Umweltschutz und Energietechnik (5. Folge)
Von Manuel Bosse, Düsseldorf
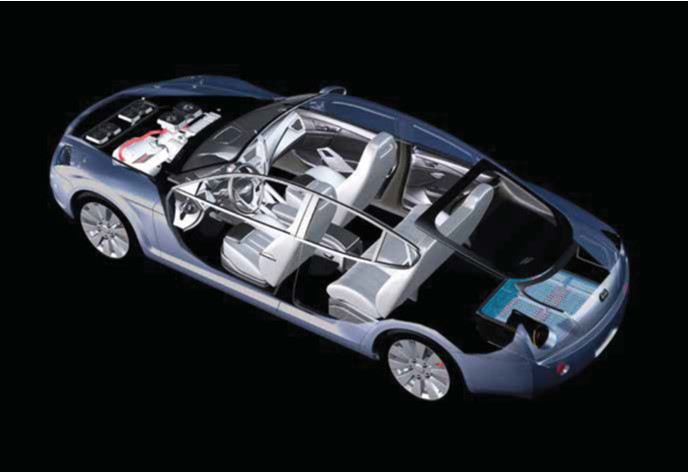
Werden zunehmend Verbrennungsmotor betriebene Fahrzeuge durch Elektrofahrzeuge
ersetzt, müssen Gießereien völlig neue Gussteillösungen entwickeln.
Erschienen in GIESSEREI 11/2017
Die Energiewende mit ihren Zielen Reduktion von Treibhausgasen, Energieeffizienz, Netzausbau bei gleichzeitiger Versorgungssicherheit und guter Wirtschaftlichkeit bleibt in den Gießereien ein wichtiges Thema. Deutsche Gießereien konnten vor allem durch kostengünstigere Strombeschaffung in Neuverträgen ebenso wie im Vorjahr Kosteneinsparungen realisieren: Der Strompreis sank für eine durchschnittliche deutsche Gießerei von etwa 16,5 ct/kWh auf 16,1 ct/kWh. Dies war auch möglich, weil sich die Prognosen in der letzten Jahresübersicht* mit einer EEG-Umlage von über 7 ct erfreulicherweise nicht erfüllt haben. Trotzdem blieb am Ende ein Anstieg der EEG-Umlage von über 8 % im Vergleich zum Vorjahr. Im Jahr 2018 wird die EEG-Umlage aufgrund hoher sogenannter Liquiditätsrücklagen voraussichtlich leicht sinken. Dieser Einmaleffekt wird dann 2019 laut Agora-Energiewende dazu führen, dass die Umlage auf über 7,5 ct/kWh steigen wird. Ob Unternehmen die im Jahr 2017 erneut gestiegene EEG-Umlage auf nun 6,88 ct pro benötigte kWh Strom zahlen müssen oder von einer reduzierten Umlage profitieren können, ist für die 581 deutschen Gießereien von erheblicher Bedeutung (Tabelle 1). Knapp 20 % der Gießereien konnten wie in der Tabelle dargestellt im Jahr 2016 erfolgreich unter bestimmten Voraussetzungen einen Antrag auf Begrenzung der EEG-Umlage stellen.
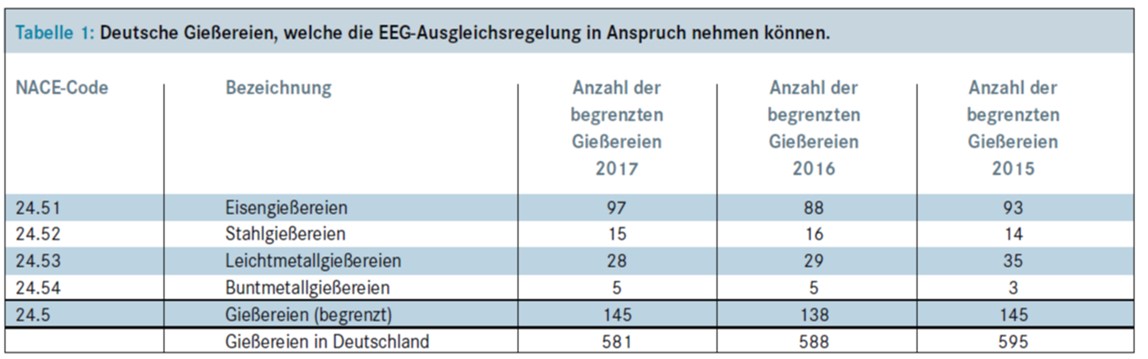
Gießereien haben in den letzten Jahren durch Einführung systematischer Energiemanagementsysteme Energieeinsparungen realisieren können, wie z. B. M. Dürkes [1] an einer Eisengießerei erläutert. Doch die starren Grenzen im Erneuerbare-Energien- Gesetz führen paradoxerweise dazu, dass ein Anreiz für energieintensive Gießereien besteht, mehr Strom zu verbrauchen anstatt energieeffizienter zu werden, um die Grenzen von 14, 17 oder 20 % Stromkosten an der Bruttowertschöpfung nicht zu unterschreiten. Gießereien hatten z. B. in der Vergangenheit durch mehrere Maßnahmen zur Verbesserung der Energieeffizienz einen niedrigeren Energiebedarf, infolgedessen die Schwellen nicht mehr überschritten wurden. Eine Stahlgießerei stellte in der Folge bewusst die erdgasbefeuerten Wärmebehandlungsöfen auf elektrisch betriebene Öfen um, um wieder von der teilreduzierten EEG-Umlage zu profitieren. Wird der CO2-Emissionsfaktor des deutschen Strommixes von 527 g pro kWh mit dem Faktor von Erdgas – je nach Quelle zwischen 200 und 300 g CO2 pro kWh – verglichen, dann ist dies gesamtwirtschaftlich betrachtet, bezogen auf den Klimaschutz, nachteilig. Die umgekehrte Ausweichreaktion lässt sich vor allem bei Nichteisenmetallgießereien beobachten, welche die volle EEG-Umlage bezahlen müssen: Da Erdgas gegenwärtig kostengünstig ist, stellen NE-Gießereien energieintensive Prozesse wie z. B. den Schmelzbetrieb von Strom auf Erdgas um.
Neben der Kostenbelastung und den gezeigten Fehlanreizen ist in den letzten Jahren eine dramatisch gewachsene administrative Belastung der Unternehmen zu verzeichnen. Abschreckendes Beispiel für die Antragstellung zur EEG-Ausgleichsregelung ist das sogenannte „Merkblatt für stromkostenintensive Unternehmen 2017“ vom Bundesamt für Wirtschaft und Ausfuhrkontrolle (BAFA), welches Ende April 2017 erschienen ist. Dieses umfasst mittlerweile 105 Seiten und wird Jahr für Jahr umfangreicher und komplizierter. Der Bundesverband der Deutschen Gießerei-Industrie (BDG) treibt daher innerhalb einer Verbändeallianz die Idee der haushaltsbasierten Finanzierung der staatlichen Stromkostenanteile voran, wodurch der bürokratische Aufwand und die hohen Umlagekosten entfallen würden. Die Stromrechnung versagt als Finanzierungsinstrument und die Kosten werden die Energiewende absehbar scheitern lassen.
Neben der Energiewende soll nun auf deutschen Straßen, wie in Bild 1 dargestellt, auch die „Verkehrswende“ mit Elektro- anstelle von Verbrennungsmotoren vorangetrieben werden. Im ersten Halbjahr 2017 steht jedoch dem Anteil erneuerbarer Energien am deutschen Strommix von etwa 38 % die Stromproduktion von elektrischer Energie in Kohlekraftwerken von knapp 41 % gegenüber. Elektroautos werden zukünftig ihre Stärken nur dann ausspielen können und klimaschützend sein, wenn die Produktion des Autos selbst klimaneutral geschieht und die Batterien nur mit Strom aus erneuerbaren Energien aufgeladen werden. Wie umweltfreundlich ein Elektroauto fährt, hängt davon ab, mit welchem Anteil Strom aus erneuerbaren Energien das Auto geladen wird. Ein BMW i3 wird in China mit einem Strommix aus fast 90 % Kohle geladen, wodurch indirekt mehr Emissionen als beim Verbrennungsmotor entstehen. In Deutschland sieht die Bilanz besser aus, denn die Emissionen pro kWh Strom sind von 761 g CO2 im Jahr 1990 auf 527 g CO2 im Jahr 2016 gesunken.
