Effizienzoptimierter Betrieb von Drehtrommelöfen
Von Kai Bloemen, Felix Ebersold und Jens Hesselbach, Kassel
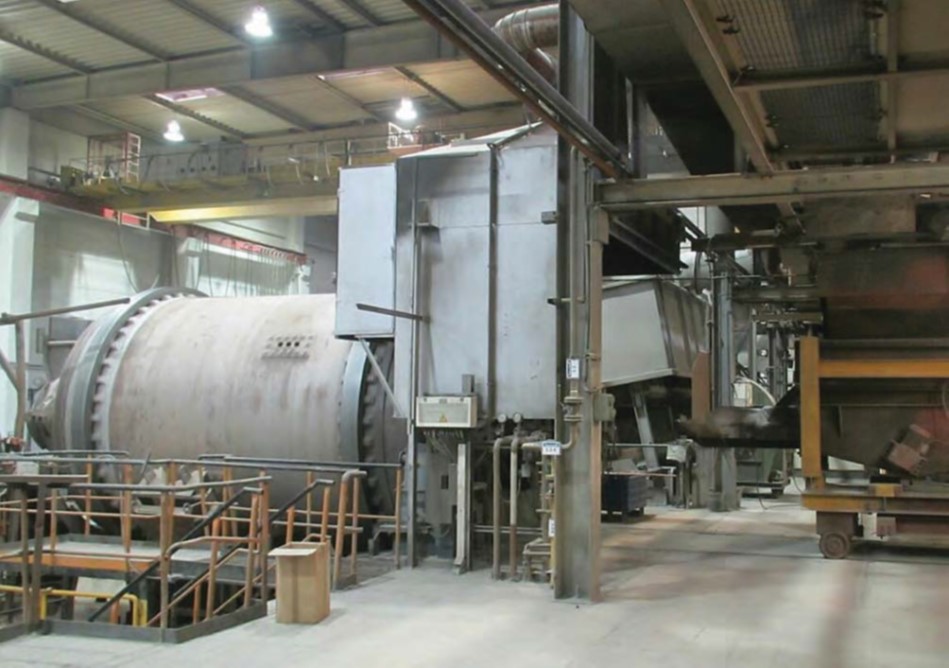
Drehtrommelofen
Erschienen in GIESSEREI 05/2017
egen der hohen Qualität und des vergleichsweise geringen Energiebedarfs liegt der Anteil des Sekundäraluminiums an der gesamten Aluminiumerzeugung in Deutschland bei über 50 % [1]. Aufgrund der steigenden Nachfrage müssen auch Vorstoffe mit hohem Anteil organischer Anhaftungen recycelt werden. Stark verunreinigte Vorstoffe werden ohne thermische Vorbehandlung in Drehtrommelöfen mithilfe von Abdecksalzen geschmolzen. Der Schmelzprozess verunreinigter Vorstoffe ist deutlich komplexer als der von Neuschrotten. Da eine Kenntnis über die genaue Zusammensetzung und die Schüttdichte der Vorstoffe mit vertretbarem Aufwand nicht erlangt werden kann, ist ein Betrieb der Schmelzöfen mit festen Parametern nicht durchführbar. Der Prozess wird im laufenden Betrieb den Vorstoffen angepasst [2]. Aufgrund der Konstruktion der Öfen, der heißen Ofenatmosphäre, korrosiver Abgase und den in der Trommel rollierenden Vorstoffen stehen den Ofenbedienern zur Bestimmung des Schmelzzustandes kaum messtechnische Hilfsmittel zur Verfügung. Wegen der Schüttdichte der Vorstoffe und der begrenzten Kapazität des Ofens muss eine Charge in mehreren Teilchargen in den Ofen eingebracht werden. Hierbei hat der Zeitpunkt des Chargierens einen wesentlichen Einfluss auf den Prozess. Die Wahl der Chargierzeitpunkte erfolgt häufig durch eine visuelle Beurteilung des Schmelzgutes. Wird der Chargierzeitpunkt zu früh gewählt, ist die Kapazität im Ofen zu gering, um eine neue Teilcharge einzubringen. Der Ofen muss geschlossen und zu einem späteren Zeitpunkt erneut geöffnet werden. Die Wärmeverluste steigen und die Prozesszeit verlängertsich. Wird der Zeitpunkt zu spät gewählt, ist das im Ofen befindliche Schmelzgut sehr heiß. Dadurch verbrennen organische Anhaftungen der nächsten chargierten Altschrotte unkontrolliert und die Abgasbelastung nimmt zu.
