Der DS-Lichtbogenofen in der Stahlgießerei
Möglichkeiten zu höherer Energieeffizienz beim Schmelzen
Von Peter Kuhlow, Parchim und Gunther Sachse, Leipzig
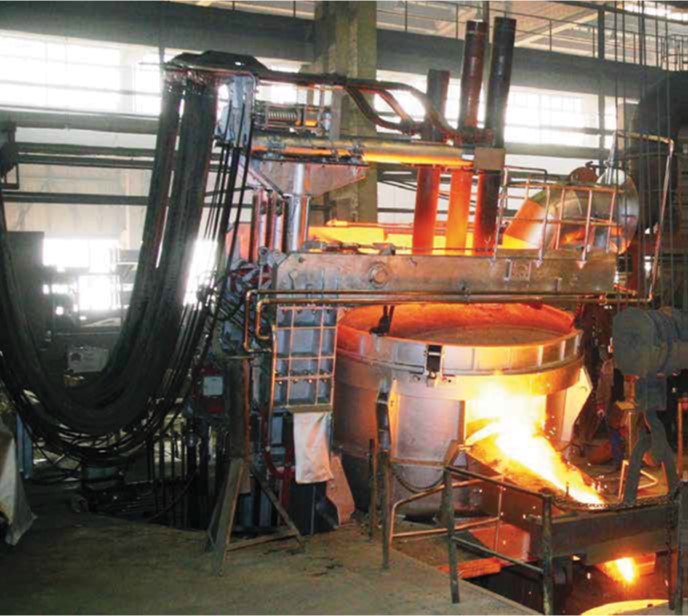
Erschienen in GIESSEREI 02/2017
Der Lichtbogenofen wurde erstmals 1906 in einer Stahlgießerei in Remscheid-Hasten für Werkzeugstahl eingesetzt. Fast 100 Jahre später wurde in Remscheid-Lüttringhausen von der Nachfolgefirma SMS Demag der modernste DS-Lichtbogenofen Europas (Bild 1) mit 3,5 t Fassungsvermögen, 4 MVA Nennleistung, wasserführender Deckel- und Obergefäßzustellung, Programmsteuerung, Fehler- und Störungsdiagnose mit Visualisierung und digitaler Elektrodenregelung mit hydraulischer Elektrodenverstellung errichtet. Bei diesem Ofen wurden nach Optimierung in mehreren Etappen Elektroenergieverbrauchswerte von 722 kWh/t Flüssigstahl für den gesamten metallurgischen Zyklus erreicht [1, 2].
Leistungs- und Energieeffizienzentwicklung
Erhöhte Anforderungen an die Energieeffizienzhatten direkte Vergleiche zum Schmelzen im Lichtbogen- und Induktionstiegelofen auf der Basis vergleichbarer Stahlqualitäten zur Folge. Bei diesem Vergleich wird aber übersehen, dass sich beide Ofenarten grundsätzlich unterscheiden: Während beim Induktionstiegelofen ein Tiegelverfahren mit vergleichbar geringer Badoberfläche vorliegt, wird beim Lichtbogenofen das Herdverfahren mit relativ großer Badoberfläche genutzt, was vorteilhaft für metallurgische Arbeiten ist. Ausdrücklich wird darauf hingewiesen, dass nicht nur im Induktionsofenbau, sondern auch im Lichtbogenofenbau entscheidende technisch-technologische Fortschritte realisiert wurden, die zu bemerkenswerten Kennzahlenentwicklungen geführt haben [3, 4]. Zur Energieeffizienz im Schmelzbetrieb durch optimierte Fahrweise von MF-Induktionsöfen ist in [5] ein empfehlenswerter Fachbericht zu finden, der differenzierte Vergleiche zum DS-Lichtbogenofen ermöglicht (Einschmelzen, Fertigmachen). Nachfolgend werden die verschiedenen Einflussfaktoren auf den Energieverbrauch und die Verbrauchszahlen quantifiziert.
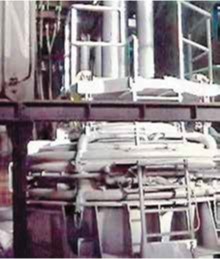
Leistungs- und Energieeffizienzentwicklung
Erhöhte Anforderungen an die Energieeffizienz hatten direkte Vergleiche zum Schmelzen im Lichtbogen- und Induktionstiegelofen auf der Basis vergleichbarer Stahlqualitäten zur Folge. Bei diesem Vergleich wird aber übersehen, dass sich beide Ofenarten grundsätzlich unterscheiden: Während beim Induktionstiegelofen ein Tiegelverfahren mit vergleichbar geringer Badoberfläche vorliegt, wird beim Lichtbogenofen das Herdverfahren mit relativ großer Badoberfläche genutzt, was vorteilhaft für metallurgische Arbeiten ist. Ausdrücklich wird darauf hingewiesen, dass nicht nur im Induktionsofenbau, sondern auch im Lichtbogenofenbau entscheidende technisch-technologische Fortschritte realisiert wurden, die zu bemerkenswerten Kennzahlenentwicklungen geführt haben [3, 4].