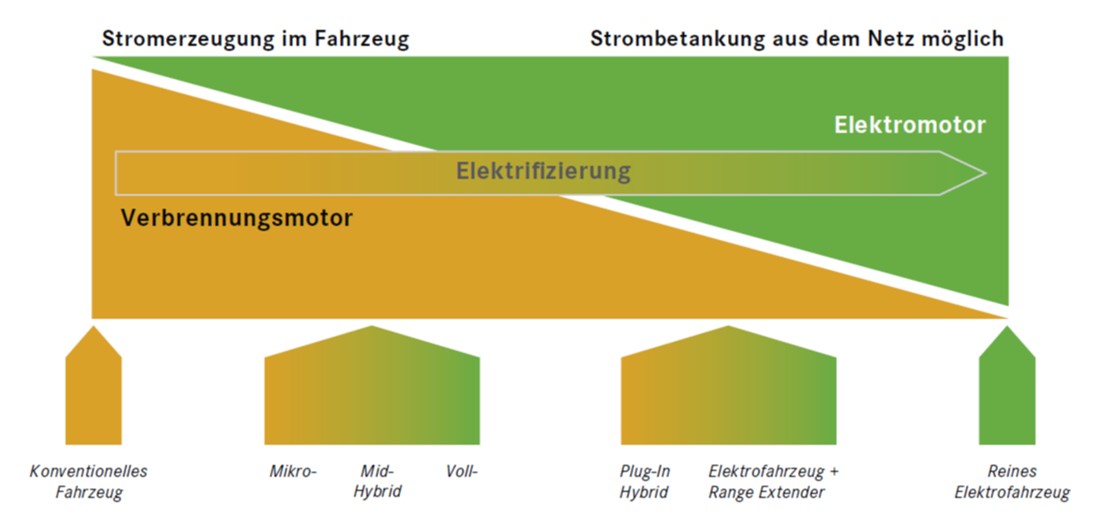
Das Institut für Energie- und Umweltforschung hat zwei Elektroautos mit einem Benziner (BMW 535i) und einem Diesel (BMW 320d) verglichen. Bei der Herstellung entstehen beim Elektroauto 9,5 bzw. 12 t CO2, wohingegen die Emissionen beim Benziner bei 8 t CO2 und 7 t CO2 beim Diesel liegen. Beim Elektroauto, das mit Ökostrom betankt wird, liegt der „CO2-Break-Even-Point“ nach etwa 20 000 km Fahrleistung vor. Spätestens nach knapp 50 000 km fällt auch das Elektroauto, welches mit dem deutschen Strommix betankt wird, effizienter als der Benziner oder der Diesel aus.
Im Jahr 2008 wurde von der Bundesregierung das Ziel gesetzt, dass im Jahr 2020 1 Mio. Elektroautos auf deutschen Straßen unterwegs sein sollen. Als Unterstützung wird seit 2016 für Elektro-, Hybrid- sowie Brennstoffzellenfahrzeuge ein sogenannter Umweltbonus für voraussichtlich 300 000 Fahrzeuge gewährt. Bis Ende August 2017 wurden jedoch erst 30 000 Fahrzeuge gefördert. Selbst Bundeskanzlerin Angela Merkel befürchtete im Mai 2017, dass das selbstgesetzte Ziel bis 2020 wohl nicht erreicht werden wird. Die ersten Länder entscheiden sich nun dafür, dass zukünftig keine Fahrzeuge mehr mit Verbrennungsmotoren zugelassen werden – z. B. in Norwegen ab 2025 sowie in Großbritannien und in Frankreich ab 2040. Sowohl China als auch vermutlich die Europäische Kommission arbeiten schon an festen Elektroautoquoten.
Für die Gießerei-Industrie bedeutet die Verkehrswende eine deutliche Herausforderung, denn heute liefern fast 85 % der Nichteisenmetallgießereien und 55 % der Eisen- und Stahlgießereien ihre Produkte an den Straßenfahrzeugbau – zum Großteil abhängig von Verbrennungsmotoren.
Vor allem die Eisengießer im Automotivebereich stehen vor großen Herausforderungen. Aufgrund aktueller politischer Überlegungen kann laut E. Flender [3] nicht davon ausgegangen werden, dass in 20 Jahren noch Pkw-Diesel gebaut werden. Es ist absehbar, dass zukünftig immer weniger Autos ausschließlich mit Verbrennungsmotor und wenn überhaupt vor allem als Plug-in-Hybridelektrokraftfahrzeug rein elektrisch oder als Brennstoffzellenfahrzeug fahren werden.Es lassen sich grob drei Bereiche für Gussteile im Elektroauto identifizieren: Antrieb, Fahrwerk und Karosserie [4]. Die Substitution des Verbrennungsmotors durch „Energiespeicher“ wird fast alle Gussteile im Antriebsbereich „wegfallen“ lassen. G. Hartmann [5] erläutert, was das Ende der Verbrennungsmotoren für Gießer konkret bedeutet: keine Zylinderköpfe, keine Kolben, keine Kurbelwellen, Nockenwellen und (Abgas-)Krümmer. Gießereien haben jedoch die Chance, völlig neue Gussteile speziell für die Elektromobilität zu entwickeln, z. B. Batteriegehäuse (aus Aluminiumdruckguss) mit integriertem Kühlsystem oder Bremsscheiben und -Felgenbetten aus Aluminium anstelle von Bremsscheiben aus Gusseisen mit Lamellengrafit [6].
G. Rau [7] sieht alle Einzelteile des Autos zudem unter einem zusätzlichen Druck durch die Forderung nach Leichtbau. Doch genau die Gewichtsreduktion durch Leichtbaukomponenten gilt weiterhin als Stärke der Gießerei-Industrie, z. B. Schwenklager aus Eisenguss, die nach bionischen Prinzipien optimiert wurden [8] (Tabelle 2).
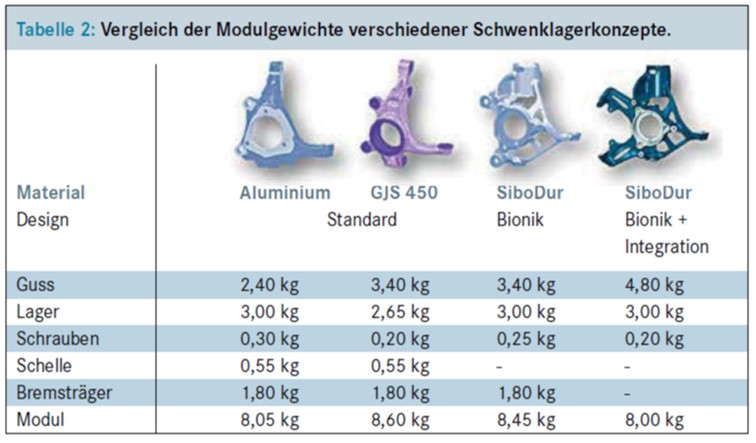
Das Thema Speicher taucht in vielen unterschiedlichen Themenbereichen auf, z. B. bei der Batteriezellenfertigung oder wenn in Tageszeitungen darauf hingewiesen wird, dass zukünftig bei Fotovoltaikund Windkraftanlagen nicht mehr die Menge, sondern der Wert des erzeugten Stroms im Vordergrund stehen. In Verbindung mit Speichern, die im netzentlastenden Betrieb laufen, können Anlagen systemdienlich ausgelegt werden. Systemdienlich bedeutet für Fotovoltaikanlagen, dass von Betrieben möglichst
nur bis Sonnenaufgang Strom aus dem Netz bezogen wird. Danach wird die Eigenversorgung sichergestellt und Überschüsse werden nicht ins Netz eingespeist, sondern es wird ein angeschlossener Speicher aufgeladen, sodass in den Abendstunden möglichst lange weiterhin eine Stromversorgung sichergestellt werden kann.
Bei Windkraftanlagen an Land ist es wichtig, dass Schwachwindturbinen verbaut werden, die auch bei niedrigen Windgeschwindigkeiten ab 3 m/s möglichst viel Strom erzeugen. Dies wird vor allem durch höhere Türme und damit durch eine größere Nabenhöhe sowie längere Rotorblätter möglich.
