Brennstoffbeheizte Schmelz- und Warmhalteöfen sowie Flüssigmetallanlieferung
Bezug zum BREF Gießerei, Ausgabe Mai 2005
Schmelzen von Nichteisen-Metalle wird im BVT-Merkblatt für die NE-Metall-Industrie abgedeckt.
Beschreibung
Unter den brennstoffbeheizten Schmelzöfen werden die Schachtschmelzöfen zum Schmelzen großer Metallmengen und zum Warmhalten der Schmelze eingesetzt. Bedingt durch die Vorwärmung des Schmelzguts im Schacht und durch den Einsatz moderner Regenerationsbrenner besitzen heute Schachtschmelzöfen relativ gute energetische Kennwerte.
Der spezielle Schmelzenergieaufwand beträgt ungefähr 700 bis 800 kWhth/tAL pro Tonne. Eine Füllstands- und Brennerregelung ist eine energetische Optimierung erforderlich. Für kleinere Schmelzleistungen und Warmhaltekapazitäten sind Tiegelöfen zu empfehlen.
Neuwertige Tiegel, Rekuperationsbrenner, wärmegedämmte und abgedichtete Ausmauerungen und eine automatische Abdeckung ergeben für Tiegelöfen energetische Kennwerte von 800 bis 900 kWhth/tAL pro Tonne.
Technische Beschreibung
Energieeffiziente Ofenregelung für brennstoffbeheizten Schmelz- und Warmhalteöfen:
- Ofendimensionierung für die zu erwartende Schmelz- und Warmhalteleistung optimieren, um hohen Schmelzenergieaufwand bei zu geringer Auslastung zu vermeiden
- Brennerauswahl: Rekuperationsbrenner für kleine und mittlere Leistungen, Regenerationsbrenner und Drehbettregeneratoren für stark ausgelastete Schmelzöfen
- Hohe Auslastung der Schmelzöfen sicherstellen
- Warmhalte- und Vorheizzeiten vermeiden
- Keine unnötige Überhitzung des Schmelzmaterials
- Längere Wartungsintervalle mit kurzen Stillstandzeiten erarbeiten
- Reinigungszeiten kurz halten
- Einheitliche Schmelzbadtemperatur sicherstellen
- Brennerleistung an die Betriebszustände, z. B. Warmhalten und Aufschmelzen, anpassen
- Ofen (immer) abdecken
- Ofenabdichtung sicherstellen
- Wärmedämmung garantieren
- Kurze Chargiervorgänge
- Schmelzgut vorwärmen
- Ofenpflege, z. B. der Tür und der Zustellung, regelmäßig durchführen
- „Energieeffizientes“ Feuerfestmaterial, z. B. in Bezug auf Isolationsfähigkeit, Temperaturwechselbeständigkeit und Verschleißfestigkeit verwenden
- Krätzeanfall minimieren
- Ofenabsaugung lastspezifischen fahren
- Abwärmenutzung prüfen
Aluminiumschmelzwerke, sogenannte Sekundärhütten, stellen aus Aluminiumschrott Schmelzen für genormte Aluminiumlegierungen her und beliefern damit vorwiegend Gießereien. Traditionell wurden die Aluminiumlegierungen als Metallblöcke, -Barren oder Masseln an die Gießereien geliefert, die dank genormter Abmessungen in größeren Stapelpaletten transportiert werden konnten.
Das bedeutet, dass das flüssige Metall zunächst erstarrt und in Form von Blöcken auf Paletten gestapelt, dann per LKW viele Kilometer transportiert und nach Ankunft in der Gießerei erneut wieder aufgeheizt und verflüssigt werden muss. Alternativ kann abhängig vom eigenen Schmelzprozess, den eigenen Kapazitäten und den benötigten Legierungen eine Flüssigmetallanlieferung geprüft werden.
Wie man in der Tabelle sieht, sind bei der Lieferung von Blockmaterial zwei Schmelzöfen an zwei verschiedenen Standorten nötig, wohingegen bei der Lieferung von Flüssigaluminium ein Schmelzaggregat beim Aluminiumschmelzwerk genügt.
