GIESSEREI
Energieeinsparung durch leistungsoptimierte Chargierung von Mittelfrequenz-Induktionstiegelöfen

Das Chargierverfahren beim Schmelzprozess in Hochleistungs-Induktionstiegelöfen hat bedeutenden Einfluss auf Produktivität und Energieeffizienz.
Von Erwin Dötsch, Robert Ibach und Marco Rische, Dortmund
Erschienen in GIESSEREI 06/2012
Umrichter mit Konstantleistungsregelung
Bei modernen Induktionstiegelöfen erfolgt die Stromversorgung entsprechend Bild 1 über einen Frequenzumrichter, der die Induktionsspule für die geforderte Leistung mit Strom einer geeigneten Frequenz versorgt. Der Umrichter besteht aus einem Gleichrichter, einem Wechselrichter und einem Zwischenkreis. Zusammen mit der parallel geschalteten Kondensatorbatterie und der Induktionsspule
bildet er einen Schwingkreis mit variablen Größen von Strom, Spannung und Frequenz, die sich automatisch an die in Form des Schmelzgutes innerhalb der Spule vorliegende Last anpassen. Strom und Spannung werden bei der Auslegung des Umrichters als Produkt der Nennleistung so überdimensioniert, dass sie zusammen mit der sich automatisch einstellenden Resonanzfrequenz stets die volle Leistung auf das sich in unterschiedlichem Zustand im Spulenbereich befindliche Schmelzgut übertragen. Auf diese Weise werden die kürzeste Schmelzzeit für eine vorgegebene Charge und damit der
geringste Energiebedarf sowie die höchste Produktivität der Schmelzanlage erreicht. Man spricht von einem „Konstantleistungsumrichter“, der entsprechend Bild 2 in Bezug auf Strom und Spannung nicht auf einen Arbeitspunkt ausgelegt ist, sondern über einen Strom- und Spannungsbereich von jeweils 60 bis 100 % verfügt, der entsprechend der eingetragenen Lastkennlinie in Abhängigkeit vom elektrischen Widerstand des Schmelzgutes in der Spule abgefahren wird [1].
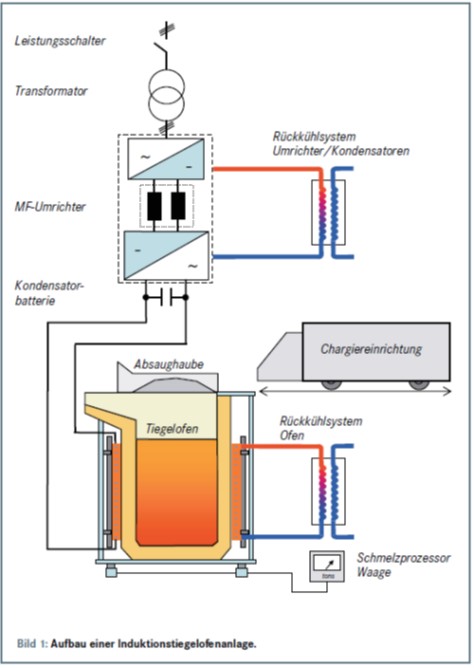
Der im Konstantleistungsumrichter vorgegebene Strom- und Spannungshub ist aus technischen und wirtschaftlichen Gründen begrenzt. Daher wird die Leistungskonstanz bei in Stückgröße und Schüttdichte stark schwankendem Schmelzgut im praktischen Schmelzbetrieb besonders zu Anfang der Schmelzcharge, wo der Tiegel nur mit festem Schmelzgut gefüllt ist, häufig nur unzureichend erreicht. In der Regel stellt sich der in Bild 3 gezeigte Leistungsverlauf über der Zeit ein (schwarze Kurve), der dort zusammen mit dem Verlauf des Ofeninhalts (grüne Kurve) und dessen theoretischer Temperatur (braune Kurve) für einen 12 t-6100 kW-Mittelfrequenz-Tiegelofen (MF-Tiegelofen) dargestellt und wie folgt zu erklären ist: Beim Anfahren des Tiegelofens mit ferromagnetischem Schmelzgut wird bereits bei niedrigem Füllgrad der volle Leistungseintrag dadurch erreicht, dass aufgrund der hohen magnetischen Leitfähigkeit (Permeabilität) mit relativ niedriger Spannung ein ausreichend
hoher Strom induziert wird. Beim Überschreiten der Curietemperatur im Bereich der Eindringtiefe fällt die magnetische Leitfähigkeit dort auf einen Wert von eins. Damit verschlechtert sich die Ankopplung
des elektromagnetischen Feldes und der Strom und damit der Leistungseintrag brechen trotz des automatischen Anstiegs der Umrichterspannung auf ihren Höchstwert deutlich ein. Erst nach Ablauf von etwa 15 min ändern sich die Verhältnisse im Spulenbereich aufgrund des steigenden Schmelzeanteils so, dass mit der maximalen Umrichterspannung ein zum Erreichen der Nennleistung ausreichend hoher Strom induziert wird. Mit dem weiteren Füllen der Spule steigt der Strom bei gleichzeitig abfallender Spannung weiter, bis beide Größen den vorgesehenen Arbeitspunkt erreichen.
