Umweltschutz und Energietechnik (1. Folge)
Von Horst Wolff Und Manuel Bosse, Düsseldorf
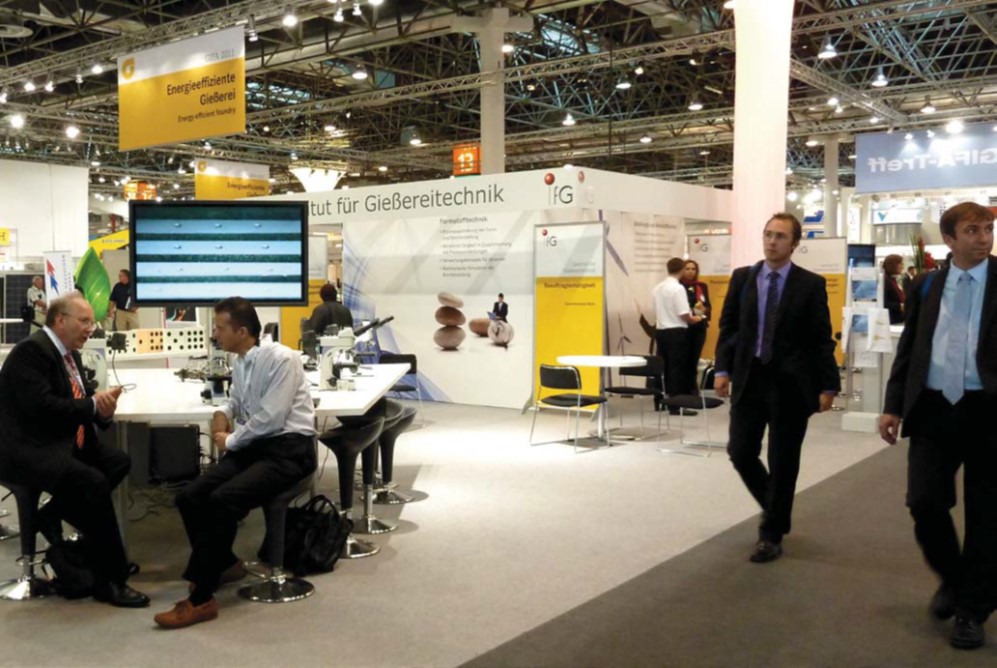
Erschienen in GIESSEREI 06/2013
Umweltschutz
Klassische, nachgeschaltete Maßnahmen des Umweltschutzes wie Einrichtungen zur Entstaubung sind technisch ausgereift. Die Schwerpunkte in der Entwicklung des Umweltschutzes in der jüngeren Vergangenheit lagen im sogenannten prozessintegrierten Umweltschutz – Beispiel: Vermeidung von Gerüchen und Schadstoffen in Gießgasen – und in der Energietechnik – u. a. zur Verminderung von Kohlendioxid emissionen.
Die deutsche Bundesregierung ist bekanntermaßen im internationalen Vergleich besonders engagiert im Klimaschutz und so verwundert es nicht, dass bei Sichtung des internationalen Schrifttums auf dem Gebiet der Energieeffizienz die meisten Entwicklungen in deutschen Unternehmen durchgeführt worden sind.
T. Wysocki u. a. [1] stellen Instrumente zur Entwicklung nachhaltiger Leichtbaukomponenten in einer Artikelreihe vor. Der Verein Deutscher Ingenieure (VDI), Düsseldorf, definiert den Begriff „Nachhaltigkeit“ für kleine und mittelständische Unternehmen wie folgt: „Nachhaltiges Wirtschaften verknüpft die Vorgehensweisen erfolgreichen Wirtschaftens mit Forderungen nach ökologischer Verträglichkeit und sozialer Gerechtigkeit und bringt sie in ein ausgeglichenes Verhältnis.“ Für Gießereien übersetzt, bedeutet das: Gießereien mit ihren Belegschaften und ihren Prozessen sowie mit ihren Produkten, den gegossenen Bauteilen, müssen sich zukunftsfähig aufstellen. Die zukünftigen Produkte einer Gießerei müssen an der zukünftigen Nachfrage orientiert sein, die Gussteile müssen mit prozesssicheren und produktiven Technologien gefertigt werden und die Arbeitssituation sowie die Qualifikation der Mitarbeiter und Mitarbeiterinnen müssen den zukünftigen Anforderungen entsprechen. Innerhalb des
vom Bundesministerium für Bildung und Forschung (BMBF) geförderten Verbundprojektes „LeiKom – Nachhaltige und innovative Produktion von Leichtbau-Komponenten“ wurden vom Institut für Gießereitechnik (IfG), Düsseldorf, und von Industriepartnern Hilfsmittel für das nachhaltige Wirtschaften in Gießereien erarbeitet. Im Teil 1 [1] werden die Entwicklungen in verschiedenen, für Gießereien interessanten Abnehmerbereichen beschrieben, relevante Leichtbaukenngrößen erläutert und Lösungskonzepte für Leichtbauprobleme aufgeführt. Teil 2 [2] befasst sich mit den Themen Informationsbeschaffung, systematische Leichtbaukonzeption für Gussteile und -werkstoff und -fertigungsgerechte Gestaltung. In diesem Teil wird auf wichtige Quellen der Informationsbeschaffung zum Thema Leichtbau eingegangen. Es werden Wege zur leichtbaugerechten Konstruktion aufgezeigt und Hinweise zur werkstoff- und fertigungsgerechten Gestaltung gegeben. In Teil 3 [3] werden Fallstudien des Leichtbaus erläutert (Bild 1). Dabei werden technische und wirtschaftliche Aspekte des Leichtbaus betrachtet. Teil 4 [4] befasst sich mit der Strategie der Nachhaltigkeit im Personalwesen. Die Ausführungen widmen sich den Erfahrungen in der Umsetzung von Maßnahmen, Methoden und Instrumenten, die Unternehmen auf dem Weg zur Entwicklung eines nachhaltigen Personalmanagements begleiten.
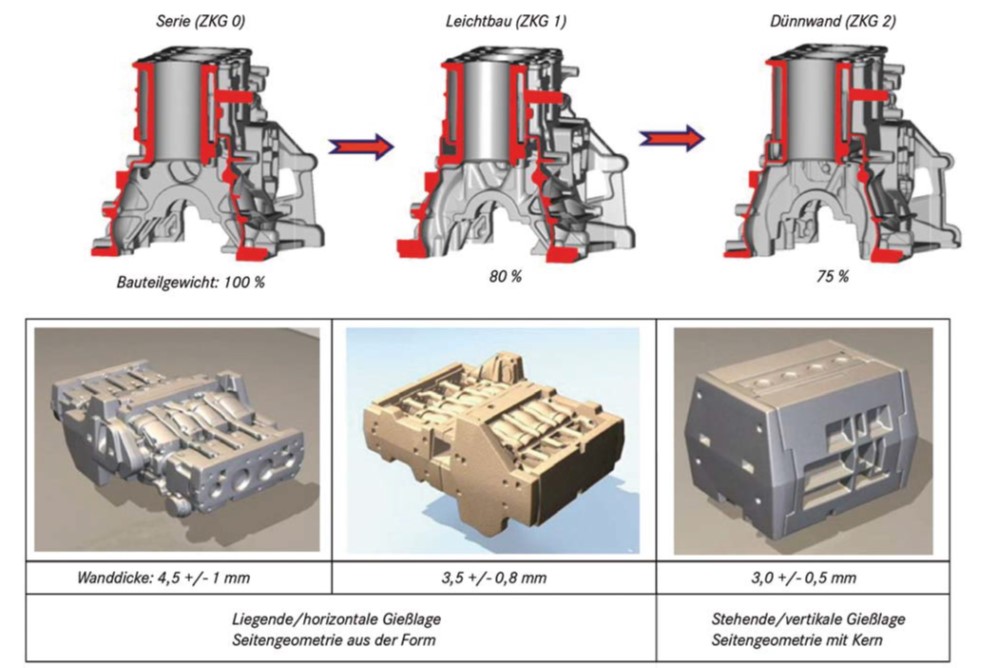
Ein Schwerpunkt des Umweltschutzes war im Berichtszeitraum die Vermeidung von Schadstoffen und Geruchsstoffen durch die Umstellung auf anorganische Bindemittel in der Kernherstellung. Ein Special zum Thema „Umweltverträgliche Bindersysteme“ gab es in drei Teilen in der Zeitschrift Giesserei.