Zur Energieeffizienz im Schmelzbetrieb durch optimierte Fahrweise von MF-Induktionsöfen ist in [5] ein empfehlenswerter Fachbericht zu finden, der differenzierte Vergleiche zum DS-Lichtbogenofen ermöglicht (Einschmelzen, Fertigmachen). Nachfolgend werden die verschiedenen Einflussfaktoren auf den Energieverbrauch und die Verbrauchszahlen quantifiziert.
Einflussfaktoren für die Energieeffizienz
Die Energieeffizienz von Lichtbogenöfen wird von vielfältigen Faktoren beeinflusst. Dabei haben technische und technologische Weiterentwicklungen zu bemerkenswerten
Verbesserungen geführt. Leistungsstarke DS-Lichtbogenöfen können nach durchgeführten Berechnungen maximale Lichtbogenbogentemperaturen von etwa 7000 bis 8000 °C erreichen [6]. Die Verbesserungen betreffen insbesondere die Drosselspulen, die Ofentransformatoren, die Hochstromleitungen einschließlich Grafitelektroden, die Automatisierungstechnik einschließlich Elektrodenregelung, die Energiebezugssteuerung, den Ofenbau, die Zustellungsart und -qualität sowie Metallurgie und Technologie (Tabelle 1).
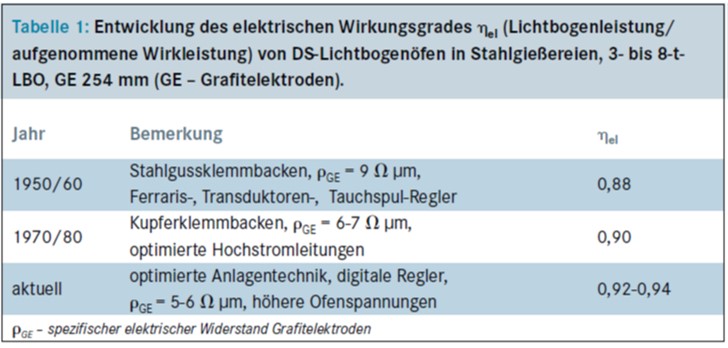
Aus betriebswirtschaftlicher Sicht sind oft Kompromisse erforderlich, die sich negativ auf die Schmelzleistung, den Energie-, Elektroden- und Zustellungsverbrauch u. a. auswirken können.
Die Grafitelektrodenqualität (spezifischer Widerstand 5 bis 8 Ω μm) hat miteinem Anteil von 0,071 mΩ pro 1 Ω μm Einfluss auf den Verlustwiderstand der Ofenanlage [3]. Bei einem mittleren Elektrodenstrom von10 kA sind das um 22,1 kWh/h höhere Energieverluste. Etwa 25 % der im Elektrodenstrang erzeugten Stromwärme sind davon im Ofen nutzbar. Damit wird ein maximaler elektrischer Wirkungsgrad von 0,94 bei einer gut dimensionierten und gewarteten Ofenanlage erreicht. Bei der Wahl der Elektrodenqualitäten spielen häufig niedrige Angebotspreise eine Rolle.
Die temperaturabhängigen Wärmeverluste eines konventionell zugestellten, betriebswarmen Ofens zeigt Tabelle 2.
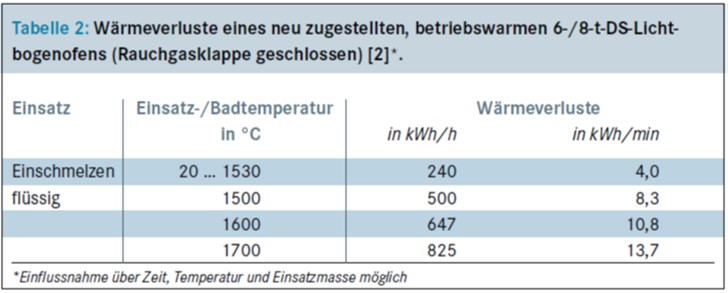
Geringe zeitliche Auslastung des Lichtbogenofens führt zu höheren Speicherwärmeverlusten, für die in Tabelle 3 Faktoren angegeben sind.
