Induktionstechnologie für große Schmelzleistungen mit hoher Energieeffizienz
Von Erwin Dötsch und Yilmaz Yildir, Dortmund
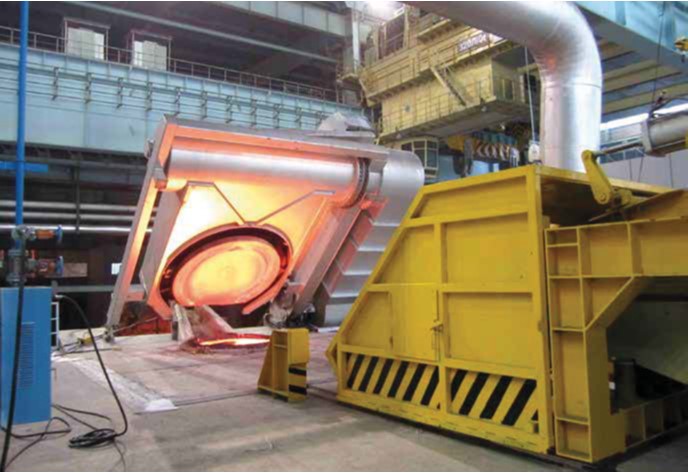
Zum Chargieren bereitstehende Deckel-Absaughaube an einem 30-t-ABPInduktionstiegelofen.
Erschienen in GIESSEREI 03/2018
Im Zusammenhang mit der weltweit angestrebten CO2-Reduzierung und dem steigenden Anteil der regenerativen Stromerzeugung kommt bei den thermischen Produktionsverfahren die Elektrowärme anstelle der fossilen Brennstoffe verstärkt zum Einsatz. Dieser Trend beeinflusst auch die Bewertung von Kupolund Induktionsöfen als Hauptschmelzaggregate in der Eisengießerei. In wieweit das induktive Schmelzen den koksbefeuerten Kupolofen ersetzen kann, wird im Folgenden diskutiert. Zur Klärung der Ausgangslage wird dabei zunächst auf die spezifische CO2-Emission der beiden Schmelzaggregate eingegangen. Anschließend wird dargestellt, dass die aktuelle Induktionstechnologie einen Entwicklungsschub dadurch erhalten hat, dass sich der Induktionstiegelofen bei der Elektrostahlerzeugung stellenweise als Alternative zum Lichtbogenofen etablieren konnte. Die Verbesserung der Energieeffizienz solcher Hochleistungsanlagen bleibt dabei eine ständige Herausforderung. Diese Aufgabe bezieht sich auf:
- die richtige Auslegung der Anlage zur optimalen Anpassung der Schmelzeproduktion an die „Schmelze-Verbraucher“, um vor allem den Energieaufwand für das Warmhalten der Schmelze gering zu halten.
- die Anlagentechnik zur Minimierung der elektrischen Verluste, hauptsächlich der Spulenverluste.
- die Verfahrenstechnik des Chargierund Schmelzablaufs, angefangen von der Zusammensetzung der Einsatzstoffe bis hin zum Abstich der Schmelze.
- die Nutzung der Abwärme der Ofenkühlung.
Schmelztechnik
CO2-Emission beim Schmelzen von Gusseisen
Zur ökologischen Beurteilung eines Produktionsverfahrens sind der vor Ort anstehende Energiebedarf (die sogenannte Endenergie) und die dabei entstehende CO2-Emission auf den Primärenergieeinsatz zurückzuführen, in den alle Aktivitäten zur Bereitstellung der Energie eingeschlossen sind (Bild 1) [2]. Bei der Bereitstellung von elektrischem Strom als Endenergie ist demnach zur Bestimmung des Primärenergiebedarfs und der CO2-Emmission der Stromerzeugungsmix aus herkömmlichen Kraftwerken und regenerativen Verfahren von maßgebendem Einfluss.
