Heißwind-Kupolofen
Zur Erzeugung des Heißwindes nutzt man die Wärme der Kupolofen-Abgase, die im Rekuperator die angesaugte Frischluft auf ca. 500 °C bis 600 °C aufheizen.
Diese Maßnahme ist neben der Optimierung der Einsatzmenge von Koks ein sinnvoller Weg eine beträchtliche Verbesserung der Wirtschaftlichkeit, verglichen mit dem Kaltwind-Kupolofen-Betrieb, zu erreichen und ist Stand der Technik.
Eine Verbesserung des Wirkungsgrades gegenüber dem Kaltwind-Kupolofen wird erreicht, indem den Winddüsen hoch erhitzte Verbrennungsluft mit Windtemperaturen zwischen 400 °C und 600 °C, zugeführt wird.
Der Ofenwirkungsgrad beträgt nach Literaturangaben ungefähr 60 %. Der Koksverbrauch liegt je nach Betrieb in einer Größenordnung von 90 kg/t bis 135 kg/t. Unter der Annahmen eines Heizwert von 8,5 kWh/kg, Europäische Kohle, gelangt man zu einem Energiebedarf von 765 kWh/t bis 1148 kWh/t.
Durch Restwärmenutzung kann Restwärme zur Erzeugung von Druckluft und Strom genutzt werden. Der theoretische Anlagenwirkungsgrad kann bis auf 75% angehoben werden.
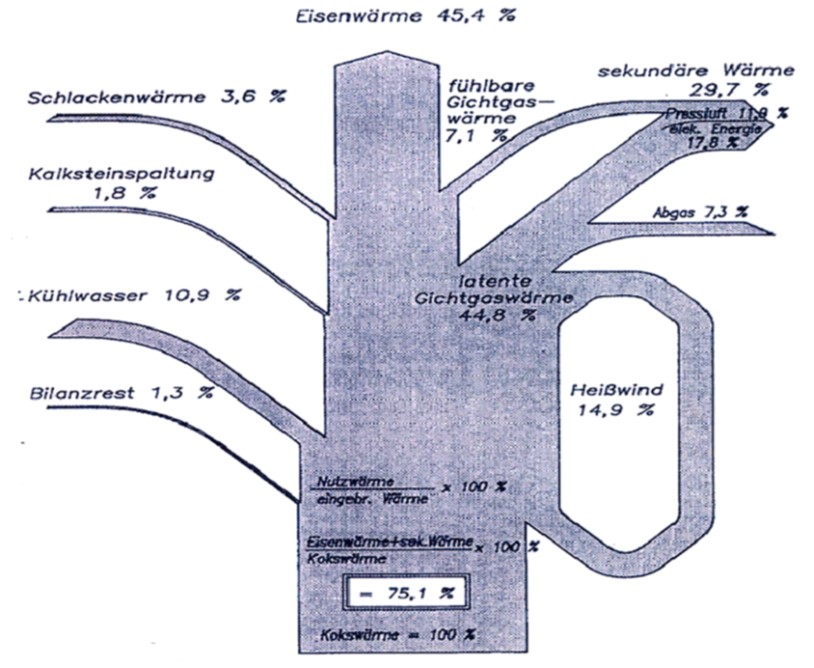
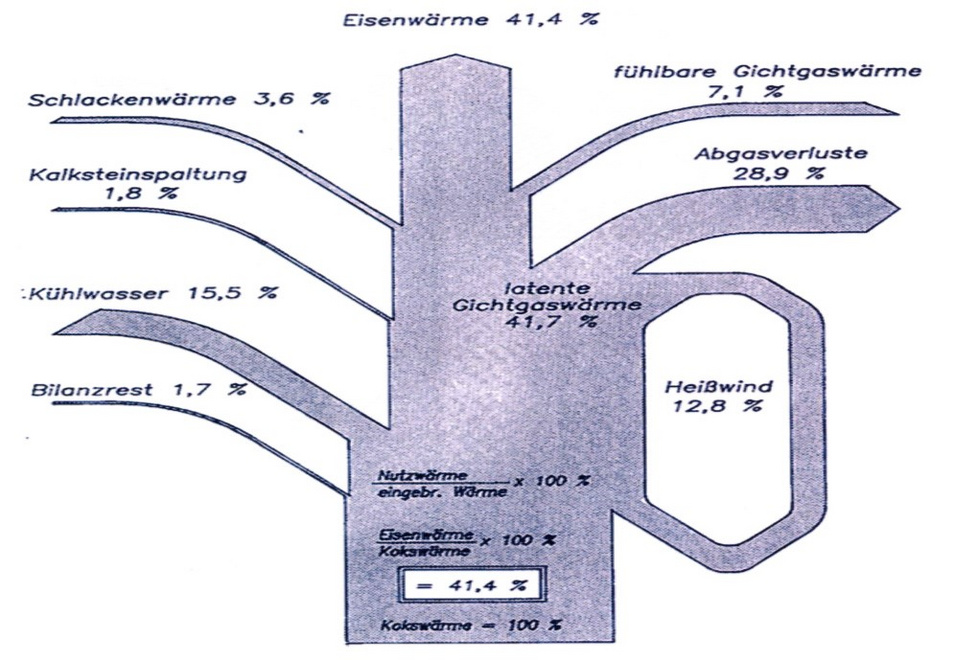
1 Verfahrensmodifikationen beim Heißwind- Kupolofen
1.1 Überhitzung des Windes
Eine Weiterentwicklung des Heißwind-Kupolofens besteht darin, die Temperatur des Heißwindes mit Hilfe einer Plasmafackel weiter zu erhöhen.