H. Wolff [5] sieht in der Entwicklung der Formstoffbindemittel ein Beispiel für Spitzenforschung in Deutschland. In den fünfziger, sechziger und siebziger Jahren des 20. Jahrhunderts stand die Entwicklung höherer Produktivität bei der maschinellen Kernherstellung im Vordergrund. Die großen Entwicklungsschritte waren gekennzeichnet durch das Kohlensäureerstarrungs-, das Hot-Box- sowie das Urethan- Cold-Box-Verfahren. Diese führten zu einer höherer Prozesssicherheit und einer höherer Produktivität. Mit den 1980er Jahren trat in Deutschland die Gefahrstoffverordnung mit verschärfenden Vorschriften im Arbeitsschutz und mit Grenzwerten am Arbeitsplatz – kurz MAK-Werte (MAK = maximale Arbeitsplatzkonzentration) – in Kraft. Deutlich höhere Ansprüche im Immissionsschutz regelte 1986 die TA Luft. Nach kurzer Zeit gelang es den Herstellern von chemischen Bindern neuartige Systeme zu entwickeln und auf den Markt zu bringen, die deutlich weniger Schadstoffe freisetzten. In den 1990er Jahren kam eine weitere gesetzliche Vorschrift hinzu, die Geruchsimmissionsrichtlinie GIRL, und mit ihr wurde der Immissionsschutz noch erweitert und noch anspruchsvoller.
Waren die Bindemittel hinsichtlich ihrer Gefahrstoff- und Schadstofffreisetzungen bereits verbessert worden, so kam mit der Aufgabe, geruchsgeminderte Einsatzstoffe zu entwickeln, eine noch anspruchsvollere Aufgabe auf die Firmen zu. Es wurden mit veränderten Bindemitteln und mit intensiven Entwicklungsarbeiten relevante Geruchsstoffe erkannt und zum Teil bereits eliminiert. In den vergangenen Jahrzehnten stiegen die Ansprüche der Gesellschaft, des Gesetzgebers und der Auf sichtsbehörden stetig. In diesem Zeitraum wurde nicht nur der technische Stand bei chemischen Bindern gesteigert und die Qualität der freigesetzten Abluft verbessert, es änderte sich auch an vielen Stellen die Kommunikation. Der Informationsaustausch zwischen den Vertretern der Gießereien und der gesamten Gießerei-Industrie mit den Vertretern von gesetzgebenden Stellen, Vollzugsbehörden und den Vertretern der Berufsgenossenschaft sowie Vertretern der Öffentlichkeit wurde intensiver und offener. Zudem half die immer weitergehende Verbesserung der Luftqualität, das Image der Gießerei-Industrie und der einzelnen Betriebe zu verbessern. Die Altersstruktur in unserer Gesellschaft verschärft zunehmend den Wettbewerb um qualifizierte Fachkräfte und den Nachwuchs. Für Gießereien ist es somit auch eine existenzsichernde Maßnahme geworden, attraktive Arbeitsplätze anbieten zu können und für ein gutes Image der Gießerei-Industrie zu sorgen. In diesem Sinne sind die erfolgreichen Entwicklungen auf dem Formstoffsektor in den vergangenen Jahren äußerst hilfreich gewesen: Die organisch gebundenen Formstoffe setzen deutlich weniger Schad- und Geruchsstoffe frei und die Entwicklung von anorganischen, praktisch emissionsfreien Bindemitteln ist auf einem guten Weg.
A. Schrey [6] berichtet über emissionsreduzierte PUR-Cold-Box-Binder. Umweltauflagen seitens der Genehmigungsbehörden und wachsender Kostendruck durch den globalisierten Gießereimarkt erfordern eine kontinuierliche Weiterentwicklung aller Fertigungsschritte innerhalb der Gießerei-Industrie. Betriebe sind daher aufgefordert,
nicht wertschöpfende Arbeitsschritte zu vermeiden, um die Produktivität zu erhöhen. Gleichzeitig ist die Belastung des Arbeitsumfelds und der Umwelt durch Lärm-, Geruchs- und Schadstoffemissionen soweit wie technisch möglich zu reduzieren reduzieren. Dies bedeutet für Kernmachereien, dass neu entwickelte Bindemittel eingesetzt werden sollten, die eine wirtschaftlichere Kernfertigung ermöglichen und zugleich weniger Emissionen während der Kernherstellung und der späteren thermischen Belastung beim Gießen freisetzen.
A. C. Psimenos, M. M. Sipos und G. Eder [7] stellen ein neues Alphaset-Harz vor, das umweltverträglicher ist. Hiernach ist es mit einem im Jahr 2007 durchgeführten Entwicklungsprojekt gelungen, ein neues, alkalisches Resolphenolharz und die dazu abgestimmten Esterhärter zu entwickeln.
H. Polzin und D. Franzen [8] berichten über Tagungsergebnisse der WFO-Kommission 1.6 „Anorganische chemische Binder“ 2008 mit neuesten Entwicklungen.
T. Steinhäuser [9] hat sich mit der Regenerierung von AWB-Kernsanden erfolgreich auseinandergesetzt. Es konnte in umfangreichen Versuchsreihen nachgewiesen werden, dass der Ansatz eines Umlaufsandes mit teilweiser Reaktivierung des anhaftenden Binders für Sande möglich ist (Bild 2). Dies gilt für Sandmischungen ohne sowie mit Additiven zur Oberflächenverbesserung. Die Kornvereinzelung und Abreinigung ist mit einfachen, handelsüblichen mechanischen Anlagen möglich und damit kostengünstig. Eine gute Entstaubung des Regenerats ist von entscheidender Bedeutung für die Verwendung des Umlaufsandes. Allerdings gilt, dass diese Regenerate nicht mit Kunstharzbindern aller Art kompatibel sind. Sie müssen getrennt gehalten werden, da die Binderreste mit Kunstharzen zu unerwünschten Reaktionen führen. Wenn diese Randbedingungen eingehalten werden, eröffnet sich besonders für das Kokillengießen eine kostengünstige und umweltfreundliche Alternative zu den heute üblichen Systemen mit kunstharzgebundenen Kernen und thermischer Regenerierung. Insbesondere können der Energieverbrauch und der CO2-Ausstoß dadurch deutlich gesenkt werden.
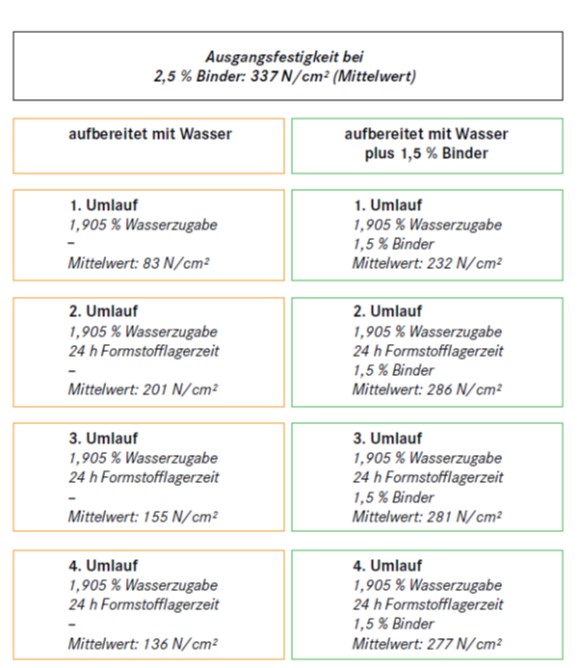
H. Polzin [10] stellt das Bindersystem Cast Clean vor und sieht vielfältige Wege zu Formen und Kernen (Bild 3). Dieses Bindersystem reiht sich in die Palette der heute verfügbaren anorganischen Bindersysteme ein und soll einen Beitrag zur Verbesserung der Arbeitsatmosphäre in Gießereien sowie zum Umweltschutz leisten. Die Bindersysteme auf Alkalisilicatoder Wasserglasbasis sind hauptsächlich anorganisch und in einigen Fällen in geringem Umfang auch organisch modifiziert. Die Binder werden als Einkomponentensystem angeboten, wobei prinzipiell auch die Lieferung von Mehrkomponentensystemen möglich ist. Nutzbar sind diese Binder zur Form- und Kernherstellung in allen bekannten Verfestigungstechnologien für Wasserglasbindersysteme und können in Aluminium-, Kupfer- sowie Eisen- und Stahlgießereien eingesetzt werden. Ziel ist es, gemeinsam mit dem Kunden eine maßgeschneiderte anorganische Binderlösung für die jeweils gestellte technologische Aufgabe zu finden.
