Umweltschutz und Energietechnik (3. Folge)
Von Manuel Bosse, Düsseldorf
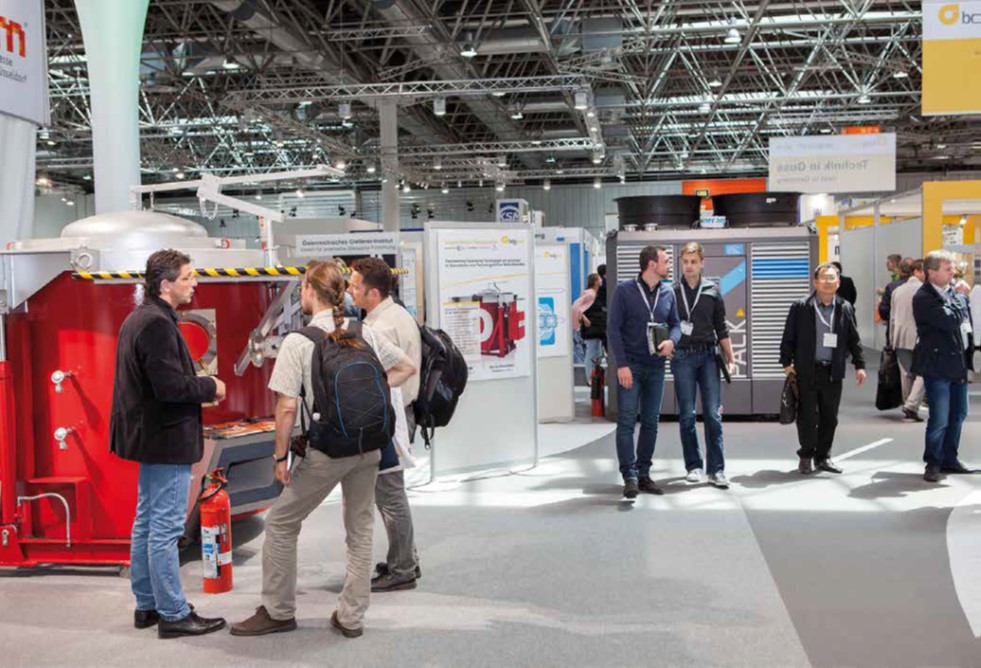
Die vom BDG initierte Sonderschau „Energieeffizienter Gießereibetrieb 2.0“ mit aktuellen Beispielen zu energieeffizienten Lösungen in der Gießerei-Industrie stieß auf der GIFA 2015 auf große Resonanz bei den Besuchern.
Erschienen in GIESSEREI 10/2015
Umwelt- und Arbeitsschutz
Die erste Jahresübersicht Umweltschutz und Energietechnik wurde in der Giesserei Nr. 6/2013 veröffentlicht. Die dort angesprochenen prozessintegrierten Umweltschutzmaßnahmen, wie z. B. Verbesserung von organischen Bindern, sind weiterhin aktuell. Positive Effekte auf die Gussoberflächenbeschaffenheit bei organischen Bindern entstehen einerseits durch die schützende Glanzkohlenstoffschicht, welche sich zwischen Guss und Kern legt, und anderseits durch die entstehenden
Gaspolster, welche das Eindringen des Flüssigmetalls in die Sandstruktur und somit die Entstehung von Penetrationen erschwert. In der Literatur wird in den letzten Jahren aber vor allem über den Umstieg von organischen auf anorganische Binder diskutiert. Der Artikel von J. Müller u. a. [1] listet Faktoren auf, die maßgeblichen Einfluss auf Penetrationen haben können (Bild 1) und hebt die Vorteile von anorganischen Bindern hervor. Gleichzeitig räumt dieser Artikel mit gängigen Vorurteilen, wie z. B. geringere
Maßhaltigkeit beim Abguss, höherer Kernbruch und Nichtregenerierbarkeit gegenüber anorganischen Bindersystemen auf.
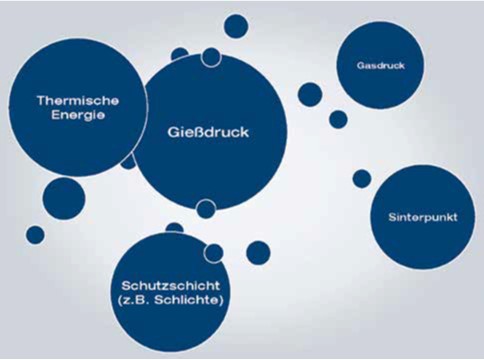
Energietechnik und Energieeffizienz
H. Deters und J. Müller [2] berichten über einen zertifizierten Ökobilanzvergleich von anorganischen Bindersystemen gegenüber klassischen Cold-Box-Bindersystemen. Der Vergleich zeigt, dass anorganische Binder zwar bei Kernherstellung, Entkernen und Sandregenerierung gegenüber dem verglichenen Cold-Box-System, z. B. durch höheren Strombedarf, (leicht) im Nachteil, jedoch über den gesamten Lebenszyklus – vor allem durch die nicht benötigte Aufbereitung der Abluft – deutlich umweltfreundlicher sind (Bild 2).