Die diesem Beitrag zugrunde liegende Arbeit zeigt eine Methodik auf, die Bedienung des Schmelzofens messtechnisch zu unterstützen, um so den optimalen Zeitpunkt zum Chargieren reproduzierbar bestimmen zu können. Zunächst werden die notwendigen Grundlagen und der Prozess im Ist-Zustand beschrieben. Darauf aufbauend folgen die Beschreibung der entwickelten Methodik und deren praktische Anwendung.
Grundlagen und Ist-Zustand
Ein starrer Drehtrommelofen besteht aus einer großen Stahltrommel, die sich liegend um die eigene Achse dreht. Mit zwei umspannenden Laufringen liegt die Trommel auf Rollvorrichtungen auf, über die sie mithilfe eines elektrischen Antriebs in eine Drehbewegung versetzt wird. Zur Verringerung der Oxidation und zum Auflösen bzw. zur Aufnahme organischer Anhaftungen findet das Schmelzen mithilfe von Abdecksalzen statt [2]. Damit die Funktion des Abdecksalzes gewährleistet ist, wird es vor den Vorstoffen chargiert und geschmolzen.
Der Ofenbetrieb wird durch die Einstellung der Maschinenparameter, die Chargenzusammensetzung, die Wahl der Chargierzeitpunkte, die Beachtung des Verhaltens der Vorstoffe im Ofen sowie das Ablassen der Schmelze und der Salzschlacke beeinflusst. Bild 1 zeigt den schematischen Aufbau eines Drehtrommelofens.
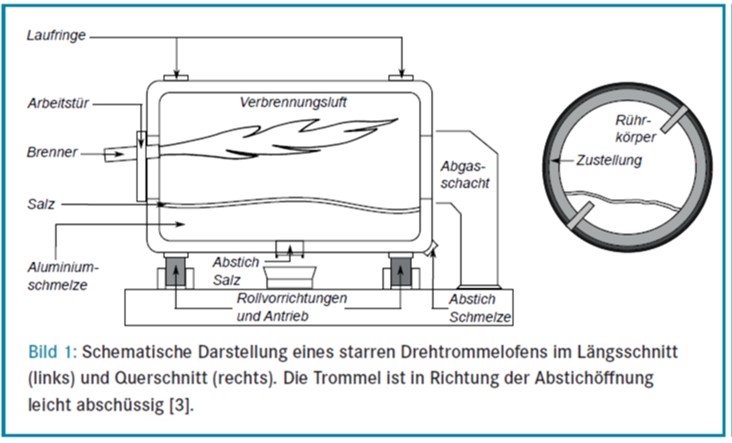
Um bei der Herstellung einer Aluminiumlegierung aus Altschrotten eine hohe Produktivität bei effizienter Energieausnutzung und geringem Salzverbrauch gewährleisten
zu können, werden in der Literatur folgende Leitsätze angegeben [2]:
- Vorstoffe so schnell wie möglich chargieren und einschmelzen,
- möglichst schnelle Bedeckung der Vorstoffe mit Abdecksalz,
- Anpassung der Reihenfolge und Zeitpunkte der Teilchargen nach ihrer Oxidationsneigung und ihrem Einschmelzverhalten,
- Türöffnungszeiten so gering wie möglich halten und
- Vermeidung von unnötigem Überhitzen und Flüssighalten der Schmelze.
Die im Schmelzwerk verarbeiteten Vorstoffchargen setzen sich aus einer Kombination von Altschrotten mit organischen Anhaftungen sowie Neuschrotten ohne organische Anhaftungen zusammen. Für die durchgeführte Untersuchung wurde eine Mustercharge, basierend auf der am häufigsten verwendeten Chargenzusammensetzung, festgelegt. Der Gewichtsanteil der Altschrotte liegt bei 50 %. Die Altschrotte sind größtenteils Bleche mit niedriger Schüttdichte und variierendem Anteil organischer Anhaftungen. Die Neuschrotte bestehen überwiegend aus Kreislaufmaterial der angeschlossenen Gießerei. Je nach Beschaffenheit der Vorstoffe werden die Chargen in 8 bis 10 Teilchargen zu je 1,3 bis 2 t aufgeteilt.
