Investition in Energieeinsparung und Umweltschonung
Von Anja Koch und Ralf Temming, Brühl
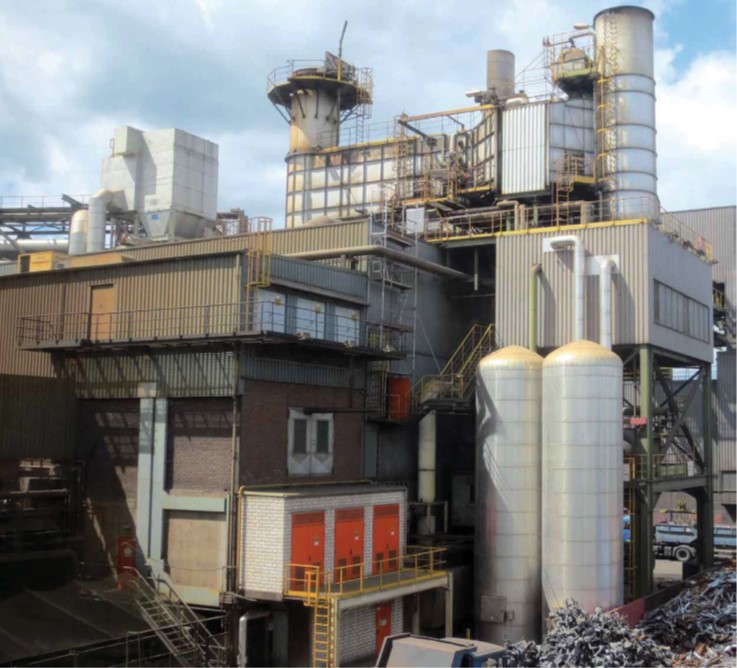
Wassergefüllter Puffer oder Latentwärmespeicher neben dem Gattierungsgelände. Die Latentwärmespeicher überbrücken die Abschaltphasen des Kupolofens energetisch. Ohne Einsatz fossiler Brennstoffe kann die Wärmemenge von 7 MW nun zur Unterstützung der Gebäudeheizung und Warmwassererzeugung mittels eines Heißwassersystems an insgesamt 15 Gebäude übertragen werden.
Erschienen in GIESSEREI 09/2015
Bereits im Jahr 2008 erhielt das Eisenwerk Brühl (EB) als eine der ersten deutschen Gießereien das TÜV-Zertifikat DIN EN 16001 Energiemanagementsysteme (heute: DIN EN ISO 50001). Das Unternehmen befasst sich somit schon seit vielen Jahren mit den Themen Energie- und Umweltschutz und investiert kontinuierlich in entsprechende Maßnahmen. Steigende Energiekosten erfordern einen sparsamen und gezielten Umgang mit Ressourcen. Allerdings sind die Einsparmöglichkeiten bei den energieintensiven Prozessen einer Gießerei im Vergleich zu anderen Branchen eher gering und rasch erschöpft, sodass über neue Wege nachgedacht werden musste.
Ausgangssituation: die vorhandene Wärmerückgewinnungsanlage
Im Eisenwerk Brühl erfolgt das Schmelzen von Eisenschrott in einem mit Koks befeuerten Heißwindkupolofen (Bild 1). Prozessbedingt fallen hierbei große Mengen Abwärme an, die seit etlichen Jahren zur Speisung einer Wärmerückgewinnungsanlage (WRG) auf dem Kamin des Rekuperators verwendet werden. Die auf diese Weise nutzbar gemachte Wärmemenge beträgt 7 MW. Diese Wärmemenge wird mittels eines Heißwassersystems an insgesamt 15 Gebäude übertragen und unterstützt die Gebäudeheizung und die Warmwassererzeugung. Dennoch verbrauchten diese Heizungen weiterhin rund 34 MWh Gas pro Jahr. Ursächlich dafür war u. a. die wenig präzise Mess- und Regeltechnik der Gebäude (Unterstationen), mit der ein übergeordnetes Wärmemanagement und eine Steuerung nach neuestem Stand der Technik nicht hinreichend möglich war. Es bot sich daher an, eine ohnehin anstehende Modernisierungsmaßnahme zur Erweiterung und Effizienzsteigerung der vorhandenen Wärmerückgewinnungsanlage zu nutzen. In Zusammenarbeit mit einem Partner aus der Energiebranche wurde ein maßgeschneidertes, nachhaltiges Energiekonzept entwickelt, um zukünftig eine deutliche Reduzierung des Energieverbrauchs zu erreichen.