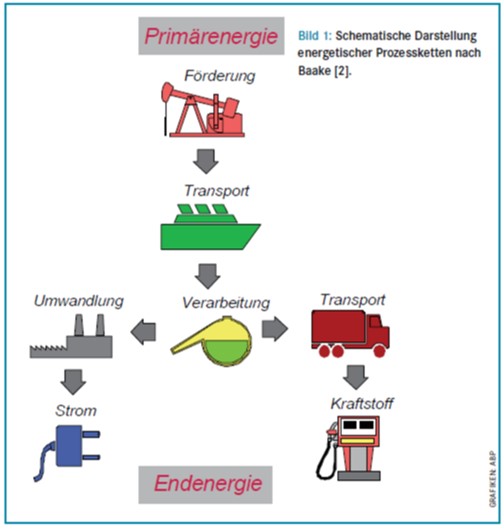
Aus der Darstellung in Bild 2 geht hervor, dass zum Erschmelzen einer Tonne Gusseisen bereits bei den Verhältnissen in 2007 die CO2-Emission des Induktionstiegelofens mit ca. 300 kg/t deutlich geringer war als die des Kupolofens mit fast 500 kg/t. Grund dafür ist, dass beim elektrischen Schmelzen über die CO2-Emission für die Energiebereitstellung hinaus keine zusätzlichen Emissionen durch die Verbrennung fossiler Brennstoffe vor Ort entstehen. Mit dem für 2020 in Deutschland prognostizierten Regenerativ-Stromanteil liegt dann die spezifische CO2-Emission mit ca. 200 kg/t bei etwa 40 % der CO2-Emission des Kupolofens, sodass der Einsatz des Induktions- anstelle des Kupolofens die CO2-Emission einer Gießerei erheblich reduzieren würde.
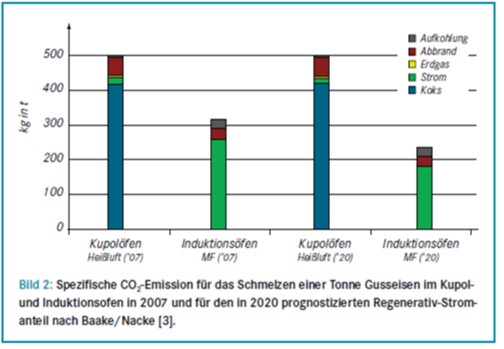
Induktionsöfen für die Stahlerzeugung
Für den Induktionsofen wurde mit seinem Einsatz in der Elektrostahlerzeugung als Alternative zum Lichtbogenofen ein neues Anwendungsgebiet erschlossen, dessen Entwicklungsbedarf sich fördernd auf die induktive Schmelztechnik auswirkt. Den derzeitigen Stand des induktiven Schmelzens im Stahlwerk beschreiben M. Chaabet und E. Dötsch [4], indem sie zunächst auf die charakteristischen Eigenschaften des Induktions- im Vergleich zum Lichtbogenofen eingehen und anschließend über signifikante Einsatzbeispiele für den Induktionsofen berichten. Dabei erscheint dessen Einsatz zur Produktion von rostfreiem Stahl wegen der hohen Ausbringung an wertvollen Legierungsstoffen besonders interessant. Auf diesem Gebiet kann der Induktionsofen als wirtschaftliches Schmelzaggregat zur Herstellung der legierten Rohstahlschmelze vor deren Weiterbehandlung in der Sekundärmetallurgie eingesetzt werden oder dem separaten Schmelzen der Ferrolegierungen dienen, die dann der Rohstahlschmelzei in flüssiger Form zugesetzt werden.