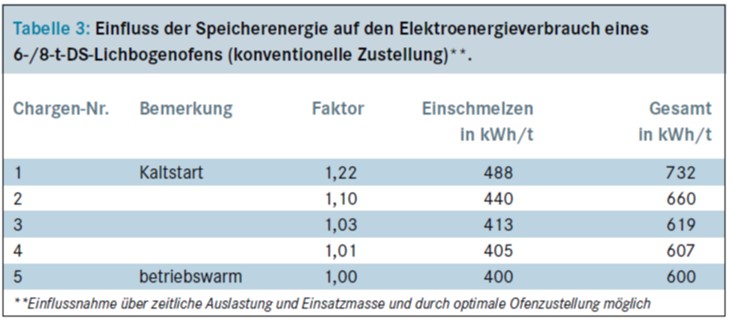
Bild 2 stellt den idealisierten Verlauf der Speicherenergie dar.
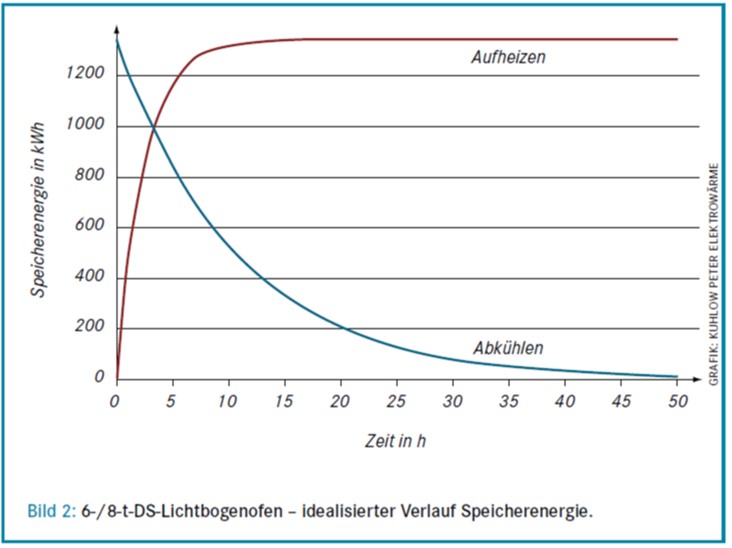
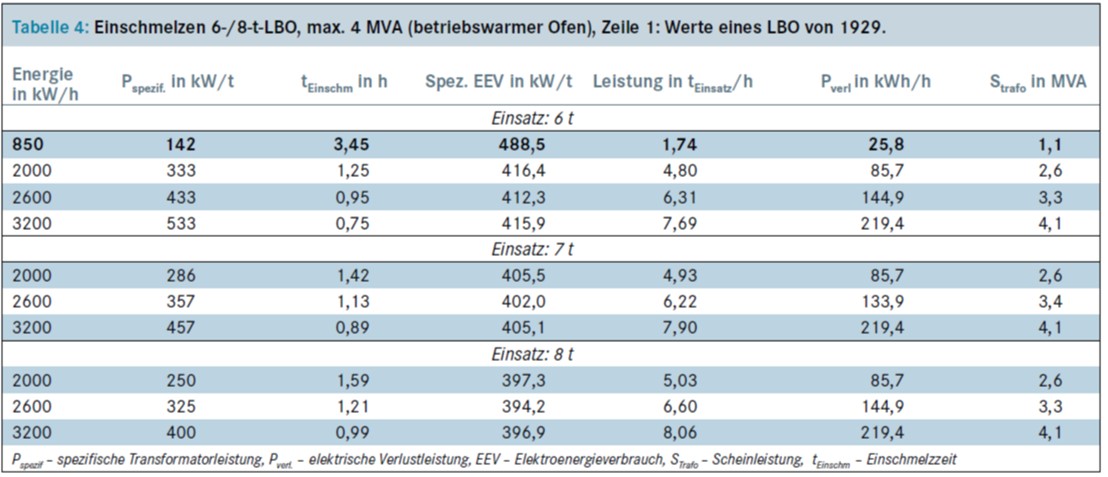
Über Verkürzungen der Prozesszeit, besonders beim Einschmelzen, können die Wärmeverluste verringert werden.
In der Literatur [7] wurde ein 5-t-Lichtbogenofen mit einer Einschmelzzeit von 3,5 h beschrieben. Die Daten dafür wurden in Tabelle 4 (Zeile in Fettdruck) näherungsweise
berechnet.
Mit den Enthalpiewerten für Stahl und Schlacke [7] und dem spezifischen Elektroenergieaufwand für unterschiedliche Heizraten in Abhängigkeit vom elektrothermischen
Wirkungsgrad (Bild 3), können die Energiebilanzen für vorgegebene Bedingungen und Einsatzmassen (Bild 4) sowie Tabellen für das Einschmelzen (Tabelle 4) und Heizen (Tabelle 5) erstellt werden.
