Von der Idee zum Gokart-Motor
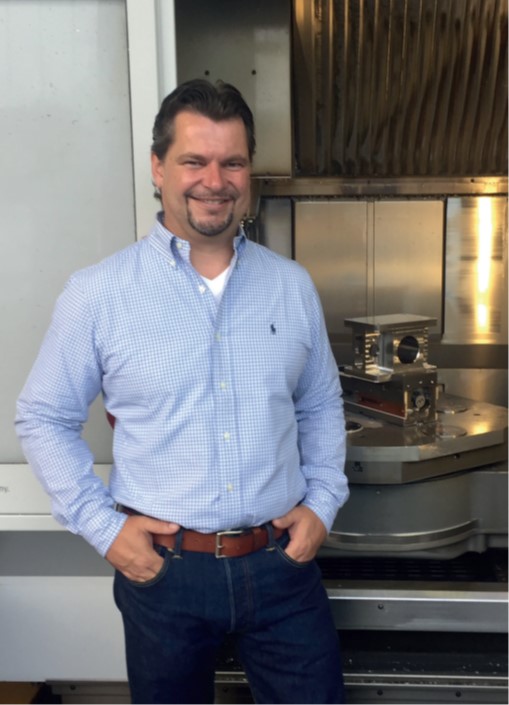
Entwickler und Produzent von Gokart-Motoren
Karlheinz Hahn hat sich seit seiner Jugend dem Kartsport verschrieben. Schon früh begann er eigene Motoren zu entwickeln.
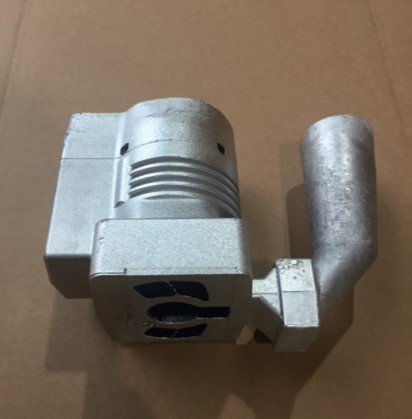
Dass sein Herz für den Kartsport schlägt, wird schnell deutlich, wenn man mit Karlheinz Hahn spricht. 1969 in Straubing geboren, entdeckte er im Alter von zehn Jahren den Gokart-Sport für sich. „Eigentlich stamme ich aus einer Fußballerfamilie. Da ich aber zwei linke Beine hatte, musste ich mir einen anderen Sport suchen“, verrät Hahn lachend.
„Ein Freund von mir ist damals Gokart gefahren und hat mich mitgenommen. Von Anfang an hat mich die Kombination aus Mensch und Technik fasziniert“. Seine Leidenschaft ist ihm bis heute erhalten geblieben und er hat sie zu seinem Beruf gemacht. Nach dem Abitur ging es 1990 direkt ins Maschinenbaustudium, und in dieser Zeit stellte er auch schon die ersten Teile für den Kartsport her. 1997, nach Beendigung seines Studiums, wagte der damals 28-Jährige den direkten Sprung in die Selbstständigkeit. Seitdem konzipiert, produziert und vertreibt er Gokart-Motoren sowie Teile für den Rennsport.
Ohne Spezialwissen geht es nicht
In seinem Beruf hat er viel Spezialwissen gesammelt, denn die Rennmotoren sind anspruchsvoll in der Produktion sowie auch in der späteren Wartung. „Zum einen braucht man das normale Ingenieurwissen,
um einen Motor zu konzipieren, hinzu kommt aber benötigtes Spezialwissen, da ein Zweitakt-Gokart-Motor sehr außergewöhnlich ist. Er hat eine extrem hohe Leistungsdichte und darf im Kartsport auch kein Getriebe haben. Aus diesem Grund muss der Motor ein breites Drehzahlband aufweisen.“
Und das kann sich sehen lassen. Mit 6.000 bis 16.000 U/min wird die Leistung des 125-ccm-Motors auf die Piste gebracht. 40 PS und Geschwindigkeiten über 130 km/h verlangen von den Fahrern viel Kondition und Können, um sich einen Platz auf dem Siegertreppchen zu erfahren.