Tabelle 1: Prozessketten der Lieferung von Blockmaterial im Vergleich zur Lieferung von Flüssigaluminium
Lieferung von Blockmaterial | Lieferung von Flüssigaluminium | |
Sekundär-Hütte | Aufbereiten von Recycling- und Umlaufmaterial | Aufbereiten von Recycling- und Umlaufmaterial |
Einschmelzen von Recyclingmaterial | Einschmelzen von Recycling- und Umlaufmaterial | |
Legierungsaufbereitung im Konverter | Legierungsaufbereitung im Konverter | |
Gießen der Barren | ||
Vorwärmen des Transportbehälters | ||
Abfüllen des Aluminiums | ||
Straßentransport | Transport der Barren | Transport des Flüssigmetalls |
Transport von Spänen | Transport von Umlaufmaterial | |
| Einschmelzen von Barren und Umlaufmaterial | |
(Selten: Warmhalten und Schmelzbehandlung) | Warmhalten und Schmelzbehandlung | |
Warmhalten am Gießplatz | Warmhalten am Gießplatz |
Das in der Sekundärhütte eingeschmolzene Aluminium wird den Gießereien in flüssiger Form zur Verfügung gestellt. Dazu muss das Aluminium in spezielle wärmegedämmte LKW-Transport-Behälter abgefüllt und direkt zu den Gießereien geliefert werden.
Eine Überhitzung des Metalls wird so vorgenommen, dass das Metall garantiert acht Stunden flüssig bleibt. Daraus ergibt sich die maximale Transportentfernung von vier Stunden LKW-Fahrtzeit, da im Fall der Nichtannahme des Metalls noch zum Sekundärschmelzwerk zurückgefahren werden können muss.
Unter ökologischen Gesichtspunkten ist ein Weniger an Energiebedarf und ein Weniger an Metallverlusten mit einem Weniger an CO2-Ausstoß gleichzusetzen. Unter Annahme eines bereits erwähnten spezifischen Energiebedarfs einzelner 0fentypen von 700 kWhth/tAL bis 1200 kWhth/tAL und unter der Annahme eines für Erdgas resultierenden Emissionsfaktors von 0,056 Tonnen CO2 pro Gigajoule Energiebedarf, ergibt sich eine Vermeidung von 141 kg CO2/t Aluminium bei 700 kWh/t und von 242 kg CO2/t bei 1.200 kWhth/tAL.
Für energetisch relevante Prozesse bei der Anlieferung mit Flüssigmetall wurden folgenden Daten ermittelt:
- Das Schmelzen und Warmhalten in der Sekundäraluminiumhütte (800 kWh/t)
- Das Vorwärmen der Transportbehälter (Etwa 150 kWh/t)
- Verluste beim Transport (Etwa 75 kWh/100 km)
Neben dem Energiebedarf ist die Betrachtung des Metallverlustes ein entscheidendes Kriterium beim Vergleich der Lieferung von Blockmaterial (Masseln) oder Flüssigmetall.
Aufgrund der bekannten Affinität des Aluminiums zum Sauerstoff treten beim Schmelzen von Aluminium unwiederbringliche Metallverluste durch Oxidation ein. Metallverluste variieren in der betrieblichen Praxis je nach Ofentyp und Fahrweise im Bereich von 2 Prozent bis 3 Prozent. Hingegen wird der Metallverlust bei einer Belieferung mit Flüssigmetall auf max. 0,2 Prozent angegeben, die vorwiegend durch den Entleervorgang der Flüssigmetallbehälter in den Gießereien entstehen. Gegenüber der Anlieferung mit Flüssigmetall ergibt sich ein Metallverlust von 2 Prozent bis 5 Prozent, angesetzt mit 20 kg/t bis 50 kg/t.
Für einen Schachtofen wird eine theoretische spezifische Schmelzenergie von 600 kWhth/tAL angegeben, die sich bei einem reinen Einsatz von Blockmaterial auf 690 kWhth/tAL erhöht. Bei einem kombinierten Schmelz- und Warmhaltebetrieb wurden Daten für typische Schachtschmelzöfen von bis zu 900 kWhth/tAL ermittelt, wobei der Anteil für den Energieaufwand zum reinen Warmhalten der Schmelze mit 180 kWhth/tAL angegeben wird. Für die in Aluminiumgießereien teilweise noch eingesetzten Herd- und Wannenöfen wird der spezifische Energiebedarf mit bis zu 1.200 kWhth/tAL. angegeben.