Als Beispiel zeigt Abbildung 3 einen im Werk Sept Fons von Peugeot installierten Kupolofen mit Plasma beheiztem Wind.

Die von der Plasmafackel auf etwa 3500 °C erhitzte Luft vermischt sich mit dem vom Rekuperator zuströmenden Heißwind von etwa 350 °C, so dass Windtemperaturen zwischen 500 °C und 1300 °C gefahren werden können.
Im praktischen Betrieb wurde der Ofen mit Temperaturen zwischen 800 °C bis 900 °C gefahren.
Nach [30] kann durch die Steigerung der Windtemperatur um 200 °C, ausgehend von 550 °C bis 750 °C, z.B. durch Einblasen von Luftplasma, rund 10 kg Koks pro erschmolzene Tonne eingespart werden.
Ausgehend von einem Heizwert europäischer Kohle von 8,5 kWh/kg gelangt man zu einer Verminderung des Energiebedarfs von 85 kWh/t.
1.2 Einsatz von Erdgas/Sauerstoff-Brennern
Der Einsatz von Erdgas-Sauerstoff-Brennern am Kupolofen wurde im Rahmen eines BMBF-Vorhaben „Ökologische und Ökonomische Optimierung des Kupolofen - Schmelzprozesses durch den Einsatz von Erdgas-Sauerstoff Brennern bei gleichzeitig möglicher Feststoffinjektion“ untersucht.
Das mit dem Kurznamen »KUPOLOPT« bezeichnete Verbundforschungsvorhaben diente der ökonomischen und ökologischen Optimierung von Kupolöfen in Gießereien. Versuche mit Erdgas-Sauerstoff-Brennern wurden an einem Langzeit-Heißwind-Kupolofen der Firma Küttner GmbH bei der Fa. Fritz Winter Eisengießerei GmbH & Co. KG über einen Zeitraum von 3 Jahren gefahren.
Angestrebt wurden die Verbesserung der Schmelzleistung, Reduzierung der Emissionen sowie die Wiederverwendung von Gießereistäuben und gießereifremden Stäube. Im Mittelteil des Schmelzofens, der heißen Schmelzzone, wird dem Schmelzofen über Blasformen vorgewärmte Verbrennungsluft zugeführt. In diesen Blasformen können Staublanzen integriert werden, mit denen sich Gießereistäube direkt in den Schmelzofen einblasen lassen. Allerdings ist zu berücksichtigen, dass das Einblasen von Gießereistäuben den Schmelzofen an der Einblasstelle abkühlt.
In Versuchen der Air Products GmbH wurde nachgewiesen, dass die auf Grund des Einsatzes von Erdgas-Sauerstoff Brennern unerwünschte Abkühlung im Einblasbereich verhindert werden kann. Darüber hinaus können Erdgas-Sauerstoff-Brenner zur Energieversorgung des Schmelzprozesses beitragen und den Kokseinsatz reduzieren.
Durch den Einsatz von Erdgas-Sauerstoff-Brennern ändert sich der eingestellte energetische Haushalt des Schmelzofens.
Die Ergebnisse zeigen eine Steigerung der Schmelzleistung bei einer Reduzierung des Kokseinsatzes. Weiterhin konnten beim Einsatz von Erdgas-Sauerstoff-Brennern gegenüber der konventionellen Betriebsweise Mangan und Silizium-Presslinge eingespart werden.
Wegen des stärkeren Einsatzes von Sauerstoff sinkt auch der Bedarf an spezifischen Heißwind wodurch weniger Heißwindenergie in den Schmelzofen eingetragen werden muss.
Allerdings steht den energetischen Einsparungen ein vermehrter Einsatz der Erdgasenergie gegenüber, so dass nach [11] mehr Energie zum Erschmelzen des Basiseisens in den Schmelzofen eingetragen werden muss.
1.3 Einsatz des Sequenz-Impuls-Verfahren
In der Gießereiindustrie wird die zum Gießen benötigte Schmelze nach [43] überwiegend im Kupolofen mit Heißwindbetrieb erschmolzen.
Um die Verbrennung zu fördern, wird Sauerstoff zugeführt. Die Entwicklung der Verfahren zur Sauerstoffzufuhr begann mit der Sauerstoffanreicherung des Heißwindes und führte zur direkten Injektion ins Koksbett.