Bis ein renntauglicher Serienmotor entsteht, ist es aber ein langer Weg. „Man braucht etwa ein Jahr, um einen Gokart-Motor serienreif zu entwickeln“, erklärt der Motorprofi. Los geht es mit der ersten Idee, die in CAD (computer-aided design) am Rechner erstellt wird. Die Teile werden anschließend anhand der technischen Zeichnungen gefertigt und zusammengesetzt. Dann geht es auf den hauseigenen Prüfstand, wie Hahn erklärt. Hier wird der neue Motor auf Herz und Nieren getestet und notfalls weiter optimiert. „Wenn auf dem Prüfstand alles in Ordnung ist, geht es auf die Rennstrecke. Gemeinsam mit den Werkteams wird der Motor im Realeinsatz dann bis zur Vollendung perfektioniert.“
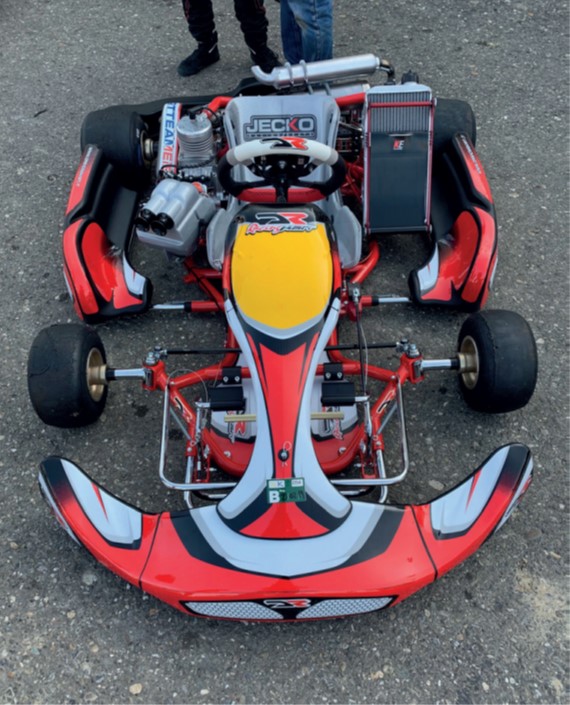
Damit der Gokart-Sport ein Breitensport bleibt, gibt es ein strenges Reglement, dass alle technischen Aspekte festlegt. „Bei einer lockereren Regelung wäre der Sport für viele Leute nicht mehr finanzierbar, da die Entwicklungskosten explodieren würden“, fasst der Motorprofi zusammen. Hierzu gehören auch die möglichen Werkstoffe und Fertigungsverfahren. „Vorgeschrieben ist z.B., dass keine exotischen Titan- oder Verbundwerkstoffe verwendet werden dürfen.“
Gegossen wird praktisch alles
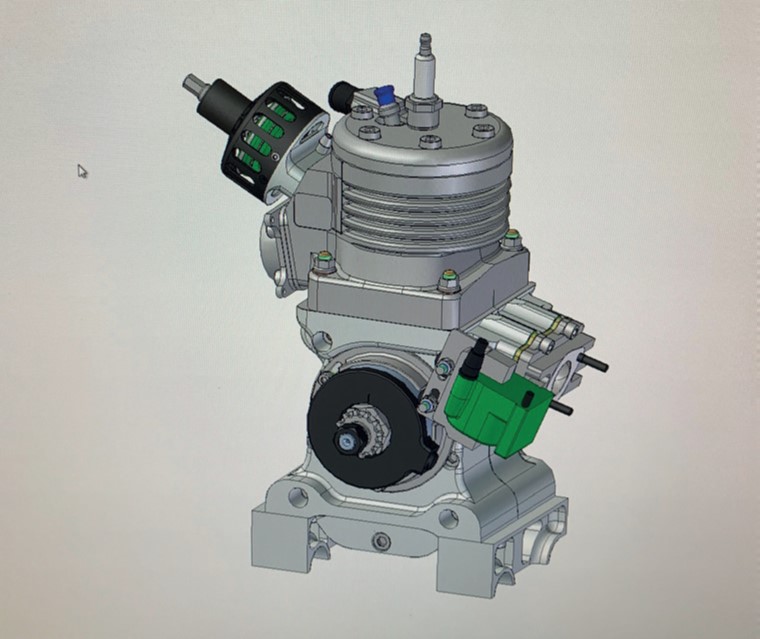
Der klassische Guss spielt beim Gokart-Motor die entscheidende Rolle, wie Hahn erklärt. „Gegossen werden praktisch alle Teile. Nur für die Kurbelgehäuseteile werden spezielle Platten gegossen, aus denen später die Bauteile herausgearbeitet werden. Gegossen werden beispielsweise die Zylinder. In einer Stahlkokille (Dauerform) wird ein Sandkern eingelegt. Dieser sorgt beim Abguss für den Wassermantel sowie die Luftführung des Motors.“ Dabei nutzen die Profis modernste Verfahren wie den 3D-Druck, um die Sandkerne präzise herstellen zu können. Hier kommt es auf extreme Genauigkeit und Reproduzierbarkeit in der Serie an.