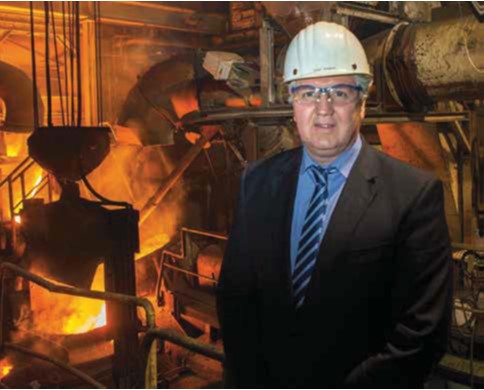
Maßnahmen zur Ertüchtigung der Wärmerückgewinnungsanlage
Pufferspeicher/Latentwärmespeicher
Das Abgas des Kupolofens steht prozessbedingt nicht kontinuierlich zur Verfügung. Dies bedeutet, dass in den Abschaltphasen des Kupolofens während der Produktion keine Abwärme für die Wärmerückgewinnungsanlage zur Verfügung stand und die angeschlossenen Gebäude automatisch mit fossilen Brennstoffen beheizt wurden. Im Zuge der Modernisierung wurden zwei wassergefüllte Pufferspeicher à 75 m³ eingebunden, welche die Abschaltphasen des Kupolofens energetisch überbrücken (Bild 2).
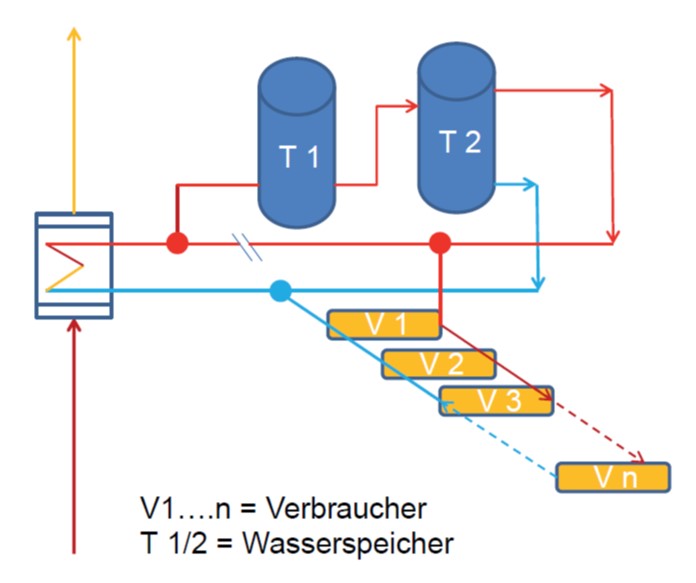
Mess-, Steuer- und Regeltechnik (MSR)
Die veralteten Steuerungen aller Gebäude wurden durch moderne MSR-Technik ersetzt. Durch die Regelung der Vorlauftemperatur in Abhängigkeit von der Außentemperatur, einer verbesserten Abstimmung zwischen WRG-Wärmetauscher und Heizkesseln sowie einer mengenvariablen Durchflussregelung wird eine deutlich bedarfsgerechtere Versorgung der Gebäude erreicht. Dies führt zu:
- einem sinkenden Wärmeverbrauch in den Gebäuden und somit zu geringerem Gaseinsatz,
- einer sinkenden Rücklauftemperatur im Primärnetz, einer geringeren Pumpenleistung und einer höheren auskoppelbaren Wärmemenge aus dem Abgas sowie
- einer Verstetigung der Hallentemperatur und
- einer verbesserten Auswertbarkeit der Energieverbräuche.
Hydraulische Maßnahmen in den Gebäuden
Durch Umbauten in den Gebäuden und die Absenkung der Rücklauftemperatur im Primär- und Sekundärnetz der Gebäudeteile wurde eine höhere Nutzung der WRG-Wärme erreicht.
Anschluss von Lüftungsanlagen an die Wärmerückgewinnung
Vorhandene Zuluftanlagen auf den Dächern der Produktionshallen wurden entsprechend ertüchtigt und an die Wärmerückgewinnungsanlage angeschlossen (Bild 3).