Nicht nur Fotovoltaikanlagen können mit Speichern gekoppelt werden, sondern auch Windkraftanlagen mit Pumpspeichern. Der sogenannte Naturstromspeicher hat im Furmfundament einen integrierten Wasserspeicher, wodurch die Nabenhöhe der Windkraftanlagen vergrößert wird. Durch den Anschluss der Speicher in den Türmen an ein Pumpspeicherwerk kann Wasser in ein Unterbecken gepumpt und die „Energie zwischengespeichert“ werden.
S. L. Prince [9] weist in seinem Standpunkt darauf hin, dass in den letzten drei Jahren die Batteriepreise um 20 % gesunken sind. So können intelligente Speicherlösungen auch für Gießereien Flexibilitätsoptionenbieten, um z. B. Netzentgelte oder Leistungsspitzen im Betrieb systematisch zu senken. In diesem Standpunkt wird zudem ein Speicher vorgestellt, der mit einer Leistung von 1 MW ungefähr 2 MWh speichert. Einen Schritt weiter geht die Forschung an der „virtuellen Batterie“, bei der ein Aluminiumproduzent die Elektrolyseöfen zwischen 75 und 125 % flexibel fahren kann, wodurch eine Speicherkapazität in den vier Werken von bis zu 3300 MWh entstehen könnte. Steuerbare Wärmetauscher haben dabei die Aufgabe, die Energiebilanz im Ofen trotz fluktuierender Energiezufuhr konstant zu halten.
Zusätzlich wird bei Windkraftanlagen zukünftig gezielt dazu übergegangen, dass neben Wirk- auch Blindleistung bereitgestellt wird, die bisher aus fossilen Kraftwerken bezogen wurde. Das wird vor allem für schwache Netzregionen interessant, die zwar viele Windkraftanlagen haben, aber kostenintensiver Netzausbau gegenwärtig nicht möglich ist. Die Gießerei GZO von Enercon in Ostfriesland stand genau vor dieser Herausforderung. Die elektrischen Schmelzaggregate würden die schwache Netzregion überlasten und Spannungen zu weit absinken lassen. Durch sogenannte statische Kompensatoren, die unzulässige Spannungsschwankungen verhindern, konnte der Bau einer neuen Hochspannungsleitung zum Werk vermieden werden.
Industrie 4.0
Das Thema „Smart Foundry“ als ein Vorbild für die „Industrie 4.0-Gießerei“ bleibt auch weiterhin ein Thema.
Wie die fahrerlosen, universell beweglichen Transportsysteme MARIE, EMMA, LENA und TINA tonnenschwere Formkästen automatisch durch den Betrieb steuern, beschreibt Michael Franken [10] aus seinen Erfahrungen vor Ort.
Was eine moderne Handformgießerei schafft, soll mit Technologiedatenmanagement (TDM) auch beim Druckgießen funktionieren (Bild 2). Folgende Ziele wurden beim „smart die casting“ verfolgt:
- Lückenlose Bauteilverfolgbarkeit in Bezug auf Fertigungsparameter und Qualitätskennwerte,
- Abbildung des Auftragsfortschritts,
- Analyse von Parameterverläufen gießtechnologischer Einflussgrößen,
- Abbildung technischer Einflussgrößen,
- Analyse komplexer Parameterzusammenhänge und Wechselwirkungen und
- Integration von Energie- und Betriebsstoffdaten, um Energieeinsparpotenziale zu identifizieren.
Eine Steigerung der Gesamtanlageneffektivität um über 10 % wurde in diesem Projekt erzielt, weil ungeplante Anlagenstillstände, Einflüsse durch den Anlagenbediener und technische Störungen ausgewertet wurden, um beeinflussbare Stillstände zu minimieren.
Wer jedoch bei Industrie 4.0 bei Gießereien nur an „Guss“ denkt, vergisst laut A. Liedtke [12] einen wichtigen Aspekt – das Sandsystem wird häufig bei der vernetzten Gießerei einfach ausgeklammert. Doch auch wenn sich Gussfehler in viele Untergruppen einteilen lassen, so sind laut Aussage des Autors durchschnittlich in über 40 % der Fälle formsandbedingte Gussfehler der Hauptgrund für Ausschuss. Eine Sandgießerei kann mit einem Formsandmanagementsystem erhebliche Verbesserungspotenziale erschließen. Häufig werden Kühler, Bunker und Mischer isoliert voneinander gesteuert. Am Beispiel einer bentonitgebundenen Formsandaufbereitung werden vier Module erläutert, die über Schnittstellen verknüpft werden sollten:
- Formsandmischer: Kontrolle des Misch prozesses zur Erreichung der gewünschten Zielfeuchte,
- Formsandkühler: Kontrolle über den Befeuchtungsprozess des Altsandes gerade bei schwankenden Umgebungsbedingungen vom Eingang bis zum Verlassen des Kühlers,
- Formsandprüfsystem: prozessintegriertes Prüfsystem inklusive Ermittlung wichtiger Formstoffwerte mit automatischer oder manueller Möglichkeit für Korrekturmaßnahmen,
- Prozess- und Qualitätssicherungssystem: Vernetzung der Teilprozesse und Überwachung, Visualisierung sowie Archivierung der Formsandqualität.
M. Lewis [13] knüpft an die Überlegungen von A. Liedtke an und verspricht durch die Umstellung auf ein systematisches Sandmanagement auch Auswirkungen auf den Einkauf. Denn das „smarte System“ bestellt proaktiv Quarzsand, wenn die Sandvorräte eine bestimmte Menge unterschreiten. Des Weiteren kann so auch der Bedarf an Sand, Chemikalien und Verbrauchsmitteln anhand der aktuellen Auslastung prognostiziert und frühzeitig auf Preissignale am Markt reagiert werden.
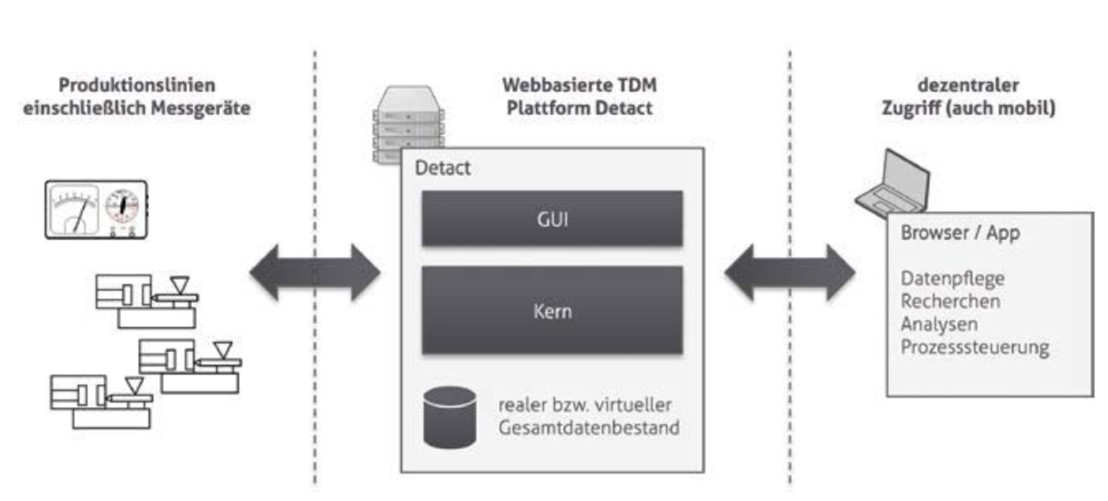
Ausbringung
S. Grund [14] beschäftigt sich mit Gießtechniken, welche die Energie- und Materialeffizienz erhöhen, speziell beim Zinkdruckgießen. Beim Warmkammerdruckgießverfahren kann der Anguss bis zu 100 % des Teilegewichts ausmachen. Der Anguss wird als Schrott wieder eingeschmolzen und führt trotz Umsetzung des Kreislaufgedankens zu erhöhtem Energiebedarf und Handlingsaufwand. Daher sollte bei jeder Gusskonstruktion versucht werden, Gießläufe und damit den Anguss zu minimieren. Bei einer Gehäuseklappe können so beispielsweise bis zu 2/3 des Kreislaufgewichts reduziert und gleichzeitig die Taktzeit um fast 40 % erhöht werden. Angussarme Zinkdruckgussteile werden als erster Schritt beschrieben, doch im nächsten Entwicklungsschritt sollten angussfreie Gussteile folgen. Teile ganz ohne Verteiler ermöglichen bei gleicher Auslegung einen Wechsel auf kleinere Druckgießmaschinen mit geringerer Schließkraft und kürzeren Zykluszeiten.