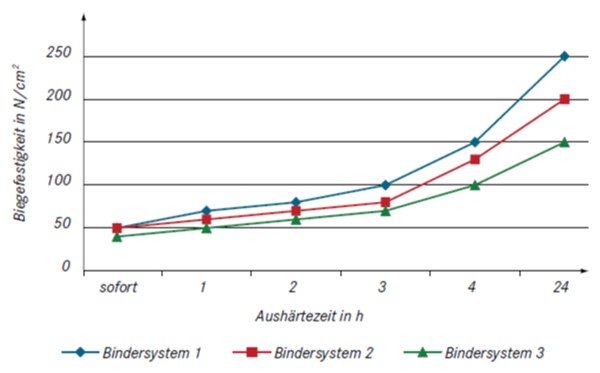
U. Pohlmann und U. Knobloch [11] berichten über eine Entwicklung umweltverträglicher Gießereiprozesse mit emissionsgeminderten Bindersystemen. Alle im Technikumsversuch erfassten Ergebnisse wurden auf ihre Praxistauglichkeit hin untersucht. Hierzu wurden Großapparaturen entwickelt, mit denen es möglich gemacht wurde, auch Emissionen von größeren Gussteilen zu detektieren (Bild 4). Des Weiteren wurde im Rahmen der Praxisversuche eng mit dem Institut für Gießereitechnik (IfG), Düsseldorf, zusammengearbeitet. Am IfG ermittelten Probanden die Geruchsintensität beim Abgießen. Es ließen sich nicht nur Aussagen hinsichtlich der Zusammensetzung und Menge der Hauptgeruchsträger treffen, sondern auch qualifizierte Angaben über die Geruchsbelastung für den Mitarbeiter und die Umwelt tätigen.
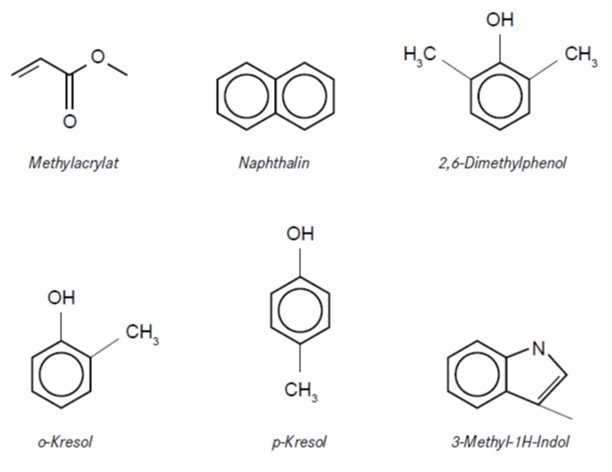
Das Special schließt mit den Beiträgen von A. C. Psimenos, W. Scheitz, und G. Eder [12] über No-Bake-Harzsysteme mit stark reduziertem Monomergehalt und M. Faller und A. Mössner [13] mit dem Titel „Die Zukunft wartet schon heute“ mit Darstellungen zur Anorganik in der Kernherstellung und der Umsetzung in der Anlagentechnik ab.
S. Sasse u. a. [14] stellen ausführlich die Entwicklung eines anorganischen Bindersystems für die GJL-Bremsscheibenfertigung vor. Im Zuge der stetig steigenden Anforderungen bezüglich Emissionen und Umweltbelastungen sowie Energie- und Materialkosten stehen die Gießereien mehr denn je in einem internationalen und nationalen Wettbewerb, in dem sie sich behaupten müssen. Hier sind Innovationen zur wirtschaftlicheren Gussproduktion von großer Bedeutung. Dies betrifft in besonderem Maße auch die Wahl des Kernherstellungsverfahrens und dessen Optimierung. Anorganische Bindemittel haben sich zur Kernherstellung bereits im Leichtmetallguss mit sehr großem Erfolg etabliert und stellen dort eine wirtschaftliche Alternative zu den gängigen Cold-Box-Bindemitteln dar. Durch den Einsatz von anorganischem Binder und der damit verbundenen Reduzierung von Emissionen und Kondensaten können Kostensenkungen u. a. im Bereich der Luftaufbereitung und Instandhaltung erzielt werden. Im Rahmen einer Bachelorarbeit wurde das anorganische Kernbindersystem Inotec bei der SHW Automotive GmbH, Tuttlingen, zur Bremsscheibenfertigung aus Eisenguss eingesetzt und der Prozess im Vergleich zur Serienanwendung bewertet.
Das Wiederverwenden von anorganisch gebundenen Kernsanden beschreiben H. Schwickal u. a. [15] in ihrem Beitrag Regenerierung von anorganisch gebundenen Gießereikernsanden. In einer ersten Studie wurde die Machbarkeit der Regenerierung anorganischer Kernsande bestätigt und die ausgewählten Verfahren in einer Pilotanlage umgesetzt. Neben einer Optimierung der Behandlungsparameter erfolgten erste Kreislaufversuche, um den späteren Serienbetrieb zu simulieren und abzusichern. Alle im Pilotbetrieb erzeugten Kreislaufregenerate konnten erfolgreich in der Serienfertigung von Zylinderköpfen und Kurbelgehäusen eingesetzt werden. Für einen Ausbau der gewonnenen Erkenntnisse läuft in Zusammenarbeit mit der Becker GmbH CAD-CAM-Cast, Steffenberg-Quotshausen, eine qualitative und wirtschaftliche Bewertung des entwickelten Regenerierungsverfahrens für anorganische Bindersysteme durch den Einsatz der anorganischen Regenerate in der Kleinserienfertigung.
J. Müller und M. Arndt-Rosenau [16] erläutern den ökologischen Nutzen und ökonomische Vorteile: Ein anorganisches Bindersystem verbessert die Produktivität. Für den Leicht- und Buntmetallguss bietet die Inotec-Technologie eine Alternative zu den herkömmlichen organischen Kernherstellungsverfahren. Die anorganischen und damit emissionsfreien Kernbinder vermeiden bis zu 98 % der Schadstoffe bei verbesserter Produktivität (Bild 5). Zusätzlich ergeben sich neue Entwicklungsmöglichkeiten durch eine verbesserte Gefügequalität.
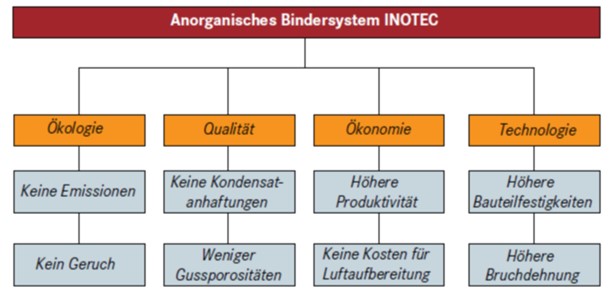
T. Kautz, E. Weissenbeck und W. Blümlhuber [17] geben einen Anwenderbericht zur anorganischen Sandkernfertigung. Bei der BMW Group am Standort Landshut werden weltweit erstmals in einer Leichtmetallgießerei alle Volumenbauteile im Kokillengießverfahren mit anorganisch gebundenen Sandkernen hergestellt. Statt herkömmlicher, organischer Bindemittel wird das besonders umweltschonende, anorganische Bindersystem Inotec eingesetzt. Dieses Bindemittel setzt nahezu keine umweltbelastenden Emissionen frei und ermöglicht dennoch die Herstellung von komplexen Sandkernen, wie sie für die Herstellung von hoch effizienten Otto- und Dieselmotoren für die Pkw-Produktion notwendig sind. Neben dem Umweltaspekt eröffnet dieses neue Fertigungsverfahren weitere Potentiale hinsichtlich Qualität, Kosten und Bauteileigenschaften.
Eine Veröffentlichung zu emissionsgebundenen organischen Kernbindemitteln kam von A. Schrey [18] über hoch reaktive Polyurethan-Cold-Box-Binder in Labor und Praxis. Es zeigt sich, dass sich ältere, konventionelle Cold-Box-Binder und die Binder der neuen Politec-Reihe zunächst hinsichtlich der Sofortfestigkeit, die häufig als einzige Bewertungsgröße von Bindern herangezogen wird, nicht unterscheiden. In Bezug auf die Härtegeschwindigkeit ergeben sich bereits deutliche Unterschiede. Wenn die zur Aushärtung einer definierten Kerngeometrie zugrunde gelegte Begasungsdauer für einen Politec-Binder der jüngsten Generation zu 100 % gesetzt wird, werden unter den gleichen Versuchsbedingungen in der betrachteten Begasungszeit lediglich 60 % der Kernformstoffmenge mit einem klassischen Cold-Box-Binder gehärtet (Bild 6).
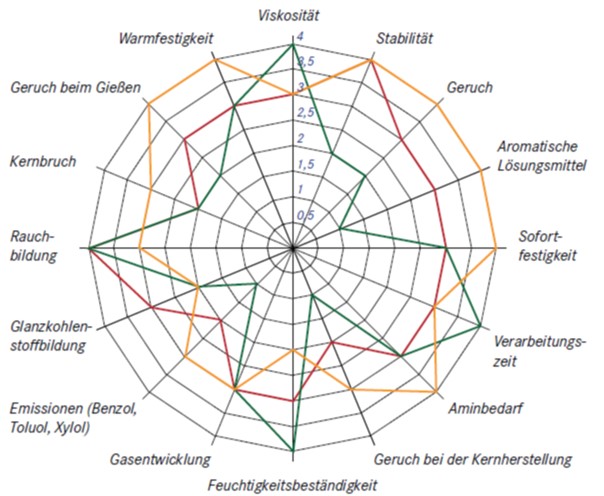
Ein weiterer Beitrag zu emissionsgeminderten organischen Bindemitteln kam von P. Michael und D. Strunk [19] zum Cold-Box-Verfahren als einer bewährten Technologie.
