Lastmanagement als Kontrollsystem für den Energieeinsatz und Lastspitzen von Induktionsöfen
Bezug zum BREF Gießerei, Ausgabe Mai 2005
In 4.2.3.1 wird auf ein möglichst effektives Induktionsschmelzen eingegangen mit der Empfehlung, die Warmhaltezeit zu minimieren. Ein Lastmanagementsystem wird dabei nicht erwähnt.
Beschreibung
In der deutschen Gießerei-Industrie sind die Strompreise zwischen den Jahren 2001 und 2012 um 40 Prozent gestiegen. Neben Energieeffizienzmaßnahmen sind daher auch Möglichkeiten zur Energiekostensenkung gefragt. Einerseits können vertragliche Gestaltungen angepasst oder Ausgleichsregelungen in Anspruch genommen, andererseits ergeben sich Potenziale durch eine effektive Leistungsbegrenzung in Gießereien.
Werden mehrere Schmelzöfen gleichzeitig betrieben, stellt die Lastspitzenbegrenzung eine Möglichkeit dar, die Energiekosten zu senken. Durch die Optimierung des Lastgangs und damit des Leistungsbezugs können Spitzenlasten frühzeitig vermieden werden. Neben der Lastspitzenbegrenzung können moderne Lastmanagement-systeme auch den spezifischen Energiebedarf reduzieren.
Die Bildung von Lastspitzen beim Strombezug beruht meist auf zufälligem und gleichzeitigem Einsatz vieler Abnehmer an elektrischer Energie. Der Energieversorger muss sich darauf einrichten, dass das belieferte Unternehmen diese Höchstmenge an elektrischer Energie (Lastspitze) dauerhaft abruft.
Gerade in einer Diskussion um die Netzauslastung durch den Ausbau von erneuerbaren Energien rückt dieser Punkt verstärkt in Diskussion. Durch Lastspitzen entstehen dem Energieversorger Bereitstellungs-kosten, die dem Abnehmer der elektrischen Energie in Rechnung gestellt werden. Mit der Reduzierung der Lastspitzen lassen sich die Energiekosten reduzieren.
Moderne Lastmanagementsysteme nehmen Schmelzöfen bei Erreichen von Lastspitzen nicht einfach vom Netz, sondern reduzieren für eine bestimmte Zeit die Leistung einzelner Schmelzöfen. Entscheidender Vorteil ist, dass kein serielles Abschalten mehr stattfindet, sondern dass alle Öfen parallel und stufenlos angepasst werden (Parallel-Difference-Power-Control).
Dies wird durch eine intelligente Prozesstechnik realisiert. Durch den Einsatz mehrerer gleichzeitig arbeitender Schmelzaggregate ergeben sich Kennlinien aus dem Schmelzverlauf. Die Kennlinie repräsentiert den Energiebezug der Schmelzaggregate in einem bestimmten Zeitraum.
Der Prozessor versucht die Leistung der einzelnen Schmelzaggregate harmonisch aufeinander abzustimmen und damit die Kennlinie, die sich aus dem Energiebedarf der einzelnen Schmelzaggregate ergibt, kontinuierlich zu verbessern. Die ermittelte optimale Energiemenge wird den Schmelzaggregaten zur Verfügung gestellt. Im Ergebnis können Energiekosten eingespart werden.