Das Einbringen der Teilchargen erfolgt so schnell wie möglich. Nach dem Einbringen einer Teilcharge befinden sich die Vorstoffe im vorderen Bereich des Ofens (siehe Bild 2). Bevor eine weitere Teilcharge chargiert werden kann, müssen die im Ofen befindlichen Vorstoffe in den hinteren Teil der Trommel gefördert werden.
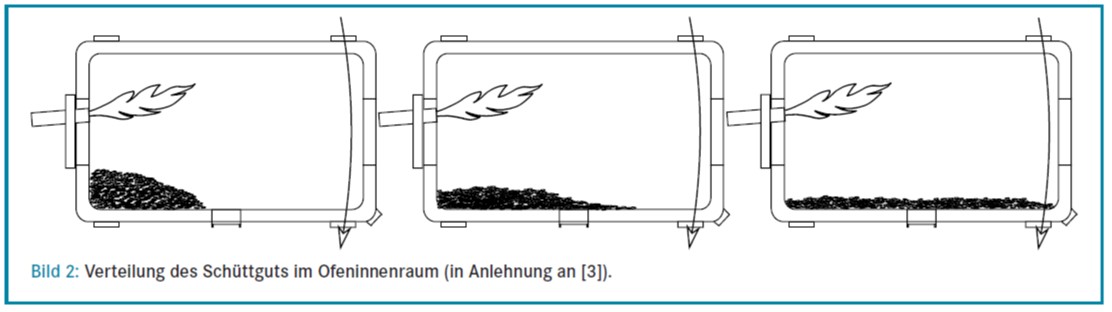
Bei allen Teilchargen ist ein unkontrolliertes Abbrennen bzw. ein zu schnelles Verbrennen unter Sauerstoffmangel der Fremdstoffe zu vermeiden. Dazu wird der Ofen bei niedriger Umdrehungsgeschwindigkeit und möglichst geringer Arbeitstemperatur, d. h. niedrigem Energieeintrag durch den Brenner, betrieben. Um eine zu hohe Konzentration von Schadgasen zu vermeiden, wird das Abgas emissionstechnisch überwacht. Das Einbringen weiterer Vorstoffe erfolgt erst, wenn alle organischen Fremdstoffe der im Ofen befindlichen Vorstoffe thermisch entfernt wurden. Dadurch wird zusätzlich ein Sauerstoffmangel im Ofeninnenraum vermieden, der durch ein zu schnelles Abbrennen großer Mengen organischer Bestandteile entsteht.
Die Kapazität des Ofens ist aufgrund der geringen Schüttdichte der Altschrotte nach dem Einbringen von ca. 5 bis 7 Teilchargen ausgelastet. Die folgenden Teilchargen können erst eingebracht werden, wenn die Vorstoffe in sich zusammengesackt sind. Dieser Punkt der Volumenreduzierung wird aufgrund von Erfahrungswerten der Mitarbeiter bzw. einer visuellen Beurteilung des Schmelzgutes bei geöffneter Arbeitstür bestimmt. Nach dem Einbringen aller Teilchargen werden die Vorstoffe auf Schmelztemperatur erhitzt, geschmolzen und für den Transport sowie die weitere Verarbeitung überhitzt. Nachdem die gewünschte Temperatur erreicht ist, werden die Schmelze in einen Tiegelofen und die Salzschlacke in einen Auffangkübel abgeführt.
Der beschriebene Prozess ist im Ausgangszustand sehr energieintensiv und kaum reproduzierbar. Bild 3 zeigt die Ofenreisedauer für 24 Chargen mit Altschrottanteilen zwischen 35 und 60 %. Die Dauer der Ofenreisen beträgt zwischen 4,1 und 7,5 h. Der Energiebedarf variiert zwischen 400 und 800 kWh/t Legierung. Neben einer
schwankenden Ausbringung ist die große Streuung der Prozesszeit auch für die Versorgung der nachgelagerten Druckgießanlagen mit Aluminiumschmelze problematisch.