C. Grefhorst u. a. [20] sehen Herausforderungen bei der Umstellung auf eine anorganische Form- und Kernherstellung. Dieser Fachbetrag bietet eine Übersicht derjenigen Einsatzstoffe, die verwendet werden, um hochwertigen Guss herzustellen und gleichzeitig dazu beitragen, positiv auf Umweltbedingungen zu reagieren. Der Ersatz von Glanzkohlenstoffbildnern wie Kohle in bentonitgebundenen Formen durch den Einsatz anorganischer Additive ist vollständig oder teilweise möglich und hat verschiedene Vorteile:
- keine Rauchentwicklung beim Gießen und Kühlen;
- deutlich weniger CO am Arbeitsplatz (ca. 30 %);
- Reduzierung der Benzol-(BTEX)-Emissionen (ca. 40 %);
- geringere Geruchsentwicklung an der Auspackstelle (indikative Messung);
- Gussoberfläche unverändert;
- Grünsandeigenschaften nicht signifikant anders;
- Ausschuss und Nacharbeit in der Summe gleich;
- deutlich weniger Penetrationsfehler, mehr Formausdehnungsfehler.
Eine Umstellung von Glanzkohlenstoffbildnern (Kohle) auf anorganische Additive sollte langsam erfolgen, damit der Prozess überwacht, Änderungen quantifiziert und – wenn nötig – der Prozess oder die Additive an die neue Situation angepasst werden können.
Es ist möglich in Grünsandsystemen, also bentonitgebundenen Formstoffen, den Gehalt an organischen Zusätzen (Glanzkohlenstoffbildner) um 50 bis 100 % zu senken und diese durch anorganische Additive zu ersetzen. Kerne kann man ebenfalls mit anorganischen Bindern produzieren, diese basieren meist auf Wasserglas inklusive
verschiedener Additive. Der Einsatz dieser Binder ist beim Aluminiumgießen und bei kleinen Kernen in Großserien am aussichtsreichsten. Zukünftige Herausforderungen liegen bei der Entwicklung anorganischer Kerne für den Eisen- und Stahlguss und in der Untersuchung der Wechselwirkung mit dem bentonitgebundenen Formstoff. Dies verlangt detaillierte Kenntnisse über das gesamte Verfahren sowie die Eigenschaften und Wechselwirkungen von Kernbindern und Bentonit, einschließlich der verwendeten Additive.
Anorganische Binder im Rapid Prototyping stellt I. Ederer [21] in seinem Beitrag zum umweltfreundlichen 3-D-Druck mit anorganischem Bindersystem vor. Der voxeljet technology GmbH, Friedberg, und der Hüttenes-Albertus Chemische Werke GmbH, Düsseldorf, ist es gelungen, anorganisch gebundene Formen und Kerne werkzeuglos im 3-D-Druckverfahren herzustellen. Mit dieser Neuentwicklung folgt das 3-D-Drucken dem zunehmenden Trend zu umweltfreundlichen Formstoffen in der Gießerei. Die Automobilindustrie hat sich die Faktoren Nachhaltigkeit und Ökologie im Produktionsprozess auf die Fahnen geschrieben. Bereits seit einiger Zeit werden in der Motorenfertigung anorganische Binder für die Herstellung von Sandkernen eingesetzt.
Im Gegensatz zu organischen Bindern lässt sich durch anorganisch gebundene Kerne eine Reihe von Vorteilen erschließen. Das fängt bei der Umweltverträglichkeit an und reicht bis hin zur Qualitätsverbesserung der fertigen Gussteile. Gerade bei der innovativen Technologie des Additive Manufacturing (AM), bei der Sandformen auf 3-D-Drucksystemen werkzeuglos nach CAD-Daten hergestellt werden, waren anorganische Binder bis heute nicht verfügbar. Das von den beiden Unternehmen entwickelte Formstoffsystem erlaubt den Einsatz auf den Voxeljet 3-D-Druckern. Der Schichtbauprozess läuft prinzipiell genauso ab wie beim Einsatz organischer Binder. Beim neuen System wird anorganischer Fertigsand, ein mit anorganischem Binder versetzter Formstoff, in mikrometerfeinen Schichten auf eine Baufläche aufgetragen und anschließend selektiv mit einer Flüssigkeit bedruckt. Die Drucklösung aktiviert den Binder im Sand, der die umliegenden Formstoffpartikel bindet. Dieser Prozess wird so lange Schicht für Schicht fortgesetzt, bis die gewünschte Form hergestellt ist. Nach dem Druck werden die Formen und Kerne vom umliegenden Formstoff befreit. Das nicht bedruckte Partikelmaterial lässt sich nach einer Aufbereitung wieder dem Prozess zuführen. Die gedruckten Bauteile kommen nach dem Schichtbauprozess für wenige Stunden zur Trocknung in einen Ofen und stehen dann für den Abguss zur Verfügung (Bild 7).
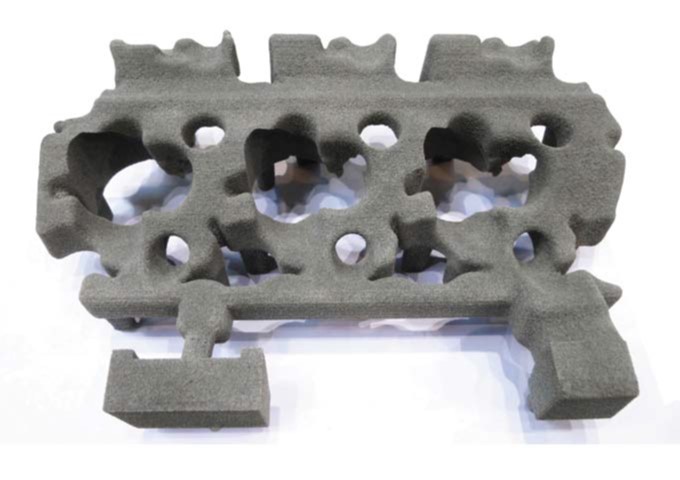
Neben der Umstellung von organischen auf anorganische Binder ist die Umstellung von Alkohol- und Wasserschlichte eine wichtige Maßnahme zur Emissionsminderung. M. Henneberg [22] berichtet über den Einsatz von Wasserschlichten für den Großund Mittelguss. In der Kette des gesamten Produktionsprozesses eines Gussteils übt die Herstellung und Behandlung der Formen einen wesentlichen Einfluss auf die Qualität eines fertigen Gussstückes aus. Neben Preis und Verarbeitbarkeit der gesamten Hilfsstoffe spielen vermehrt die Umweltverträglichkeit und die Belastung auf die Mitarbeiter beim Handling durch flüchtige organische Substanzen eine entscheidende Rolle bei der Auswahl sämtlicher Materialien. Hierbei ist insbesondere mittel- und langfristig die Substitution von Wasserschlichten für den Groß- und Mittelguss als ein wesentliches Mittel anzusehen, die Arbeits- und Produktionsbedingungen zu verbessern.
Untersuchungen haben gezeigt, dass sich neben diesen positiven Effekten sowohl qualitativ als auch vom Produktionsablauf her weitere Verbesserungen ergeben. So sind höhere Gussoberflächenqualitäten und ein geringer personeller Aufwand bei der Verarbeitung in der Praxis nachgewiesen worden. In diesem Zusammenhang spielt jedoch die Wahl eines geeigneten Trocknungsverfahrens eine wesentliche Rolle, wenn die Rahmenbedingungen einer Gießerei lange Standzeiten der geschlichteten Formen von bis zu 3 Tagen nicht zulassen. Die klimatischen Bedingungen sind hierfür mit entscheidend und insbesondere aus der Sicht der Qualitätssicherheit ist die unkontrollierte Trocknung an der Umgebung nicht akzeptabel. Es wird ein neuartiges Trocknungskonzept vorgestellt, welches im Gießereibetrieb erfolgreich validiert ist. Bei der Entwicklung war die effektive Trocknung oberstes Ziel – minimaler energetischer Einsatz bei geringen Trocknungszeiten, wobei eine einfache, robuste und automatisierte Anlagentechnik den rauen Gießereibedingungen zu entsprechen hat. Neben der technischen Beschreibung wird die Wirtschaftlichkeit des Verfahrens dargestellt (Bild 8).