Schmelzmaschine für Edelstahl
Beispiel für den Einsatz des Induktionsofens als Schmelzaggregat zur Herstellung der Basisschmelze für Edelstahl ist die Schmelzanlage beim indischen Stahlhersteller Viraj Profile in Tarapur, Maharashtra, nahe Mumbai. Sie besteht aus drei ABP-25-t-/18-MW-Induktionsöfen. Jeweils zwei der 25-t-Öfen arbeiten im Schmelzbetrieb und liefern im Stundenzyklus gemeinsam eine 50-t-Charge zur Weiterbehandlung im AOD-Konverter und schließlich in der Stranggussanlage. Der dritte Ofen steht für die periodische Neuzustellung und Sinterung bereit.
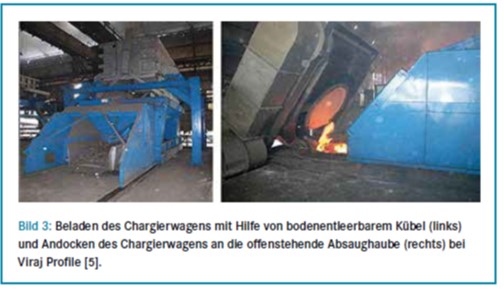
Schmelzen von Ferrolegierungen
in der weltweit leistungsstärksten Induktions-Schmelzanlage Der chinesische Stahlhersteller TISCO (Taiyuan Iron Steel Co Ltd) betreibt in Taiyuan ein Stahlwerk mit einem Ausstoß von 10 Millionen Tonnen pro Jahr, davon 3 Millionen Tonnen Edelstahl. Für den Ausbau der Produktion der rostfreien Stähle entschied man sich, in der neuen Schmelzanlage den Rohstahl und die Legierungsstoffe separat zu schmelzen. Dabei werden die Ferrolegierungen im Induktionsofen geschmolzen und der mit Rohstahl gefüllten Pfanne für die Nachbehandlung flüssig zugesetzt. Die Wahl fiel auf den Induktionsofen, wegen des hohen Ausbringens der wertvollen Metalle, weil Oxidation und Abbrand weitgehend vermieden werden. Beispielsweise steigt mit diesem neuen Verfahren das Ausbringen von Chrom von 93 % auf 98 %, was für TISCO im Gesamtprojekt eine Ersparnis von 1 Mrd. Yuan pro Jahr einbringt [6].
Die Investition wurde in zwei Stufen realisiert. Die für den Südbereich gelieferte Schmelzanlage besteht aus zwei 30-t-Öfen mit einer gemeinsamen 24,4-MW-Stromversorgung (Bild 4). Dabei befindet sich ein Ofen im Schmelzbetrieb, während der andere für die Neuzustellung bereitsteht.
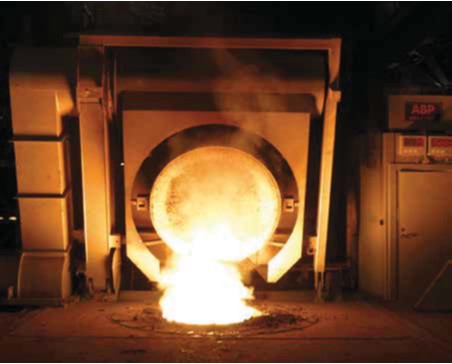
Das elektrische Sintern erfolgt mithilfe eines zusätzlichen IGBT-Umrichters. Auch das in TISCO-Nord installierte Schmelzsystem besteht aus jeweils zwei Öfen mit einer gemeinsamen Schaltanlage sowie einem zusätzlichen IGBTUmrichter für das Sintern. Hier wurde ein Riesenschritt in der Induktionstechnologie realisiert, indem sechs 65-t-Öfen mit drei 42-MW-ABP-Umrichtereinheiten gebaut wurden. Einen ersten Eindruck von dieser leistungsstärksten Induktionsanlage der Welt gibt Bild 5.