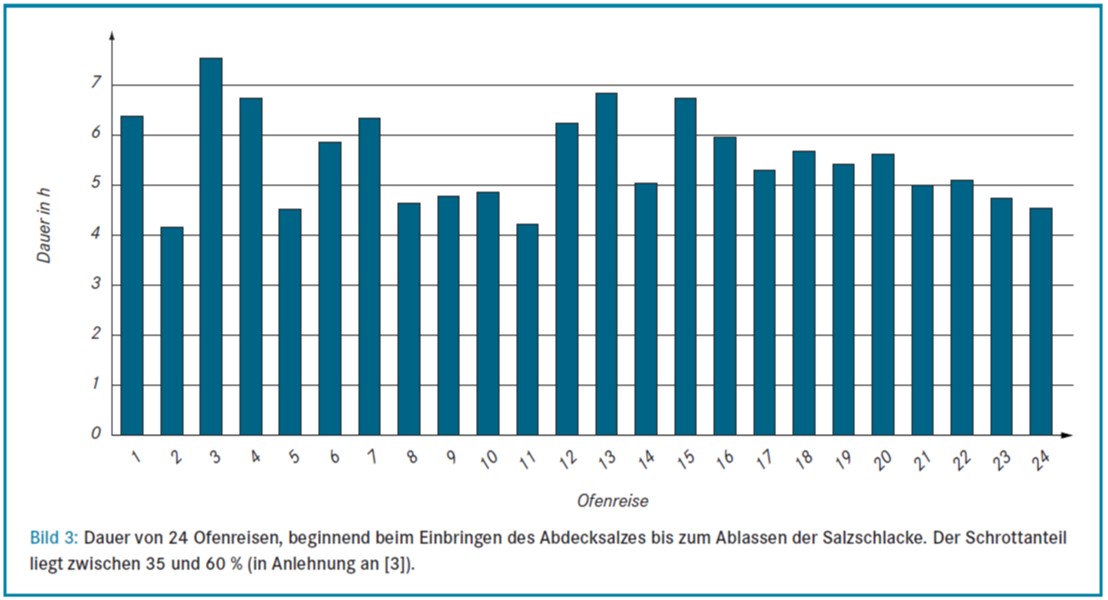
Untersuchung
Das Chargieren der Vorstoffe aufgrund von Erfahrungswerten und visueller Beurteilung hat sich in der Praxis als Methodeerwiesen, die trotz nicht vorhandener messtechnischer Überwachung in Bezug auf Prozessdauer und Schmelzertrag zu guten Ergebnissen führt. Diese Vorgehensweise setzt neben einem tiefen Prozessverständnis ein häufiges Öffnen des Schmelzofens voraus. Durch die kontinuierliche Entlüftung kommt es bei geöffneter Arbeitstür zu einem alschluftvolumenstrom, der den Ofen durchströmt und Wärme über das Abgas aus dem Ofen transportiert.
Weiterhin kann es aufgrund eingeschränkter messtechnischer Überwachung zu einer ineffizienten Wahl der Chargierzeitpunkte kommen. Wenn der Chargierzeitpunkt zu früh gewählt wird, ist nicht ausreichend Volumen im Ofen vorhanden, um die nächste Teilcharge aufzunehmen. Der Ofen muss geschlossen und zu einem späteren Zeitpunkt erneut geöffnet werden.
Zur Lösung dieser Problemstellung soll eine Messgröße ermittelt werden, die zur nicht-invasiven Beurteilung des Schmelzzustandes geeignet ist. Dadurch können
eine effiziente Bestimmung der Chargierzeitpunkte bei geschlossener Arbeitstür erfolgen und eine Reduzierung der Türöffnungszeit sowie der Prozessdauer erreicht
werden.
Aufgrund von Verweisen in [1, 4, 5] wurden die Parameter Abgastemperatur, Temperatur der Ofenhülle und Leistungsaufnahme des Trommelantriebs auf Eignung
zur nicht-invasiven Beurteilung geprüft. Theoretisch ist die Bestimmung der Temperatur des Aluminiums bzw. der vom Aluminium aufgenommen Energie anhand der Temperatur des Abgases oder der Ofenhülle möglich. Werden die ein- und ausgehenden Energieströme bilanziert, ergeben sich die im Ofen verbleibende Energie sowie die Temperatur des Aluminiums. Praktisch ist diese Methode jedoch aus den folgenden Gründen nur bedingt umsetzbar:
- Die genaue Zusammensetzung der Vorstoffe, insbesondere der Anteil organischer Fremdstoffe, die je nach Schrottsorte einen hohen Energiegehalt aufweisen (Farben, Lacke, Öle, Papier, Polymere, vgl. [7]), ist unbekannt.
- Die Ofenwand unterliegt durch fortlaufenden Kontakt mit Abdecksalzen und Vorstoffen einem kontinuierlichen Verschleiß, wodurch sich der Wärmedurchgang durch die Ofenwand ständig, aber nicht gleichmäßig über die gesamte Fläche des Mantels verändert [3].
