Energieaspekte bei elektrisch beheizten Schmelzöfen
Für die Aufgaben im Gießereibetrieb haben sich zwei grundlegende Induktions-Ofentypen in den Gießereien etabliert. Dabei handelt es sich um Induktions-Rinnenofen und Induktions-Tiegelofen mit Netz- oder Mittelfrequenz.
Für den spezifischen Energiebedarf einer Induktions-Schmelzanlage verantwortlich gemacht werden müssen die Ofengröße und Konstruktion (Netz- oder Mittelfrequenz-Induktionstiegelöfen) und der Aufbau der Induktions-Schmelzanlage (z.B. Mono oder Tandembetrieb).
Den Energiebedarf beeinflussen ebenfalls die Ofenfahrweise und Produktionsorganisation, das zu erschmelzende Metall, die Chargenzusammensetzung, Chargierung, Deckelbetrieb und insbesondere zusätzliche Warmhaltezeiten.
Beim Schmelzen von Gusseisen ergibt sich der resultierende Endenergiebedarf als Summe aus dem Energiebedarf für das Schmelzen, der energetischen Berücksichtigung der Materialverluste durch Abbrand und dem Energieaufwand für die Überhitzung und dem zusätzlichen Aufkohlungsprozess, der bei den koksgefeuerten Verfahren im Schmelzprozess integriert ist.
1. Energieaspekte bei Induktions-Tiegelöfen
Für das Erwärmen, Schmelzen und Überhitzen von Gusseisen bis auf eine Temperatur von 1.500 °C müssen theoretisch 387 kWh/t reine Nutzenergie aufgebracht werden.
Dieser theoretische Energiebedarf wird aufgrund des Gesamtwirkungsgrades der Schmelzanlage sowie der betrieblichen Produktionsabläufe zum Schmelzen von Gusseisen überschritten.
Durch den Einsatz moderner Mittelfrequenz-Induktions-Tiegelofen beläuft sich der Energiebedarf zum Schmelzen von Gusseisen bis auf eine Temperatur von 1.500 °C auf 490 KWh/t bis 520 KWh/t.
2. Modernisierung bestehender Schmelzanlagen
Die Ausstattung älterer Induktions-Schmelzöfen mit moderner Mittelfrequenztechnik, einhergehend mit der Ausstattung einer modernen Prozessleittechnik bietet Möglichkeiten um Energiekosten einzusparen.
- Der Wirkungsgrad moderner Frequenz – Umrichter liegt zwischen 96 % und 97,5 % während bei älteren Anlagen zur Frequenzumrichtung (z. B. Quintduktoren) Werte von < 88 % zu verzeichnen sind.
- Die Umrüstung von Netzfrequenz-Induktions-Tiegelofen auf die Mittelfrequenz-Induktions-Tiegelofen-Technik ermöglicht das Schmelzen ohne Sumpf, die das Anfahren mit festem Einsatzmaterial im Chargenbetrieb erlaubt.
- Im Vergleich dazu arbeiten nach [7] Netzfrequenz-Induktions-Tiegelofen nur wirtschaftlich, wenn man sie mit einem Sumpf von 50 % bis 70 % betreibt.
- Beim Schmelzen von Eisenwerkstoffen erlaubt die Mittelfrequenz-Induktions-Tiegelofen-Technik gegenüber der Netzfrequenz-Induktions-Tiegelofen-Technik eine bessere elektromagnetische Ankopplung, die im Ergebnis eine Einsparung von Energie erzielt.
- Die Umrüstung von Netzfrequenz-Induktions-Tiegelofen auf die Mittelfrequenz-Induktions-Tiegelofen-Technik gestattet die Realisierung einer höheren Leistungsdichte durch die die Schmelzzeit verkürzt wird, die thermischen Verluste geringer ausfallen und Energie eingespart wird.