Das spätere Produkt ist ein Hochleistungsmotor im Kleinformat. Er wiegt 9,2 kg, hat bis zu 40 PS und kostet etwa 3.500 Euro. „Der Motor ist eigentlich sehr preiswert“, erklärt Hahn. „Die hohen Folgekosten entstehen eher dadurch, dass die Motoren sehr wartungsintensiv sind. In der höchsten Leistungsklasse haben wir Kolbenwechselintervalle von zwei Stunden. Alle zehn Stunden müssen dann auch alle Lager am Motor gewechselt werden.“
In den professionellen Kartsport-Teams gibt es daher Experten, die sich um die Wartung der Motoren kümmern. „Natürlich werden im Sport noch weitere Optimierungen am Motor vorgenommen“, so Hahn. „Im Großen und Ganzen, kann man aber sagen, dass die Leistung der Serienmotoren schon sehr hoch ist. Tuner holen in der Regel keine 10 Prozent Mehrleistung aus den Motoren heraus.“
Interview mit Karlheinz Hahn
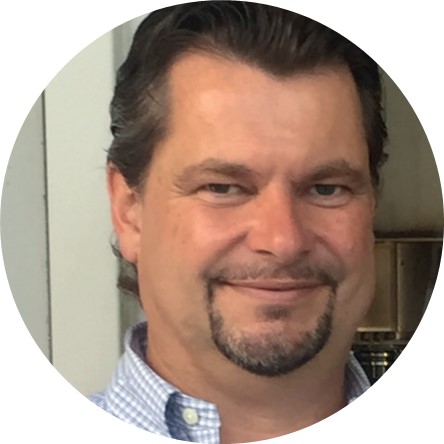
Wie lange dauert die Herstellung eines Motors?
Mit unseren 15 Mitarbeitern schaffen wir etwa zehn Motoren pro Tag. In der Nacht werden dabei vollautomatisch die Teile gefräst, die wir am nächsten Tag direkt verbauen. So ist eine optimale Auslastung gewährleistet.
Welche Werkstoffe kommen beim Gokart-Motor zum Einsatz?
Im Reglement ist strikt verboten exotische Werkstoffe wie Titan- oder Verbundwerkstoffe zu nutzen. Bei Stahl müssen sämtliche Werkstoffe magnetisch sein. Der Zylinder ist mit einer Stahlbüchse auszustatten. Bei den Aluminiumlegierungen gibt es aber kaum Vorgaben.
Was ist sonst noch alles reglementiert?
Kurbelgehäuse und Zylinder müssen beispielsweise aus Aluminiumguss hergestellt sein, ebenso sind der Vergaserquerschnitt, Hubraum, Verdichtungsverhältnis und die Zündanlage genau festgelegt.
Wie entwickelt man unter diesen Voraussetzungen einen Serienmotor weiter?
Es ergeben sich vom Markt her öfter Neuerungen, z.B. dass es neue Kolben gibt, neue Kolbenringgrößen, Lösungen zur Reibungsminimierung sowie bessere Beschichtungsverfahren im Bereich der Kolben. Wir gehen da mit den Trends aus der Motorenindustrie und versuchen das in die Gokart-Motoren einfließen zu lassen. Dadurch, dass wir auch Motoren für BMW fertigen, bekommen wir die Trends immer mit und können schnell reagieren.
Welche Teile werden im Betrieb produziert?
Wir fertigen bei uns im Haus alle Teile für den Motor. Zukaufteile sind lediglich Schrauben, Lager, Dichtringe und die Zündanlage. Kurbelwellen, Kolben, Zylinder, Zylinderköpfe, Kurbelgehäuse, Pleuelstangen und Vergaser werden bei uns im Hause individuell gefertigt. Wir haben eine extrem hohe Fertigungsdichte von 95 %.
Wie viele Personen sind bei der Entwicklung der Motoren involviert?
Im Entwicklungsprozess werden natürlich Teams und Fahrer mit einbezogen. Jeder Motorhersteller hat seine zwei oder drei Werksteams, die er ausstattet und mit denen er die ganzen Versuche macht. Die Grundentwicklung findet auf dem Prüfstand statt, die Verfeinerung muss aber dann auf der Rennstrecke in Teamarbeit erfolgen. Hinzu kommen natürlich unsere Mitarbeiter im Betrieb.
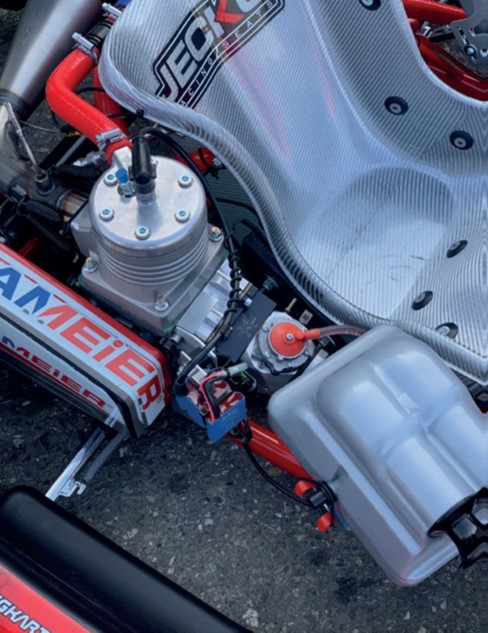
Kann man mit einem Serienmotor ein Rennen gewinnen?
Prinzipiell sind die Motoren erst einmal renntauglich. Man kauft sich ein Gokart und einen Motor und ist damit technisch in der Lage an nationalen Rennen teilzunehmen und auch gewinnen zu können. Das ändert sich erst auf der internationalen Kartsportebene.