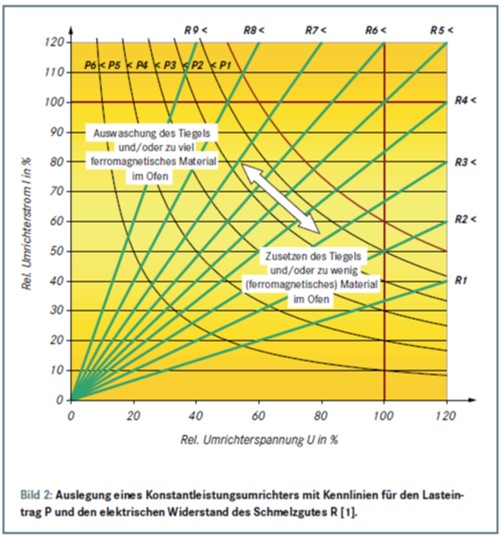
Trotz der Ausstattung des Umrichters mit dem in Bild 2 dargestellten Strom- und Spannungshub ist demnach die Leistungsnutzung am Anfang der Schmelzperiode unbefriedigend. Im Folgenden wird ein
Weg zur optimalen Leistungsnutzung auch in diesem Bereich und damit zur Minimierung des Energieverbrauchs aufgezeigt.
Leistungsoptimiertes Chargieren
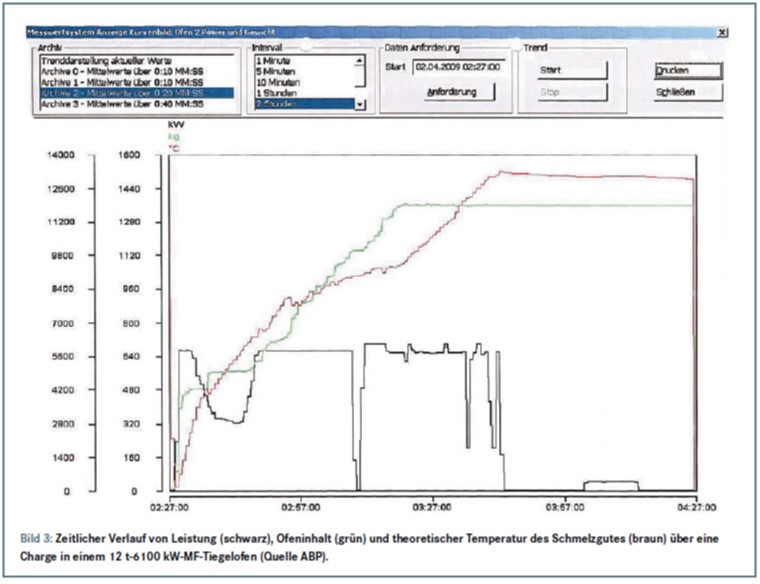
Der satzweise Betrieb der MF-Tiegelöfen erfordert eine quasikontinuierliche Beschickung [2]. Dazu werden die eisentragenden Einsatzstoffe in vorgegebener Reihenfolge für eine Schmelzcharge per Magnetkran in eine fahrbare Vibrationsrinne geladen. Die Zuschlagstoffe werden in einen separaten Behälter dosiert, der das Material in einen Bunker im vorderen Teil der Chargiereinrichtung ablädt. Mit dieser Beladung, meist für eine komplette Schmelzcharge, fährt die Beschickungseinrichtung auf der Ofenbühne in Chargierposition Bild 4) und chargiert das Schmelzgut möglichst in der in Bild 5 dargestellten Reihenfolge in den Tiegelofen [3]. Der Chargierund Schmelzprozess wird über den so genannten Schmelzprozessor gesteuert. Dazu werden der aktuelle Inhalt des Tiegelofens über Druckmessdosen erfasst und die zum Schmelzen der Teilchargen auf eine vorgegebene Temperatur benötigte Energie vom Schmelzprozessor jeweils berechnet und freigegeben. Der aktuelle Inhalt und die
aus dem jeweiligen Energieeintrag berechnete mittlere Temperatur werden auf dem Bildschirm des Schmelzprozessors als kennzeichnende Größen für die Ofenbedienung deutlich angezeigt (Bild 6).