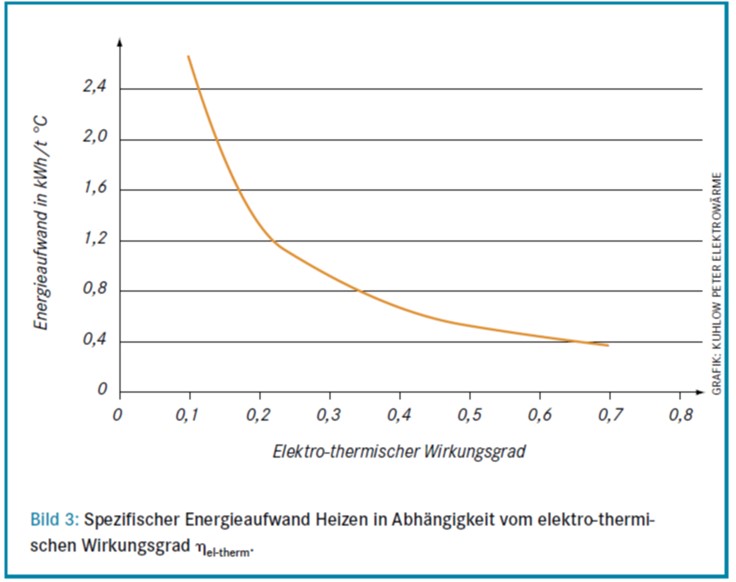
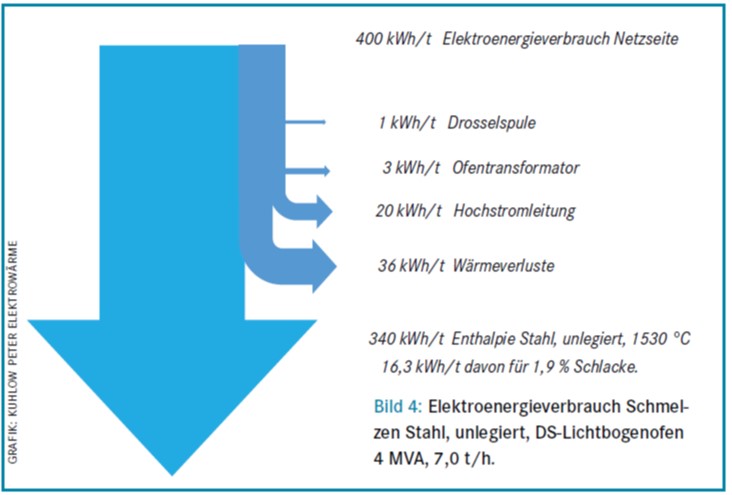
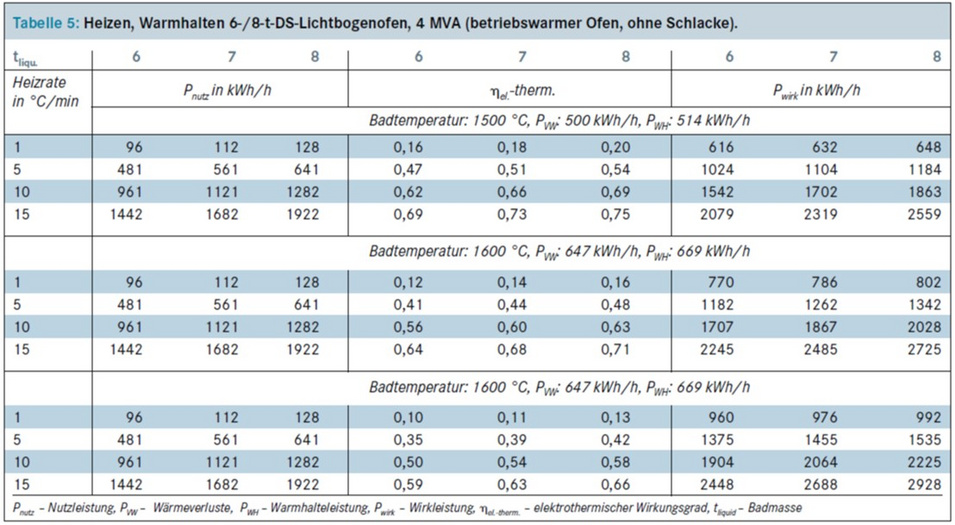
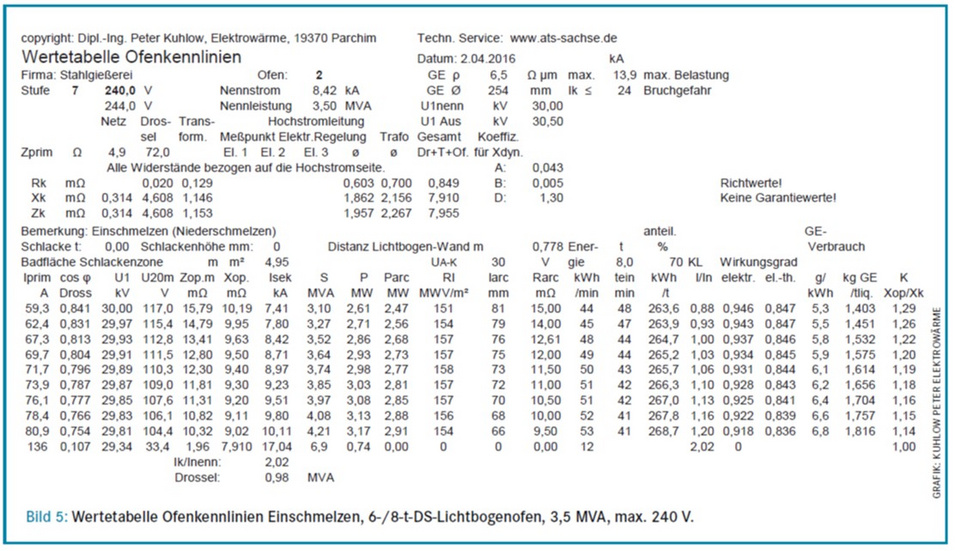
Die Warmhalteleistung für definierte Bedingungen kann man praktisch ermitteln, indem für verschiedene Heizraten, z. B. für 1 und 10 °C/min die Energieeinträge in kWh/h (x-Achse) gemessen werden. Der Schnittpunkt der Heizkurve mit der x-Achse bei 0 °C/min ergibt dann die Warmhalteleistung. Daraus können nach Abzug der elektrischen Verluste die Wärmeverluste bestimmt werden.
Einflussnahme durch Service und Messungen
Diese, für die Betreiber von Lichtbogenöfen wichtigen Dienstleistungen zum Erreichen optimaler Anlagenbedingungen werden seit Bestehen des Ingenieurbüros für Elektrowärme Peter Kuhlow durch ATS Sachse GmbH weltweit weitergeführt. Die unterschiedlichsten, im Folgenden genannten Aufgaben werden im Rahmen einer Serviceleistung behandelt, um die Aggregate leistungsfähig und optimal betreiben zu können:
- Berechnung, Auslegung von Transformatoren und Drosselspulen,
- theoretische Berechnung von Kennzahlen pro Transformatorstufe,
- Beratungen bei Umbaumaßnahmen oder Gesamtmodernisierungen,
- Einschätzung, Reaktanzberechnung vom Hochstromsystem,
- Erstellen von Einschmelzprogrammen mit Hinweisen zu Fahrweisen,
- Einstellung analoger, elektronischer Regelungen auf optimale Sollwerte,