Schmelzbetrieb
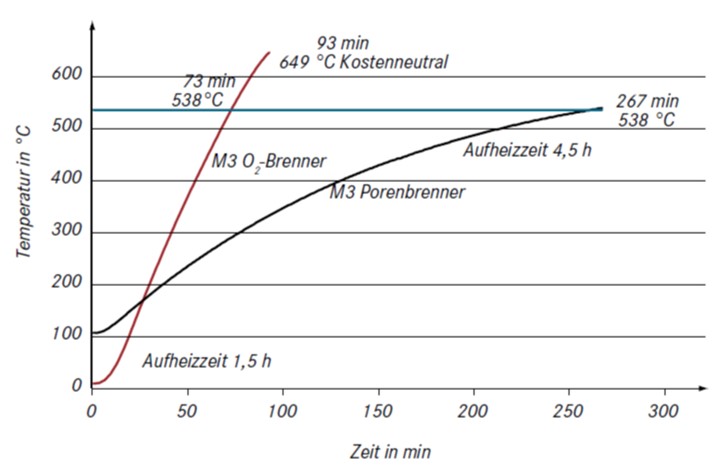
Der Energiebedarf eines Schmelzbetriebs ist vor allem abhängig von der Auslastung und der Betriebsweise des Gesamtbetriebes. Zusätzlich sind bei den Schmelzaggregaten selbst die Bauart und das Alter entscheidend. Gerade wenn es um Neuinvestitionen in einen „energieeffizienten Schmelzbetrieb“ geht, sind transparente und langfristig ausgelegte energiepolitische Rahmenbedingungen für Gießereien sehr wichtig. So diskutierten zuletzt beispielsweise zwei Geschäftsführer von Eisengießereien darüber, ob man zusätzlich zum gemischten Kupol- und Induktionsofenschmelzbetrieb auch zukünftig wieder auf kostengünstige erdgasbefeuerte Drehtrommelöfen setzen sollte.
Die Herstellung von Flüssigmetall in Eisen-, Stahl-, Nichteisen- und Buntmetallgießereien ist mit hohem Energieaufwand verbunden. Theoretisch wären weniger als 400 kWh im Schmelzbetrieb nötig, um 1 t Flüssigeisen zu schmelzen, allerdings sind es im Schmelzbetrieb in der Realität eher 600 kWh. E. Dötsch [15] nennt für den höheren Energiebedarf folgende Gründe:
- Setzen von sandbehaftetem Kreislaufmaterial,
- Warmhalten mit offenem Ofendeckel,
- ungedrosselte Absaugung beim Warmhalten,
- längeres Warmhalten durch mangelhafte Logistik und
- nicht sachgemäßes Chargieren.
Weitere begleitende Nebenprozesse wie Warmhalteöfen und Pfannenvorwärmung führen laut M. Jolly [16] letztendlich zu einem Gesamtenergiebedarf von über 1200 kWh/t Flüssigeisen. G. Deike [17] hebt jedoch hervor, dass durch die in den Schmelzbetrieben wieder eingesetzten Sekundärrohstoffe Kreisläufe entstehen, die unendlich wiederholt werden können und dabei sogar die Qualität der Metalle im Verlauf des Recyclings zu- anstatt abnimmt. Daher handelt es sich nicht um eine „alte Industrie“, sondern ganz im Gegenteil, bei den Prozessen in Gießereien handelt es sich um eine echte Zukunftstechnologie mit weitgehend geschlossenen Rohstoffkreisläufen gemäß des Cradle-to-Cradle-Konzepts (Ökoeffektivität/ Upcycling ist sichergestellt).
In Deutschland ist die Anzahl an Gießereien mit Kupolöfen im Schmelzbetrieb auf 57 gesunken, sodass mittlerweile mehr Flüssigeisen in Induktionsöfen als in brennstoffbefeuerten Aggregaten erschmolzen wird. Bestehende Aggregate werden kontinuierlich verbessert, um im Wettbewerb mit effizienten (Tandem-) Mittelfrequenz-Induktionsöfen zu bestehen. H. Kadelka und M. Weber [18] stellen eine Ofensteuerungssoftware für Kupolöfen vor, die sowohl einen präventiven als auch einen direkten Eingriff in den Schmelzprozess ermöglicht. Durch diese Optimierung der Prozessführung kann der Koksbedarf und damit auch der Energiebedarf pro t Flüssigeisen gesenkt werden. Zudem werden folgende Vorteile genannt:
- deutlich verbesserte Gichtgasführung,
- Vergleichmäßigung des Energiegehaltes des Gichtgases,
- reduzierte und gleichmäßige Saugzugleistung,
- geringerer Falschluftanteil über die Obergicht,
- geringerer Fremdenergieeintrag in der Brennkammer,
- engere Analysentoleranzen,
- gleichmäßigere Analysen,
- geringere Temperaturschwankungen und
- schnelleres Erreichen von Rinneneisen- und Heißwindtemperatur.
Ist der Temperaturwechsel durch Flüssigmetall in Transport- und Gießpfannen zu groß, führt dies zu höherem Verschleiß, kürzerer Lebensdauer der Ausmauerung und Schlackenanhaftungen. Die „auf die Schnelle durchgeführte Vorwärmung mit Hilfe von flüssiger Schmelze“ ist aufgrund der großen Temperaturwechsel als ungeeignet zu bezeichnen.
H. Kadelka und M. Weber [19] untersuchten anhand einer 4-t-Transportpfanne, ob man konventionelle Pfannenvorwärmung mit Luft-Erdgas-Brennern lieber durch Sauerstoff- (Oxyfuel) oder Porenbrenner ersetzt, um die Pfannen kontinuierlich betriebswarm zu halten. Wichtig sind bei der Pfannenvorwärmung zudem die zu den Pfannen passenden Abdeckungen. Beim Vergleich im Betrieb wurde die gewünschte Zieltemperatur durch die Sauerstoffbrenner nach einem Drittel der Aufheizzeit im Vergleich zum Porenbrenner erreicht (Bild 3). Sogar höhere Temperaturen konnten mit dem Sauerstoffbrenner erreicht werden, wohingegen die Erdgastemperatur beim Porenbrenner aus materialtechnischen Gründen begrenzt ist. Letztendlich kann sich der Sauerstoffbrenner nicht nur technisch, sondern auch in ökonomischen Belangen gegenüber dem Porenbrenner durchsetzen. Der Porenbrenner hingegen spielt seine Stärken vor allem bei der Pfannentrocknung, niedrigen Abgusstemperaturen und großen Wanddicken aus.
Ein Beispiel für eine Verbesserung der Energieeffizienz nennt R. Wamsbach [21] beim Retrofit zweier Radialgebläse an einem Heißwindkupolofen, die einen 5 % höheren Wirkungsgrad aufweisen und zusätzlich mit Frequenzumrichtern ausgestattet sind. Weitere Projekte werden auch genannt: So gibt es z. B. mehr als 20 Kühlwasserpumpen am Kupolofen, die ebenfalls Einsparpotenziale bieten.
In Nichteisenmetallgießereien ohne Teilentlastung bei der EEG-Umlage ist in den letzten Jahren ein Umstieg von elektrischen Schmelzöfen auf brennstoffbefeuerte Aggregate zu beobachten. M. Henniger u. a. [22] beschreiben das Projekt „Smart Melting“, bei dem eine Verringerung des Energiebedarfs durch bessere Abstimmung des Schmelz- und Druckgießbetriebs skizziert wird. Aufgrund von diskontinuierlicher Betriebsweise infolge von Aufheiz- und Abkühlvorgängen liegt der Energiebedarf in Aluminium-Schmelzbetrieben häufig 25 % über den Herstellerangaben und die Schmelzleistung am unteren Ende der Angaben des Ofenbauers. Daher sollte von Mitarbeitern im Schmelzbetrieb immer eine kontinuierliche Betriebsweise mit einem möglichst hohen Schachtfüllstand durch eine angepasste Beschickung der Einsatzmaterialien angestrebt werden. Ein wirksamer Indikator zur Messung der Effizienz des Ofens ist die Rauchgastemperatur, die abnimmt, wenn der Ofen möglichst effizient gefahren wird. Gleichzeitig lässt sich das Rauchgas nutzen, um das Einsatzmaterial bereits in einer Vorwärmkammer anzuwärmen. Tabelle 3 [23] zeigt beispielhaft die Kosteneinsparungen bei einem Erdgaspreis von etwa 3,5 ct/kWh und 300 Produktionstagen.