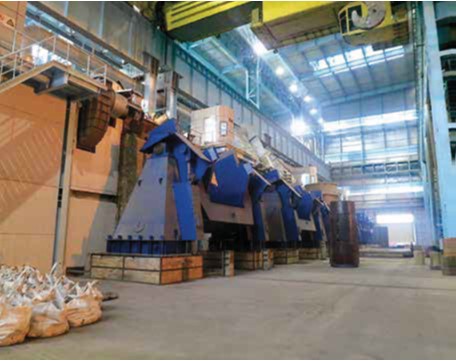
Gleichmäßige Netzbelastung durch Tandembetrieb
Für den Einsatz in der Gießerei stehen somit Induktionsanlagen mit Schmelzleistungen von über 60 t/h zur Verfügung. Für die meist geforderte kontinuierliche Flüssigeisenversorgung werden sie als Tandem ausgeführt, bei dem zwei Tiegelöfen aus einer Umrichter-Stromversorgung mit elektronischer Leistungsaufteilung so beaufschlagt werden, dass der eine als Schmelz- und der andere als Warmhalteofen arbeitet (Bild 6). Indem auf diese Weise einer der beiden Öfen ständig im Schmelzbetrieb läuft, wird eine gleichmäßige Netzbelastung mit niedrigem Leistungsmaximum erreicht, verstärkt durch die Auslegung des Umrichters mit Leistungskonstanz-Regelung (siehe unten). Zusätzlich wird mit der Tandemanordnung Energie gespart, weil die Verluste für das Umfüllen der Schmelze in einen separaten Warmhalteofen wegfallen.
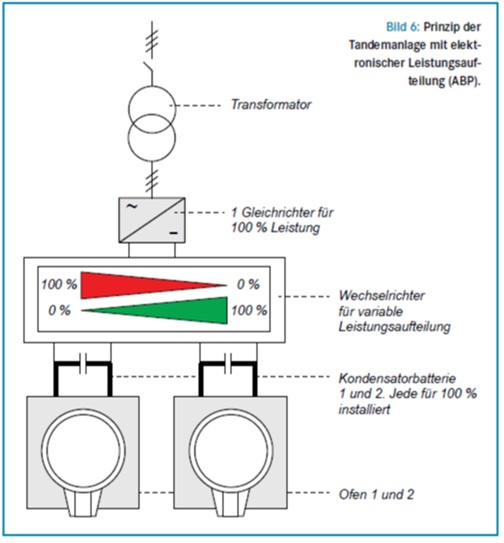
Verbesserung der Energieeffizienz
Energieverbrauch in Theorie und Praxis
Basis für den Energieverbrauch beim induktiven Schmelzen von Gusseisen ist zunächst der Energiefluss einer Tiegelofenanlage mit den in Bild 7 dargestellten Kennzahlen. Es entstehen hauptsächlich elektrische Verluste, nämlich im Transformator (1,5 %) im Umrichter (3 %), in Kondensator und Leitungen (2,5 %) sowie der Hauptanteil in der Spule (15 %). Dazu kommen im Idealfall 3 % thermische Verluste, sodass bei einer spezifischen Enthalpie von 390 kWh/t für das Schmelzen und Überhitzen von Gusseisen auf 1500 °C der Energiebedarf am Netz bei 520 kWh/t und der Gesamtwirkungsgrad bei 75 % liegen.
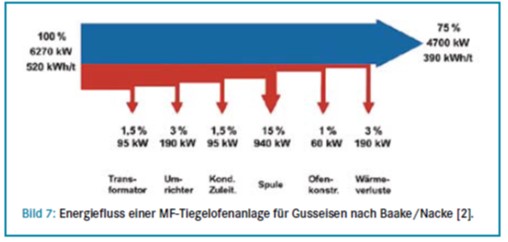
Bis zur Bereitstellung der gießfertigen Schmelze entsteht über den Schmelzprozess hinaus zusätzlicher Energiebedarf für das Warmhalten und andere Manipulationen. In einem gut geführten MFSchmelzbetrieb liegt dann der durchschnittliche Energieaufwand bei 560 bis 600 kWh/t.