- Der Ofen ist gegenüber seiner Umgebung nicht abgedichtet. Über die Ofentür und einen Ringspalt zwischen Trommel und Abgaskanal wird ein unbekannter Falschluftstrom ins System eingebracht [3].
Demnach wird die genaue Beurteilung des Schmelzzustandes aufgrund der Energiebilanz für das vorliegende System als ungeeignet bewertet.
Die Bestimmung der Aufnahme der elektrischen Leistung des Trommelantriebs ist mit geringem messtechnischem Aufwand verbunden und wird nicht direkt von den thermischen Vorgängen im Ofen beeinflusst. Die zur Bewegung der Trommel notwendige Energie ist von der Umdrehungszahl, der Vorstoffmasse und dem Zustand des Vorstoffes in der Trommel abhängig [3]. Um die Eignung für eine Bestimmung der Chargierzeitpunkte zu prüfen, wurden Untersuchungen an einem Drehtrommelofen während des Schmelzprozesses durchgeführt und alle relevanten Größen messtechnisch erfasst. Bild 4 stellt die Abhängigkeit der Leistungsaufnahme des Ofenantriebs
(graue Kurve) von der Vorstoffmasse, der Drehgeschwindigkeit (rote Kurve) und des Aggregatzustandes der Vorstoffe dar.
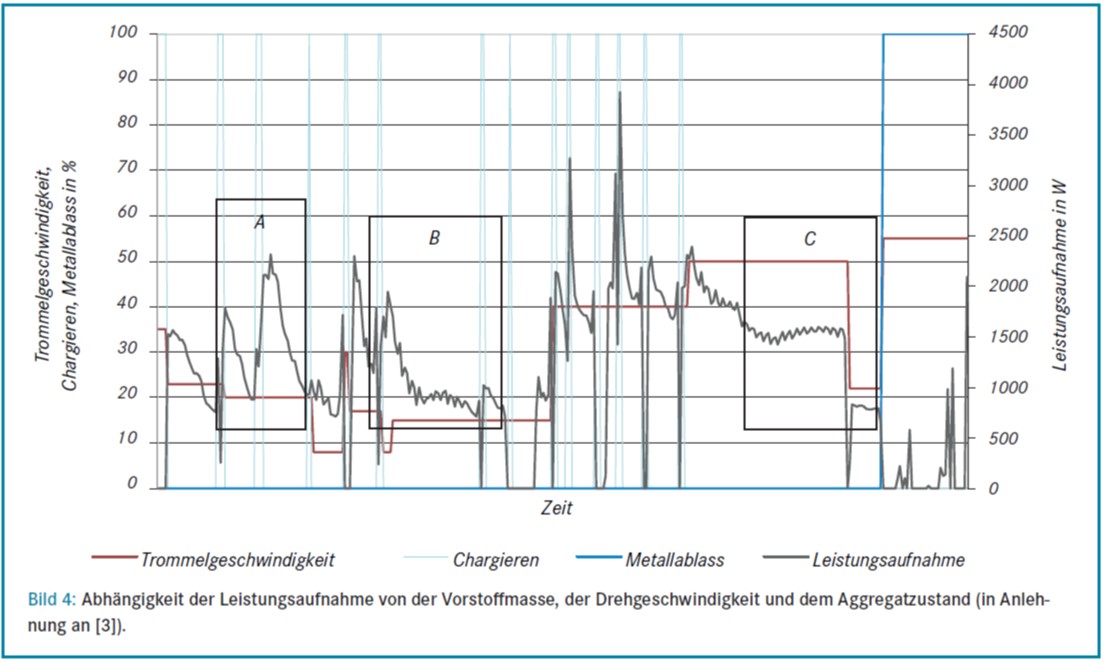
In Bereich A ist zunächst ersichtlich, dass beim Einbringen der Teilchargen (hellblaue Linie) die Leistungsaufnahme ohne den Einfluss anderer Mechanismen steigt. In Bereich C lässt sich der Einfluss der Drehgeschwindigkeit erkennen. Bei einer Verringerung der Drehgeschwindigkeit verringert sich die Leistungsaufnahme.