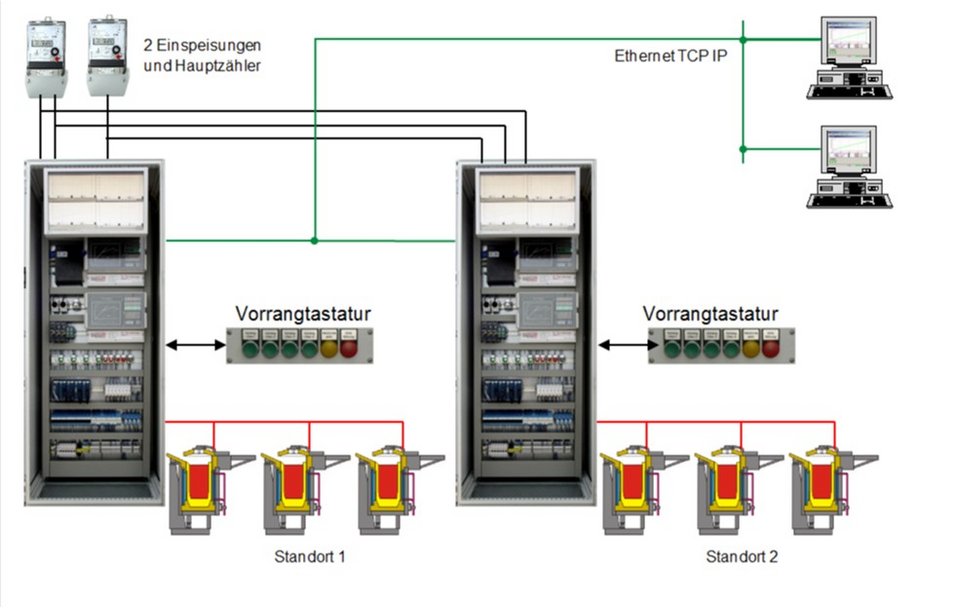
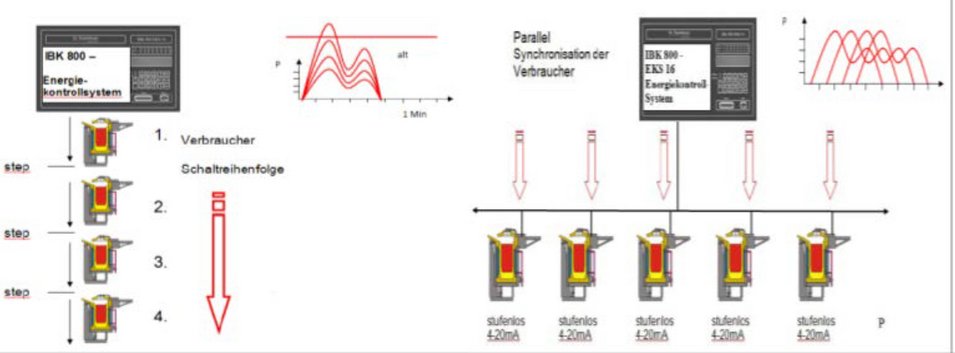
Technische Beschreibung
Die Reinhard Tweer GmbH beispielsweise ist ein Zulieferbetrieb u. a. für den Maschinen- und Fahrzeugbau. Die jährliche Produktionsmenge der Gießerei liegt bei durchschnittlich 27.000 Tonnen Stahlguss und Gusseisen mit Kugelgraphit. Im Schmelzbetrieb werden sechs Mittelfrequenzöfen eingesetzt, die sich maßgeblich auf die Energiekosten der Gießerei auswirken.