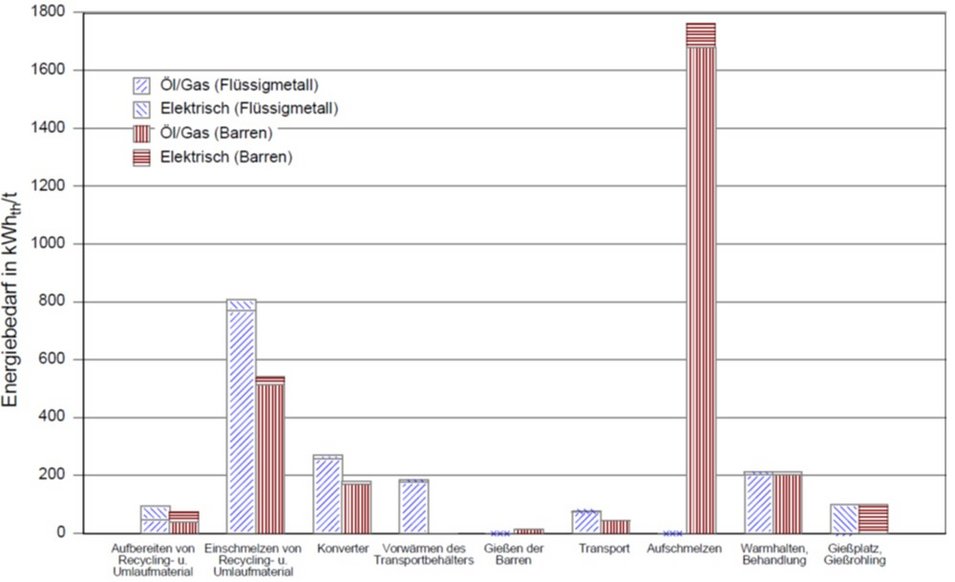
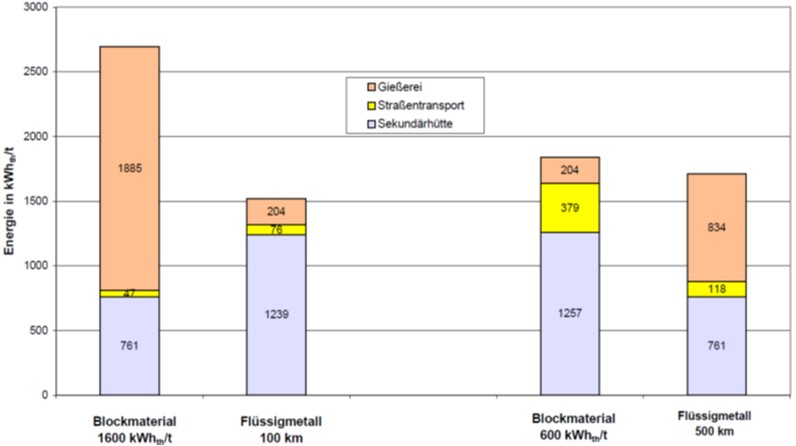
Bei der hohen Bedeutung des Schmelzens für den Energieeinsatz einer Gießerei bekommt der Einsatz von Flüssigmetall oder festem Blockmaterial entsprechend hohe Bedeutung für die Gesamtbewertung einer Aluminiumgießerei hinsichtlich der Energieeffizienz.
Soll in die Betrachtung der Energieeffizienz einer Aluminiumgießerei auch die Wertschöpfungskette mitbetrachtet werden, so ist bei Aluminiumgießereien besonders relevant, ob Primär- oder Sekundäraluminium zur Herstellung der Gussteile eingesetzt wird.
In einer Aluminiumhütte ist der Energieeinsatz für die Herstellung von Primäraluminium etwa zwanzigmal höher als wie für die Herstellung einer vergleichbaren Menge von Sekundäraluminium. Sowohl für den Einsatz von Flüssig- oder Fest-Aluminium als auch für die Entscheidung Primär- oder Sekundäraluminium einzusetzen, sind technische und wirtschaftliche Kriterien mitentscheidend.
So sind für den Einsatz von Flüssigaluminium beispielsweise die Entfernung zur liefernden Aluminiumhütte und/oder die Vielfalt der verwendeten Aluminiumgusslegierungen und ihrer jeweiligen Einzelmengen wichtig. Bei der Entscheidung zwischen Primär- und Sekundäraluminium sind entscheidende metallurgische und Werkstoff-Kriterien mit einzubeziehen.
Um die Effizienz des Flüssigmetalltransports zu verbessern, wurde die Auskühlung der Transportbehälter in einem Forschungsprojekt näher untersucht, da die Transportbehälter trotz Zustellung mit Feuerleichtsteinen und Isoliermatten zu hohe Temperaturverluste aufwiesen.
Bei neu zugestellten Behältern und funktionsfähiger Dämmschicht sind Verluste von minimal 5 K/h möglich, wohingegen bei schlecht wärmeisolierten Transportbehältern bis zu 20 K/h gemessen wurden. Gleichzeitig sollten die Oberflächentemperaturen 70 °C nicht überschreiten. Der Einsatz neuer Hochtemperaturisolierstoffe kann zu einer Reduzierung der Wärmeverluste beitragen.
Dazu wurde eine simulationsgestützte Prozessanalyse mit Fahrdaten und Strömungssimulation durchgeführt. Die Transportbehälter wurden in sechs Zonen eingeteilt: Verschluss, Stutzen, Deckel, Oberteil, Mittelteil und Boden.