In der Praxis werden diese Werte oft erheblich überschritten. Grund dafür sind meist höhere Prozessverluste, beispielsweise durch
- Setzen von sandbehaftetem Kreislaufmaterial,
- Warmhalten mit offenem Ofendeckel,
- ungedrosselte Absaugung beim Warmhalten,
- längeres Warmhalten durch mangelhafte Logistik,
- nicht sachgemäßes Chargieren.
Über das Vermeiden dieser zusätzlichen Verlustquellen wurde bereits früher von E. Dötsch [7] und D. Trauzeddel [8] berichtet. Im Folgenden wird auf zwei zusätzliche verfahrenstechnische Potentiale zur Verbesserung der Energieeffizienz hingewiesen, ehe auf die Möglichkeiten der Anlagentechnik eingegangen wird.
Zusammensetzung der Einsatzstoffe
Der richtige Mix von grobem und kleinerem Stückgut ist verantwortlich für ein gutes Ankoppeln des elektromagnetischen Feldes an das Schmelzgut. Eine hohe Schüttdichte der Einsatzstoffe ist besonders beim Anfahren der Schmelzcharge von ausschlaggebender Bedeutung für die volle Leistungsaufnahme und Energieeffizienz.
Eine zusätzliche, oft jedoch nicht beachtete Einflussgröße der Einsatzstoffe liegt in der Wahl des Silizierungsmittels. Bekanntlich ist die Auflösung des Siliziums in der Eisenschmelze ein exothermer Vorgang, der sich durch den Einsatz von FeSi energietechnisch nutzen lässt, wie von E. Dötsch [9] gezeigt wird. Dazu wird Gusseisen als idealisiertes Dreistoffsystem aus Eisen, Kohlenstoff und Silizium betrachtet, sodass dessen Enthalpie als Wärmebilanz nach K. Hack [10] aus den tabellierten thermochemischen Daten der Komponenten berechnet werden kann.
Tabelle 1: Spezifische Enthalpie von Gusseisen mit 3,7 % C und 1,8 % Si bei 1500 °C für verschiedene Zusammensetzungen der Eingangsstoffe (9]
Enthalpien von GJS, erschmolzen aus: | |
Reinen Stoffen | 369 kWh/t |
Stahlschrott, FeSi, Grafit | 371 kWh/t |
Stahlschrott, SiC, Grafit | 387 kWh/t |
Kreislaufmaterial | 392 kWh/t |
In Tabelle 1 sind die auf diese Weise ermittelten Enthalpiewerte einer Gusseisenschmelze mit 3,7 % Kohlenstoff und 1,8 % Silizium bei 1500 °C für verschiedene Zusammensetzungen der Einsatzstoffe aufgeführt. Man erkennt, dass die Enthalpie beim Erschmelzen des Gusseisens aus den drei reinen Stoffen aufgrund der positiven Mischungswärme des Siliziums mit 369 kWh/t wesentlich niedriger ist, als die 392 kWh/t für das Erschmelzen aus Kreislaufmaterial, in dem Silizium ja bereits gelöst ist. Der Einsatz von Stahlschrott, FeSi und Graphit kommt mit 371 kWh/t den Verhältnissen der idealisierten reinen Stoffe sehr nahe, während das Silizieren mit SiC statt FeSi dem positiven Mischungseffekt entgegenwirkt, weil dann Silizium nicht mehr als fast reiner Stoff, sondern als Verbindung vorliegt, zu deren Auflösung beim Schmelzen zusätzlich Energie benötigt wird.
Wie in Bild 7 dargestellt, wird in der Praxis von 390 kWh/t für den Wärmeinhalt der Gusseisenschmelzen bei 1500 °C ausgegangen. Dabei wird der relativ hohe Anteil an Kreislaufmaterial der Eisengießereien berücksichtigt sowie die Tatsache, dass überwiegend mit SiC statt FeSi siliziert wird. Grund für Letzteres ist der positive Einfluss des SiC-Legierens auf den Keimhaushalt der Schmelze. Unabhängig davon ist der maximale Unterschied im Energiebedarf beim Silizieren mit FeSi unter Berücksichtigung des Ofenwirkungsgrades von 70 % mit ca. 30 kWh/t doch so hoch, dass man diesen Effekt bei der Wahl des Siliziumträgers so weit wie möglich berücksichtigen sollte.