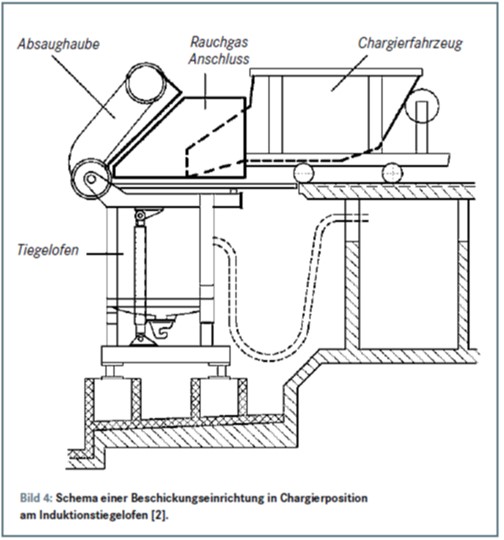
Der in Bild 3 zu sehende Leistungseinbruch zu Beginn einer Schmelzcharge lässt sich nun durch eine geeignete Chargierfolge beim Einbringen der ferromagnetischen Einsatzstoffe verhindern. Dazu wird der Einfluss der Permeabilität auf die Ankopplung des elektromagnetischen Feldes an das magnetische Schmelzgut genutzt. Bei kaltem Schmelzgut hat die Permeabilität einen Wert von mehr als 100, um bei Überschreiten des Curiepunktes bei etwa 770 °C auf den Wert 1 zu fallen. Die hohe Permeabilität des kalten Schmelzgutes ist der Grund für die gute Ankopplung und damit den hohen Leistungseintrag zu Beginn der Schmelzperiode, wie zuvor beschrieben.
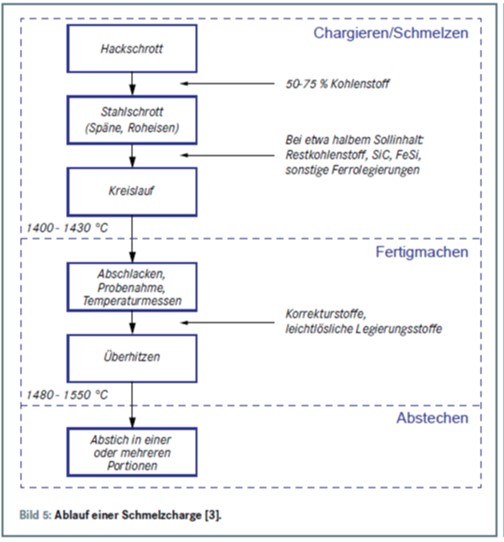
Dieser Leistungseintrag nahe der Nennleistung stellt sich erfahrungsgemäß auch dann ein, wenn die Spule zu Beginn der Schmelzperiode mit Schmelzgut nicht wie üblich voll-, sondern nur teilgefüllt wird. Der hohe Leistungseintrag lässt sich im weiteren Schmelzablauf aufrecht erhalten, wenn auf die niedrige Anfangsfüllung das weitere ferromagnetische Schmelzgut in kleinen Portionen nachchargiert wird. Dazu wird der Leistungsbezug vom Schmelzprozessor kontinuierlich erfasst und bei Abfallen unter Nennleistung aufgrund des Überschreitens der Curietemperatur des jeweils chargierten Schmelzgutes gerade soviel Material nachchargiert, dass sich die Nennleistung wieder einstellt. Der Vorgang wird so lange wiederholt, bis das verfügbare freie Tiegelvolumen über dem eingefüllten Schmelzgut erschöpft ist. Dann ist nach vorliegender Erfahrung der Füllgrad innerhalb der Spule so hoch, dass der volle Leistungsbezug auch bei einer Temperatur des Schmelzgutes über Curie mit dem Konstantleistungsumrichter gewährleistet ist. Im weiteren Schmelzablauf wird quasikontinuierlich so weiter chargiert, dass der Ofen mindestens bis Spulenoberkante gefüllt bleibt und somit bis zum Ende
des Schmelz- und anschließenden Überhitzungsprozesses
die volle Leistung zieht.
