Gewebefiltern führte, wo große Teile der eingebrachten Mengen wiederzufinden waren. Die betriebenen Injektionsanlagen sind so meist demontiert worden oder nicht mehr im Einsatz. In mehreren Gießereien wird diese Technik zur temporären Analysenkorrektur mittels Elektrodengraphit jedoch weiterhin erfolgreich genutzt.
Seit der Schließung der letzten deutschen Kokereien ist die Gießerei-Industrie in Mitteleuropa im zunehmenden Maße mit einer qualitativen Verschlechterung der Importkokssorten und mit Fragen der generellen Versorgungssicherheit konfrontiert. Daher wird die Suche nach alternativen, kostengünstigeren Energieträgern, die wirtschaftlich und technisch im Kupolofen als Ersatz für Gießkoks dienen können, immer dringlicher. Im Herbst 2010 beschloss daher ein Konsortium, bestehend aus den Unternehmen Linde Gas, Pullach, Linde Material Handling (MH) GmbH, Aschaffenburg, und Dako Kohlen Ex- und Import GmbH, Witten-Herbede, die generelle Eignung es bereits seit Jahren in verschiedenen Industriefeuerungen eingesetzten Petrolkoksstaubes für den Kupolofenprozess in einem Langzeitversuch in der Gießerei Weilbach der Linde MH zu testen. Dabei sollte neben den anwendungstechnischen Erkenntnissen des Staubeinblasens in die Schmelzzone, insbesondere in Verbindung mit dem Linde TDI-Verfahren, das Hauptaugenmerk auf die metallurgischen Parameter und Prozessveränderungen gerichtet werden.
Versuchsziele
Bereits im Frühjahr 2010 begann in Weilbach unter messtechnischer Begleitung des Instituts für Gießereitechnik (IfG), Düsseldorf, ein Vorversuch mit einer provisorischen Versuchsanlage, um erste Erkenntnisse über die Auswirkung des Einblasens von Petrolkoksstaub in den Kupolofen zu gewinnen. Hierbei wurde der Staub über eine Big-Bag-Anlage mittels separater Lanzen, die seitlich neben der TDI-Jet-Lanze angebracht waren, in die Schmelzzone injiziert. Auf Grund der positiven Erkenntnisse aus diesen Vorversuchen, wie z. B. der spontanen CO-Erhöhung im Gichtgas und der Eisentemperaturerhöhung bei Einsatz von Petrolkoksstaub, wurde im Spätsommer 2010 beschlossen, einen Langzeitversuch unter Produktionsbedingungen durchzuführen. Die Versuchsreihe sollte entsprechend Bild 1 über ein Jahr mit kontinuierlicher Reduzierung des Kokses bei gleichzeitigem Einsatz von Petrolkoksstaub erfolgen. Der Start erfolgte dann ab Oktober 2011.
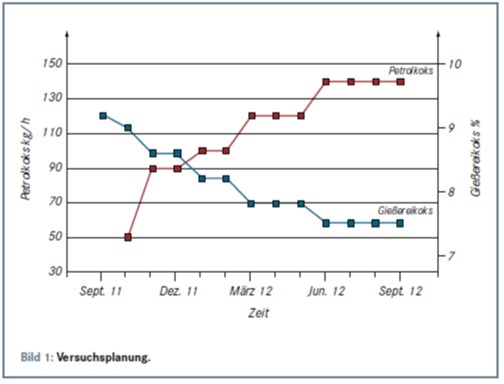
Kupolofenbetrieb Weilbach
Die Langzeit-Kaltwindkupolofenanlage mit Untergichtabsaugung ist mit einer thermischen Nachverbrennung ausgerüstet und wird für die Produktion von Gusseisen mit Lamellengraphit für Gabelstaplergewichte der Linde MH eingesetzt. Die Ofenanlage wurde vor ca. 10 Jahren von Heißwind- auf Kaltwindbetrieb umgestellt. Um die notwendigen wirtschaftlichen Effekte zu erreichen, ist die Anlage zeitgleich mit einem Linde Highjet-TDISystem ausgestattet worden. Als letzte größere technologische Neuerung wurde die Anlage 2009 auch mit CO/CO2-Lasern an der Gichtgasmessung aufgerüstet und zusätzlich ein O2-Lasersystem im Ausgang der Brennkammer installiert. Über diese Messgrößen werden die notwendigen Verbrennungsluftmengen und technischer Sauerstoff sowie die Brennkammertemperatur geregelt (Lambdawert).