Leistungsoptimiertes Chargieren
Der konstante Eintrag der Nennleistung über die gesamte Schmelzperiode ist maßgebend für eine optimale Energieeffizienz beim induktiven Schmelzen. Das Einhalten dieser Anforderung führt zur kürzesten Schmelzzeit, damit zum geringsten Energieaufwand und schließlich auch zur höchsten Produktion. Wie an anderer Stelle ausführlich dargestellt, sind die folgenden drei Kriterien Voraussetzung für das Erreichen dieses Zieles [11]:
- Bereitstellen einer Schmelzgutmischung aus kleinstückigem Schrott und Kreislaufmaterial mit hoher Schüttdichte von ca. 2,5 t/m³, besonders für das Anfahren der Schmelzcharge.
- Sachgerechtes Chargieren des Schmelzgutes, d.h. rechtzeitiges prozessorgeführtes Nachchargieren auffestes Schmelzgut unter Berücksichtigung der optimalen Leistungsaufnahme.
- Einsatz eines Konstantleistungsumrichters, der mit einem Strom- und Spannungshub im Bereich von 70 –100 % ausgerüstet ist. Entsprechend der Darstellung in Bild 8 wird damit, in Anpassung an den sich ändernden elektrischen Widerstand des Schmelzgutes, die eingetragene Lastlinie mit 100 % Leistungseintrag automatisch abgefahren.
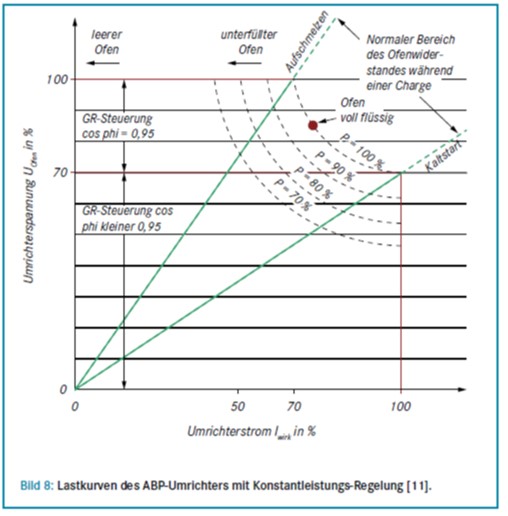
Praxisbeispiel für die Realisierbarkeit dieser Anforderungen sind die von A. Ament beschriebenen Verhältnisse an der 12-t-8,4-MW-Tandemanlage bei Buderus in Breidenbach [12]. Bild 9 zeigt beispielhaft den zeitlichen Verlauf von Leistung, Stromstärke, Spannung, Frequenz und Ofenfüllung einer Schmelzperiode. Man erkennt, dass Stromstärke und Spannung sich in Abhängigkeit vom Zustand der Ofenfüllung so anpassen, dass über die gesamte Schmelzperiode die Nennleistung in Höhe von 8400 kW abgerufen wird.
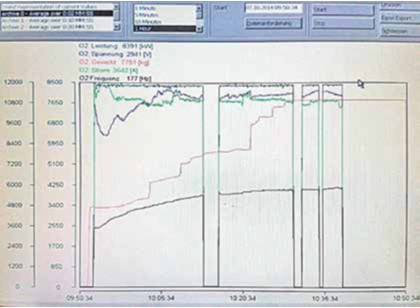
Häufig kann in der Praxis mindestens eines der drei genannten Kriterien nicht eingehalten werden. Vor allem eine zu niedrige Schüttdichte führt zu Beginn des Schmelzvorgangs auch bei Umrichtern mit Leistungskonstanz zum Leistungseinbruch. Dieser lässt sich durch das System Opticharge vermeiden, bei dem das Anfahren der Charge mit einer Teilfüllung an ferromagnetischem Schmelzgut und mit automatischem Nachfüllen kleiner Portionen dieses Materials durchgeführt wird [13].