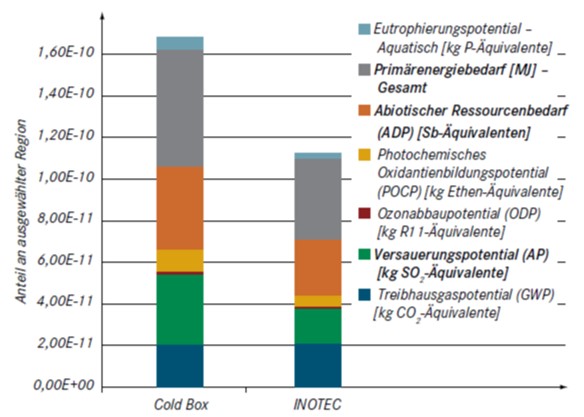
Um auch weiterhin den Gießereisand zu einem hohen Anteil im Kreislauf fahren zu können, sind energieeffiziente Sandregenerierungen in der Gießerei-Industrie gefragt. Neue Sandregenerierungen bedingen durch Einbau einer thermischen Regenerierungsstufe einen erhöhten Strombedarf, was sich in den Energiekennzahlen pro Tonne guter Guss negativ bemerkbar macht. K. Herbers [3] berichtet über eine neue Sandregenerierung für das in Deutschland eher selten angewandte Pep-Set-Verfahren. Die gewählte Regenerieranlage verfügt neben der mechanischen auch über eine thermische Regenerierungsstufe, die den Binder während eines Brennprozesses in einem etwa 700 °C heißen Ofen vom Sand trennt. Durch diese intensive Regenerierung sank der Neusandbedarf von 40 auf 10 %, was die Gießereirestsand-Entsorgungskosten und die Kosten für Neusand insgesamt reduziert. Diese Verbesserung überwiegt den Mehrbedarf an elektrischer Energie bei weitem.
Mit der Möglichkeit zur Aufbereitung von genutztem Trennmittel – gelöst bzw. emulgiert im betrieblichen Abwasser aus einer Aluminiumdruckgießerei – beschäftigt sich J. Freund [4]. Die Entsorgung von Abwasser zusammen mit anderen betrieblichen Abfällen führt zu hohen Entsorgungskosten, weshalb eine hausinterne Aufbereitung des Abwassers ökonomisch und ökologisch sinnvoll ist. Mit effizienten Vakuumdestillationssystemen werden alle Substanzen, die einen höheren Siedepunkt als Wasser haben, verdampft. Zurück bleibt eine zu entsorgende Menge von unter 5 % im Vergleich zu einer ungefilterten Abwassermenge.
Zunächst war vorgesehen, dass im Jahr 2012 mit der Revision des „Merkblatts über Beste Verfügbare Techniken (BVT) in der Gießerei-Industrie“ begonnen wird. inzwischen ist mit einem Beginn der Revision frühestens Ende 2016 rechnen. Für diese Revision sind fundierte deutsche Beiträge wichtig, um einen, den Entwicklungen in Deutschland gerecht werdenden Stand der Technik in dieses internationale Dokument einzubringen. Dafür sind im IfG - Institut für Gießerei-technik, Düsseldorf, die gegenwärtig besten verfügbaren Techniken in der Gießerei-Industrie recherchiert und dokumentiert worden. Ende 2013 wurde das Projekt „Innovative Techniken: Beste Verfügbare Techniken (BVT) in Gießereien“ abgeschlossen und seit Anfang 2015 sind die Ergebnisse auf der Homepage des Umweltbundesamts abrufbar [5]. Im ersten
Teilprojekt wurden 23 Maßnahmen in deutschen Gießereien systematisch beschrieben, z. B. Verbesserungen im Schmelzbetrieb oder beim Ausbringen sowie Maßnahmen zur Reduzierung von Emissionen. Eine Übersicht über alle BVTMaßnahmen gibt die Tabelle 1.
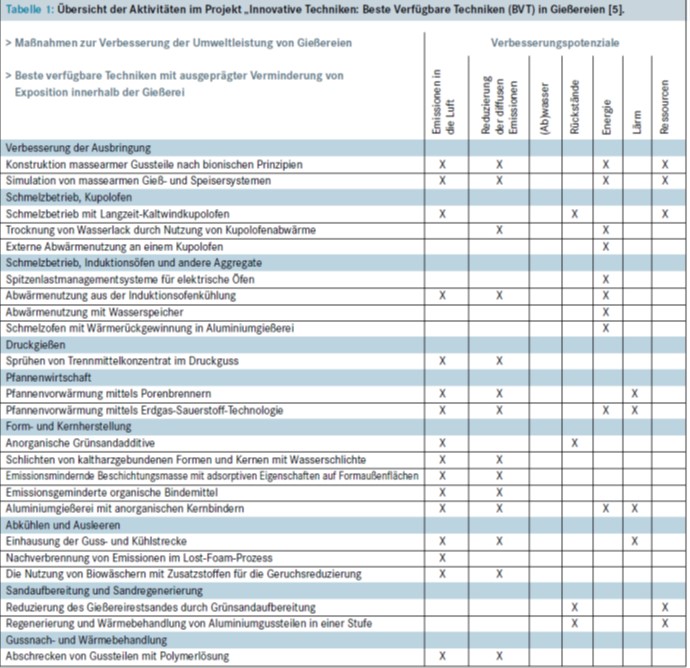
Energieeffizienter Gießereibetrieb
Im zweiten Teilprojekt folgte eine Darstellung der Emissionssituation in deutschen Gießereien Anfang der 2010er-Jahre sowie abschließend die Erhebung zur Verbreitung von Verfahren der Fertigungsund der Umwelttechnik in deutschen Gießereien.