- Service, Beratungen zu Fehlern im Betriebsverhalten mittels messtechnischer Untersuchungen,
- Berechnung, Austausch von Hochstromkabeln Erarbeitung von Sonderlösungen,
- Beschaffung, Reparatur älterer Regler-Bauteile (BBC, Feig, KGYV), die nicht mehr lieferbar sind,
- Nachfertigung von elektronischen Baugruppen (Reglerkarten) als Sonderlösung und
- begleitende Inbetriebnahmen nach Umbaumaßnahmen oder Gesamtmodernisierungen.
Zum Nachweis der aktuellen Betriebsverhältnisse werden Messungen mittels Leistungsmessgerät AC Power Analyzer nach geltender Prüfnorm IEC 60676 durchgeführt. Je nach Aufgabenstellung sind bis 4 Chargen notwendig, um mögliche Fehlerquellen elektrisch, elektrothermisch oder mechanisch zu erkennen. Nach Fehlerbehebung
oder Einstellung der Regler sind Folge-Chargen notwendig, bis die optimalen Betriebsbedingungen erfüllt sind. Ein Messintervall ist auf 60 s festgelegt, gemessen wird vom Start bis zum Abstich. Das Messprotokoll beinhaltet:
- aktuelle Uhrzeit,
- Sekundärstrom/Phase und Mittelwert,
- Spannung am Messpunkt/Phase und Mittelwert,
- Wirkleistung/Phase und Mittelwert,
- Leistungsfaktor cos w/Phase und Mittelwert,
- Resistanz/Phase und Impedanz/Phase,
- Energieverbrauch/Phase und Summe Energieverbrauch (kumulativ),
- unter Bemerkungen können aktuelle Informationen während der Charge eingetragen werden.