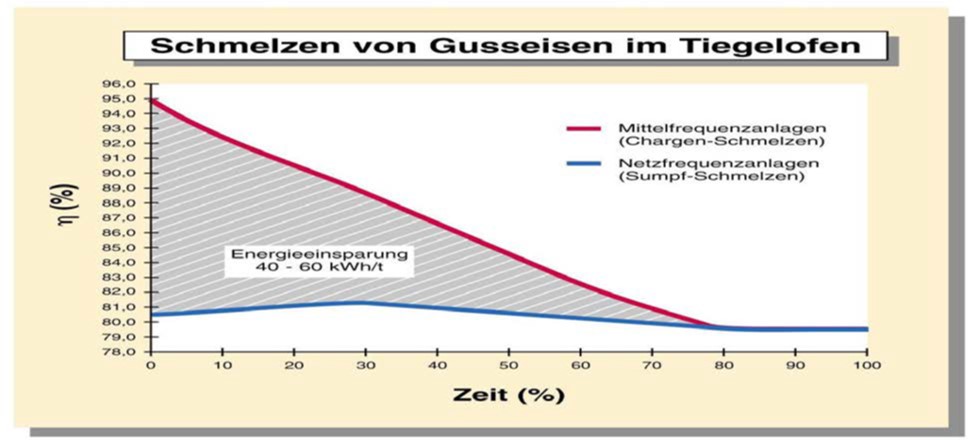
3. Optimierung der Ofenkonstruktion
Den elektrischen Verlusten in der Spule bzw. dem Induktor kommen die größten Verluste zu. In diesem Bereich lässt sich die höchste Einsparung an Energie realisieren.
Bei Mittelfrequenz-Induktions-Schmelzanlagen liegen die Spulenverluste nach heutigem Stand der Technik in einer Größenordnung bis zu 15 % beim Schmelzen von Gusseisen, bezogen auf die zugeführte Energie.
Die Otto Junker GmbH hat bei der Konstruktion von Hochleistungs-Induktoren für Induktions-Rinnenöfen mit Hilfe der numerischen Simulation des elektromagnetischen Feldes die Verteilung und Streuung dieses Feldes ermittelt.
Die aus diesen Ergebnissen abgeleiteten Schlussfolgerungen führten zu einer Veränderungen der Ofenkonstruktion z.B. hinsichtlich der Größe des Jochfensters, der Dimensionierung des Rinnenquerschnittes und der Art und Ausführung der Kühlschale.
Im Ergebnis konnte eine Reduzierung der Verlustleistung im Induktor um 40 % erzielt werden.
Für Induktions-Tiegelöfen flossen die Erkenntnisse in die hauseigene Edelstahlgießerei an einem 1,5 Tonnen Induktions-Tiegelöfen ein. Die erreichte Energieeinsparung lag bei 5-10 % [48].
4. Einsatz moderner Frequenzumrichter-Technik
Die Energieversorgung von Induktions-Schmelzöfen erfolgt entweder durch Einspeisung aus dem Netz über einen entsprechenden Transformator mit Netzfrequenz, oder mittels Frequenzumrichter, die eine höhere Frequenz des Wechselstromes erzeugen. Die Induktions-Schmelzöfen mit Frequenzumrichter arbeiten hauptsächlich im Bereich der Mittelfrequenz von 110 Hz bis 1.000 Hz.
Zu Beginn der Entwicklung der Mittelfrequenz-Induktions-Schmelzöfen standen rotierende Umformer, gefolgt von magnetischen Umformern mit Frequenzvervielfachung und sind bekannt unter den Bezeichnungen Triduktoren und Quintduktoren.
Bei den Frequenzumrichtern moderner Bauart wird der über einen Stromrichtertransformator eingespeiste Netzstrom zunächst in Gleich-spannung bzw. Gleichstrom umgewandelt und in einem Wechselrichter wird dann die gewünschte Mittelfrequenzspannung erzeugt.
Eine derzeit moderne Umrichter – Technologie wird durch den IGBT-Frequenzumrichter (Insulated Gate Bipolar Transistor) repräsentiert, bei dem Transistoren neuester Bauart im Wechsel-richter anstelle von Thyristoren zum Einsatz kommen.
Die Umrichter – Technologie führte zu sehr leistungsfähigen und zuverlässigen Systemen, die mit geringen elektrischen Verlusten und guter Netzverträglichkeit arbeiten.
Das Bestreben mit einer Schmelzanlage eine möglichst hohe Schmelzleistung zu erreichen, führte zu der Entwicklung von Tandemanlagen und der DUOMELT-Technik.
Bei der DUOMELT-Technik werden zwei Induktions-Schmelzöfen an einen Umrichter – Anlage angeschlossen und durch eine geeignete Schaltungstechnik kann die Gesamtleistung der Umrichter – Anlage in einem beliebigen Verhältnis auf beide Öfen aufgeteilt werden.
5. Einfluss der Leistungsdichte auf den Energiebedarf
Die Leistungsdichte eines Induktions-Schmelzofens hat Einfluss auf den Energiebedarf.