Größere Potenziale zur Verbesserung der Umweltleistung von Gießereien lassen sich jedoch insbesondere in Ländern wie den sogenannten BRICS-Staaten (Brasilien, Russland, Indien, China und Südafrika) erreichen. In den letzten Jahrzenten wählte die Volksrepublik China bei der Auswahl zwischen Umweltschutz und Wirtschaftswachstum alle Möglichkeiten, um BIP-Steigerungsraten von über 10 % zu erzielen. Spätestens seit Beginn der 2010er-Jahre treibt das „Reich der Mitte“ jedoch seine eigene Energiewende voran. China hat mittlerweile weltweit die größte installierte Windenergieleistung und wird Deutschland voraussichtlich im Jahr 2015 auch bei der installierten Photovoltaikleistung den Spitzenplatz streitig machen. Bei nachgelagerten Umweltschutzmaßnahmen sind chinesische Gießereien sehr interessiert, wie man zuletzt im Jahr 2014 beim persönlichen Austausch von Vertretern des Hauses der Gießerei-Industrie anlässlich einer Konferenz in China oder auch auf der GIFA 2015 bemerken konnte. Auch die anderen BRICS-Staaten treiben Umweltschutzbemühungen voran, z. B. verschiedene Projekte zur Sandregenerierung oder Sandverwertung in brasilianischen Gießereien oder auch gemeinsam mit deutschen Partnern durchgeführte Forschungsprojekte mit südafrikanischen Gießereien [6].
Wie ein ganzheitlicher Ansatz zur Ressourcenschonung im Gießereibetrieb aussehen kann, ist in [7] anhand spezialisierter Bindemittel beschreiben (Bild 3).
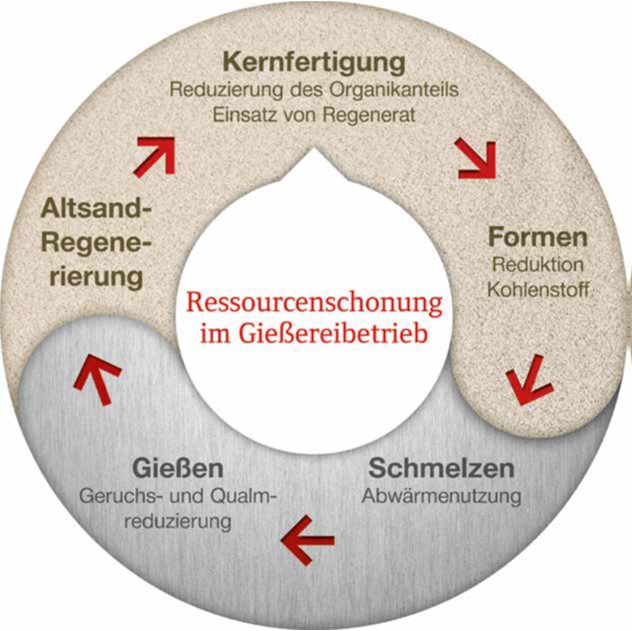
Bindemittel [7].
Deutsche Gießereien stehen vor Herausforderungen mit höheren Deponiekosten aufgrund schrumpfender Deponiekapazitäten oder zu hoher DOC/TOC-Werte im Gießereirestsand sowie sich verschärfender gesetzlicher Auflagen. Daher werden gegenwärtig veraltete VDG-Merkblätter zurückgenommen und durch neue, überarbeitete BDG-Richtlinien ersetzt.
Wichtige (politische) Informationen aus Berlin, Brüssel und den BDG-Arbeitskreisen zu aktuellen Umwelt- und Energiethemen bieten regelmäßige Newsletter sowie die jährlichen BDG-Umwelttage im September. Das Haus der Gießerei-Industrie hat im Zuge des Erneuerbare-Energien-Gesetzes (EEG) 2014 Gießereien mit umfangreichen Informationen und zahlreichen Einzelberatungen unterstützt und im Rahmen einer Verbändeallianz Änderungen und neue Ideen eingebracht.
Energiepolitische Rahmenbedingungen
Für die Wettbewerbsfähigkeit deutscher Gießereien sind Energiepreise ein entscheidender Faktor. Die Mittel zur Finanzierung der deutschen Energiewende werden über die Energiepreise auf die Endverbraucher umgelegt. Um die Belastungen insbesondere für die energieintensive Industrie zu begrenzen, hat die Bundesregierung unterschiedliche Ausnahmeregelungen geschaffen, sodass große Aluminium- und Kupferhersteller auf dem Weltmarkt wettbewerbsfähige Strompreise zahlen. Die mittelständisch geprägte Gießerei-Industrie muss jedoch im internationalen Vergleich mit hohen Strompreisen guten Guss produzieren [8]. Eine entscheidende Belastung für Gießereien stellt weiterhin die EEG-Umlage dar. In der letzten Jahresübersicht wurde aufgrund damaliger Prognosen noch gehofft, dass die Umlage auf 5,8 Cent sinken könnte, doch am Ende sank diese nur um 0,07 Cent auf 6,17 Cent pro kWh [9]. Dadurch zahlen die Gießereien im Durchschnitt nun 16,96 Cent pro kWh elektrische Energie.