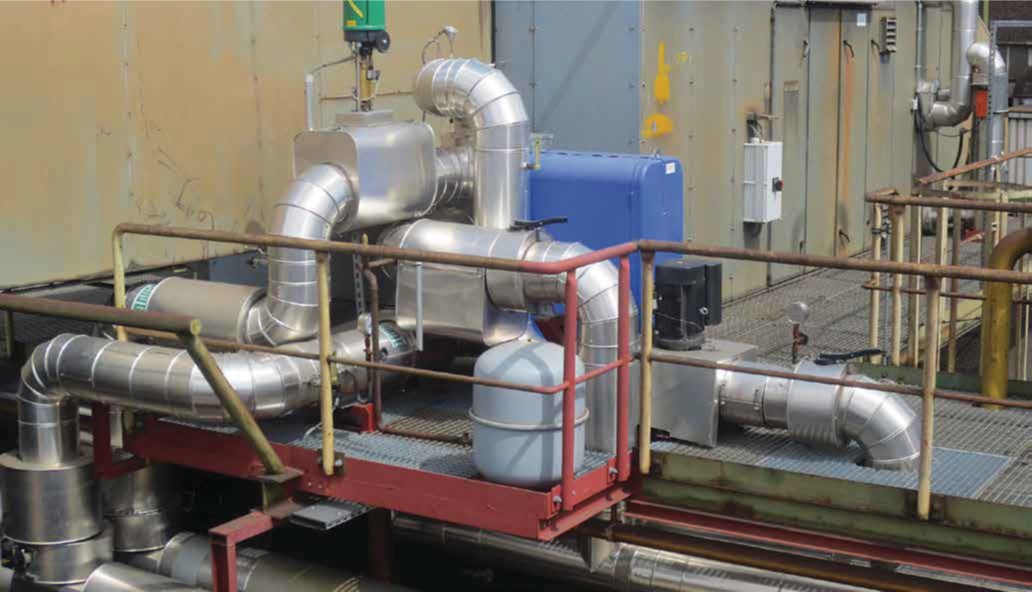
Nach erfolgreicher Umsetzung aller genannten Maßnahmen wurden beachtliche Energieeinsparungen in den an die WRG angeschlossenen Gebäuden erreicht:
- Reduzierung des Erdgasverbrauchs: Die Einsparung entspricht dem Gasverbrauch von ca. 850 Einfamilienhäusern.
- Reduzierung des Stromverbrauchs: Die Einsparung entspricht dem Stromverbrauch von 80 –100 Einfamilienhäusern.
- Reduzierung des CO²-Ausstoßes: Die Reduzierung entspricht den Emissionen von rund 260 Einfamilienhäusern.
Dies ergibt eine beeindruckende Energiebilanz und lässt ein enormes Investitionsvolumen mit entsprechend hohem Kapitalbedarf vermuten. Aber das Eisenwerk Brühl hat – gemeinsam mit einem Partner – einen Finanzierungsweg gefunden, um diese Maßnahmen liquiditätsschonend umsetzen zu können.
Finanzierung mit garantierter Wirtschaftlichkeit
Die Einsparungen werden vom Hersteller garantiert und deren Wert per Vertrag abgesichert. Zur Ermittlung des Einsparpotenzials wird der monatliche Gasverbrauch eines Referenzjahres erfasst und in Relation zu den Wetterdaten (Gradtagszahlen) des gleichen Jahres gesetzt. So wird der maßgebliche, wetterabhängige Anteil des Energieverbrauchs errechnet und mit dem Referenzverbrauch verglichen. Der Energieverbrauch ist prinzipiell abhängig von der Witterung, dies bedeutet für das System der Wärmerückgewinnung, je kälter es draußen ist, desto größer ist die Energieersparnis.
Dass dieses Prinzip funktioniert, hat sich im Eisenwerk Brühl bereits nach wenigen Monaten erwiesen: obwohl der Winter 2014/2015 insgesamt vergleichsweise milde Temperaturen hervorgebracht hat, wurde die vorgesehene Energieeinsparung und somit auch der erwartete Finanzausgleich mehr als erreicht. Die Modernisierung der Wärmerückgewinnung wurde erfolgreich umgesetzt und bietet in der jetzigen Konzeption zahlreiche Möglichkeiten, zusätzliche Anlagen in das System zu integrieren und hierdurch weitere Synergien für das Unternehmen und die Umwelt zu realisieren.
„Als Zulieferer und Entwicklungspartner für moderne, gewichtsoptimierte Zylinderkurbelgehäuse in Dünnwandtechnologie sind für uns die Themen Verbrauchsminderung und CO2-Reduzierung keine Fremdworte“, so Ralph Wegener, Geschäftsführer der Eisenwerk Brühl GmbH. „Das Eisenwerk Brühl ist sich seiner Verantwortung zum sorgsamen Umgang mit begrenzten Rohstoffen und nachhaltigem Klimaschutz bewusst und trägt mit den umgesetzten Maßnahmen zur Steigerung der Energieeffizienz und zur Reduzierung der Umweltbelastungen durch Energieeinsparungen bei. Wir stehen für Nachhaltigkeit - mit unseren Produkten aus innovativen, recycelbaren Werkstoffen und in unserer energieoptimierten Produktionsstätte.“
Mit einer Tradition von über 85 Jahren ist die Eisenwerk Brühl GmbH auf die Entwicklung und Großserienfertigung von Zylinderkurbelgehäusen (ZKG) aus Eisenguss für den Pkw-Markt spezialisiert. Die Produkte werden weltweit in alle Märkte exportiert. Mit ca. 1600 Mitarbeitern werden bis zu 5 Mio. ZKG pro Jahr in Brühl hergestellt. Mit einem hohen Automatisierungsgrad und einem technologisch ausgereiften Fertigungsprozess für Leichtbau- und Dünnwandkonzepte zählt EB zu den wichtigsten Lieferanten von Eisenguss-ZKG für die Automobilindustrie.
Anja Koch und Ralf Temming, Eisenwerk Brühl GmbH, Brühl