Dass sich der umgekehrte Fall ebenfalls lohnt, nämlich von brennstoffbefeuerten zu elektrischen Aggregaten zu wechseln, wenn der Schmelzbetrieb noch mit Heizöl betrieben wird, zeigt eine kleine Aluminium- und Magnesiumgießerei [24]. In Verbindung mit der Eigenstromerzeugung aus einer Fotovoltaikanlage konnte der Fremdenergiebedarf von etwa 380 000 kWh auf unter 100 000 kWh reduziert werden.
Bei Lichtbogenöfen in Stahlgießereien konnte der elektrische Wirkungsgrad seit den 1950er-Jahren bis heute von 88 % auf bis zu 94 % erhöht werden, sodass der Strombedarf pro t Flüssigstahl bis auf 720 kWh sank. P. Kuhlow und G. Sachse [25] betonen, dass auch beim Lichtbogenofen wie bei anderen Schmelzaggregaten eine bessere zeitliche Auslastung zu besseren Energiekennzahlen führt. Durch Verkürzung der Einschmelzzeiten können Wärmeverluste verringert werden, was gerade bei den im Vergleich zum Induktionsofen größeren Badoberflächen von entscheidender Bedeutung ist. Nachweise über vorbeugende Instandhaltung sollten nicht „nur“ für die Qualitäts-, Umwelt- und Energiemanagementnormen DIN EN ISO 9001/14001/50001 erbracht werden, sondern zur Routine werden, denn im Artikel beschriebene Nachlässigkeiten erhöhen unweigerlich den Energiebedarf und den Verschleiß an mechanischen Bauteilen und verkürzen die Lebensdauer ganzer Baugruppen. Es folgt eine Auflistung von möglichen Einflussfaktoren, die zu erfahrungsgemäß höheren Energieverbräuchen führen:
- Sperriger, unsauberer Schrott und zu hohe Schrottdichte,
- unregelmäßiges Schmelzen mit kaltem Ofen,
- Vernachlässigung der Wartungsmaßnahmen,
- ungenügende Reinigung der Anlage,
- Deformation, Beschädigung mechanischer Bauteile und
- unzureichend arbeitende Regelung und Fehler an elektrischen Baugruppen.
Durch ein schwenkbares Brennersystem, das mit Messtechnik zur sensorischen Erfassung gekoppelt wird, konnte laut B. Kuhnert [26] der Energiebedarf in einem Al-Schmelzofen um bis zu 15 % gesenkt werden. Entscheidend ist die Steigerung der Schmelzleistung durch das Schwenken der Brenner, ohne dass die Qualität der Schmelze beeinflusst wird.
K. Bloemen, F. Ebersold und J. Hesselbach [27] beschäftigen sich mit dem energieeffizienten Betrieb von Drehtrommelöfen zur Sekundaraluminiumerzeugung, bei der stark verunreinigte Vorstoffe aufgeschmolzen werden. Entscheidender Einflussfaktor für die Herstellung einer Al-Legierung aus Altschrotten ist die Wahl der richtigen Chargierzeitpunkte:
- Vorstoffe so schnell wie möglich chargieren und einschmelzen,
- möglichst schnell die Vorstoffe mit Abdecksalz abdecken,
- Reihenfolge und Zeitpunkte der Teilchargen nach ihrer Oxidationsneigung und ihrem Einschmelzverhalten anpassen,
- Türöffnungszeiten so gering wie möglich halten und
- unnötiges Überhitzen und Flüssighalten der Schmelze vermeiden.
Mittels geeigneter Maßnahmen sollten die richtigen Chargierzeitpunkte für die bis zu 10 Teilchargen gefunden werden. Je nach Altschrottanteilen schwankte der Energiebedarf zwischen 400 und 800 kWh/t Aluminiumlegierung. Bild 4 zeigt Unterschiede zwischen dem „Normalbetrieb“ und dem effizienten Betrieb mit messtechnischer Unterstützung. Durch das leistungsabhängige Chargieren konnten die Schmelzdauer etwa um 15 % verkürzt und der Energiebedarf um fast 18 % reduziert werden.
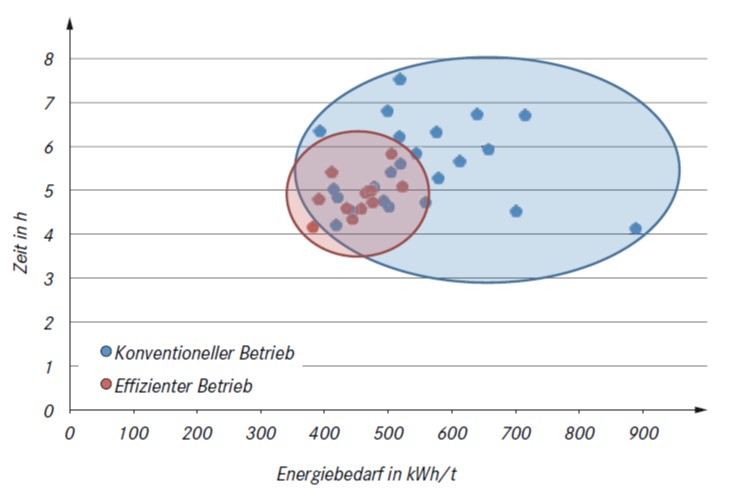
Nachfolgend werden von Morgan Advanced Materials fünf Punkte aufgelistet, die für eine energieeffiziente Zustellung von Schmelzöfen wichtig sind [29]:
- Die Außenwände sollten regelmäßig durch Infrarot-Thermografie geprüft werden, um heiße Stellen und mangelhafte Ausmauerung frühzeitig zu erkennen.
- Erkannte Schwachstellen an den Öfen sollten umgehend ausgebessert werden. Dabei können neuartige Isoliermassen oder ähnliche Ausmauerungsmaterialien bei Wartezeiten in den Ofen „gepumpt“ werden, um kleine Risse zu schließen.
- Verschiedene Zustellmaterialien sollten erprobt werden, wobei Schwindung und Ausbreitung der Materialien während des Schmelzens möglichst niedrig sein sollten.
- Es sollte nicht zu „dick“ und nicht „zu dünn“ ausgemauert werden. Zwar werden durch eine bewusst breite Ausmauerung des Ofens die Wärmeverluste geringer, aber im Endeffekt steigt auch der Energiebedarf.
- Schließlich sollte der Schmelzbetrieb optimal zum Flüssigmetallbedarf der Gießerei passen. Auch eine Kopplung von älteren Öfen im Monobetrieb zu einem Tandembetrieb kann den Energiebedarf pro t Flüssigmetall erheblich senken.
Abwärme
Wie kann man die Wärme am Kupolofen am besten speichern? Eine Möglichkeit wird aktuell in einem Forschungsprojekt mit einem Feststoffspeicher untersucht, der im Direktkontakt von einer Wärmeträgerflüssigkeit umströmt wird (Informationen zum Projekt unter forschungenergiespeicher.info/waerme-speichern/projektliste/projekt-einzelansicht/108/Giesserei_nutzt_Abwaerme_des_Schmelzofens). Wenn sich jedoch Strom und Wärme nicht speichern lassen und in Gießereien mehr Abwärme vorhanden ist als man in anderen Bereichen nutzen kann, besteht die Möglichkeit, die Abwärme zu verstromen. Kompakte ORC-Module können an verschiedenen Abwärmequellen in der Gießerei eingesetzt werden. J. Lechner [30] betont, dass sich zudem mehrere Module zu „Stacks“ verschalten lassen. Dadurch lassen sich auch größere Wärmequellen in Schmelzbetrieben verstromen, wodurch die Energiekosten durch kostengünstige Eigenstromerzeugung gesenkt werden können.
Leistungsfähige Wasserkühlungsanlagen an Induktionsöfen führen auch in betriebsfreien Zeiten zu einem hohen Energiebedarf, weil diese auch am Wochenende in Betrieb sind und in der Regel nicht über eine Drehzahlregelung verfügen. Bei einer Untersuchung der Grundlast an einem Wochenende wurde bei zwei Gießereien mit älteren Kühlanlagen eine Dauerlast von fast 50 kW gemessen. Ein intelligentes Wasserrückkühlsystem, das die Kühlleistung proportional zur Temperaturerhöhung und zur Durchflussmenge des Kühlwassers regelt, amortisierte sich in weniger als15 Monaten [31].