Der Einfluss des Aggregatzustandes der Vorstoffe ist u. a. in Bereich B ersichtlich. Die ungeschmolzenen Vorstoffe reiben an der Ofenwand und den Rührkörpern. Beim Übergang von der festen in die flüssige Phase sinkt der Reibungswiderstand zwischen Ofenwand und Aluminium. Bei gleicher Masse muss wenigerEnergie aufgewendet werden, um die Trommel zu bewegen. Mit steigendem Anteil flüssiger Legierung wird die Abnahme der Leistungsaufnahme geringer. Auch nach vollständigem Übergang der Vorstoffe in die flüssige Phase sinkt die Leistungsaufnahme so lange, bis die Schmelze die in Bezug auf den Energieeintrag maximal mögliche Temperatur erreicht hat. Dieser Zusammenhang beruht auf der Temperaturabhängigkeit der Viskosität der Schmelze [6]. Um eine flexible Wahl der Vorstoffzusammensetzung zu ermöglichen, berücksichtigt die entwickelte Methode den Verlauf der Leistungsaufnahme. Demnach wird zunächst ein Leistungsbereich ermittelt, der in Bezug auf den Schmelzzustand auf einen optimalen Chargierzeitpunkt hinweist. Dieser Bereich ergibt sich aufgrund der Zeitpunkte, zu denen die Mitarbeiter, basierend auf der visuellen Beurteilung der Schmelze, den Zustand der Schmelze und des Ofens als optimal zur Aufnahme der nächsten Teilcharge bewerten. Er liegt bei einer Abnahme der Leistung zwischen 30 und 50 % [3]. Dieser relativ große Leistungsbereich erleichtert die praktische Anwendung. Auf Basis dieses Leistungsbereiches wurden Pilotofenreisen durchgeführt, bei denen das Chargieren aufgrund der Abnahme der Leistung erfolgte. Bild 5 zeigt den untersuchten Drehtrommelofen und den Verlauf der Leistungsaufnahme inklusive des empfohlenen Leistungsbereiches.
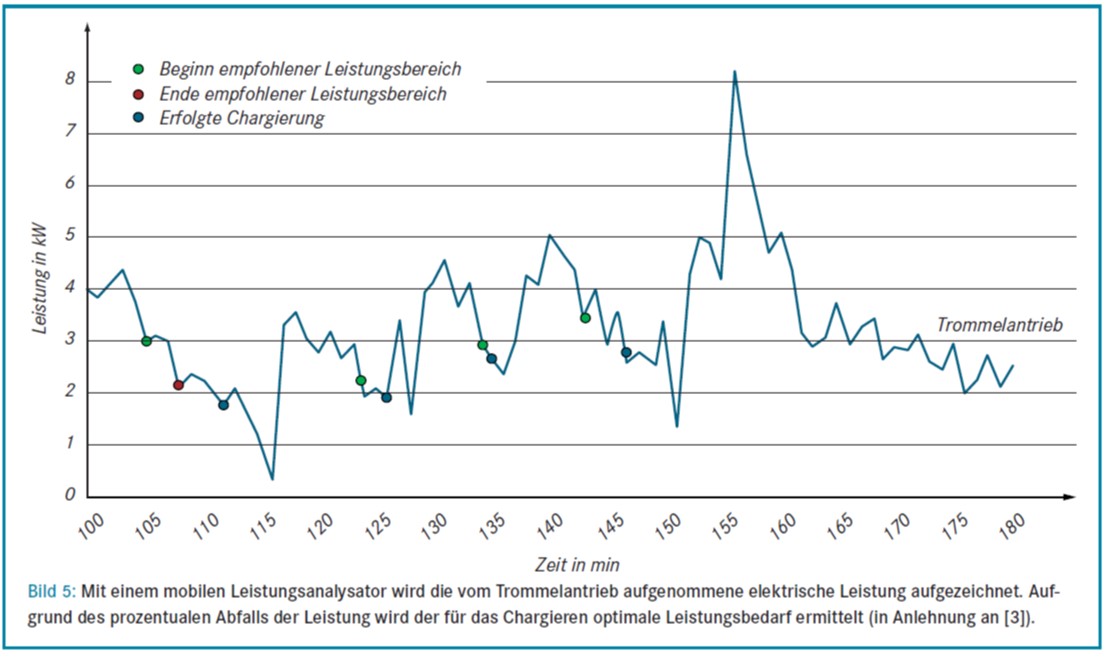
Die Leistungsaufnahme wurde im Verlauf der Ofenreise überwacht. Das Chargieren der Teilchargen 1 bis 6 erfolgte aufgrund der visuellen Beurteilung des Abgases und der Emissionsüberwachung. Der Verlauf der elektrischen Leistung in Bild 5 beginnt bei der siebten Teilcharge. Bei einer Abnahme um jeweils 35 % wurde der Mitarbeiter informiert, dass laut Leistungsaufnahme die nächste Teilcharge eingebracht werden kann (Bild 5, grüne Punkte). Die visuelle Beurteilung des Schmelzzustandes durch einen erfahrenen Ofenfahrer diente als Verifikation, ob der Zustand der Schmelze zum Einbringen weiterer Vorstoffe geeignet ist. Das Chargieren (Bild 5, blauer Punkt) erfolgte bei der vierten Teilcharge kurz nach und bei den drei folgenden innerhalb des zuvor theoretisch bestimmten optimalen Bereichs (Bild 5, der optimale Bereich liegt zwischen dem grünen und dem roten Punkt).