Technische Daten des Kupolofen:
- Futterloser Kaltwindkupolofen mit 4 wassergekühlten Kupferdüsen und Drucksyphon
- Sauerstoffmodifiziert nach dem Linde TDI-Verfahren
- Ofenwindmenge 3500 – 4500 Nm/h
- Ofendurchmesser zwischen den Düsen 1250 mm
- Sauerstoffmenge nach TDI, 400 – 500 m3/h
- Gattierung Gussbruch für GJL 150 – 200
- Satzkoks 9 – 9,2 %
- Schmelzleistung 12 – 14 t/h
- Schmelztonnage z. Zt. 55 000 t/a
- Rinneneisentemperatur 1440 – 1460 °C
- Gichtgastemperatur <100 °C
- Gasmessung über Laseranlagen im Gichtgas (CO/CO2) und O2 in Brennkammer
- TNV – Nachverbrennung mit O2-Modifikation mit automatischer Lambdaregelung
- Propangasstützbrenner 20 – 120 m3/h
- Gaskühler und Trockenfilteranlage
Petrolkoks – weltweit genutzter Brennstoff
Petrolkoks (Bild 2) als fester Rückstand der Erdölraffination wird seit jeher weltweit als preisgünstiger Festbrennstoff großtechnisch in Kraftwerks- und Zementfeuerungen eingesetzt. Der nach dem Cracken des Vakuumrückstandes durch eine Trommelverkokung gewonnene sogenannte Grünkoks weist als herausragendes Merkmal einen extrem niedrigen Aschegehalt von <0,5 % auf, der wiederum einen hohen Kohlenstoffgehalt und damit verbunden hohen Heizwert von über 31 000 kJ/kg im Rohzustand bewirkt. Weltweit werden zurzeit ca. 110 Mio. t Petrolkoks mit steigender Tendenz vornehmlich in den USA und Südamerika produziert. Verlässliche Zahlen über die Produktion und den Verbrauch in Asien sind schwer zugänglich. Da diese aber insbesondere in China komplett verbraucht werden, sind sie für den europäischen Markt ohnehin von geringer Bedeutung. Die nach Westeuropa importierten Mengen schwanken in erster Linie – abhängig von der Nachfrage – zwischen 2 – 4 Mio. t jährlich. In der BRD wird Petrolkoks an 2 Standorten produziert, und zwar der BP-Raffinerie in Gelsenkirchen und der Esso-Raffinerie in Karlsruhe mit einer Kapazität von jeweils ca. 350 000 – 400 000 t/a. Somit kann festgestellt werden, dass in der BRD eine einheimische Produktionskapazität in der Größenordnung zwischen 400 000 – 500 000 t/a vorhanden ist, die dauerhaft zu einem preislich interessanten Niveau auch für die deutsche Gießerei-Industrie zur Verfügung stehen.