Bei Induktionsöfen mit einer Leistung von 8 MW fallen etwa 2 MW „Verlustwärme“ an. Somit bietet sich nicht nur Abwärme, die an brennstoffbefeuerten Schmelzaggregaten anfällt, für die weitere Nutzung (z. B. zur Fußboden- oder Hallenheizung oder zum Erwärmen des Brauchwassers) an, sondern auch die, die an Induktionsöfen auftritt. Bei neuen Aggregaten sollte die Möglichkeit zur weiteren Wärmerückgewinnung bereits vorgesehen sein. Z. B. beschreiben D. Eckl und D. Trauzeddel [32] das Vorgehen bei der Installation eines neuen Mittelfrequenz- Induktionsofens mit einer Schmelzleistung von 6 t/h, der Abwärme von etwa 1 MW bei etwa 60 °C zur weiteren Nutzung bereitstellt. Dazu sollten laut M. Dahmen [33] auch bestehende Induktionsöfen mit einem intelligenten Wasserrückkühlsystem nachgerüstet werden. Diese Frequenzumrichter gesteuerten Kühlkreispumpen können den Energiebedarf um bis zu 30 % senken. Um dann zusätzlich eine große Wärmemenge des Anlagenkühlwassers zu nutzen, sollten möglichst konstante und hohe Kühlwassertemperaturen gewährleistet sein.
Querschnittstechnologien
R. P. Jung [34] stellt fest, dass nur Arbeitsgänge wertschöpfend sind, die den Wert des Produktes erhöhen. Auch wenn es manchmal im Gießereialltagsbetrieb mit vielen Kundenaufträgen vergessen wird: Prüfen, Putzen, Nacharbeiten sowie innerbetriebliche Logistik sind kein Bestandteil der Wertschöpfung, sondern Verschwendung, die es nach Möglichkeit zu vermeiden gilt. Dies trifft auch für Druckluft zu – die teuerste Energieform im Gießereibetrieb überhaupt. Druckluft sollte im Betrieb sparsam eigesetzt werden. Kontinuierliche Druckluftaudits können „hörbare“ und mit dem richtigen Equipment auch „versteckte“ Verschwendung aufdecken. Die Energieagentur NRW zeigt seit Jahren bei ihren Vorträgen immer wieder folgende Top-6-Maßnahmenliste für Verschwendung im Bereich der Druckluftnutzung:
- Nichtnutzung der Abwärme (Verluste bis zu 94 %),
- Leckagen (bis 30 %),
- fehlende Kompressorsteuerung (bis 25 %),
- veraltete Technik (bis 15 %),
- ungenutzte Substitutionspotenziale (bis 15 %) und
- Druckverluste (bis zu 10 % pro bar).
Viele Gießereien haben daher in den letzten Jahren bei der Drucklufterzeugung angesetzt und dezentrale Kompressorstationen zentralisiert. M. Gaar [35] stellt eine mobile Containerlösung bei einem Formbauer vor, bei der zwei Grundlastkompressoren mit einem drehzahlgeregelten Aggregat für die Spitzenlast gekoppelt werden. Insgesamt wurde der Strombedarf für die Drucklufterzeugung um 30 % gesenkt. Durch zusätzliche Abwärmenutzung wurden weitere 30 % im Bereich der Hallenheizung eingespart.
Im Bereich der Putzerei wird immer wieder sowohl mit Elektroschleifmaschinen als auch mit Druckluftschleifern gearbeitet. Bei Umbaumaßnahmen oder Neugestaltung von Putzereien werden jedoch Pneumatikwerkzeuge bevorzugt, weil diese seltener ausfallen, geringere Vibrationen aufweisen und sich durch geringeres Gewicht und damit verbunden durch eine bessere Wendigkeit auszeichnen. H. Wenke [36] beschreibt den Neuaufbau von Schleifkabinen, die ausschließlich mit Druckluftwerkzeugen mit
Turbinenmotor ausgestattet werden. In Verbindung mit Kompressoren mit Schraubenverdichter und integriertem Kältetrockner konnte der Druckluftbedarf um über 30 % gesenkt werden.
R. Thormann [37] berichtet über die Installation von insgesamt 10 Schraubenverdichtern mit jeweils 250 kW Antriebsleistung, die bei gleicher Leistung über
10 % mehr Druckluft liefern als vergleichbare Kompressoren. In Verbindung mit einer automatischen Steuerung können alle Leistungsdaten in Echtzeit visualisiert werden, und Fehlermeldungen werden direkt vom System per SMS oder E-Mail an die Instandhaltung gesendet.
Um sowohl die Erzeugung als auch die Verwendung von Druckluft effizient zu gestalten, setzen Gießereien in vielen Anwendungsbereichen auf Energiespardüsen. A. Golibrzuch [38] stellt ein spezielles Modell dieser Düsen für Warmkammerdruckgießmaschinen vor, die den Strombedarf im Vergleich zu herkömmlichen Düsen um über 50 % senken.
Die europäische Ökodesign-Richtlinie hat zu Herstellungs- und Vertriebsverboten von Lampen mit geringer Energieeffizienz geführt, u. a. sind davon die in Gießereien häufig verwendete Quecksilberdampflampen betroffen. M. Oberliesen, M. Tippel und T. Herweg [39] beschreiben beispielsweise die Umrüstung von 80 Lampen mit jeweils 430 Watt in zwei Hallen einer Gießerei. Durch die Umrüstung auf LED sank die Leistung auf 200 Watt pro Leuchte. Durch den gleichzeitigen Einbau einer automatischen Steuerung von Lichtsensoren, können die Leuchten zwischen 10 und 100 % gedimmt werden. Während tagsüber die Leuchten deutlich gedimmt werden, werden gegen Nachmittag und vor allem am Abend auch weiterhin annähernd gleiche Lichtverhältnisse wie am Tag gewährleistet. Die Hersteller versprechen, dass die LEDs mindestens doppelt so lange bzw. sogar vier Mal länger als die alten Quecksilberdampflampen halten. Insgesamt konnten nach dem Umbau so bis zu 70 % der Stromkosten für die Beleuchtung in den Hallen eingespart werden. Wenn die Mittel für solche Investitionen nicht verfügbar sind, könnte auch ein von S. Gladkov [40] vorgestelltes Mietmodell die Lösung sein. Nach Abzug der Mietzahlungen bleiben Einsparungen bei den Beleuchtungskosten von etwa 15 %. Die alten Halogenstrahler sorgten jahrelang 24 Stunden am Tag für eine gleichmäßige Ausleuchtung, mussten allerdings regelmäßig ausgetauscht werden. Daher wurden wie in Bild 5 dargestellt robuste LED-Industrieleuchten ausgewählt, die spritzwasserfest und staubdicht sind sowie eine hohe Wärmetoleranz aufweisen. Mittlerweile haben schon einige Gießereien auch im Schmelzbetrieb die Beleuchtung auf LED umgestellt, und sowohl für Mitarbeiter als auch für Außenstehende gibt es nun „deutlich sichtbar besseres“ Licht, was auch zu spürbar mehr (Arbeits-)Sicherheit beiträgt.
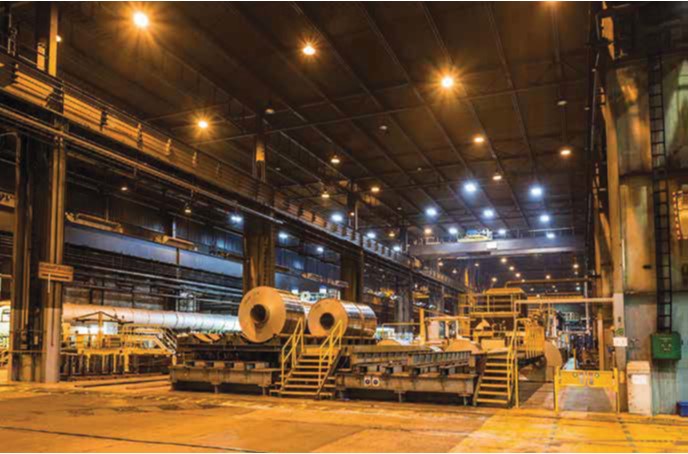
Umweltschutz
Bereits in der letzten Jahresübersicht wurde das Thema „Gießereiprodukte und ihr Mehrwert bei Lebenszyklusbetrachtungen“ beschrieben. Lebenszyklusanalysen sollen Gießereien helfen, ökologische Auswirkungen verschiedener Gussteile zu bewerten und danach strategische Entscheidungen für das „richtige Bauteil“ zu treffen. Zahlreiche internationale Datenbanken können dabei unterstützen, eine detaillierte Datenanalyse durchzuführen und so beispielsweise die Umweltauswirkungen von Fahrzeugen bestimmen und vergleichen zu können. Besonders beliebt, jedoch auch umstritten, ist in Gießereien auch der Vergleich zwischen verschiedenen Werkstoffen, um jeweils die eigenen Vorteile z. B. beim Gusseisen- oder Aluminiumzylinderblock hervorzuheben.