Werte, wie z. B. Einsatzmasse, Chargennummer, kWh-Zählerstand Ofen, Umschaltung Spannungs- und Stromstufen sowie Primärspannung werden erfasst. Es sind Messungen primär- und sekundärseitig möglich. Sollten keine Wandler vorhanden sein, erfolgt der Aufbau einer Messschaltung mittels Rogowski-System (Klasse 1) bis max. 20 kA. Mit einer Serviceleistung werden zusätzliche Daten erfasst. Das sind: Leistungsschalter (Schutzeinstellung), Transformator, Drosselspule, Aufbau und Abmessung Hochstromleitung, Elektrodentragarmführung, Temperaturen von Anlagenteilen mittels Wärmebildkamera u. a. Die Auswertungen nach allen Messungen im Vergleich zu den Wertetabellen für Ofenkennlinien lassen Aussagen über zweckmäßige Arbeitsbereiche zu. Zusätzliche Betrachtungen über Einschmelzzeiten (min), Heizraten (°C/min), Strahlungsindex mit Abstandsfaktor (MWV/m²) und Kochfaktor, Einstellwerte in Abhängigkeit vom Einsatz, spezifischen Elektroenergieverbrauch (kWh/t) und GE-Verbrauch (kg/t) sind möglich. Damit sind die Einflussfaktoren hinsichtlich einer höheren Energieeffizienz messtechnisch erfasst. Durch gezielte Instandhaltungsmaßnahmen, Einstellung oder Reparatur können effektivere Verbrauchswerte wieder erzielt werden. Außerdem sind zusätzliche Verbesserungen
durch Kennlinienberechnungen mit effizienteren Einstellwerten für die Regelung erreichbar.
Einflussnahme durch Kontrolle, Instandhaltung
Ein betriebsinternes Qualitätsmanagement bewertet monatlich Daten zu Verbräuchen. Mit Auswertungen und Kontrollen kann zeitnah Einfluss auf Veränderungen genommen werden.
Nach zahlreichen Untersuchungen wurden immer wieder Nachlässigkeiten im Umgang mit Reparaturen, Teilinstandsetzungen oder einfachen Wartungsmaßnahmen festgestellt. Bereits kleine Fehler können an diesen energieintensiven Aggregaten höhere Verluste und Kosten verursachen, u. a. erhöhte Energie- und Materialverbräuche.
Zusätzlich erhöht sich der Verschleiß an mechanischen Bauteilen – die Lebensdauer von Baugruppen wird verringert. Zu Anlagen älterer Bauart (bis 1990) können durch die ATS Sachse GmbH Wartungsund Instandhaltungspläne erstellt werden. Des Weiteren werden Wartungen der Lichtbogenofenanlagen als vorbeugende Instandhaltung
angeboten. Dazu erfolgt eine Sichtkontrolle aller Anlagenteile, z. B. Schaltzyklen Stufenschalter, Kontrolle von elektrischen Verbindungen an Klemmleisten, lose Verbindungen Hochstromleitung, Überprüfung des Drehmoments bei Schraubenverbindungen, Kontrolle von mechanischen Bauteilen hinsichtlich Deformierung oder Beschädigungen, Undichtigkeiten, Flüssigkeitsverlust, thermografische Aufnahmen mittels Wärmebildkamera und Referenzbildern. Eine Protokollierung durch Checklisten gibt dem Betreiber Sicherheit in der Durchführung der Maßnahmen und zeigt eine Übersicht über Fehler bzw. Missstände auf.
Es wird empfohlen, vorbeugende Instandhaltungsmaßnahmen jährlich durchzuführen. Eine messtechnische Überprüfung der Ofenanlage ist im Abstand von mindestens 2 Jahren zweckmäßig. Sollten sich Verbrauchswerte vorher verschlechtern, sind zeitnahe Instandhaltungsmaßnahmen zur Fehlerursache durchzuführen. Zu den iederkehrenden Wartungsmaßnahmen können Verträge abgeschlossen werden. Damit ist für alle Beteiligten eine kalkulierbare Kostengrundlage geschaffen.
Einflussnahme durch Optimierung
Basis für eine Einflussnahme durch Optimierung sind Wertetabellen für Ofenkennlinien, die speziell für jeden Lichtbogenofen und die entsprechenden Betriebsbedingungen im Rahmen vielfältiger Aufgabenstellungen bei zahlreichen Ofenuntersuchungen ständig weiterentwickelt wurden.
Für die Auslegung und die Bewertung der elektro-thermischen Verhältnisse und wesentlicher Anteile, wie z. B. Drosselspule, Ofentransformator, Hochstromleitung einschließlich Grafitelektroden und Kennzahlen des Ofenbetriebes, sind die Wertetabellen ein effizientes Hilfsmittel (Bild 5).