Insgesamt können weiterhin nur etwa 20 Prozent der deutschen Gießereien von der Besonderen Ausgleichsregelung im EEG profitieren. Um für eine einzelne Gießerei eine Teilentlastung von der EEG-Umlage zu erreichen, war im Geschäftsjahr 2014 eine Stromkostenintensität (Verhältnis der Stromkosten zur Bruttowertschöpfung) von 17 % erforderlich, um Ende Juni 2015 einen Antrag für das Jahr 2016 zu stellen. Zusätzlich musste ein Energiemanagementsystem zertifiziert oder eine EMAS-Urkunde für ein verifiziertes Umweltmanagementsystem vorgelegt werden. Aus einigen deutschen Gießereien ist bekannt geworden, dass diese nun schrittweise die volle EEG-Umlage zahlen müssen, da die 17-%-Hürde nicht übersprungen wurde [10]. Die Zusatzbelastung allein durch die EEG-Umlage liegt häufig über der durchschnittlichen Umsatzrendite von Gießereien. Es wird durch das EEG tatsächlich gesetzlich ein Anreiz gesetzt, dass der Strombedarf unnötig gesteigert wird, um die Stromkosten zu erhöhen oder noch viel schlimmer, dass auf dem Rücken der Mitarbeiter womöglich versucht wird, die Bruttowertschöpfung zu senken.
Um zumindest die im Vergleich zur Besonderen Ausgleichsregelung deutlich geringere Gewährung der steuerlichen Rückvergütung durch den Spitzenausgleich vom Energie- und Stromsteuergesetz zu erhalten, wurde die Einführung von Systemen zur Verbesserung der Energieeffizienz vorangetrieben: Ein (integriertes) Energiemanagementsystem nach DIN EN ISO 50001 haben aktuell etwa 165 Gießereien zertifizieren lassen. Weitere 250 Gießereien haben ein sogenanntes alternatives System zur Verbesserung der Energieeffizienz etabliert oder ein Energieaudit nach DIN EN 16247-1 durchführen lassen.
Im April 2015 ist das neue Energiedienstleistungsgesetz in Kraft getreten, was für Nicht-KMU-Gießereien ein Energieaudit oder den Beginn der Einführung eines Energiemanagementsystems fordert. Davon sind nur etwa 5 % der deutschen Gießereien betroffen und bis auf zwei bekannteFälle ergeben sich aus diesem Gesetz für Gießereien keine unmittelbaren Konsequenzen bis Jahresende. Zum besseren Verständnis sind in der Tabelle 2 die wichtigsten Punkte der drei energierelevanten Gesetze zusammengefasst.
Tabelle 2: Die wichtigsten Punkte der drei energierelevanten Gesetze EEG 2014, SpaEfV und EDL-G (Quelle: TÜV Rheinland mit Ergänzungen M. Bosse 2015).
Gesetz | EEG 2014 | SpaEfV | EDL-G |
KMU-Gießerei | Bei Strombedarf 1-5 GWh, ein System zur Verbesserung der Energieeffizienz nach Anlage 2 SpaEfV oder ein Energieaudit nach DIN EN 16247-1; oder bei über 5 GWh DIN EN ISO 50001 Zertifizierung oder EMASUrkunde | Ein System zur Verbesserung der Energieeffizienz nach Anlage 2 SpaEfV oder ein Energieaudit nach DIN EN 16247-1; oder alternativ DIN EN ISO 50001 Zertifizierung oder EMAS-Validierung | Nicht davon betroffen |
Nicht KMU-Gießerei | Kein Unterschied zur KMU-Gießerei | DIN EN ISO 50001 Zertifizierung oder EMAS-Urkunde | Bis zum 5. Dezember 2015 ein Energieaudit nach DIN EN 16247-1; oder Beginn mit der Einführung eines Energiemanagementsystems nach DIN EN ISO 50001 oder Aufbau eines Umweltmanagementsystems nach EMAS (Abschluss Zertifizierung/ Validierung 2016) |
EDL-G - Energiedienstleistungsgesetz EEG - Erneuerbare-Energien-Gesetz EMAS - Eco-Management and Audit Scheme (Umweltmanagementsystem/EU-Öko-Audit) KMU - Kleine und mittlere Unternehmen (Schwellenwerte unter 50 Millionen Euro Umsatz und bis 43 Millionen EUR Bilanzsumme pro Jahr, unter 250 Mitarbeiter SpaEfV - Spitzenausgleich-Effizienzsystemverordnung |
Auf Basis der Ergebnisse aus abgeschlossenen Projekten unterstützt die IfGService GmbH Gießereien bei der Einführung von Systemen zur Verbesserung der Energieeffizienz (Energiemanagementsysteme nach DIN EN ISO 50001 oder sogenannte Alternative Systeme nach Anlage 2 der Spitzenausgleich-Effizienzsystemverordnung) oder stellt bei Bedarf den Umwelt- und Energiemanagementbeauftragten. Die Gießerei-Industrie möchte kontinuierlich noch energieeffizienter werden, jedoch werden der Industrie immer wieder gesetzliche Hürden auferlegt, wie z. B. bei der effizienten Eigenstromerzeugung in Blockheizkraftwerken zur Strom- und
Wärmeerzeugung, auf die nun ebenfalls eine EEG-Umlage fällig wird. Gleichzeitig ist es für eine EEG-teilentlastete Gießerei schlichtweg ökonomischer Unsinn, gute Maßnahmen zur Verbesserung der Energieeffizienz, Projekte zur (erneuerbaren) Eigenstromerzeugung oder Stromerzeugung aus Abwärme durchzuführen, weil ansonsten womöglich der Schwellenwert von 17 % unterschritten wird und somit die volle EEG-Umlage in den Folgejahren gezahlt werden muss.