In einem Forschungsprojekt haben M. Topic u. a. [42] ein idealtypisches 10-kg-Gusseisenteil in der Serienproduktion untersucht und die direkten CO2-Emissionen aus dem Gießprozess in einer Tabelle bewertet (Tabelle 4) [43]. Die Autoren betonen, dass diese Auswertung auch eine gute Grundlage für die energetische Ausgangsbasis im Rahmen eines Energiemanagementsystems nach DIN EN ISO 50001 oder eines Energieaudits nach DIN EN 16247-1 liefert. Es ist daher nicht verwunderlich, dass der Schmelzbetrieb und die abschließende Wärmebehandlung die höchsten Treibhausgasemissionen verursachen.
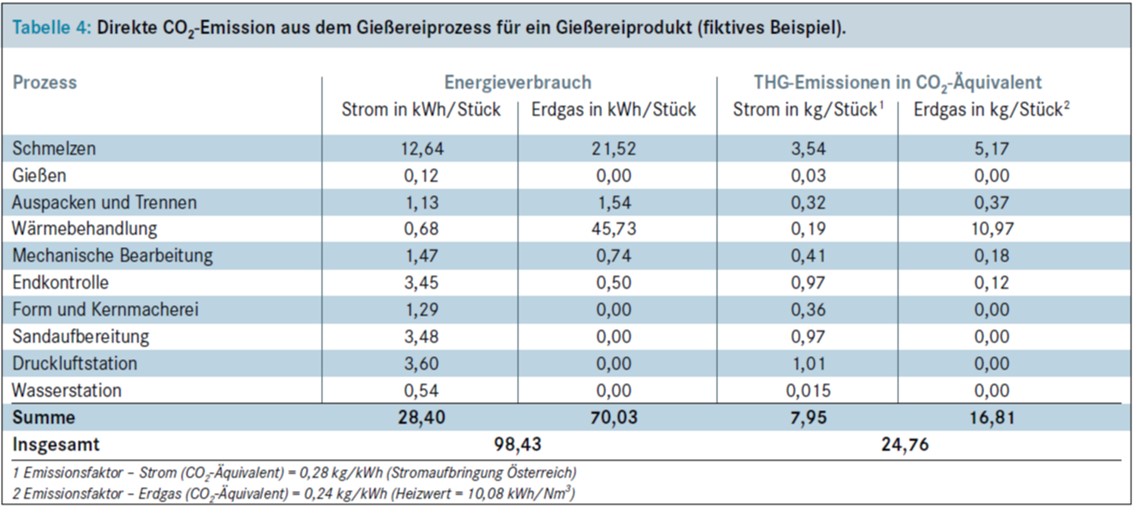
Die aktuelle Fassung der Technischen Anleitung zur Reinhaltung der Luft (TA Luft) aus dem Jahr 2002 wird derzeit überarbeitet. In der TA Luft werden u. a. für Gießereien Anforderungen und Grenzwerte bei Immissionen und Emissionen für bestimmte Luftschadstoffe bundeseinheitlich verbindlich festgesetzt und der Stand der Technik konkretisiert. Genau wie bei der geplanten Mantelverordnung, welche die neue Ersatzbaustoffverordnung und die Neufassung der Bundesbodenschutzverordnung enthält, wird die neue TA Luft voraussichtlich nicht mehr im Jahr 2017 im Bundestag und -rat verabschiedet. Umso wichtiger ist es bei Neu- und Umbauten auf Abluftreinigungslösungen zu setzen, die Verunreinigungen durch Schad- und Geruchsstoffe deutlich reduzieren. Ein Beispiel für eine Anlage zur Abluftreinigung liefert F. Hartung [44] mit einer Pilotanlage. Diese lässt sich sowohl als kompletter Ersatz für bestehende Reinigungsvorrichtungen nutzen, oder sie kann bestehenden Filtern auch vorgeschaltet werden, um die Reinigungsleistung zu erhöhen. Damit der Energiebedarf der Abluftreinigung insgesamt gesenkt werden kann, werden der Verschmutzungsgrad der Luft kontinuierlich gemessen und die Reinigungsleistung entsprechend angepasst. Bei Tests konnten BTEX um bis zu 97 %, Amine bis zu 99,99 % und der Gesamtkohlenwasserstoff bis zu 95 % aus der Abluft entfernt werden.
Radcliffe [45] berichtet über die erfolgreiche Realisierung von Maßnahmenumsetzungen im Anschluss an ein „Luftmanagement- Audit“ in einer 16 Jahre alten Aluminiumgießerei aus Wales. Vor dem Audit konnten drei Eingangs- und drei Ausgangslüfter keine optimalen Umgebungsbedingungen bieten, obwohl sie
dauerhaft 24 h an sechs Tagen pro Woche in Betrieb waren. Im Anschluss an das Audit wurden innerhalb von 12 Wochen fünf Luftaufbereitungsanlagen installiert, die von 18 unterschiedlichen Be- und Entlüftungen unterstützt werden. Dieses System ist nun in der Lage, abhängig von den Außentemperaturen, die angesaugte Außenluft zu erwärmen oder zu kühlen. Der Umbau hat eine bessere Ausleuchtung der Arbeitsplätze und ein deutlich besseres Arbeitsklima für die Mitarbeiter zur Folge und nach etwa drei Jahren soll sich die Investition „in bessere Luft“ amortisieren.
Um Schmier- und Trennmitteldämpfe zu reinigen, hat sich ein Aluminium-Druckgießer für einen Elektroabscheider entschieden. Dieser ermöglicht eine Rückführung der gereinigten Luft in die Gießhallen. Dazu wird der Luftstrom im Vorabscheider erst von groben Partikeln gereinigt, anschließend werden die restlichen luftfremden Teilchen im eigentlichen Abscheider entfernt [46].
W. Neun und M. Poetzsch [47] möchten den strengen Emissions- und Arbeitsplatzgrenzwerten in Eisen- und Stahlgießereien mit einem neuen auf Phenolharz basierenden Cold-Box-Binder begegnen. Ziel war es, komplett auf kennzeichnungspflichtige Inhaltsstoffe zu verzichten. Gleichzeitig sollten die Bindermengen reduziert werden. Die im Folgenden genannten drei spezifische Emissionsquellen sollten mit dem neuen Binder reduziert werden:
- leicht flüchtige Komponenten während der Kernherstellung,
- Phenol- und Formaldehydmonomere während des Abgießens,
- Benzol-Emissionen im Speziellen bzw. BTX-Emissionen im Allgemeinen während der Gießphase.
Ein Langzeittest in einer Eisengießerei zeigte schließlich, dass eine Binderreduktion von mehr als 20 % möglich ist und dabei zusätzlich die Benzolemissionen beim Abgießprozess um 2/3 sinken. Zudem sind auch die Phenolemissionen beim Produkt Ecocure Blue deutlich niedriger Bild 6. Des Weiteren kann die Reduktion des Phenolgehaltes im Altsand zu einer Einstufung in niedrigere Deponieklassen führen, was niedrigere Entsorgungskosten zur Folge hat.