Mit der praktischen Untersuchung konnte die Annahme, dass bei einer Abnahme der elektrischen Leistung zwischen 30 und 50 % das Volumen der Vorstoffe weit genug verringert ist, um eine neue Teilcharge aufzunehmen, verifiziert werden. Weiterhin wurde verdeutlicht, dass das leistungsabhängige Chargieren eine geeignete Methode zur Wahl der Chargierzeitpunkte und analog der Reduzierung der Ofenreisedauer und Türöffnungszeiten ist.
Zur Anwendung der entwickelten Methodik wurde ein Drehtrommelofen umgerüstet. Der Verlauf der elektrischen Leistung wird über einen nachgerüsteten Leistungsanalysator aufgenommen und auf einem Monitor am Bedienfeld des Ofens ausgegeben. Je nach Abnahme der elektrischen Leistung wird dem Ofenbediener signalisiert, ob sich der Ofen im optimalen Leistungsbereich befindet. Zur Bestimmung des Potenzials in Bezug auf eine Reduzierung des Energiebedarfs und einer Produktivitätssteigerung wurden weitere Ofenreisen durchgeführt. Die Ergebnisse werden im Folgenden dargestellt.
Ergebnisse
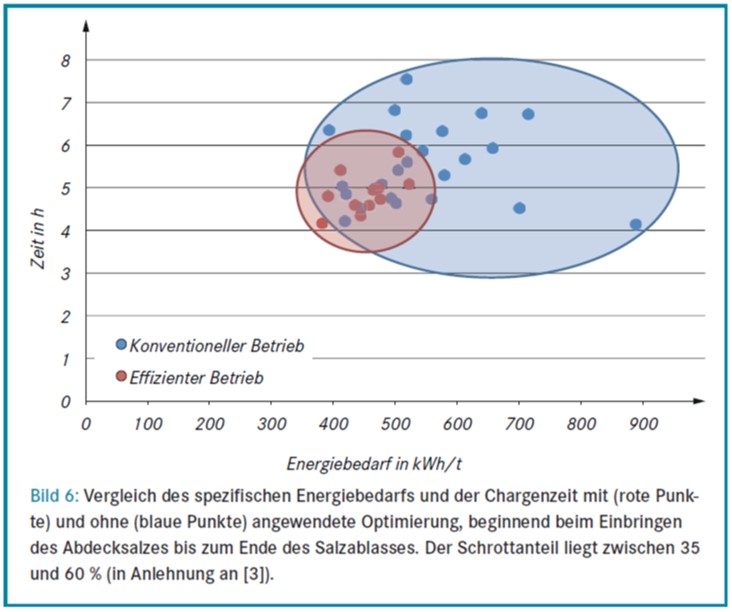
Die Messdaten von 24 Ofenreisen mit konventioneller Vorgehensweise wurden mit Daten von 9 Ofenreisen verglichen, die nach der leistungsorientierten Methodik durchgeführt wurden. Ofenreisen mit längeren Standzeiten durch materialflussbedingte Störungen wurden nicht mit in den Vergleich einbezogen. Bild 6 zeigt die Ergebnisse für die Dauer der Ofenreisen und den Energiebedarf im Vergleich.