Als Weiterentwicklung folgte die Injektion des Sauerstoffes mit Überschallgeschwindigkeit. Das Einbringen des Sauerstoffes mit Überschallgeschwindigkeit kann aber an Grenzen bei der Durchdringung des Koksbettes führen, da ein Großteil der kinetischen Energie des gebündelten Strahls beim Aufprall auf den Koks verbraucht wird.
Neu ist die Überlagerung eines konstanten Sauerstoffstromes mit einer kurzzeitigen im-pulsartigen Sauerstoffzufuhr über konventionelle Lanzen. Erreicht wird damit ein tiefes Eindringen des Sauerstoffs in die Beschickungssäule und eine gleichmäßige Durchgasung.
Damit verbunden sind die Auflockerung des Koksbettes und eine gute Verbrennung auch im Inneren der Koksschüttung durch ein kurz-zeitiges lokales Überangebot an Sauerstoff Durch das von der ThyssenKrupp AT.PRO tec GmbH entwickelte Sequenz-Impuls-Verfahren führte bereits an Kupolöfen mittlerer Bauart mit Durchmessern von 1200 mm bis 1800 mm zu einer Verbesserung der Wirtschaftlichkeit des Kupolofenbetriebes.
1.4 Kokseinsparung eines futterlosen, wassergekühlten
Heißwind-Kupolofen gegenüber einem Kaltwind-Kupolofen Der Koksbedarf zum Schmelzen von 1000 kg Eisen im Kaltwind-Kupolofen, dessen Innendurchmesser größer als 750 mm ist, wird nach [7] wie nachfolgend dargestellt angegeben:
Tabelle 1: Koksbedarf zum Schmelzen von 1000 kg Eisen in einem feuerfest ausgekleideten Kaltwind-Kupolofen
Abstichtemperatur [°C] | Koksbedarf [kg/t Eisen] |
1.400 | 95 |
1.426 | 110 |
1.454 | 140 |
1.510 | 155 |
1.538 | 170 |
Bei Heißwind-Kupolöfen ersetzt die Luftvorwärmung einen Teil des Schmelzkoksbedarfs. Angaben der Literatur zufolge werden je 100 °C Windtemperatur etwa 8 kg Koks/t Eisen eingespart.
Unter Berücksichtigung dieses Sachverhaltes und unter Berücksichtigung des in Tabelle 1 dargelegten Koksbedarfes lässt sich folgende Berechnung erstellen:
Für einen futterlosen, wassergekühlten Heißwind-Kupolofen mit einer Schmelzleistung von 20 t/h und einer Abstichtemperatur von 1510 °C erhält man einen Koksbedarf von 155 kg/t Eisen, obgleich dieser Wert zunächst nur für den feuerfest ausgekleideten Kaltwind-Kupolofen gilt. Für eine Heißwind-Temperatur von 420 °C, etwa 400 °C über Raumtemperatur, ergibt sich eine Kokseinsparung von 8*4 = 32 kg.
Bei einem angenommenen Ofendurchmesser von 1800 mm wäre bei Wasserkühlung der zu deckende Wärmeverlust nach Abbildung 14 mit einem zusätzlichen Koksbedarf von etwa 8 kg/t Eisen auszugleichen. Daraus folgt ein Gesamtbedarf von 155 – 32 + 8 = 131 kg Koks/t Eisen.
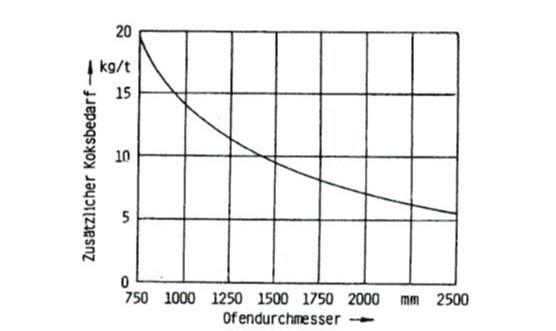
Quellen:
[7] F. Neumann, Gusseisen - Schmelztechnik, Metallurgie, Schmelzbehandlung, 1999, Expert Verlag, S. 186
[11] Ökologische und Ökonomische Optimierung von des Kupolofen-Schmelzprozesses durch den Einsatz von Erdgas-Sauerstoff Brennern bei gleichzeitig möglicher Feststoffinjektion; BMBFFöderprogramm; Integrierter Umweltschutz in der Gießereiindustrie; 2003
[20] St. Hasse; Merkmale, Wirtschaftlichkeit und Entwicklungstendenzen des Kupol- und Induktionsprozesses in Eisengießereien; Gießerei-Rundschau; 1991; 11/12 November/Dezember
[30] Merkblatt über Beste Verfügbare Techniken in der Gießereiindustrie; Umweltbundesamt; Juli 2004
[43] Sauerstoff hilft; Verbesserung der Wirtschaftlichkeit des Kupolofenbetriebes Giesserei 95; 03/2008