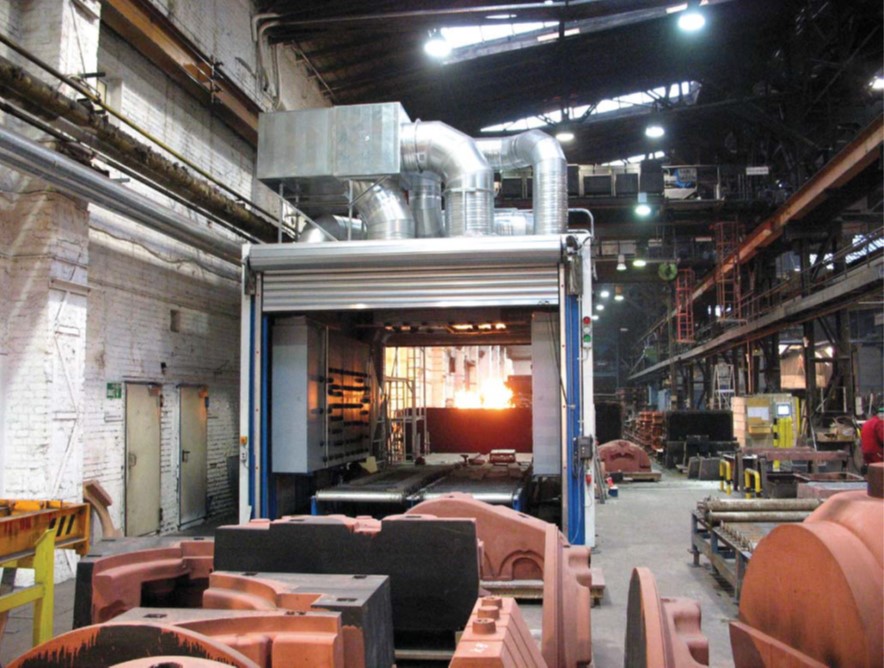
Für den Entformungsprozess von bentonitgebundenen Formen hat die Ashland- Südchemie-Kernfest GmbH, Hilden, ein lösemittelfreies Formentrennmittel entwickelt [23]. Es reduziert die ökologisch bedenklichen, flüchtigen organischen Komponenten deutlich und trägt dadurch zur Vermeidung von Emissionen in Gießereien bei. Zudem erleichtert die Anwendung des Trennmittels durch eine deutliche Reduktion der Adhäsionskräfte zwischen Modell und Formwänden den Abformprozess, was die Formwerkzeuge schont und ihre Lebensdauer erhöht. Die zusätzliche Wirkung einer korrosionshemmenden Sperrschicht schont Modelle und -lacke und schützt so bei der Lagerung. Gegenüber den prozessintegrierten Maßnahmen zur Emissionsminderung treten die sekundären in den jüngeren Veröffentlichungen deutlich zurück.
Die Scheuch GmbH [24], Aurolzmünster, Österreich, hat ein Gesamtkonzept zur Entstaubung einer Gießerei im sächsischen Elsterheide erfolgreich abgeschlossen. Das Werk gehört zur SLR-Gruppe mit Hauptsitz in St. Leon-Rot, die deutschlandweit 1000 Mitarbeiter beschäftigt und rund 85 000 t Gusseisen mit Kugelgraphit pro Jahr produziert. Bei dieser technischen Lösung kommen insgesamt fünf Impulsschlauchfilter mit einer Leistung von jeweils 250 000 m³/h zum Einsatz. Ein interessantes
technisches Detail der Entstaubungsanlage ist die Vermischung der Luftströme aus der Formanlage (warme Luft) und der Sandaufbereitung (feuchte Luft) durch die Taupunktunterschreitungen und damit die Vermeidung der Gefahr von Anbackungen. Projektpartner waren das Institut für Gießereitechnik (IfG), die Hochschule für Technik und Wirtschaft in Dresden und die TU Bergakademie Freiberg.
Das Reinigen von Gießgasen mit einem Niedertemperaturkatalysator ist Gegenstand des AiF-Forschungsvorhabens Nr. 15728 [25] gewesen. Das erreichte Ziel dieses Projektes war die Entwicklung einer technischen Maßnahme, mit der kritische gasförmige Schadstoffe aus Gießgasen entfernt werden können. Zudem sollte die Maßnahme unter vertretbaren ökologischen und ökonomischen Bedingungen einsetzbar sein. Daher wurde ein Katalysatorsystem mit integriertem Thermomanagement entwickelt, das die Abwärme des Gießprozesses nutzt. Normalerweise werden hierfür Wärmetauscher eingesetzt, die aber einen hohen gerätetechnischen Aufwand darstellen. Es wurde daher nach alternativen Maßnahmen gesucht (Bild 9).
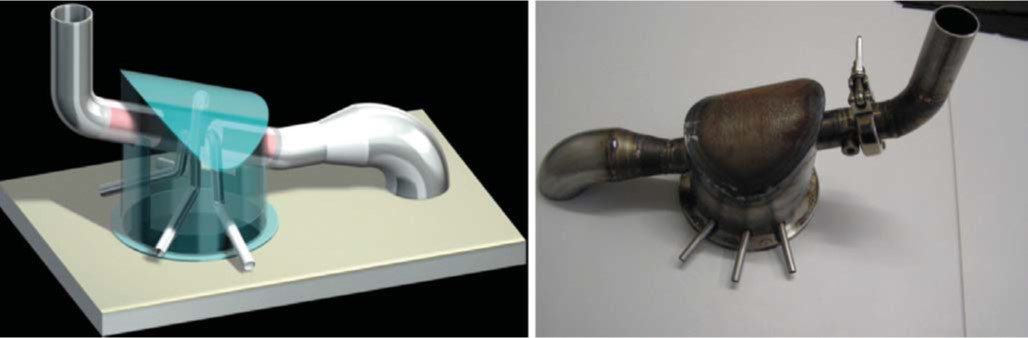
Sporadisch wie bei der Emissionsminderung mit lufttechnischen Anlagen sind aus den letzten Jahren Veröffentlichungen zur Abfallvermeidung oder -entsorgung zu finden.
Zum Recycling von Aluminiumspänen äußert sich P. Klingauf [26]. Nach ihm ermöglicht das Brikettieren von Aluminiumspänen eine hohe Direktausbeute. Aluminiumspäne sind wertvoller Rohstoff. Die Rückgewinnung macht also durchaus Sinn. Eine von der Ruf GmbH & Co. KG, Zaisertshofen, einem Hersteller von Brikettieranlagen, in Auftrag gegebene Studie des Ingenieurbüros Dr. Urbach (IMR), Stade, untersuchte das Brikettieren von Aluminiumspänen. Die Versuchsreihen zeigen, dass durch dieses Verfahren eine Gesamtausbeute von rund 99 % erreichbar ist (Direkt- und Indirektausbeute) und damit noch eine Reihe weiterer Vorteile einhergehen. Grundsätzlich führen zwei Wege der Späneaufbereitung zum Ziel: das Brikettieren und das Zentrifugieren mit anschließendem Trocknen der Späne und Schmelzen in Ofenaggregaten mit Einrühranlagen (Submerged Melting).
Laut Ruf ist das Brikettieren schnell und kostengünstig, das Zentrifugieren dagegen kosten- und verfahrensintensiv. Die Hersteller von Anlagen zum Zentrifugieren von Spänen geben eine erreichbare Schmelzausbeute von etwa 98 % an. Laut einer vom Ingenieurbüro Dr. Urbach durchgeführten Studie ist mit dem Brikettieren von Aluminiumspänen eine Gesamtausbeute von 98,6 % möglich. Dabei bietet dieses Verfahren noch weitere Vorteile, die sich immer mehr Betriebe zu Nutze machen. So lässt sich beispielsweise das aus den Spänen gepresste Kühlschmiermittel nach der Aufbereitung mit Filteranlagen direkt in den Fertigungsprozess zurückführen. Außerdem benötigen Briketts erheblich weniger Lagerplatz und sind durch das geringere Volumen für den Verkauf preiswerter zu transportieren. Und schließlich sorgt die enorme Komprimierung der Späne dafür, dass die oxidierende Oberfläche auf ein Minimum reduziert wird (Bild 10).