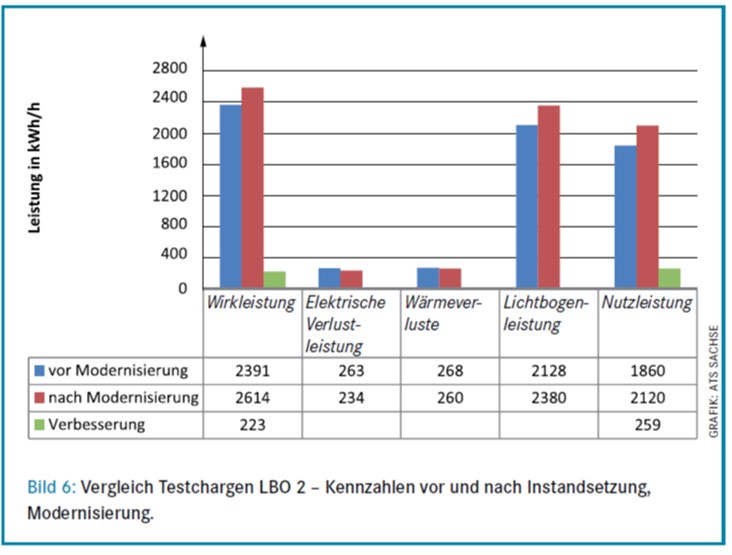
Für Hersteller und Zulieferfirmen dienen die Berechnungswerte mit als Grundlage für Dimensionierungen von Anlagenteilen. Außerdem können speziell für die Kundenbedingungen Berechnungen zu energetisch-elektrothermischen Einflüssen erstellt werden.
In bereits durchgeführten Projekten erfolgten im Vorfeld theoretische Berechnungen z. B. zur Betrachtung kürzerer Einschmelzzeiten. In den nachfolgenden Messungen konnten die Ergebnisse bestätigt werden.
Aus den Berechnungswerten der Kennlinien werden Einschmelzprogramme als Vorgabe einer Programmsteuerung oder Fahrweise per Hand erstellt. In Abhängigkeit von Tonnage und Schrottverhältnissen werden pro Transformatorstufe mit einer berechneten Zeit zum Energieverbrauch die Programmschritte festgelegt. Damit ist bis zur Probennahme (bei Temperaturen um etwa 1530 °C) die Einschmelzzeit rechnerisch ermittelt und kann als Orientierung für den Ofenbetrieb und als Planungsgrundlage
verwendet werden. Weitere Einflussfaktoren zu längeren Schmelzzeiten oder höheren Energieverbräuchen sind zusätzlich festgestellt worden:
- Beschickung Schrottkörbe – zu hohe Schrottdichte, sperriger Schrott,
- schlechte Kontaktierung durch unsauberen Schrott,
- überwiegend Schmelzen mit kaltem Ofen, ungenügende Auslastung,
- Vernachlässigung der Wartungsmaßnahmen (Flüssigkeitsverluste Hydraulik, mangelhafte Entlüftung Hydrauliksystem, defekte Ventile ohne Nullstellung, lose Verbindungen der Hochstromleitung, defekte Hochstromkabel, verschlissene Elektrodentragarmführung usw.),
- ungenügende Reinigung und Instandhaltung von Klemmbacken (alle 14 Tage empfohlen),
- Deformation, Beschädigung mechanischer Bauteile,
- unzureichend arbeitende Reglung und
- Fehler an elektrischen Baugruppen.
Bei älteren Anlagen mit analogen Baugruppen bzw. Reglungen zeigt die Vergangenheit, dass eine jährliche Überprüfung bessere Verbrauchszahlen liefern kann und das Ausfallverhalten verringert. Entscheidende Verbesserungen von Einflussfaktoren der Anlagen bedeuten auch, nach langen Laufzeiten eine Modernisierung entsprechend des Standes der Technik anzustreben. Technische Ausrüstungen für Lichtbogenofenanlagen wurden ständig weiterentwickelt. Spezielle digitale Reglungssysteme, Visualisierungen, Darstellungen von Anlagenzuständen, Ventiltechniken und Steuerungssysteme gewährleisten eine hohe Betriebssicherheit mit optimaler Überwachung. Damit werden die Bedienung der Anlagen erleichtert, Fehlerursachen schneller erkannt, Stillstände verkürzt und zusätzliche Sicherheiten im Umgang mit den Anlagen geboten. Durch Netzwerke und spezielle Softwarelösungen zur Auswertung erfolgt eine zentrale Überwachung zu Verbrauchszahlen und Zeiten. Damit kann zeitnah in den Prozess eingegriffen werden. Diese Leistungen werden im Partnerverbund Elektro-Industriemontagen GmbH Riesa als Gesamtmodernisierung „Mechanik, Hydraulik und Elektro-Steuerungs- und Regelungstechnik“ angeboten.