Automatisierung des optimierten Anfahrens
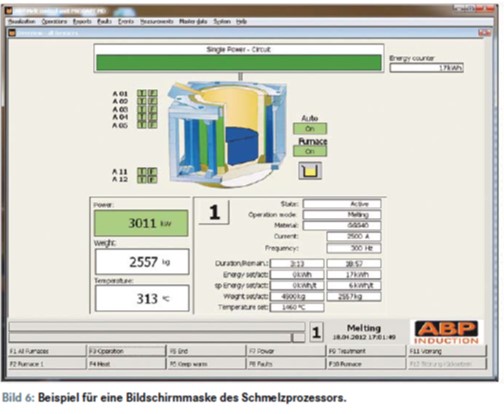
Die im vorstehenden Abschnitt beschriebene Beschickung erfolgt mit Chargiereinrichtungen, die trotz sonstiger Automatisierung des Schmelzprozesses von Hand betätigt werden. Grund dafür ist, dass man dem Bediener die Aufgabe überträgt, den laufenden Chargier- und Schmelzprozess per Augenschein zu überwachen und somit das Risiko zu vermeiden, dass sich das Schmelzgut im Tiegel beim Chargieren zu einer „Brücke“ oberhalb der Spule staut und dass das darunter im Tiegel befindliche Schmelzgut möglicherweise bis zum Tiegeldurchbruch überhitzt wird. Die genannte Brückenbildung
findet bei Einsatz von ausreichend kleinstückigem Schmelzgut nicht innerhalb der Aktivspule, sondern nur über Spulenoberkante, d. h. ohne Eingriff des elektromagnetischen Feldes, statt. Da der beschriebene Chargierprozess zum Start der Schmelzcharge bei minimaler Füllung innerhalb der Aktivspule abläuft, lässt er sich ohne zusätzliches Sicherheitsrisiko automatisieren. Dazu wird die Steuerung der Chargiereinrichtung in geeigneter Weise mit den Schmelzprozessordaten der Leistungsaufnahme des Tiegelofens so verbunden, dass das beschriebene Chargierverfahren quasikontinuierlich
mit kleinen Zugabeportionen automatisch abläuft und somit die Optimierung des Chargierablaufs sichergestellt ist, ohne dass der Bediener überfordert wird.