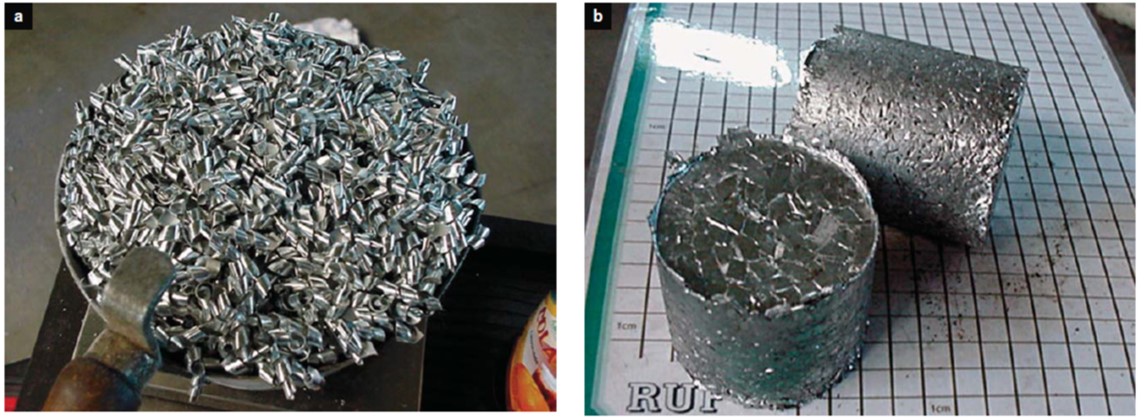
B. Cochran [27] appelliert in seiner Veröffentlichung; „Ignorieren Sie nicht die Vorschriften für Aluminium-Dross“. Obwohl Aluminiumdross ein in Metallgießereien allgemein anfallendes Material ist, ist dies ein potentiell gefährliches Material und die Handhabungs- und Transportvorschriften sollten beachtet werden. Aus Aluminiumdross können in Reaktionen mit Wasser gefährliche Gase wie Methan, Ammoniakgas und Wasserstoff gebildet werden.
Eine gute Übersicht über die Vermeidung und Entsorgung gibt M. Holmgren [28] in seinem Beitrag zur externen Wiederverwendung von Gießereiabfall – Erfahrung, Grenzen und Vorschriften in der EU. Es werden die Entwicklung eines neuen Grünsandes mit deutlicher Emissionsreduzierung sowie die Möglichkeiten zur Wiederverwendung von Gießereiabfall, insbesondere Altsand, außerhalb von Gießereien beschrieben.
Energietechnik und Energieeffizienz
Deutsche Gießereien stehen dauerhaft vor ökologischen Herausforderungen, weshalb im Rahmen dieses Artikels genau diese dritte Säule der Nachhaltigkeit, die Ökologie, im Vordergrund steht. Bei ökonomischen und sozialen Herausforderungen stehen mehrere Experten im Haus der Gießerei-Industrie unter [29] zur Verfügung (z. B. in den BDG-Wirtschaftsreferaten, in der VDGAkademie oder auch durch Online-Informationen zur Nachwuchswerbung für die Gießerei- Industrie. Historisch betrachtet hatte das Thema Energie(technik) in den letzten Jahresübersichten „Umweltschutz“ im Jahr 2004 [30] und im Jahr 2006 [31] keine Bedeutung. In der Jahresübersicht im Jahr 2009 [32] wurde das Thema Energie „immerhin schon an letzter Stelle“ erwähnt. Gerade aktuelle Forschungsprojekte im Institut für Gießereitechnik, wie z. B. das europäische Foundrybench [33], haben gezeigt, wie wichtig dieses Thema ist und auch in den nächsten Jahren sein wird. Haupttreiber ist neben ökonomischen Überlegungen vor allem die Gesetzgebung in Brüssel und Berlin, z. B. bei der EU-Energieeffizienz-Richtlinie oder beim Thema Belastung durch die Erneuerbare-Energien-Gesetz-Umlage, welches intensiv durch den Bundesverband der Deutschen Gießerei-Industrie (BDG) vor Ort begleitet wird [34]. Das führt dazu, dass der Klimawandel sowie die Energiewende und die damit verbundenen steigenden Energiepreise [35], die Umsetzung der Richtlinie über Industrieemissionen, Energiemanagementsysteme und Energieeffizienz gegenwärtig für Gießereien Themen auf dem Gebiet des Umweltschutzes und der Energietechnik darstellen, die im besonderen Fokus stehen (Bilder 11 und 12).
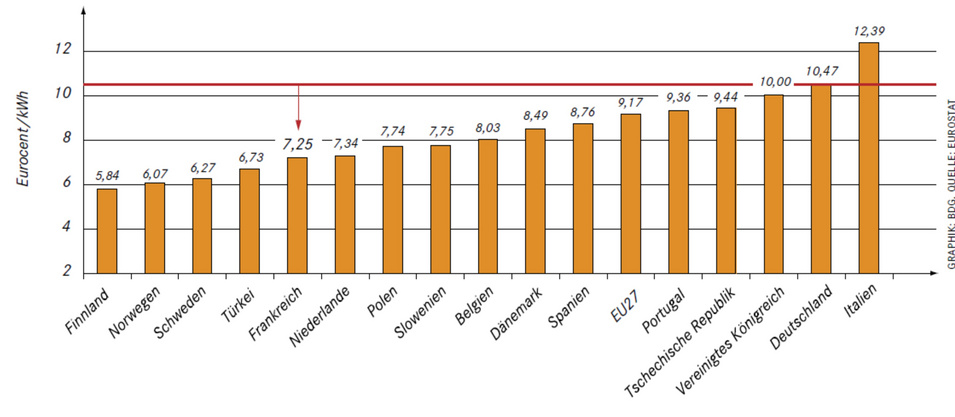
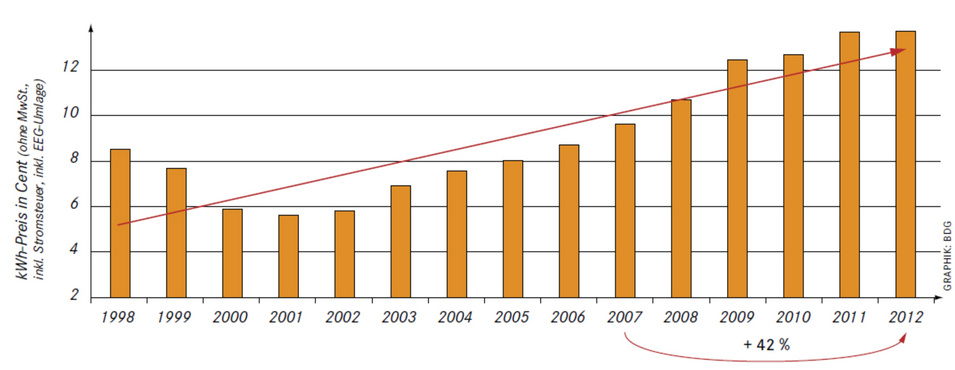
In Fachberichten wird das Thema Emissionshandel vermehrt als „Problemfeld der Gießerei-Industrie“ skizziert. Fakt ist, dass der Emissionshandel für die betroffenen Gießereien als echtes „Bürokratiemonster“ daherkommt, bei dem man zeitweise unter hohem Zeitdruck bis zu 1000 Seiten im digitalen Formular-Management-System ausfüllen muss [36]. Es sei aber dabei auch erwähnt, dass dieser Handel vierzehn (Eisen) Gießereien betrifft, die große Kupolöfen mit einer Feuerungswärmeleistung von 23 t pro Stunde aufweisen.
In Deutschland wird ein Großteil der Energie aus fossilen und nuklearen Energieträgern gewonnen, bei denen Deutschland, bis auf Braunkohle, importabhängig ist. Zum einen zeigen jedoch die im März 2011 havarierten Atomkraftwerke in Fukushima, dass diese im Betrieb kohlendioxidfreie Stromgewinnung erhebliche Risiken birgt. Zum anderen bedarf es einer nahezu vollständigen Dekarbonisierung menschlicher Aktivitäten, um die globale Erwärmung einzugrenzen. Die Europäische Union hat daher die so genannten 20-20-20-Ziele verabschiedet, die eine Verringerung der Treibhausgasemissionen um 20 %, eine Erhöhung des Anteils erneuerbarer Energien auf 20 % und eine Einsparung beim EU-Energieverbrauch von 20 % vorsehen. Auf deutscher Ebene wurden diese Ziele auf Senkung der Treibhausgasmissionen um 40 % gegenüber 1990, 35 % Anteil erneuerbare Energien bei der Stromerzeugung und Senkung des Primärenergieverbrauchs gegenüber 2008 um 20 % heruntergebrochen. Auch ein langfristiges Ziel steht heute schon fest: Die Verringerung der Treibhausgasemissionen um minus 80 bis 95 % im Jahr 2050 gegenüber dem Jahr 1990.
Somit werden Gießereien in den nächsten Jahren nicht um das Thema erneuerbare Energien im Gießereibetrieb herumkommen, um einen Beitrag zur Erreichung der 20-20-20-Ziele zu leisten. Daher untersucht das IfG zusammen mit Ecofys in einem Forschungsprojekt des Bundesumweltamts, wie erneuerbare Energien in Gießereien verstärkt integriert werden können. Es gibt bereits einige Gießereien, die Anlagen zur regenerativen Stromerzeugung installiert haben. Ein erstes Zwischenfazit des Forschungsprojekts beschreibt, dass grundsätzlich, an technischen Gesichtspunkten orientiert, eine nahezu 100- prozentige Substitution fossiler durch erneuerbare Energieträger entlang der Gießereiprozesskette möglich ist. Konventioneller Strom könnte durch Ökostrom ersetzt werden, Erdgas durch Biomethan und Dieselkraftstoff durch Biodiesel; mittel- oder langfristig kann von heizöl- oder dieselbetriebenen Aggregaten auf strom- oder erdgasbetriebene umgestellt werden. Ob erneuerbare Energien
in der Gießerei-Industrie zum Einsatz kommen, hängt in Zukunft neben der technischen Machbarkeit letztendlich auch in starkem Maße von der Wirtschaftlichkeit ab (Bild 13).