Beim Einsatz der Mittelfrequenztechnik kann gegenüber der Netzfrequenztechnik eine 2 bis 3-mal höhere Leistungsdichte zum Einsatz kommen. Dies führt zu einer deutlichen Senkung des Energiebedarfs.
Die höhere Frequenz der Mittelfrequenztechnik gegenüber der Netzfrequenztechnik, anstatt 50 Hz vorzugsweise 250 Hz, erlaubt eine höhere Anschlussleistung der Anlage bei gleichem Ofenfassungsvermögen.
Eine hohe Leistungsdichte verkürzt die Schmelzzeit und die thermischen Verluste werden geringer, so dass nach Aussage von [36] 30 bis 40 kWh/t weniger Energie benötigt werden.
Die Leistungsdichte kann auch für den Vergleich zweier Mittelfrequenz-Schmelzöfen herangezogen werden. Der Gesamtwirkungsgrad einer Schmelzanlage ergibt sich aus der nachstehenden Formel.
ŋges. = ŋel * (1 – Warmhaltewert/Nennleistung)
Da der Gesamtwirkungsgrad einer Schmelzanlage von dem Verhältnis von Warmhaltewert zu Nennleistung abhängig ist, sinkt der spezifische Stromverbrauch mit steigender Nennleistung bei gleicher Ofengröße.
Dieser Sachverhalt lässt sich nachfolgend verdeutlichen. Vergleicht man beispielsweise zwei Schmelzöfen gleichen Fassungsvermögens, jedoch unterschiedlicher Leistung, so sind zunächst die statischen Wärmeverluste durch den Wärmefluss von der heißen zur Tiegelinnenseite zur wassergekühlten Spule aufgrund der gleichen Geometrie beider Schmelzöfen gleich.
Der leistungsstärkere Schmelzofen vermag jedoch in diesem Zeitraum eine höhere Menge an Einsatzstoff durchzusetzen, da der Anteil der Gesamtleistung, der zum Schmelzen zur Verfügung steht, höher ist als bei dem vergleichsweise schwächeren Ofen.
Aus wirtschaftlichen und energetischen Gründen ist es sinnvoll, einen möglichst kompakten Ofen mit hoher Leistungsdichte einzusetzen, da er einen geringeren Stromverbrauch besitzt.
Nach theoretischer Überlegung ist die Ofenfahrweise mit maximal verfügbarer elektrischer Leistung und damit hoher Leistungsdichte energetisch am günstigsten. Durchgeführte Versuche an einem 12 Tonnen Mittelfrequenz-Induktions-Tiegelofen zeigen, dass mit abnehmender Leistungsdichte, der Stromverbrauch exponentiell ansteigt, da bei einer sehr niedrigen Leistungsdichte der Anteil der Energie zum Abdecken der statischen thermischen Verluste überproportional hoch ist.
Der Vergleich zwischen dem Schmelzen mit 6000 kW oder 3000 kW zeigt eine Differenz im Stromverbrauch von 20 kWh/t. Dieser energetische Vorteil kann beim Wechsel von Netzfrequenzanlagen auf Mittelfrequenzanlagen genutzt werden, da die maximale Leistungseinspeisung bei Netzfrequenzanlagen dieser Ofengröße bei 3000 kW liegt [36].
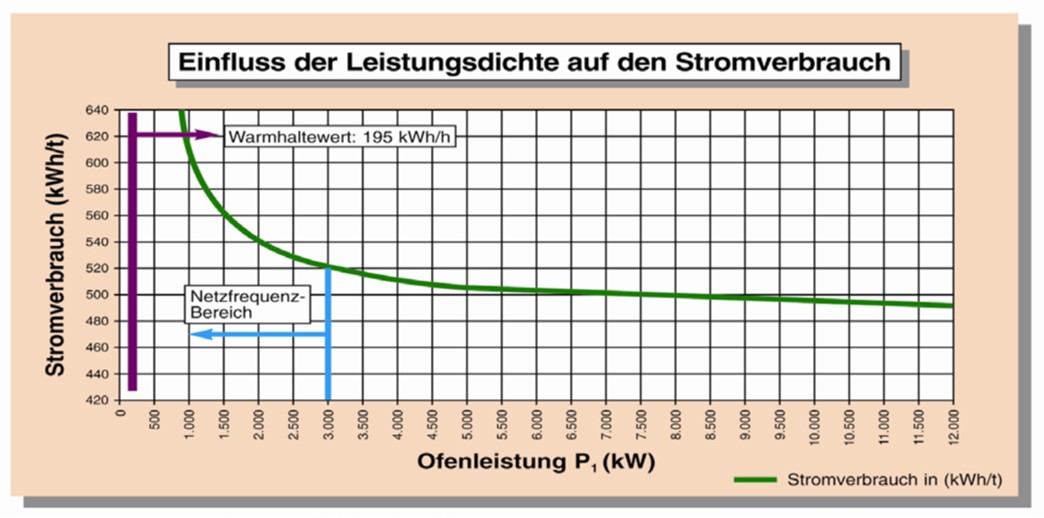
Festzuhalten ist auch, dass sich bei gleicher Leistungsdichte ein größerer Schmelzofen hinsichtlich der statischen Wärmeverluste generell günstiger verhält als ein Schmelzofen mit geringem Fassungsvermögen.