Energietechnik und Energieeffizienz
In der letzten Jahresübersicht wurde bereits über die Studie „Treibhausgasneutrales Deutschland bis 2050“ des Umweltbundesamts berichtet [11]. In einem rein nationalen Szenario soll nur mit technischen Maßnahmen ein Treibhausgasminderungsziel bis ins Jahr 2050 von 95 % gegenüber dem Jahr 1990 erreicht werden. Wirtschaftliche Überlegungen wurden bei dieser Studie ausgeklammert, was zu dem Ergebnis führte, dass aus rein technischer Sicht eine Substitution brennstoffbefeuerter Öfen möglich sei. Einzig der kokslose Kupolofen könnte eine Perspektive haben. In Deutschland wird jedoch aus verschiedenen Gründen kein solches Schmelzaggregat mehr betrieben. Etwa 50 bis 60 % des Flüssigeisens wird in Deutschland an einem der 60 Gießerei-Standorte in Kupolöfen geschmolzen.
Die letzte Technikerhebung im IfG vor über fünf Jahren wies 75 Kupolofen-Standorte aus. Die IfG-Service GmbH, Düsseldorf, hat in einer aktuellen Studie im Jahr 2015 insgesamt 28 Gießereistandorte mit Heißwind- und 32 Kaltwindkupolöfen ermittelt. Diese Daten wurden zusätzlich mit Industrieofenbauern abgeglichen. Damit lässt sich im Bereich der Kaltwindkupolöfen als Schmelzaggregate in deutschen Gießereien ein deutlicher Trend über die letzten zehn Jahre erkennen: Entweder werden die Aggregate auf den neusten Stand gebracht oder, was in den letzten Jahren häufiger der Fall war, durch Induktionsöfen substituiert.
Große Heißwindkupolöfen sind weiterhin für die Branche unverzichtbar, was das Positionspapier des Bundesverbandes der Deutschen Gießerei-Industrie ausführlich darlegt (Bild 4) [12]. Gleichzeitig muss betont werden, dass diese großen Schmelzaggregate unter den EUEmissionshandel fallen und somit ohnehin eine kontinuierliche Senkung des CO2-Ausstoßes vorangetrieben werden muss.
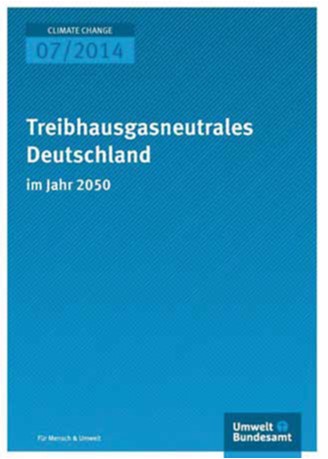
Energieeffizienter Gießereibetrieb
Neuste Beispiele zu energieeffizienten Lösungen für die Gießerei-Industrie wurden bei der gut besuchten Sonderschau „Energieeffiziente Gießereibetrieb 2.0“ auf der GIFA 2015 gezeigt. Die vier Themenfelder behandelten Abwärmepotenziale, erneuerbare Energien, beste verfügbare Techniken sowie das Thema „Ausbringung erhöhen“. Es sei auf die Nachberichterstattung in [13] verwiesen.
Nicht alle Maßnahmen zur Verbesserung der Energieeffizienz in Gießereien, über die in Fachartikeln berichtet wurden, konnten auf der Sonderschau präsentiert werden. Daher sind im Folgenden die wichtigsten Beiträge seit der letzten Jahresübersicht in der GIESSEREI Nr. 10/ 2014 systematisch aufgearbeitet:
Größte Einflussmöglichkeiten auf eine effiziente Gestaltung von Gussstücken ergeben sich bereits vor der Serienproduktion in der Planung, Simulation und Durchführung von Gießversuchen. Mittels statistischer virtueller Methoden kann ein belastbares Verfahren zur Auslegung robuster Fertigungsprozesse geschaffen werden. An Beispielen aus dem Automobilguss wurden verschiedene Optimierungsziele in der Gießprozesssimulation verdeutlicht [14]. Die bestmöglichen Bedingungen für Fertigungsparameter, für die Laufdimensionierung und Anschnittpositionen, aber auch für die Lage und Größe von Speisern und Kühlkokillen zeigen anhand weiterer Beispiele I. Hahn und J. C. Sturm [15].
Ein innovatives Angusskonzept mit optimiertem Strömungsverlauf im Aluminiumdruckguss wurde von P. Kohlmeyer, O. Lemanski und G. Röders [16] entwickelt.
K. Bembenek und K. Gregel [17] beschreiben ein funktionierendes Enterprise Content Management, welches die Basis für einen energieeffizienten Gießereibetrieb legt und wichtige Verwaltungsund Produktionsprozesse standardisiert.