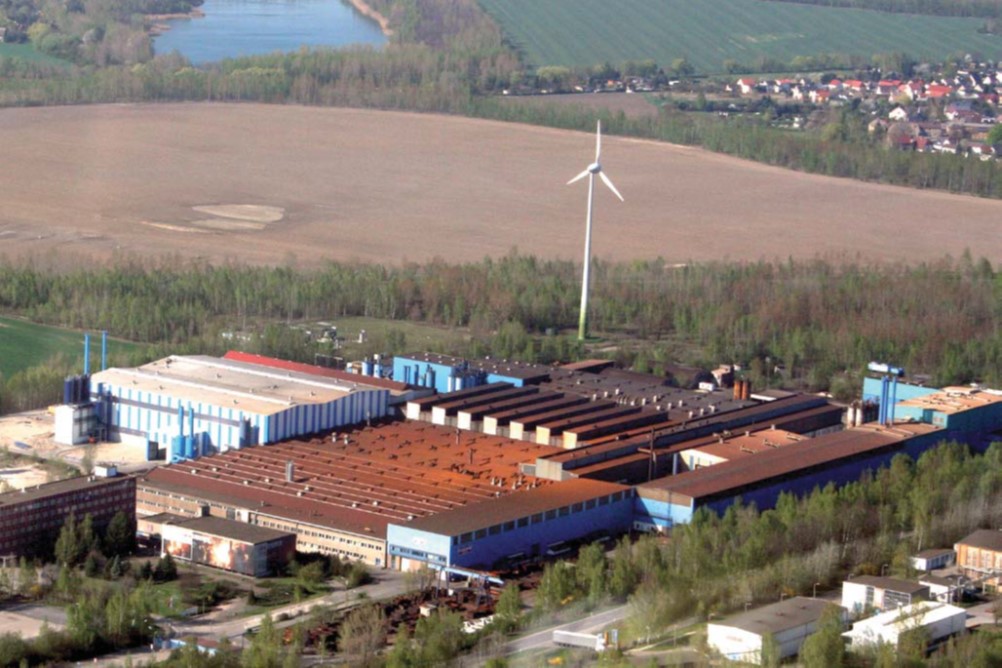
Die Gießerei-Industrie gehört zu den energieintensiven Branchen, weil das Fertigungsverfahren Gießen per Definition mit dem Schmelzen von metallischen Werkstoffen verbunden ist, wozu schon aus physikalischen Gründen ein erheblicher Energieeinsatz notwendig ist. Gleichzeitig gilt die Gießereibranche als Vorreiter beim effektiven Recycling von Werkstoffen, da über 90 % aller Gussteile durch das Wiedereinschmelzen von Schrott erzeugt werden [37]. Im Vergleich zu anderen Fertigungsverfahren, mit denen metallische Bauteile gefertigt werden, hat das Gießen deutliche Vorteile und Potentiale hinsichtlich des Materialeinsatzes und der Energieeffizienz, was auch für Betrachtungen der gesamten Wertschöpfungskette einschließlich der Endprodukte wie Bauteile für Fahrzeuge oder Maschinen gilt. Auch Gießereien müssen einen Beitrag zur Zielerreichung der europäischen Energieeffizienzziele leisten, was über den gesamten Lebenszyklus betrachtet mit Gussteilen, z. B. für Windkraftanlagen oder dünnwandigen Gussstücken für die Automobilindustrie, bereits in der Praxis vollzogen wird.
In der letzten Folge der Jahresübersicht Umweltschutz war das Thema (Energie) Lastmanagement(systeme) noch als wichtiges Thema für Gießereien erkannt worden. Gegenwärtig kommen gerade größere Gießereien nicht mehr um ein systematisches Energiemanagement(system) nach der internationalen Norm DIN EN ISO 50001 [38] herum, die deutlich mehr als ein einfaches (Energie)Lastmanagement(system) fordert [39]. Die Senkung des Spitzenlastbedarfs und die Optimierung des Lastgangs, um Stromspitzen zu vermeiden und damit den Leistungspreis beim Energieversorger zu senken, ist dabei „nur noch“ eines von fünf Themen zur Verbesserung der energiebezogenen Leistung. Das Praxisbeispiel eines Lastmanagementsystems in einer Gießerei, die ihre Spitzenlast von 8,2 MW auf 7 MW absenken konnte, wird von R. Donnerbauer beschrieben [40].
Wie bei den bekannten Qualitäts- (DIN EN ISO 9001) und Umweltmanagementsystemen (DIN EN ISO 14001), eher selten EMAS-III [41] (Abkürzung für Eco-Management and Audit Scheme, ein freiwilliges Instrument innerhalb der Europäischen Union zur Verbesserung der Umweltleistung) hat ein Energiemanagementsystem die Etablierung eines idealtypischen Plan-Do-Check-Act-Zyklus mit den damit verbundenen kontinuierlichen Verbesserungsprozessen zum Ziel. Entscheidend für den Erfolg von Energiemanagementsystemen ist die Integration aller Mitarbeiter durch Schulungen zum Thema Energieeffizienz, um den sparsameren Um gang mit Energie in allen Unternehmensbereichen zu fördern. Ferner muss im Rahmen eines Energiemanagementsystems ein Messstellenkonzept erarbeitet und der Aufbau eines Rechtskatasters vorangetrieben werden. In der Einführungsphase müssen zudem weitere Möglichkeiten zur Minderung des Energieverbrauchs und zur Verbesserung der Energieeffizienz erfasst werden. Dabei kann z. B. der Leitfaden „Energieeffizienter Gießereibetrieb Version 1.0“ [42] helfen, welcher im Jahr 2013 in einer neuen digitalen Version 2.0 in Zusammenarbeit zwischen BDG und dem IfG veröffentlich wird. Auch die online abrufbaren Informationen aus dem Projekt Foundrybench können Vergleichszahlen liefern [43].
Während der großen internationalen Gießereifachmesse GIFA 2011 wurde zum Thema Energieeffizienz eine große Sonderschau durchgeführt, auf der verschiedene Best-Pratice-Beispiele gezeigt wurden [44] (siehe Bild S. 66).
Um den Energiebedarf in Gießereien zu senken, muss ein ganzheitlicher Optimierungsansatz gewählt werden. Sich einseitig auf Querschnittstechnologien wie Beleuchtung und Druckluft zu fokussieren, verspricht nicht die erhofften Erfolge zu erzielen. Es ist dauerhaft das Ziel, schwere körperliche Arbeiten in Gießereien zu vermeiden oder zu vermindern, weshalb Prozesse in den Gießereien mechanisiert oder automatisiert worden sind. Dies führt aber simultan zu einem höheren Energiebedarf. M. Naumann beschäftigt sich daher mit Energieeffizienzsteigerungen in der Automatisierungstechnik [45]. In einem vom Bundesumweltministerium geförderten Projekt wurde in einer Großgießerei ein EDV-gestütztes Fertigungsleitsystem implementiert [46]. Dieses Systems half dabei, Prozesse transparent darzustellen, Wartezeiten und Leerläufe zu reduzieren und so Durchlaufzeiten sowie damit verbunden den Energiebedarf im Betrieb zu senken.
Die effiziente Verwendung von Energie in einer Gießerei wird entscheidend vom Putzaufwand am fertigen Gussteil bestimmt, weshalb (gewichts)optimierte Speiser helfen, diese Effizienz zu verbessern, weil dadurch der Putzaufwand sinkt [47]. Gleichzeitig lässt sich durch die Verwendung von Gießprozesssimulation und der damit erzielten Optimierung der Gießtechnik das Ausbringen messbar erhöhen und „unnötige Energieverschwendung“ am Gussteil vermeiden [48].
Im Schmelzbetrieb ist der Energiebedarf in Gießereien am größten, sodass gerade hier mit Energieeffizienzmaßnahmen angesetzt werden sollte. Heinz Kadelka stellt das
High Efficiency Furnace-Verfahren vor, bei dem zurückgeführtes Gichtgas im Heißwindkupolofen mit reinem Sauerstoff angereichert wird, wodurch signifikante Energieeinsparungen durch Kokssatzreduzierung realisiert werden können [49]. Eine weitere Möglichkeit zur Kokssatzreduzierung wird in einem Forschungsprojekt mit Einblasung von Petrolkoksstaub untersucht [50], wohingegen in einem anderen Projekt eine Reduzierung von Emissionen durch Substitution von Koks durch biogene Kohlenstoffträger erforscht wird [51].