Ein 8 Tonnen Schmelzofen mit 8.000 KW verbraucht spezifisch weniger Energie als zwei parallel betriebene 4 Tonnen Schmelzofen mit jeweils 4.000 KW [48].
6. Einfluss der Betriebsweise auf den Energiebedarf
Der Einsatz der Mittelfrequenztechnik ermöglicht das Schmelzen ohne Sumpf und das Einschmelzen von kleinstückigem Material. Aufgrund der besseren elektromagnetischen Ankopplung des festen Einsatzmaterials (gilt nur für Gusseisenwerkstoffe) werden im reinen Chargenbetrieb 8 % weniger Energie benötigt, da bis zum Curiepunkt ein wesentlich höherer Spulenwirkungsgrad erreicht wird.
Dieser Vorteil kann bei der Mittelfrequenztechnik genutzt werden, da bei den Netzfrequenzanlagen nur mit einem Sumpf angefahren werden kann.
Wenn von der Netzfrequenz- auf die Mittelfrequenztechnik gewechselt wird, ergeben die höhere mögliche Leistungsdichte und der bessere Spulenwirkungsgrad im Chargenbetrieb in der Summe eine Energieeinsparung von 12 bis 15 %.
Die Speicherwärme eines Tiegelofens, d. h. die erforderliche Energie, um den kalten Ofen in den voll wärmegespeicherten Zustand aufzuheizen, ist in der Regel um den Faktor 3 bis 5 größer als der Energieaufwand für das Warmhalten über einen. vergleichbaren Zeitraum.
So beträgt die Speicherwärme bei einem 8-t-Ofen 800 kWh, d. h. für das Schmelzen einer Charge in einem kalten Ofen werden 100 kWh/t mehr Energie benötigt als zum Schmelzen in einem voll wärmegespeicherten Ofen.
Da für das Warmhalten der Schmelze pro Stunde nur 25 kWh/t erforderlich sind, also nur ein Viertel davon, macht es Sinn, bei Unterbrechungen und Pausen kleiner 4 h, den Ofen mit einem Sumpf an flüssigem Metall warm zu halten und nicht abkühlen zu lassen.
Energie wird verschwendet, wenn der Ofen länger als erforderlich mit offenem Deckel betrieben wird. Der geringe thermische Verlust von z. B. nur 140 kW bei einem 8-t-Ofen steigt dann auf 400 kW an, so dass pro Minute Öffnungszeit 4 kWh Energie zusätzlich verbraucht werden.
Bei 20 min ergibt dies immerhin 80 kWh pro Charge, entsprechend 10 kWh/t Mehrverbrauch. Unnötig Energie wird aus dem Ofen „abgesaugt", wenn die Absauganlage immer mit voller Leistung und ungedrosselt arbeitet, auch dann, wenn keine Rauchgase abzuführen sind oder nur eine geringe Menge anfällt. Der Mehrverbrauch kann in ungünstigen Fällen in einer Größenordnung von 3 % liegen. Dies entspricht 15 kWh/t Eisen.
Der nächste Punkt betrifft das Überhitzen des Eisens, da für eine Temperaturerhöhung von 50 K immerhin ca. 20 kWh/t erforderlich sind. Bei Einsatz des Schmelzprozessors JOKS kann die Endtemperatur bis auf 5 K genau eingehalten und damit eine unnötige Überhitzung vermieden werden.
Der Wirkungsgrad von Netzfrequenz-Tiegelöfen liegt nach dem Sankey Diagramm bei ungefähr 70%. Bei modernen Mittelfrequenz-Tiegelöfen können Wirkungsgrade von etwa 75% erreicht werden.