Wie die Einführung einer Software die Prozessabläufe in einer Stahlgießerei verbessert, wird von J.-J. Alperowitsch u. a. [18] beschrieben. Durch durchgängige Dokumentation und gesicherte Vorgaben für die Nachlegierung und die Schmelzebehandlung wird für eine hohe Prozesssicherheit sowie Fehlervermeidung gesorgt.
C. Herrmann, T. Heinemann und S. Thiede [19] plädieren dafür, dass bei Neu- oder Umbauten in Gießereien die Ressourcen- und Energieeffizienz noch systematischer in die betrieblichen Entscheidungsprozesse einfließen müssen. Dazu müssen ganzheitliche Lösungen geschaffen werden, indem die energetischen und stofflichen Flüsse innerhalb der Gießerei transparent gemacht werden (Bild 5). Auf die energie- und ressourceneffiziente Gestaltung der Prozesskette beim Aluminiumdruckgießen wird dann im weiteren Beitrag intensiv eingegangen. Die Energiebedarfserfassung in Druckgießereien erfordert spezielles Knowhow, weshalb Druckgießereien sich von den Werkzeugbauunternehmen durch integrierte Lösungen Unterstützung erhoffen. Erste Ergebnisse wurden für Druckgießereien und einzelne Druckgießzellen präsentiert [20]. S. Theis [21] beschreibt eine weitere Software zur Energiedatenerfassung und -auswertung. Wie viel Energie für die tatsächliche Wertschöpfung beim Druckgießprozess erforderlich ist, wird in vielen Gießereien trotzdem nicht erfasst.
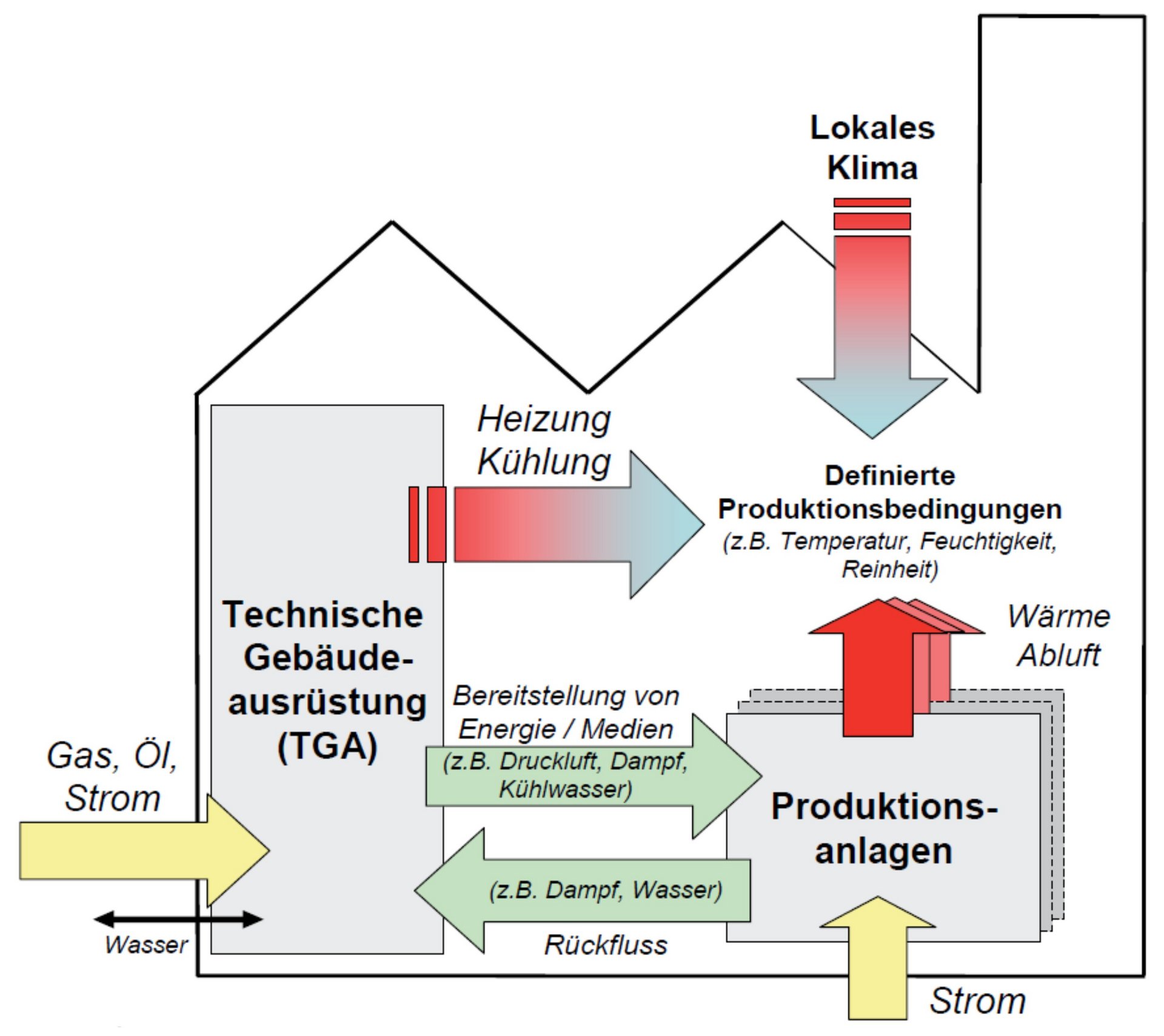
Die Energiebedarfserfassung in Druckgießereien erfordert spezielles Knowhow, weshalb Druckgießereien sich von den Werkzeugbauunternehmen durch integrierte Lösungen Unterstützung erhoffen. Erste Ergebnisse wurden für Druckgießereien und einzelne Druckgießzellen präsentiert [20]. S. Theis [21] beschreibt eine weitere Software zur Energiedatenerfassung und -auswertung. Wie viel Energie für die tatsächliche Wertschöpfung beim Druckgießprozess erforderlich ist, wird in vielen Gießereien trotzdem nicht erfasst.