Verfahrensbedingte Leistungseinbrüche
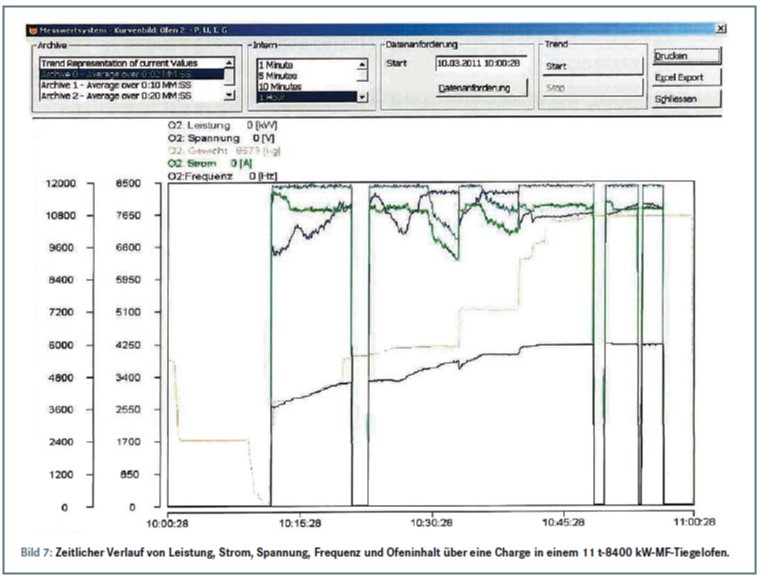
Bild 5 zeigt den im Regelfall praktizierten Schmelzablauf, bei dem die Legierungsstoffe zusammen mit dem metallischen Schmelzgut chargiert werden. Da auch die Korrekturstoffe für die Endanalyse während des Überhitzens bei mit voller Leistung eingeschaltetem Ofen eingerührt werden, wird für das Legieren weder zusätzliche Schmelzzeit benötigt, noch der Leistungsbezug beeinträchtigt.
Diese für den Energieverbrauch günstigen Verhältnisse ändern sich dann, wenn an den Legierungsprozess besondere Anforderungen gestellt werden. Das ist beispielsweise bei der Herstellung von Gusseisenlegierungen mit Kohlenstoffgehalten nahe der Sättigungsgrenze der Fall. Dafür hat es sich bewährt, das Aufkohlungsmittel bei einem Badstand innerhalb der Aktivspule in das freie Schmelzbad zu chargieren. Man erreicht dann ein hohes Ausbringen der Kohle bei gleichzeitig geringer Schlackenbildung.
Die daraus entstehenden Folgen für den Energieeintrag lassen sich aus Bild 7 ablesen, wo beispielhaft für die Herstellung einer hoch kohlenstoffhaltigen Legierung der zeitliche Verlauf von Strom, Spannung, Leistung, Frequenz und Ofenfüllung für die Schmelzperiode in einem 11 t-8400 kW-MFTiegelofen dargestellt ist. Man erkennt, dass sich beim Anfahren mit Schmelzgut offensichtlich guter Schüttdichte Strom, Spannung und Frequenz im Schwingkreis automatisch so einstellen, dass zunächst die Nennleistung von 8400 kW konstant gezogen wird. Bei einem Inhalt von etwa 6 t wird nach ca. 15 min die Chargierung unterbrochen, um bei weiterer Leistungsbeaufschlagung für eine von Feststoff freie Badoberfläche zu sorgen. Wegen der dadurch geringer werdenden Spulenfüllung fällt der Strom trotz des Spannungsanstiegs bis zur Spannungsgrenze so ab, dass die Leistung auf ca. 7000 kW einbricht. Bei diesem Zustand werden das Aufkohlungsmittel und anschließend ca. 800 kg Schrott chargiert, dann bei wieder vollem Leistungsbezug eingerührt. Nach erneut kurzzeitigem Strom- und Leistungsrückgang werden ca. 1,5 t und weiter quasikontinuierlich Schmelzgut bis zur Nennfüllung von etwa 11 t nachchargiert. Strom, Spannung und Frequenz stellen sich dabei auf ihre für diesen Arbeitspunkt ausgelegten Werte ein, so dass die Spule während dieser Zeit konstant mit der vollen Leistung
beaufschlagt wird. Für solche besonderen Bedingungen des Schmelzablaufs lässt sich die Leistungsaufnahme nur soweit optimieren, wie die Zugabe der Legierungsstoffe bei möglichst hohem Badstand innerhalb der Aktivspule durchführbar ist. Dabei sind die Grenzen dadurch gegeben, dass zum einen die Intensität der Badbewegung bei größerer Ofenfüllung abnimmt und zum anderen die für die Auflösung und homogene Verteilung der Legierungsstoffe benötigte Zeit nicht mehr zur Verfügung steht.