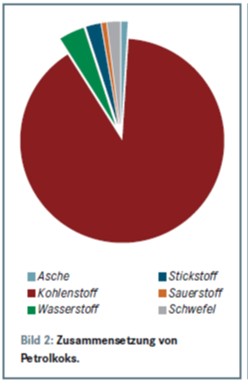
Qualität und Liefersicherheit
Die Weiterverarbeitung zu einem für die Industrieöfen erforderlichen blasfähigen Brennstoff erfolgt in einem Mahltrocknungsprozess, bei dem der mit einer Restfeuchte von ca. 10 – 12 % von der Raffinerie angelieferte Koks auf einen Wassergehalt unter 1 % getrocknet und zur Erzielung einer optimalen Verbrennung erforderlichen Mahlfeinheit von ca. 6 % R 0,09 μm gemahlen wird. Die Dako Kohlen Ex- und Import GmbH ist über einen langfristigen Mahlvertrag an das Werk der Microca GmbH, Lünen, gebunden, in der jährlich ca. 200 000 t Steinkohlenstaub für die Stahlindustrie und ca. 30 000 t Petrolkoksstaub ausschließlich für das Unternehmken Dako im Lohnverfahren für verschiedene Industriekunden produziert werden. Der so für von der Dako Kohlen Ex-und Import GmbH für Industrieöfen vertriebene Petrolkoksstaub weist die Spezifikationen in Tabelle 1 auf. Aufgrund der extrem niedrigen Wasser- und Aschegehalte weist Petrolkoksstaub einen garantierten Heizwert von 35 MJ/kg auf und ist somit der mit Abstand heizwertreichste Festbrennstoff (vgl.: Steinkohlenstaub ca. 28 MJ/kg, Braunkohlenstaub ca. 22 MJ/kg). Die hohe Mahlfeinheit ist für die Stabilisierung der Flammen in Industrieöfen zwingend erforderlich, da Petrolkoksstaub ein feuerungstechnisch vergleichsweise träger Brennstoff ist (Zündtemperatur ca. 690 °C).
Tabelle 1: Analysenblatt Petrolkoksstaub.
1 Immediatanalyse | Gew. % |
Wassergehalt | < 1,0 |
Aschegehalt wf | 0,5 - 1,0 |
Flüchtige Bestandteile wf | 9,0 - 11,0 |
Heizwert (Hu) GJ/kg | 34,3 - 35,4 |
2 Elementarzusammensetzung (wf) | Gew. % |
Kohlenstoff | 88,0 - 92,5 |
Stickstoff | 2,2 - 2,6 |
Wasserstoff | 3,6 - 3,9 |
Schwefelgehalt | 2,0 - 3,0 |
3 Aschezusammensetzung | Gew. % |
SiO2 | 10,0 - 25,0 |
Al2O3 | 5,0 - 15,0 |
Fe2O3 | 25,0 - 35,0 |
SO3 | 5,0 - 10,0 |
CaO | 3,0 - 8,0 |
MgO | 0,5 - 1,0 |
Na2O | 0,3 - 0,8 |
P2O5 | 0,3 - 0,8 |
TiO2 | 0,1 - 0,2 |
NiO | 5,0 - 7,0 |
V2O5 | 13,0 - 17,0 |
Die emissionsrelevanten Schwermetalle Hg, Cd etc. sind < 0,1 ppm | |
4 Mahlfeinheit | R 90 μm < 6 % |
5 CO2- Emissionsfaktor | 94,5 - 96,2 CO2/GJ |
Anlagentechnik für PC-Staubfeuerungen in kleineren Industriefeuerungen
Die Idee, Petrolkoksstaub auch in kleineren Industriefeuerungen einzusetzen, kam in den 1980er Jahren in der BRD nach der 2. Ölkrise insbesondere in der Glas- und Keramikindustrie auf und führte vorübergehend zu meist werkseigenen Entwicklungen in der Dosier- und Brennertechnik. Die konsequente Umsetzung erfolgte jedoch aufgrund des erforderlichen Anlageninvestments für die Staubtechnologie vor dem Hintergrund des sich wieder auf niedrigem Niveau stabilisierenden Öl- bzw. Gaspreisniveaus Ende der 1980er Jahre nicht. Aufgrund des langfristig absehbaren hohen Energiepreisniveaus für Öl und Gas werden derzeit in mehreren Industriezweigen die Ideen zur Nutzung von Petrolkoksstaub wieder aufgegriffen. Hierbei wird der Einsatz von Petrolkoks insbesondere in den Industrieöfen favorisiert, in denen ein niedriger Ascheeintrag über den Festbrennstoff z. B. zur Vermeidung von Verunreinigungen im Ofengut zwingend erforderlich ist.