Hohe Temperaturverluste im breiten Mittelteil, in dem die Aluminiumschmelze lagert, waren zu erwarten gewesen. Interessantes Ergebnis der Simulation war aber, dass fast genau so viel Wärme über den nicht isolierten Stutzen wie über den Mittelteil verloren geht. Ferner waren die Wärmeverluste im mittleren der drei Behälter während des Transports am höchsten.
Zwei Optimierungsmaßnahmen wurden daher erarbeitet: Isolierung von Stutzen und Verschluss und Einhausung von Behälter 1 bis 3, was zu einer Reduzierung der Wärmeverlustmenge von ungefähr 37 Prozent und 49 Prozent führen würde.
Tabelle 2: Wärmemengenverlust pro Bereich (1. Behälter) in Wh
Boden | Mittelteil | Oberteil | Deckel | Stutzen | Verschluss | |
Ohne Isolierung | 2.525 | 7.669 | 3.981 | 2.286 | 7.056 | 2.821 |
Mit Isolierung | 2.555 | 7.763 | 4.029 | 2.314 | 227 | 85 |
Mit Einhausung | 2.087 | 5.986 | 2.961 | 1.855 | 472 | 176 |
Erreichter Umweltnutzen
- Geringerer Energiebedarf
In der Literatur kommt man insgesamt zu der Schlussfolgerung, dass die Anlieferung von Flüssigmetall in der Regel energetisch günstiger als der Schmelzbetrieb in einer Gießerei ist, was sich sowohl auf den Gesamtenergieverbrauch als auch nur der Energieverbrauch innerhalb der Gießerei bezieht.
Verlagerungseffekte
Keine Verlagerungseffekte
Anwendbarkeit
In Gießereien mit brennstoffbeheizten Schmelz- und Warmhalteöfen oder Flüssigmetallanlieferung.
Wirtschaftliche Aspekte
Unabhängig von der ökologischen Dimension und der Energieeffizienz wurde die Anlieferung in der Vergangenheit vorwiegend aufgrund des ökonomischen Optimierungspotenzials betrachtet, da der eigene Schmelzbetrieb reduziert oder ganz entfallen kann.
Gerade bei Neuinvestitionen im Schmelzbetrieb lohnt sich der Vergleich mit einer Flüssigaluminiumanlieferung. Bestehende Schmelzbetriebe weisen häufig niedrigere Schmelzkosten auf. In Gießereien sind aber auch „Mischformen“ zu finden, nämlich dass ein Teil flüssig angeliefert wird und ein Teil selbst geschmolzen wird, um flexibel auf Kapazitätsanpassungen zu reagieren.
Bei Automobilherstellern sind zwei Trends zu erkennen:
- Überwiegende Anlieferung von Fest- anstatt Flüssigmetall
- Das Kreislaufmaterial wird nicht mehr ins Umschmelzwerk zurückgeliefert, sondern in eigenen Schmelz- und Warmhalteöfen erneuet eingeschmolzen
Gründe für die Anwendung dieser Technik
- Ökonomische und ökologische Vorteile der Maßnahmen
Der Flüssigmetalltransport erfordert zwar einen relativ hohen logistischen Aufwand in den Sekundärschmelzwerken, erspart jedoch den Gießereien Schmelzöfen und ein entsprechend dimensioniertes Blocklager.
Referenzanlagen
- Literaturquellen
- BMW Werk/Leichtmetallgießerei, Landshut
Informationsquellen
- Bayerisches Landesamt für Umweltschutz (Hrsg.) (2005): Effiziente Energieverwendung in der Industrie – Teilprojekt Metallschmelzbetrieb – Effiziente Energienutzung in Nicht-Eisen-Metall-Schmelzbetrieben, www.lfu.bayern.de/energie/co2_minderung/doc/energieverwendung_metallschmelzbetriebe.pdf, Abruf April 2013
- Energieeffizienter Gießereibetrieb Version 1.0
- Kegelmann, D. (2013): Neue Öfen für Automobilguss. In: Giesserei-Erfahrungsaustausch, Nr. 3+4, S. 18-19
- Kuom, M.; Urbach, R. (2007): Erweiterte Belieferungsmöglichkeiten von Aluminiumgießereien mit Flüssigaluminium. In: Giesserei, Nr. 6, S. 162-171
- Lange, O. (2007): Energiefresser auf Diät setzen. In: Giesserei-Erfahrungsaustausch, Nr. 1+2, S. 36-41
- Ringleb, A. (2012): Vortrag BDG Fachausschuss Leichtmetallguss - Steigerung der Energieeffizienz beim Transport von Flüssigmetall durch simulationsgestützte Prozessanalyse, Neckarsulm 2012
- Strikowestofen Group (2013): Schmelz-Energiekosten nahezu halbiert. In: Giesserei, Nr. 07, S. 17