Verbesserungspotenzial in der Ofenkonstruktion
Entsprechend ihrem Anteil an den elektrischen Verlusten ist die Senkung der Spulenverluste der größte Hebel in der Ofentechnik zur Reduzierung des Stromverbrauchs. Allerdings scheitert die Realisierung theoretischer Ansätze, beispielsweise der Röbeltechnik, bisher an fertigungstechnischen Problemen und an der Einhaltung der Betriebssicherheit, wie D. Trauzeddel in seinem Beitrag über Entwicklungstrends der Induktionsofentechnik ausführt [14]. Die realisierbaren Verbesserungspotenziale beschränken sich daher auf die Optimierung des Spulenprofils und die Ausführung der Kühlspule, womit sich die Verluste um maximal drei Prozentpunkte senken lassen. Beim Umrichter liegen durch den Einsatz neuer Leistungselektronik- Komponenten wie IGBT und IGLT vergleichbare Möglichkeiten vor.
In der Verringerung der Tiegelwanddicke liegt ebenfalls ein marginales Verbesserungspotential. Für mittelgroße Öfen gilt hier die Faustformel, dass eine Reduzierung um 1 cm eine Wirkungsgradverbesserung von etwa 0,5 - 1 % ermöglicht.
Nutzung der Abwärme
Wenn die Senkung der Spulenverluste technisch begrenzt ist, so liegt das größte Potential zu verbesserter Energieeffizienz in der Nutzung der Abwärme, die mit bis zu 20 % der Ofenleistung greifbar im Kühlwasser der Spule vorliegt, allerdings auf einem schwierig zu nutzenden Temperaturniveau von bisher maximal 80 °C. Für diese Verhältnisse gibt es Erfahrungen mit folgenden Lösungen:
- Einspeisung in ein Fernwärmenetz. In nur seltenen Fällen der örtlichen Bedingungen bringt dieses System einen messbaren Nutzen.
- Einsatz der warmen Luft, wie sie beim Kühlsystem nach dem Autokühlerprinzip anfällt, zur Schrotttrocknung oder zur Hallenheizung. Wegen der zu bewegenden großen Luftmengen ist auch diese Art der Abwärmenutzung wenig effektiv.
- Nutzung von warmem Wasser für Sanitär- und Heizungszwecke. Trotz des relativ hohen Investitions- und Regelaufwandes ist ein solches System aufgrund der hohen Energieeffizienz sinnvoll. Dazu wird über temperaturgesteuerte Regelventile und frequenzgesteuerte Pumpen die Kühlleistung den Wärmeverlusten der Induktionsanlage angepasst. Dementsprechend wird durch Regelung der Kühlwasserdurchflussmenge die Kühlwassertemperatur trotz unterschiedlicher Leistungsbeaufschlagung konstant gehalten. Gleichzeitig wird bei niedriger Ofenleistung (beispielsweise im Warmhaltebetrieb) die Pumpenleistung reduziert, sodass der Stromverbrauch des Kühlsystems gesenkt wird.
Es ist selbsterklärend, dass mit steigender Temperatur des Kühlmediums neue Möglichkeiten für die Abwärmenutzung erschlossen werden. Beispielsweise wird mit einer Kühlmedium-Temperatur ab etwa 180 °C der Einsatz des ORC-Prozesses zur Stromerzeugung interessant. Allerdings ist zu berücksichtigen, dass mit höherer Spulentemperatur der elektrische Widerstand des Kupfers und damit die Spulenverluste ansteigen. Außerdem muss die Ofenkonstruktion an die höhere Spulentemperatur angepasst werden.