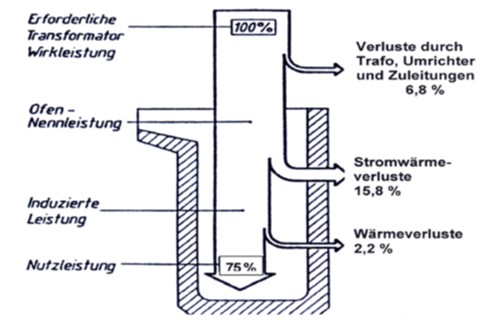
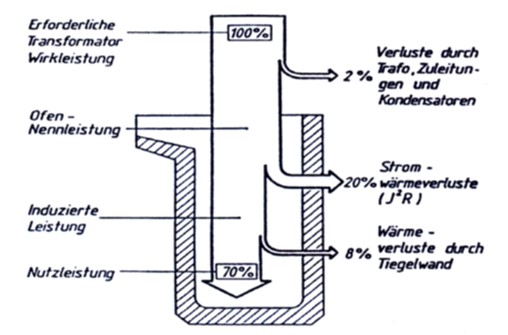
Tabelle 1: Energiebedarf, elektrische und thermische Verluste beim induktiven Schmelzen
Energiebedarf [kWh/t] | 390 |
Energieverluste [kWh/t] | |
Trafo | 7 |
Umrichter | 18 |
Zuleitungen | 9 |
Spule | 77 |
Joche | 4 |
Wärmeverluste | 11 |
Energiebedarf [kWh/t] | 516 |
Gesamtwirkungsgrad [%] | 75,5 |
7. Einfluss der Chargenzusammensetzung auf den Energiebedarf
Kenntnis über die genaue Chargenzusammen-setzung auf Basis der Analysenwerte der Einsatzstoffe, das Wissen um die genaue Dosierung der Einsatzstoffe und der entsprechenden Legierungszuschläge, einschließlich der Korrekturen zwischen Soll- und Ist-Gewicht sind Grundvoraussetzung für das Vermeiden von Zeit und Energie im Schmelzbetrieb [21].
Mit in die Betrachtung aufgenommen werden muss die Qualität der Einsatzmaterialien.
Das Chargieren von trockenem und sauberem Einsatzmaterial macht sich im Energiebedarf bemerkbar. Für das Verschlacken von Sand, der an nicht gestrahltem Kreislaufmaterial haftet, wird eine spezifische Energie von ca. 500 kWh/t verbraucht. Das entspricht in etwa der Energie, die zum Schmelzen von Eisen benötigt wird.
Bei einer realistischen Menge von 25 kg Sand pro Tonne Eisen entspricht dies einem Energiebedarf von ca. 12,5 kWh/t.
Neben den Sandanhaftungen die hinsichtlich eines erhöhten Energiebedarfs reduziert werden sollten, sollten auch verrostete Einsatzmaterialien vermieden werden.
In vergleichenden Versuchen wurden der Energiebedarf und die Chargierzeiten für das Schmelzen von sauberem und stark verrostetem Stahlschrott ermittelt.
Allerdings ist beim Autor zu hinterfragen, wie weit die Korrosion vorangeschritten sein muss, um den dargelegten Anstieg an Zeit und Energie zu verursachen.
Zurückzuführen ist der Anstieg an Zeit und Energie auf die schlechte elektromagnetische Ankopplung des Materials im Ofen.
Tabelle 2: Einfluss der Schrottqualität auf den Stromverbrauch bei 1500 °C
Einsatzmaterial | Gewicht in kg | Zeit in min | Energie in kWh/t | Verbrauch in kWh/t |
Sauberer Stahlschrott | 250 | 75 | 210 | 840 |
Rostiger Stahlschrott | 200 | 185 | 270 | 1.350 |
Rostiger Stahlschrott | 275 | 192 | 335 | 1.218 |
Selbst unter der Annahme, dass die Werte einen Extremfall darstellen, ist ein ungünstiger Einfluss von verrostetem Einsatzmaterial nachweisbar.
Neben dem höheren Energiebedarf beim Einsatz von verrosteten Einsatzmaterialien wirken sich negativ der höhere Abbrand und die größere Schlackenmenge aus, so dass von einem Einsatz verrosteter Einsatzmaterialien vermieden werden sollte.