R. Schillig u. a. [22] stellen ein praxistaugliches Verfahren vor, das es erlaubt, Effizienzbetrachtungen durchführen und Verbesserungspotenziale daraus abzuleiten.
Wie ein moderner, energieeffizienter Elektroschmelzbetrieb aussehen sollte, wird auch auf internationaler Ebene diskutiert [23]. An fünf Beispielen aus Schmelzbetrieben wird beschrieben, wie Schmelzraten von ungefähr 6,5 t Flüssigeisen pro Stunde in der Praxis erreicht werden (Tabelle 3). Entweder es existieren historisch gewachsen nur ein 20-t-Netzfrequenz-Induktionsofen, zwei parallele 20-t-Öfen oder drei 5-t-Mittelfrequenz-Induktionsöfen. Im Schmelzbetrieb 2 kann entweder Ofen 1 oder Ofen 2 efahren
werden. Durch zwei Energieversorgungseinheiten können im Schmelzbetrieb 3 zwei der drei Öfen gleichzeitig betrieben werden. Die Auslastungsrate steigt von 65 auf 75 % bei Schmelzbetrieb 2 und 3 gegenüber 1 und die Leistungsdichte ist mit 400 kW gegenüber 250 kW/t bei Schmelzbetrieb 3 deutlich höher. Die Schmelzbetriebe 4 und 5 laufen im Tandem-/Tridem-ähnlichen Betrieb mit zwei 5-t- bzw. drei 4-t-Mittelfrequenzöfen. Beim Tandemkonzept sichert ein Ofen die Flüssigeisenversorgung während der andere Ofen mit der zur Verfügung stehenden Restleistung beaufschlagt wird, in der Regel zum Aufschmelzen. Bei drei gleichzeitig betriebenen Öfen im Schmelzbetrieb 5 kann parallel beispielsweise in einem Ofen geschmolzen, ein Ofen vorbereitet und ein Ofen abgestochen werden. Insgesamt erhöht sich die Leistungsdichte bei Gießereibetrieb 5 auf 750 kW/t Flüssigeisen dadurch, dass die Auslastung auf (nahezu) 100 % steigt.
Tabelle 3: Vergleich von 5 Schmelzbetrieben, wie Schmelzraten von ungefähr 6,5 t Flüssigeisen pro Stunde in der Praxis erreicht werden [23].
Gießerei | Gießerei 1 | Gießerei 2 | Gießerei 3 | Gießerei 4 | Gießerei 5 |
Öfen | 20 t- Netzfrequenzbetrieb | 2 x 20 t- Netzfrequenzbetrieb | 3 x 5 t- Mittelfrequenzbetrieb | 2 x 5 t- Tandembetrieb | 3 x 4 t- Tridembetrieb |
Spitzenlast in kW | 5000 | 4500 | 4000 | 3000 | 3000 |
Schmelzrate in t/h | 10 | 9 | 8,6 | 6,7 | 6,5 |
Auslastung | 65 | 75 | 75 | 95 | 100 |
Flüssigeisen pro h | 6,5 | 6,75 | 6,5 | 6,3 | 6,5 |
Leistungsdichte | 250 | 225 | 400 | 600 | 750 |
Um hohe Leistungspreise durch Stromspitzen zu vermeiden, ist der Tridem-Betrieb für die Gießerei nicht nur „praktisch“ sondern auch ökonomisch vorteilhaft. Bei Schmelzbetrieb 1 ist der Leistungsbedarf um 40 % höher als bei Betrieb 5. Folglich sinken die Schmelzkosten (Leistungspreis) von 23 Dollar auf etwa 13 Dollar/t Flüssigeisen bei Gießerei 5 (Zwei-Schicht-Betrieb, Fünf-Tage -Woche). Abschließend fasst der Autor zusammen, unter welchen Bedingungen der Schmelzbetrieb 5 auch wirklich am effizientesten arbeitet:
- regelmäßige Wartungen der Schmelzöfen,
- ausreichende Leistungsbereitstellung für die Öfen,
- funktionierende, (automatisierte) Ofenabdeckungen mit integrierter, drehzahlgeregelter Absaugung,
- saubere und trockene Einsatzstoffe,
- richtige Reihenfolge bei der Gattierung und keine Beladung über der Befüllungslinie („Coillinie“),
- regelmäßige Überwachung und effiziente Zustellung des Ofens,
- Wärmerückgewinnung nutzen oder Konzepte dafür entwickeln.