Die bereits bearbeiteten Projekte waren immer wieder herausfordernde, einzelne Sondervarianten, da kundenspezifische Lösungen gefunden werden mussten. Das entwickelte Konzept der Gesamtmaßnahme hat sich dabei bewährt, Verbesserungen an den Anlagen zu erkennen und dem Kunden in der Auswertung beim Dauerbetrieb zu belegen. Nach schriftlichem Bestelleingang zur Beauftragung läuft ein konzeptionelles Prozedere ab:
- Berechnung der Kennlinien interessierender Transformatorstufen, eventuelle Optimierungen,
- chargenbegleitende Messung mit Ist-Zustandsaufnahme,
- Auswertung, Erstellung Fahrweisen, Programme, Anpassung der Kennlinien an veränderte Werte,
- technische Begleitung während der Baumaßnahmen,
- technische Begleitung zur Inbetriebnahme, Kaltfunktionstests,
- chargenbegleitende Messungen nach Inbetriebnahme, Kontrolle der Kennlinienwerte, Optimierung, Anpassung der Reglung mit Inbetriebnehmer vor Ort und
- Auswertung, Gegenüberstellung der Werte und Verbesserungen als Abschlussbericht.
Eine Gesamtumbaumaßnahme wurde mit einer Vorbereitungszeit von 3 Monaten beim Kunden innerhalb von 6 Wochen realisiert. Damit war der Produktionsstillstand der Anlage kalkulierbar. Die Verbesserungen, welche u. a. durch das digitale Reglungssystem erreicht wurden, zeigt Bild 6 (weitere Angaben in [8], S. 62). Dieses Konzept kann auch bei bereits modernisierten Anlagen angewandt werden.
Fazit
Erreichbar sind diese durchaus wettbewerbsfähigen Ergebnisse durch:
- Optimierungen der Anlagentechnik,
- ein Ausrichten der Instandhaltung auf die Gewährleistung der anlagentechnischen Erfordernisse,
- weitere Optimierungen der technologischen und metallurgischen Abläufe, um die temperatur- und zeitabhängigen Wärmeverluste zu verringern und
- weiteres Erhöhen der zeitlichen und kapazitiven Ofenauslastung, um die anteiligen Speicherwärmeverluste zu verringern.
Diesem Bestreben stehen nicht selten die mangelnden Kundenaufträge gegenüber, wobei sich auch der Wettbewerb zunehmend verschärft. Unter diesem Aspekt kommt der Modernisierung veralteter Ofenanlagen eine besondere Bedeutung zu, weil moderne und leistungsfähige neue DS-Lichtbogenöfen hohe Investitionen erfordern [8, 10].
Auf der Basis jahrzehntelanger Erfahrungen wurden für die Optimierung und zweckmäßige Einstellung der Lichtbogenöfen Wertetabellen zur Ofencharakteristik vermittelt. Durch die Berücksichtigung vieler Einflussfaktoren für das Einschmelzen und Fertigmachen (Aufheizen) für entsprechende Spannungsstufen können mittels Messungen im Rahmen von Serviceleistungen bei Inbetriebnahmen, nach Modernisierung oder Überprüfungen in kurzer Zeit effektive Einstellungen vorgenommen werden [1, 8-10].
Dipl.-Ing. Peter Kuhlow, Berater Elektrowärme, Parchim, Gunther Sachse, ATS Sachse GmbH, Leipzig
Literatur:
[1] ewi – elektrowärme international (2004), [Nr. 4], S. 171-176.
[2] ewi – elektrowärme international (2005), [Nr. 2], S. 74-79.
[3] ewi – elektrowärme international (2003), [Nr. 3], S. 117-124.
[4] Heinen, K.-H.: Elektrostahlerzeugung. Verlag Stahleisen GmbH, Düsseldorf, 1997.
[5] ewi – elektrowärme international (2015), [Nr. 4], S. 43-49.
[6] ewi – elektrowärme international (2010), [Nr. 2], S. 115-122.
[7] Sommer, F.; Pollack, H.: Elektrostahlerzeugung. Verlag Stahleisen, Düsseldorf, 1950.
[8] ewi – elektrowärme international (2012), [Nr. 4], S. 57-64.
[9] Giesserei 100 (2013), [Nr. 6], S. 40-46.
[10] ewi – elektrowärme international (2015), [Nr. 4], S. 57-62.