Darüber hinaus sind insbesondere in der Kalkindustrie in den letzten 10 Jahren mehrere Anlagen zur Befeuerung von sogenannten Ringschachtöfen in Betrieb genommen worden. Generell ist hierbei von erheblichem Investitionsvorteil, dass Anlagen für Petrolkoksstaub aufgrund der produktspezifischen Sicherheitsanforderungen mit deutlich geringerem Aufwand gebaut und betrieben werden können, da im Gegensatz zu Förder- und Dosieranlagen für höherflüchtige Stäube wie Steinkohle- oder Braunkohlenstaub auf tertiäre Maßnahmen zum Explosionsschutz, wie z. B. druckstoßfeste Silos, gänzlich verzichtet werden kann.
Versuchsanlage Weilbach
Eine bereits vorhandene Versuchsanlage der Dako Kohlen Ex- Import GmbH wurde für den Einsatz in Weilbach modifiziert und den spezifischen Bedingungen angepasst. Ein eigens entwickeltes Prozessfließbild mit automatischer Petrolkoksmengenregelung wurde in der Ofenwarte der Kupolofenanlage installiert, maßgebende Prozessparameter dafür sind der CO-Gehalt im Gichtgas und die Temperatur in der Brennkammer. Aus dem Vorratssilo wird der Petrolkoksstaub über eine Förderschnecke entsprechend der Materialanforderung des Dosierbehälters durch PC Vario zugeführt. Der PC Vario in der in Weilbach ausgeführten Funktions- und Bauweise ist das Kernstück der Anlage. Neben seiner Funktion als Puffervolumen hat der Dosierbehälter primär die Aufgabe, die erforderliche kontinuierliche Staubzufuhr zum Kupolofen zu gewährleisten. Zu diesem Zweck ist der PC Vario mit insgesamt 3 Auslauforganen, bestehend aus jeweils einer drehzahlüberwachten Zellenradschleuse und azugehörigem Injektor ausgerüstet, die bei einem eventuellem Ausfall eines Abzugorganes automatisch auf das nächste umschalten. Aufgrund des geringen Ofengegendruckes und des Druckverlustes bis zum Ofen arbeitet dieser praktisch staub- und drucklos im Schüttgutbetrieb, was im Vergleich zu anderen Systemen mit beispielsweise Druckwechselbehältern erheblich kostengünstiger in Anschaffung und Betrieb ist. Die Mengenzufuhr des Petrolkoksstaubes auf die Blasleitung zum Ofen erfolgt durch die Drehzahlregelung der Zellenradschleusen mittels Frequenzumrichter. Die Aufzeichnung der verbrauchten Mengen erfolgt über die Messungen der Gewichtsveränderungen über Druckmessdosen mit einer Genauigkeit von 0,5 Gew. %. Die weitere Verteilung zu den Ofendüsen erfolgt über einen statischen Staubverteiler. Zur Überwachung der Anlage sind an geeigneten Stellen Durchflussmessungen installiert, zusätzlich überwachen Druckmessungen den einwandfreien Förderbetrieb (Bilder 3 und 4).
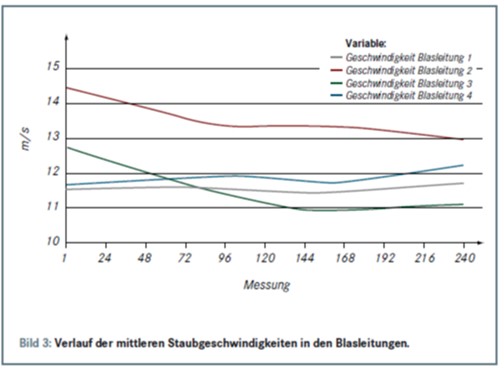
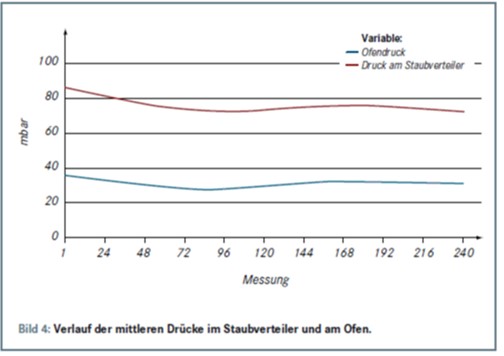
Beschreibung TDI-Düsensystem
Technischer Sauerstoff wird mit hohem Druck durch eine Lavaldüse in das TDI-System eingetragen. Durch den vor der Lavaldüse entstehenden Unterdruck wird ein Teilstrom des Primärwindes, der sogenannte Injektorwind (Bild 5) angesaugt, gemessen und geregelt. Der eingetragene Injektorwind kann so in jeder beliebigen möglichen Menge in den Sauerstoffstrom eingetragen werden. So können hohe Sauerstoffkonzentrationen (30 – 50 %) und Geschwindigkeiten von über 90 m/s im Kaltwindbetrieb und 250 m/s im Heißwindbetrieb erzielt werden. Bis zu 50 % des für das Schmelzen benötigten Sauerstoffes kann so durch das TDI-System eingesetzt werden.