In Bezug auf die konventionelle Methodik betrug die Dauer im Schnitt 5,5 h bei einem spezifischen Energiebedarf von 540 kWh/t Legierung. Aufgrund der leistungsorientierten Vorgehensweise konnten die Ofenreisedauer auf durchschnittlich 4,6 h und der Energiebedarf auf 440 kWh/t Legierung gesenkt werden. Dies entspricht einer Verringerung der Prozessdauer um 16,3 % sowie einer Senkung des spezifischen Energiebedarfs um 18,5 %. Darüber hinaus konnte die Streuung der Chargenzeiten deutlich verringert werden. Bild 6 veranschaulicht dies über die farbigen Flächen. Eine geringere Streuung vereinfacht die Abstimmung zwischen dem Schmelz- und seinem Folgeprozess. Eine ausführlichere Darstellung sowie weitere Ergebnisse können [3] entnommen werden.
Zusammenfassung
Mit dem leistungsabhängigen Chargieren wurde eine Methode entwickelt, die eine nicht-invasive Beurteilung des Schmelzzustandes im Drehtrommelofen und damit einhergehend eine Verringerung der Ofenreisedauer und des Energiebedarfs ermöglicht. Zur Herleitung dieser Methode wurden verschiedene Ofenreisen beobachtet und analysiert. Aufgrund der Beschaffenheit der Vorstoffe und der begrenzten Kapazität des Ofens müssen die Vorstoffe in mehreren Teilchargen in den Ofen eingebracht werden. Dabei stellte sich heraus, dass die Mitarbeiter die Chargierzeitpunkte aufgrund einer eingeschränkten messtechnischen Überwachung mithilfe ihres Erfahrungswissens und einer visuellen Beurteilung des Schmelzgutes wählen. Diese Vorgehensweise ist insbesondere beim Schmelzen von Altschrotten kaum reproduzierbar. Infolgedessen variieren Dauer und Energiebedarf einzelner Ofenreisen teilweise erheblich.
Bei der Untersuchung verschiedener Ofenparameter wurde die Abhängigkeit der Leistungsaufnahme des Trommelantriebs von der im Ofen befindlichen Vorstoffmasse, der Drehgeschwindigkeit und dem Aggregatzustand der Vorstoffe ersichtlich. Aufgrund dieser Erkenntnis wurde ein Leistungsbereich ermittelt, der in Bezug auf den Schmelzzustand auf einen effizienten Chargierzeitpunkt hinweist. Dieser liegt bei einer Abnahme der Leistung des Ofenantriebs zwischen 30 und 50 %. Zur Verifikation wurden Versuche durchgeführt, bei denen der Chargierzeitpunkt aufgrund der Leistungsaufnahme gewählt wurde. Der optimale Chargierzeitpunkt konnte ohne ein Öffnen des Ofens reproduzierbar bestimmt werden. Es kam zu einer durchschnittlichen Verringerung der Ofenreisedauer um 16,3 %. Der Energiebedarf konnte um 18,5 % gesenkt
werden.
M.Sc. Kai Bloemen, Dipl.-Wirtsch.-Ing. M.Sc. Felix Ebersold, Prof. Dr. Jens Hesselbach, Fachgebiet Umweltgerechte Produkte und Prozesse, Universität Kassel
Literatur:
[1] WVM. n. d.: Produktion von Primär- und Sekundäraluminium in Deutschland in den Jahren 2006 bis 2015 (in 1000 Tonnen). Statista. Zugriff am 14. November 2016.
Verfügbar unter https://de.statista.com/statistik/daten/studie/197960/umfrage/produktion-von-primaer-und-sekundaeraluminium-in-deutschland/.
[2] Krone, K.: Aluminium-Recycling. Vom Vorstoff bis zur fertigen Legierung. Aluminium-Verlag, Düsseldorf, 2000.
[3] Bloemen, K.: Klima- und energieeffiziente Bereitstellung von Flüssigaluminium für den Druckgießprozess. Dissertation, Universität Kassel, 2017.
[4] Schmitz, C.: Handbook of aluminium recycling. Mechanical preparation, metallurgical processing, heat treatment. 2. Auflage. Vulkan-Verlag, Essen, 2014.
[5] Zhou, Bo: Modelling the melting of postconsumer scrap within a rotary melting furnace for aluminium recycling. Delft University of Technology, 2005.
[6] Yao, T. P.: Die Viskosität metallischer Schmelzen. In Brandt, L. (Hrsg.). Forschungsberichte des Wirtschafts- und Verkehrsministeriums Nordrhein-Westfalen. Springer Fachmedien, Wiesbaden, 1956.
[7] Schwalbe, M.: Grundlagen und Möglichkeiten der Verarbeitung von höher kontaminierten Aluminiumschrotten. World of Metallurgy – Erzmetall 64 (2011), [Nr. 3].