Herausforderungen im Lichtbogenofen sind die hohen Staubemissionen und die höhere Lärmbelastung im Vergleich zu Induktionsöfen. Dies führt dazu, dass sich der Induktionstiegelofen zumindest in kleineren und mittleren Stahlgießereien wegen seiner Umwelt-, Arbeitsplatz- sowie auch Anlagen- und Verfahrensvorteile gegenüber dem Lichtbogenofen verstärkt durchsetzt. Studien des IfG belegen, dass in deutschen Stahlgießereien die Zahl der Standorte mit Lichtbogenöfen in den letzten zwanzig Jahren von über 20 auf 12 gesunken ist. Passend dazu berichten W. Ertl und E. Dötsch [24] über die Praxiserfahrungen beim Schmelzen im Induktionstiegelofen in einer österreichischen Gießerei für große Stahlgussteile, welcher einem Lichtbogenofen vorgezogen wurde.
Vor dem Hintergrund steigender Komplexität von Gussteilen ist neben der Simulation auch die Wahl der Speiser entscheidend. Der in der letzten Jahresübersicht vorgestellte ECO-Speiser wird kontinuierlich zwischen Gießereien und Zulieferindustrie weiterentwickelt, um die prozesssichere Speisung des Gussteils zu optimieren [25]. Trotz einer deutlich geringeren Einbringung von Energie in das Speisersystem ist es mit diesen Speisern möglich, die im Speiserhohlraum befindliche Schmelze länger flüssig zu halten.
Die (teilweise unsystematische) Pfannenwirtschaft zeichnet sich in deutschen Gießereien durch einen hohen Erdgasbedarf aus. Bei der GIFA-Sonderschau „Energieeffizienter Gießereibetrieb“ wurden gleich drei unterschiedliche Systeme anstelle „alter“ Erdgas-Luft-Brenner zur Umsetzung einer energieeffizienten Pfannenwirtschaft präsentiert (siehe [13]):
- Erdgas-Sauerstoff-Brenner,
- Erdgas-Porenbrenner,
- und eine isolierende Pfannenauskleidung in Form eines gießbaren Pulvers, die keine Pfannenvorwärmung mehr benötigt.
Zwei weitere Lösungen konnten auf der GIFA nicht gezeigt werden [26]: Speziell für Aluminiumgießereien konnte durch ein neues Tiegelsystem mit gutem thermischen Wirkungsgrad der Energiebedarf um 10 % gesenkt werden [27]. Ferner beschreibt A. Wynn [28] die Eigenschaften von isolierenden Schamottesteinen, die den Energiebedarf um bis zu 38 % reduzieren.
Die Ablufttechnik ist in Gießereien einer der zweitgrößten „Energieverbraucher“, weshalb bei Neu- und Umbauten ein individuell zugeschnittenes raumlufttechnisches Konzept einerseits die Arbeitsplatzqualität erhöht und andererseits sich auch als besonders energieeffizient erweist. Eine frequenzgesteuerte Luftrückführung in Verbindung mit Wärmerückgewinnung führt zu Energieeinsparungen, da der Heizöl- oder Erdgasbedarf für die Heizungsanlage reduziert oder sogar auf Heizungen vollständig verzichtet werden kann [29].
Literatur:
[1] Giesserei 102 (2015) Nr. 6, S. 116-123.
[2] Giesserei 101 (2014) Nr. 10, S. 80-82.
[3] Giesserei 101 (2014) Nr. 10, S. 84-87.
[4] Giesserei 101 (2014) Nr. 9, S. 98-99.
[5] www.umweltbundesamt.de/publikationen/innovative-techniquesbest-available-techniques-bat.
[6] siehe Forschungsprojekt EffSAFound in: Giesserei 102 (2015) Nr. 5, S. 120.
[7] Giesserei 102 (2015) Nr. 6, S. 219.
[8] www.ecofys.com/files/files/ecofys-fraunhoferisi-2015-stromkostender-energieintensiven-industrie.pdf.
[9] Giesserei 101 (2014) Nr. 11, S. 84-85.
[10] www.vdi-nachrichten.com/Technik-Gesellschaft/Zu-effizient-umprofitabel-zu.
[11] www.umweltbundesamt.de/sites/default/files/medien/378/publikationen/07_2014_climate_change_dt.pdf
[12] Giesserei 102 (2015) Nr. 6, S. 38-39.
[13] Giesserei 102 (2015) Nr. 9, S. 90-98.
[14] Giesserei 102 (2015) Nr. 5, S. 28-39.
[15] Giesserei 102 (2015) Nr. 6, S. 86-100.
[16] Giesserei 102 (2015) Nr. 5, S. 92-95.
[17] Giesserei 102 (2015) Nr. 3, S. 96-99.
[18] Giesserei 102 (2015) Nr. 5, S. 76-79.
[19] Giesserei 102 (2015) Nr. 2, S. 90-97.
[20] Giesserei-Rundschau 61 (2014) Nr.1/2, S. 25-31.
[21] Giesserei 102 (2015) Nr. 7, S. 74-77.
[22] Giesserei 102 (2015) Nr. 7, S. 54-59.
[23] Modern Casting (2015) Nr. 2, S. 47-49.
[24] Giesserei 102 (2015) Nr. 5, S. 20 –29.
[25] Giesserei 102 (2015) Nr. 1, S. 80-83.
[26] Giesserei 102 (2015) Nr. 2, S. 90-97.
[27] Foundry Trade Journal (2014) März, S. 48-49.
[28] Foundry Trade Journal (2014) Juni, S. 160-162.
[29] Giesserei 101 (2014) Nr. 10, S. 84-87.