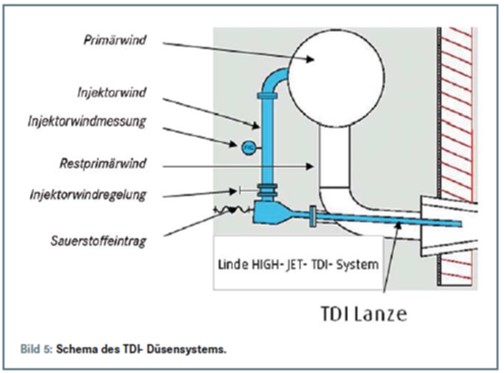
Kombination von Petrolkoksstaubinjektion mit dem Linde High-Jet-TDI-Verfahren
Ein Hauptziel der Versuchsreihe war von Beginn an die Petrolkoksstaubeindüsung in Kombination mit dem Linde High-Jet-TDI-Verfahren zu optimieren, da die Verfahrenstechnischen Vorteile wie höhere Strömungsgeschwindigkeit und somit Durchdringung der Schmelzzone sowie sofortige Umsetzung des einzelnen Kohlepartikels im Sauerstoffstrom offensichtlich sind. Zu Versuchsbeginn wurde die Anordnung der Petrolkoksstaublanzen so gewählt, dass diese seitlich und am Ende im TDI-Jet eindüsten. Eine Optimierung der Gas-/Feststoffvermischung wurde in einem zweiten Schritt durch Verkürzung der Petrolkokslanzen und Einbau eines kegelförmigen Diffusors erreicht (Bild 6). Hierdurch wird der Feststoff gleichmäßig in den Gasstrom mit einer Geschwindigkeit von ca. 70 m/s und einer Sauerstoffkonzentration von bis zu 40 % verteilt.
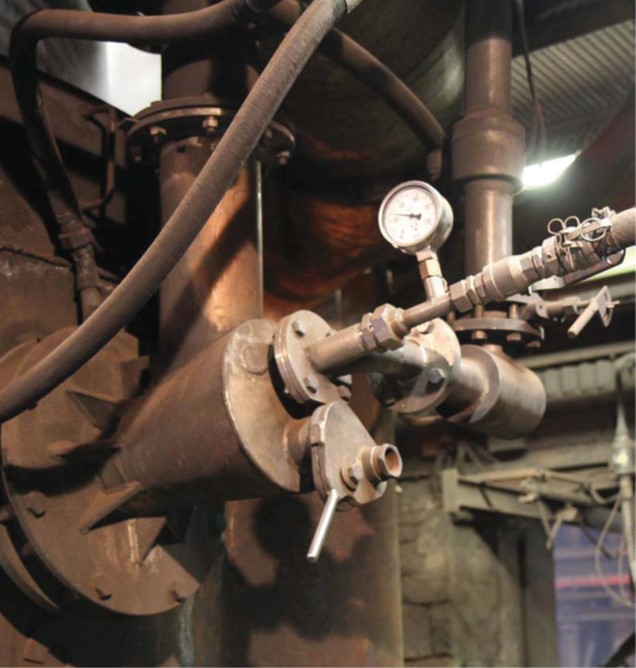
Versuchsergebnisse
Vorversuche
Bereits in den Vorversuchen mit provisorischer Big-Bag-Beschickung zeigten sich schon bei geringer Staubzugabe signifikante Effekte, wie eine CO-Erhöhung im Gichtgas und eine deutliche Rinneneisentemperatursteigerung, ohne dass die Gichtgastemperaturen anstiegen. Dies deutete auf eine völlige Umsetzung der unter 90 μm gemahlenen Staubpartikel in der Schmelzzone hin. Zudem konnten in den Vorversuchen keine negativen Auswirkungen auf Metallurgie und Emissionen gemessen werden. Die Bilanzierung des höheren Schwefeleintrages durch Petrolkoks wurde vom IfG anhand von SO2-Emissionsmessungen und gleichzeitigen Messungen der Schwefelgehalte im Eisen vorgenommen. Beide Untersuchungen wiesen keine höheren Konzentrationen auf (Bild 7).