7. Einfluss der Packungsdichte auf den Energiebedarf
Den Einfluss der Packungsdichte des Chargier-gutes auf den Energiebedarf wurde unter Produktionsbedingungen an einer Mittelfrequenzschmelzanlage untersucht.
Die Mittelfrequenzschmelzanlage hat ein Fassungsvermögen von 10 Tonnen und eine Nennleistung von 8.000 KW bei 250 Hz.
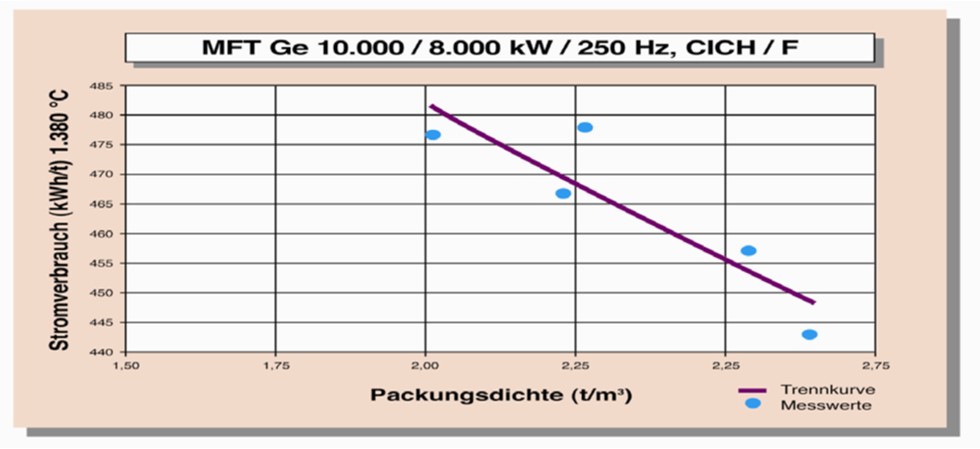
Der leere Ofen wurde mit einer festgelegten Chargenzusammensetzung aus Roheisen, Gussbruch, Kreislaufmaterial, Stahlschrott und Zuschlagstoffen einmal gefüllt. Dann wurde nach [21] ohne Nachchargieren bis auf 1380 °C aufgeschmolzen und der Energiebedarf ermittelt.
Durch unterschiedliche Abmessungen des Kreislaufmaterials und des Stahlschrottes ergaben sich Packungsdichten im Bereich von 2 t/m³ bis 2,7 t/m³. Die Ergebnisse sind in Abbildung 5 festgehalten:
- Mit abnehmender Packungsdichte des Einsatzmaterials steigt der Stromverbrauch
- Mehrverbrauch von 25 kWh/t bei Senkung der Packungsdichte von 2,5 auf 2,0 t/m³
Unter Berücksichtigung des beschriebenen Sachverhaltes ist es empfehlenswert, sperriges Einsatzmaterial zu zerkleinern, um eine höhere Packungsdichte zu erreichen.
Mit der Zerkleinerung des Einsatzmaterials wird auch gleichzeitig das Chargieren vereinfacht und die Gefahr der Brückenbildung im Schmelzofen verringert.
8. Einfluss von Spänen auf den Energiebedarf
Bei der zerspanenden Bearbeitung von Gussbauteilen fallen Späne an, die sich zum Einschmelzen, möglichst im eigenen Schmelzbetrieb, eignen. Besonders gut als Schmelzaggregat geeignet ist der Induktions-Tiegelofen.
Besonders Späne aus Gusseisen mit Lamellengraphit, im Allgemeinen fallen diese ohne den Einsatz von Kühlschmierstoffen an, können ohne größere Vorbehandlung eingeschmolzen werden.
Späne weisen nach [21], bedingt durch ihre geringe Berührungsoberfläche und die oberflächliche Oxidation, trotz der guten Packungsdichte untereinander nur einen schlechten elektrischen Kontakt auf. Beim Schmelzen von Spänen sollte daher immer mit einem Sumpf größer 40 % gearbeitet werden.
Bei einer Fahrweise ohne Sumpf ist mit einem zusätzlichen Energiebedarf von 50 kWh/t für das Einschmelzen gegenüber stückigem Einsatzmaterial zu rechnen. Auch verlängert sich nach [21] die Schmelzzeit.
Das vollständige Füllen des Schmelzofens spart 2 % bis 3 % Energie und senkt den Abbrand. Dabei ist eine Brückenbildung des Einsatzmaterials zu vermeiden.