E. Dötsch erläutert das Thema Energieeffizienz an Induktionsöfen [52]. Den Einfluss auf den Energiebedarf von Mittelfrequenz- Induktionstiegelöfen durch optimierte Chargierung diskutieren E. Dötsch, R. Ibach und M. Rische [53]. Durch gezielte Steuerung der Chargierung können Leistungseinbrüche beim Ofen weitestgehend vermieden und gleichzeitig Schmelzzeiten verkürzt werden. In Gießereien stehen gerade im Schmelzbetrieb hohe Abwärmepotentiale zur Verfügung, die häufig ungenutzt in die Umwelt abgegeben werden.
J. Würz u. a. [54] diskutieren die Frage, wie sich die Abwärme des Kupolofens sinnvoll weiterverwenden lässt. Mit Überführung der Abwärme in einen Thermalölkreislauf lässt sich diese ausgekoppelte Wärme zu anderen internen oder externen Prozessen führen [55]. Beispielsweise ermöglicht die dem Abgas entzogene Wärmeenergie eine direkte Nutzung in anderen benachbarten Unternehmen, wenn z. B. die Abwärme des Schmelzbetriebs zur Dampferzeugung bei einem Nachbarunternehmen genutzt und dadurch der Erdgasbedarf vermindert wird [56]. Alternativ wird die Abwärme in mobilen thermischen Energiespeichern zwischenspeichert, sodass diese an anderer Stelle, z. B. in Verwaltungsgebäuden, Schulen oder Schwimmbädern genutzt werden kann [44]. Innerhalb der Gießerei kann die prozessbedingte Abwärme dazu genutzt werden, z. B. die Hallenluft zu erwärmen, Warmwasser für Sanitäranlagen zur Verfügung zu stellen, Roh- und Betriebsstoffe zu trocknen, Kälte oder sogar selbst elektrische Energie zu erzeugen [57].
Die Pfannenwirtschaft bietet in Gießereien Verbesserungspotential in Bezug auf Energieeffizienz, weil häufig noch einfache Erdgas-Luft-Brenner verwendet werden, die „mit offenem Feuer“ in die Pfannen gehalten werden. Erdgas-Sauerstoff-Brenner stellen eine Weiterentwicklung dar und verringern den Brennstoffbedarf [44]. Alternativ können Kaltstartersysteme verwendet werden, wodurch das Vorheizen der Transportpfannen entfällt und geringere Energieverluste durch gute Isolierung garantiert werden [44]. Derzeit werden Gasporenbrenner in mehr als zwanzig Gießereien im Bereich der Vorwärmung von Transportpfannen eingesetzt [58]. Die Verbrennung in diesen Volumenbrenner findet in einer porösen Hochtemperaturkeramik statt, die eine flammenlose, schnelle und homogene Erwärmung der Transportpfannen garantiert [59].
Zu- und Abluftanlagen und die damit verbundene Be- und Entlüftung sind in Eisen- und Nichteisenmetall-Gießereien häufig der zweitgrößte Energieverbraucher. Sie sind notwendig, um die erforderliche Reinluftqualität an Arbeitsplätzen sicherzustellen. P. J. Namin [60] beschreibt in ihrem Beitrag, dass der Umluftbetrieb in Verbindung mit einem leistungsstarken Filter das energieeffizienteste Verfahren ist, da die Abluft dabei nicht ins Freie gegeben, sondern nach der Reinigung wieder dem Arbeitsbereich zugeführt wird, wodurch keine zusätzliche Erwärmung vorgenommen werden muss. Gleichzeitig ist es wichtig, dass Drehzahl sowie Absaugleistung der Ventilatoren auf Gießereiprozesse abgestimmt werden, um so, z. B. bei der Absaugung während und kurz nach dem Auftragen von Trennmitteln an Druckgussmaschinen, bis zu 30 % Energie einzusparen [61].
Literatur:
[1] Giesserei 97 (2010) Nr. 8, S. 20-27.
[2] Giesserei 97 (2010) Nr. 9, S. 28-45.
[3] Giesserei 97 (2010) Nr. 11, S. 24-41.
[4] Giesserei 98 (2011) Nr. 2, S. 18.
[5] Giesserei 96 (2009) Nr. 7, S. 50-53.
[6] Giesserei 96 (2009) Nr. 7, S. 56-58.
[7] Giesserei 96 (2009) Nr. 7, S. 60-65.
[8] Giesserei 96 (2009) Nr. 8, S. 66-68.
[9] Giesserei 96 (2009) Nr. 8, S. 70-73.
[10] Giesserei 96 (2009) Nr. 8, S. 74-76.
[11] Giesserei 96 (2009) Nr. 9, S. 62-66.
[12] Giesserei 96 (2009) Nr. 9, S. 68-71.
[13] Giesserei 96 (2009) Nr. 9, S. 73-75.
[14] Giesserei 98 (2011) Nr. 4, S. 36-40.
[15] Giesserei 96 (2009) Nr. 11, S. 40-44.
[16] Giesserei 97 (2010) Nr. 2, S. 50-51.
[17] Giesserei 97 (2010) Nr. 9, S. 76-79.
[18] Giesserei 97 (2010) Nr. 2, S. 20-28.
[19] Giesserei 98 (2011) Nr. 6, S. 114-118.
[20] Giesserei 98 (2011) Nr. 2, S. 74 -79.
[21] Giesserei 98 (2011) Nr. 8, S. 88.
[22] Giesserei 98 (2011) Nr. 6, S. 56-58.
[23] Giesserei 98 (2011) Nr. 1, S. 77.
[24] Giesserei 97 (2010) Nr. 9, S. 122.
[25] AiF-Forschungsvorhaben Nr. 15728, Düsseldorf 2012.
[26] Giesserei 98 (2011) Nr. 3, S. 63.
[27] Modern Casting (2012) Nr. 1, S. 41-43.
[28] Foundry Trade Journal International (2012) Nr. 3694, S. 124-126.
[29] www.powerguss.de.
[30] Jahresübersicht: Umweltschutz Folge 22, 91 (2004) Nr. 5. S. 42-50.
[31] Jahresübersicht: Umweltschutz Folge 23, 93 (2006) Nr. 8. S. 42-49.
[32] Jahresübersicht: Umweltschutz Folge 24, 96 (2009) Nr. 2 S. 40-46.
[33] Giesserei100 (2013) H. 6, S. ??-??.
[34] Giesserei 98 (2011) Nr. 4, S. 68-72 sowie 99 (2012) Nr. 5, S. 55.
[35] Giesserei 93 (2006) Nr. 6, S. 262-268.
[36] Giesserei 99 (2012) Nr. 5, S. 64- 67.
[37] Giesserei 98 (2011) Nr. 4, S. 74-79.
[38] DIN EN 16001, ersetzt durch DIN EN ISO 50001:2011-12.
[39] Giesserei 99 (2012) Nr. 5, S. 22-23.
[40] Giesserei 99 (2012) Nr. 5, S. 51-54.
[41] EMAS-III 2009/2010.
[42] Der energieeffiziente Gießereibetrieb Version 1.0 unter: www.bdguss.de/de/data/energieeffizienz_0.pdf abrufbar.
[43] Projekt Foundrybench unter: foundrybench.fi.
[44] Giesserei 98 (2011) Nr. 10, S. 73-80.
[45] Giesserei 97 (2010) Nr. 4, S. 86.
[46] Giesserei 100 (2013) Nr. 3, S. 72-75.
[47] Giesserei-Erfahrungsaustausch 57
(2013) Nr. 1+2, S. 6-10 sowie 57 (2013) Nr. 1+2, S. 12-17.
[48] Giesserei 98 (2011) Nr. 6, S. 82-98.
[49] Giesserei 99 (2012) Nr. 9, S. 52-56.
[50] Giesserei 100 (2013) Nr. 1, S. 58-63.
[51] IGF-Vorhaben 343 ZN.
[52] Giesserei 98 (2011) Nr. 6, S. 158-170.
[53] Giesserei 99 (2012) Nr. 6, S. 20-25.
[54] Giesserei 100 (2013) Nr. 3, S. 76-80.
[55] Giesserei 96 (2009) Nr. 10, S. 68-74.
[56] Giesserei 95 (2008) Nr. 6, S. 10-11 sowie 97 (2010) Nr. 3, S. 66-69.
[57] Giesserei 98 (2011) Nr. 6, S. 194-196.
[58] Giesserei 97 (2010) Nr. 1, S. 80-81.
[59] Giesserei 98 (2011) Nr. 4, S. 80-82.
[60] Giesserei 99 (2012) Nr. 11, S. 76-78.
[61] Giesserei 97 (2010) Nr. 5, S. 112.