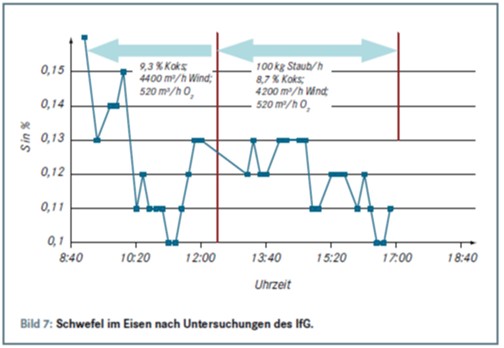
Langzeitversuche
Der Satzkoks wurde im Laufe der Versuchsreihen schrittweise reduziert, entsprechend wurde Petrolkoksstaub über die Versuchanlage eingeblasen, der Trend ist in Bild 8 dargestellt. Aus brennstofftechnischer Sicht ist besonders bedeutsam, dass offensichtlich für das erzielbare Austauschverhältnis Petrolkoksstaub/Gießkoks beim Eindüsen in den Schmelzbereich des Kupolofens tatsächlich das Verhältnis der Heizwerte (Hu GK/Hu PC ~0,83) ausschlaggebend ist und nicht der für die Beurteilung von festen Brennstoffen in metallurgischen Prozessen oftmals herangezogene fixe Kohlenstoff (Cfix=100-Asche-Flüchtige), da dieser bei beiden Brennstoffen fast identisch ist.
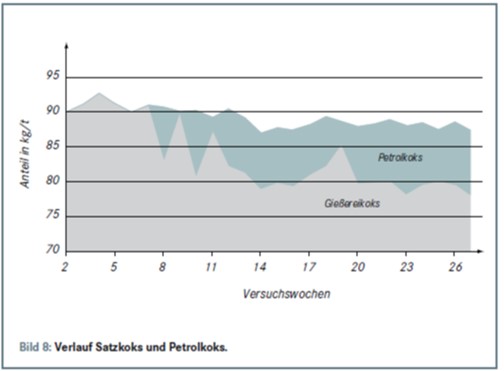
Prozessergebnisse im Langzeitversuch
Nach mehrmonatiger Petrolkoksstaubeindüsung unter Betriebsbedingungen bei einem konstanten Kokssatz von 7,8 % ist als Kernaussage festzuhalten, dass es bislang bei dieser Betriebsweise keine relevanten negativen Auswirkungen auf den Schmelzprozess gibt. Zudem führt die Substitution von Gießereikoks mit Petrolkoksstaub dazu, dass der CO-Gehalt im Gichtgas konstant auf hohem Niveau gehalten wird, was sich auch am Erdgasverbrauch der Brennkammer widerspiegelt (Bild 9).