9. Einfluss von Aufkohlungsmittel auf den Energiebedarf
Die Art und Weise der Zugabe von Aufkohlungsmittel hat Einfluss auf den Energiebedarf.
Nach Aussage von [21, 36] ergibt sich ein deutlicher Mehrverbrauch an Energie, wenn das Aufkohlungsmittel nicht am Anfang des Schmelzvorganges zusammen mit den metallischen Einsatzstoffen eingesetzt wird, sondern erst nach dem Aufschmelzen in das flüssige Bad eingebracht wird.
Erfahrungen aus Versuchsreihen, gefahren im Hause der Otto Junker GmbH, gehen davon aus, dass im letzteren Fall ca. 1 bis 2 kWh/kg Kohlungsmittel zusätzlich erforderlich sind.
Bei einer Zugabe von 2 % Aufkohlungsmittel sind etwa 40 kWh/t Eisen an Mehrverbrauch zu erwarten.
10. Einfluss der Zustellung auf den Energiebedarf
Die Wanddicke der keramischen Zustellung des Ofens – beim Schmelzen von Gusseisen kommen fast ausschließlich Quarzitmassen zum Einsatz – stellt immer einen Kompromiss zwischen einer hohen thermischen Isolierung sowie einem ausreichenden mechanischen Schutz der Spule und einer guten elektromagnetischen Kopplung zwischen Spule und Schmelzgut dar.
Im Rahmen durchgeführter Untersuchungen wurde bei abnehmender Zustelldicke eine deutliche Reduzierung des Stromverbrauches festgestellt. Mit zunehmender Betriebszeit und damit zunehmender Auswaschung der Zustellung sinkt der Stromverbrauch nach 3 Wochen um fast 10 %.
Tabelle 2: Zusammenhang zwischen Verschleißgrad der Zustellung und Stromverbrauch
Leistungsaufnahme in kW | Stromverbrauch in kWh/t | Energievergleich in % | |
Neue Zustellung | 615 | 656 | 100 |
Betriebszeit 1 Woche | 650 | 622 | 95 |
Betriebszeit 3 Wochen | 750 | 598 | 91 |
Der Einfluss der Zustelldicke auf den Spulenwirkungsgrad geht aus Abbildung 6 hervor.
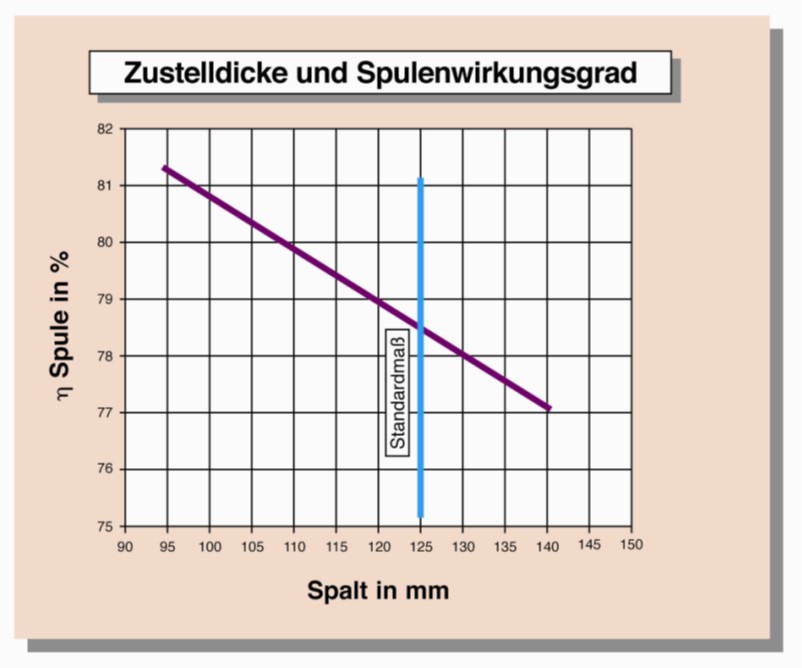
Abbildung 6 verdeutlicht, dass mit abnehmender Dicke der keramischen Zustellung der Spulenwirkungsgrad verbessert wird und eine Senkung des Energiebedarfes eintritt.
Aus dem Zusammenhang zwischen Wanddicke der Zustellung des Ofens und dem Stromverbrauch leitet sich die Überlegung ab, ob mit dem Einsatz eines modernen Tiegel-Überwachungssystems, zum Beispiel des Optical Coil Protection Systems „OCP“ nicht auf einen zu hohen Sicherheitszuschlag für die Zustellung verzichtet werden kann.