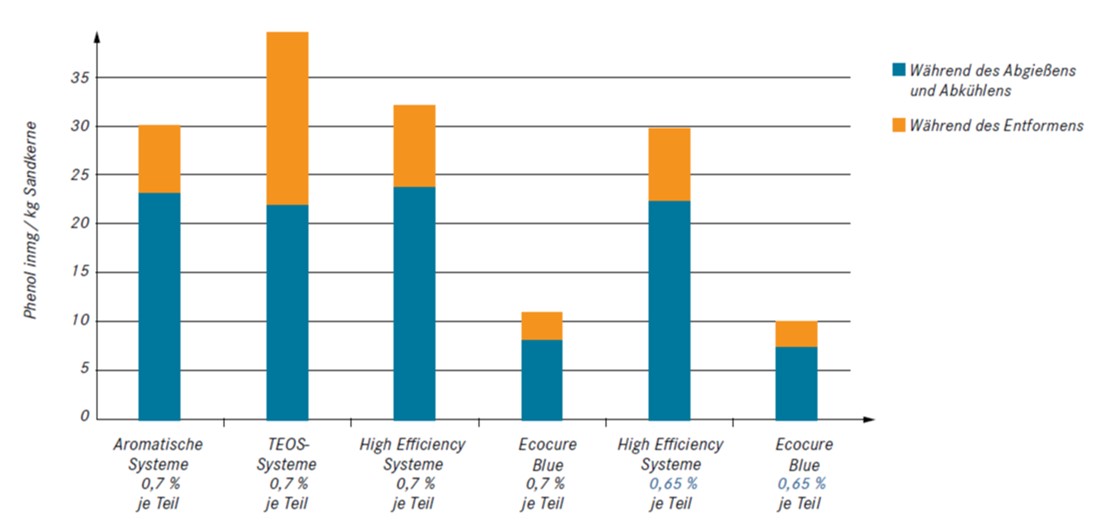
S. Umla-Latz [49] erläutert, dass es bei Bindersystemen mit einem hohen Schwefelanteil zu Schmelze-Formstoff- Reaktionen kommt, die zu pockenartigen Aufrauungen und Vertiefungen an den Gussoberflächen führen. Eine Kleinserien-Handformgießerei hat daher ein schwefelreduziertes Furanharz-Bindersystem für die Form- und Kernherstellung eingeführt. Dieses Bindersystem führt zu höheren Festigkeiten im Formstoff und gleichzeitig durch geringere Harzzugabe zu niedrigeren Emissionen beim Abgießen. Ferner können Furan-No-Bake-Binder besser regeneriert und länger im Sandkreislauf gefahren werden, wenn bei der Aufbereitung darauf geachtet wird, dass bestimmte Grenzwerte für die Anreicherung von Schwefel nicht überschritten werden.
In Nichteisenmetallgießereien wird die anorganische Kernbinder-Technologie vorangetrieben, um ein „emissionsfreies Gießen“ zu ermöglichen. Zwar steigt laut R. Boehm [50] der Energiebedarf in der Kernherstellung durch Begasung des Wasserglasbinders mit auf 130 °C erwärmter Luft. Diese höheren Energiekosten können jedoch auf der anderen Seite durch die Reduzierung der Absaug- und Luftreinigungsleistung mehr als ausgeglichen werden. Eine Herausforderung bei anorganisch gebundenen Kernen ist weiterhin die Lagerstabilität unter feucht-warmen Bedingungen. Daher kommen beispielsweise Gießereien mit längeren Lagerzeiten in subtropischen Zonen bei anorganischen Bindern nicht daran vorbei, Kernlagerbereiche zu klimatisieren und diese Bereiche genau zu überwachen. Neue anorganische Bindersysteme können ansonsten nur etwa fünf Tage Lagerstabilität bei 30 °C und 70 % Luftfeuchtigkeit garantieren, bevor die Festigkeit der Kerne verloren geht.
E. Müller [51] beschreibt die Vorteile des Mikrosprühens beim Aluminiumdruckgießen. Durch diese Minimalmengenschmierung sollen ermüdungsbedingte Risse in Folge der Temperaturwechselbelastung an den Formoberflächen verhindert und die Formstandzeit erhöht werden. Neben der Verlängerung der Formstandzeit stellt E. Müller weitere Effizienzvorteile fest, die er in einem weiteren Beitrag auflistet [52]:
- Verkürzung der (Sprüh-)Zykluszeiten um mehr als 10 %,
- niedrigere Energiekosten durch Reduzierung des Druckluftbedarfs am Sprühkopf und geringerer Heiz- und Kühl(geräte-)bedarf und
- Senkung des Wasserverbrauchs beim Sprühprozess auf null bei gleichzeitiger Reduzierung des Trennmittelverbrauchs um fast 80 %.
Dipl.-Kfm. Manuel Bosse, BDG-Service GmbH, Düsseldorf
Literatur:
[1] Giesserei 103 (2016), [Nr. 9], S. 21.
[2] Institut für Energie- und Umweltforschung Heidelberg GmbH, www.ifeu.de/index.php=
[3] Giesserei 104 (2017), [Nr. 5], S. 37-44.
[4] Giesserei-Rundschau (2010), [Nr. 9-10], S. 190-194.
[5] Giesserei 103 (2016), [Nr. 12], S. 26-29.
[6] (https://www.continental-corporation.com/de/presse/pressemitteilungen/innovatives-radkonzept-und-bremskonzept-fuerelektrofahrzeuge-92494).
[7] Giesserei 104 (2017), [Nr. 5], S. 80-83.
[8] Giesserei 104 (2017), [Nr. 5], S. 82.
[9] Giesserei 104 (2017), [Nr. 5], S. 108-109.
[10] Giesserei 104 (2017), [Nr. 5], S. 110-115.
[11] Giesserei 104 (2017), [Nr. 5], S. 85.
[12] Giesserei 104 (2017), [Nr. 7], S. 62-67.
[13] Giesserei 104 (2017), [Nr. 8], S. 20-23.
[14] Giesserei 103 (2016), [Nr. 9], S. 36-38.
[15] Giesserei-Praxis (2016), [Nr. 6], S. 232-236.
[16] Foundry Trade Journal (2016), [Nr. 6], S. 144-145.
[17] Giesserei 104 (2017), [Nr. 6], S. 64-72.
[18] Giesserei 102 (2015), [Nr. 8], S. 72-76.
[19] Giesserei 104 (2017), [Nr. 2], S. 74-81.
[20] Giesserei 104 (2017), [Nr. 2], S. 77.
[21] Giesserei 104 (2017), [Nr. 1], S. 58-61.
[22] Giesserei 104 (2017), [Nr. 3], S. 48-55.
[23] Giesserei 104 (2017), [Nr. 3], S. 52.
[24] Giesserei 104 (2017), [Nr. 8], S. 9.
[25] Giesserei 104 (2017), [Nr. 2], S. 42-48.
[26] Giesserei 104 (2017), [Nr. 5], S. 104-107.
[27] Giesserei 104 (2017), [Nr. 5], S. 52-57.
[28] Giesserei 104 (2017), [Nr. 5], S. 56.
[29] Foundry Trade Journal (2017), [Nr. 5], S. 110-111.
[30] Giesserei 103 (2016), [Nr. 12], S. 72-74.
[31] Gießerei-Erfahrungsaustausch (2016), [Nr. 9+10], S. 42-43.
[32] Giesserei 103 (2016), [Nr. 11], S. 44-45.
[33] Giesserei 103 (2016), [Nr. 10], S. 70-73.
[34] Giesserei 103 (2016), [Nr. 12], S. 50-51.
[35] Giesserei 103 (2016), [Nr. 9], S. 40-41.
[36] Giesserei 102 (2015), [Nr. 8], S. 58-61.
[37] Giesserei 104 (2017), [Nr. 6], S. 56-59)
[38] Giesserei 104 (2017), [Nr. 4], S. 76-78.
[39] Giesserei 104 (2017), [Nr. 6], S. 60-61.
[40] Giesserei 104 (2017), [Nr. 6], S. 62-63.
[41] Giesserei 104 (2017), [Nr. 6], S. 63.
[42] Giesserei 104 (2017), [Nr. 7], S. 30-37, Foundry Trade Journal (2017), [Nr. 3], S. 57-62.
[43] Giesserei 104 (2017), [Nr. 7], S. 36.
[44] Giesserei 103 (2016), [Nr. 12], S. 69-71.
[45] Foundry Trade Journal (2017), [Nr. 7/8], S. 164-165.
[46] Giesserei 104 (2017), [Nr. 5], S. 102-103.
[47] Giesserei-Rundschau (2017), [Nr. 3], S. 12-18, i. V. m. Giesserei-Rundschau (2016), [Nr. 11-12], S. 263-269.
[48] Giesserei 103 (2016), [Nr. 10], S. 44.
[49] Giesserei 104 (2017), [Nr. 2], S. 50-53.
[50] Giesserei 103 (2016), [Nr. 12], S. 30-35.
[51] Giesserei 103 (2016), [Nr. 6], S. 78-80.
[52] Giesserei 103 (2016), [Nr. 12], S. 64-67.