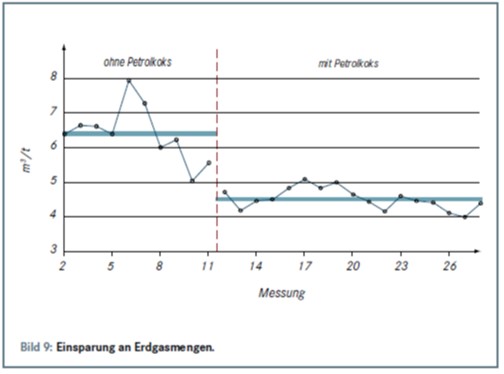
In der Permanentmessung für CO und Staub im Reingas kann festgestellt werden, dass diese sich sogar teilweise verbessern und deutlich unter den gesetzlichen Grenzwerten bewegen. Die Befürchtung, dass sich unverbrannte Stäube im Gichtgassystem oder in der Brennkammer ablagern, ist ebenfalls nicht eingetreten, auch der Staubanfall an der Trockenfilteranlage ist nahezu unverändert geblieben. Zudem haben sich die angefallenen Schlackenmengen nicht messbar erhöht. Die Eisenqualität ist sowohl bei der Spektralanalyse als auch bei thermoelektrischen Messungen nahezu unverändert geblieben, als wirtschaftlich signifikanter Nebeneffekt ist zudem ein geringerer Siliciumabbrand festzustellen. In der Tabelle 2 ist ein Auszug der wesentlichen Versuchsdaten im Vergleich Versuchsanfang zum Stand Juli 2012 festgehalten. Das vor Versuchsbeginn anvisierte wirtschaftliche Ziel die Schmelzkosten um 5 Euro/t zu senken, ist 3 Monate vor Beendigung der Versuche mit 4,50 Euro/t fast erreicht.
Tabelle 2: Versuchsdaten im Vergleich.
Parameter | Anfang (Sep. 2011) | Ende (Sep. 2012) | Delta |
Satzkoks (%) | 9,2 | 7,8 | -1,4 |
Petrolkoksstaub (%) | 0 | 1 | 1 |
Schmelzleistung (t/h) | 12,2 | 12,5 | 0,3 |
Rinnentemperatur (°C) | 1440 | 1450 | 10 |
Windmenge (Nm3/h) | 4400 | 4300 | -100 |
Sauerstoffmenge (m3/h) | 450 | 450 | 0 |
CO-Gehalt im Gichtgas (%) | 14 | 16 | 2 |
Erdgasverbrauch (m3/h) | 6,5 | 4,5 | -2 |
Si-Abbrand (%) | 25 | 20 | -5 |
S-Gehalt im Eisen (%) | 0,158 | 0,163 | 0,005 |
SO2-Gehalt im Abgas (mg/m3) | 110 | 100 | -10 |
Vorläufiges Fazit und Perspektiven
Der bisherige, eindeutig positive Versuchsverlauf an einem Kaltwindkupolofen mit Sauerstofftechnik hat gezeigt, dass der Einsatz von zuvor nur in Industriefeuerungen eingesetzte Petrolkoksstaub auch im Kupolofenprozess technisch und wirtschaftlich erfolgreich ist. Die wirtschaftlichen Effekte sind primär in der Reduzierung an Satzkoks und damit Einsparungen an Flüssigeisenkosten zu sehen. Die verbesserte Prozessstabilität ist darauf zurückzuführen, dass sich das Boudouard-Gleichgewicht in einem gleichmäßig hohem CO-Gehalt im Gichtgas einstellt, was wiederum den Siliciumabbrand verbessert und zugleich zu einem geringeren Erdgasverbrauch in der Brennkammer führt.
Die bisherige Nachweisführung zur Schwefelbilanz weist auf einen unbedeutenden Einfluss auf die Eisenqualität hin, erwartet werden an dieser Stelle keine nennenswerten Veränderungen. Am Versuchskupolofen in Weilbach konnten weitere Potentiale nicht ausgeschöpft werden, da bezogen auf die Produktpalette Beschränkungen hinsichtlich Rinnen- und Eisentemperaturen vorgegeben sind. Mit dem Einsatz der neu entwickelten Einblastechnik für Petrolkoksstaub steht für alle Kupolofenbetreiber eine neue Technologie zur Verfügung, um Schmelzkosten deutlich zu reduzieren. Besonders prädestiniert sind hierfür Heißwindanlagen, in denen Einsparung von 6 – 8 Euro/t erreichbar sind und somit die Satzkoksmengen unter 8 % gesenkt werden können. Mit ausgereifter Anlagentechnik und Prozessüberwachung kann hier nahezu verschleißfrei und vollautomatisiert Petrolkoksstaub dem Schmelzprozess zugeführt werden.