Das Tiegel-Überwachungssystem führt mit hoher Geschwindigkeit eine ständige lokale Temperaturmessung in der Tiegelwand durch.
Durch die Auswertung der Messungen des Tiegel-Überwachungssystems können der Verschleißzustand des feuerfesten Futters an unterschiedlichen Stellen des Tiegels exakt bestimmt werden und lokale Risse und Auswaschungen detektiert werden.
11. Zusammenfassung der Energieaspekte bei Induktions-Tiegelöfen
- Der tatsächliche durchschnittliche Energieeinsatz zum Schmelzen von Gusseisen bietet Potential zum Einsparen von Energie.
- Der Energiebedarf von Hilfs- und Nebenaggregaten beläuft sich auf ca. 2 %, bezogen auf den Energiebedarf zum Schmelzen.
- Einsatz moderner Prozessleittechnik. Mit Hilfe des automatisierten rechnergestützten Betriebs des Schmelzprozesses lassen sich Energieeinsparungen realisieren.
- Der Einsatz von rostigem Schrott und nicht gereinigtem Kreislaufmaterial erhöht den Energiebedarf.
- Für die Reduzierung des Energiebedarfes ist es empfehlenswert, sperriges Einsatzmaterial zu zerkleinern, um eine hohe Packungsdichte zu erreichen.
- Das Aufkohlungsmittel ist unter Beachtung einer metallurgisch sinnvollen Chargierfolge zu setzen. Ein deutlicher Mehrverbrauch an Energie ist zu verzeichnen, wenn das Aufkohlungsmittel nicht am Anfang des Schmelzvorganges zusammen mit den metallischen Einsatzstoffen eingesetzt wird, sondern erst nach dem Aufschmelzen in das flüssige Bad eingebracht wird.
- Späne weisen, bedingt durch ihre geringe Berührungsoberfläche und die oberflächliche Oxidation trotz der guten Packungsdichte untereinander nur einen schlechten elektrischen Kontakt auf. Beim Schmelzen von Spänen sollte daher immer mit einem Sumpf größer 40 % gearbeitet werden. Bei Mittelfrequenz-Induktionsöfen ist das Anfahren mit stückigem Einsatzmaterial ohne Sumpf möglich.
- Der Schmelzofen sollte, im Zuge eines günstigen Energiehaushaltes, mit der maximal verfügbaren Leistung gefahren werden.
- Der Ofendeckel ist geschlossen zu halten. Die Absauganlagen sind entsprechend der Emissionsmengen anzupassen.
- Bei Unterbrechungen des Schmelzbetriebes < 4 Stunden ist der Schmelzofen warmzuhalten, da das Kaltanfahren 3 – 4 mal mehr an Energie benötigt, wie das Warmhalten.
- Exakte Temperaturführung im Ofen durch Einsatz des Schmelzprozessors (JOKS).
- In Verbindung mit dem Einsatz moderner Tiegelüberwachungssysteme, z. B das „ Optical Coil Protection-System“ (OPC), ist die Dicke der feuerfesten Zustellung zu optimieren und auf unnötige Sicherheitszuschläge zu verzichten.
- Bei Einsatz des neu entwickelten Energiesparsystems kann eine Senkung des Stromverbrauches zwischen 5 und 10 % erreicht werden.
Quellen:
[4] VDI Berichte 1057;Elektrische Prozesswärme für Aluminium, Gusseisen und Stahl; VDI-Verlag GmbH Düsseldorf 1993
[7] F. Neumann, Gusseisen - Schmelztechnik, Metallurgie, Schmelzbehandlung, 1999, Expert Verlag, S. 186
[21] Dietmar Trauzeddel; Einfluss der Betriebs- und Fahrweise auf den Energieverbrauch beim induktiven Schmelzen von Gusseisen; Giesserei 93; 04/2006
[24] R. Donnerbauer, Frankenberg; Kostenfaktor Energie; Stromkosten sparen mit gezieltem Energiemanagement; Giesserei 93; 10/2006
[36] W.Schmitz; D.Trauzeddel; Energieeinsparpotential beim induktiven Schmelzen von Gusseisenwerkstoffen; Gießerei 95; 06/2008
[37] Sicheres und energiesparendes Schmelzen im Mittelfrequenz-Tiegelofen; Otto Junker GmbH; 2005
[48] GP-Special;Otto Junker; 1-2/2007