Die nachfolgende Abbildung zeigt, welcher energetische Vorteil hier mit einer Reduzierung der Lastspitzen verbunden ist:
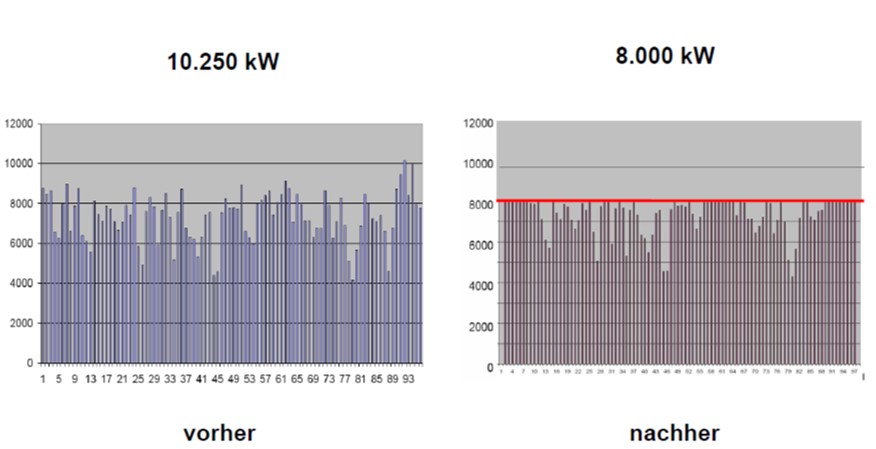
Erreichter Umweltnutzen
- Senkung des Stromverbrauchs und der Energiekosten durch Lastoptimierung
- Verminderung von CO2-Emissionen
- Verringerung des Energiebedarfs zum Schmelzen von Metallen
- Das Energieversorgungsunternehmen muss dauerhaft nicht mehr den Energiebedarf für die Deckung der Lastspitzen vorhalten
Verlagerungseffekte
Keine Verlagerungseffekte
Anwendbarkeit
In allen Gießereien, die mehrere elektrische Schmelzöfen betreiben.
Wirtschaftliche Aspekte
Die Verminderung der zu beziehenden Leistung kann anhand der Strombezugskosten, unter Berücksichtigung des Schichtbetriebes, berechnet werden.
Bei folgenden Strombezugskosten der Gießereien (Bezugsjahr 2010 und im 1-Schichtbetrieb bei 13,1 ct/kWh, im 2-Schichtbetrieb bei 12,4 ct/kWh und im 3-Schichtbetrieb bei 11,1 ct/kWh hat) sich ergeben:
Anlage | Einsparung [€/Jahr] |
Walzengießerei Coswig | 160.000 |
Klaus Kuhn Edelstahl - Radevormwald | 120.000 |
Jürgens Gießerei Emsdetten | 60.000 |
Flender Siemens - Chemnitz | 80.000 |
Affilips V.N. – Tienen/Belgien | 100.000 |
Gießerei und Glasformenbau - Radeberg | 80.000 |
KM Europa Metal AG - Osnabrück | 90.000 |
Intermet/Sakthi - Neunkirchen | 180.000 |
Eisenwerk Hasenclever & Sohn GmbH - Battenberg | 130.000 |
Meuselwitzer Guss Eisengießerei GmbH | 80.000 |
Technoguss Tangerhütte GmbH | 50.000 |
Gründe für die Anwendung dieser Technik
- Erreichtes Einsparpotential: 5 % bis 23 % der bisherigen Energiekosten für Strom
- Verkürzte Warmhaltezeiten durch Just-in-time-Schmelzen
- Die dauerhafte Absenkung kann als ein gutes Argument für die Verhandlung der Stromlieferverträge gesehen werden
- Darüber hinaus kann das liefernde Energie-versorgungsunternehmen den Strombedarf sicher planen
- Auch ermöglicht das Verfahren zu jedem gewünschten Zeitraum eine transparente Übersicht über den Stromverbrauch jedes angeschlossenen Schmelzofens
Referenzanlagen
Siehe wirtschaftliche Aspekte
Informationsquellen
- BDG-Schrift „Energieeffizienter Gießereibetrieb“: GIFA 2011-Sonderschau
- Zak, B.,: Industrial Heating, The International Journal of Thermal Technology, Cut Costs and Stay Competitive with Advanced Energy Management, June 2011
- Dr. Tanneberger GmbH, Abruf März 2013 Vortrag bei BDG-VDMA-Tagung 2010 in Frankfurt
- Alpiq Suisse SA Homepage Donnerbauer, R. (2006): Kostenfaktor Energie. In: Giesserei, Nr. 10, S. 49-51
- Donnerbauer, R. (2007): Energieeinsatz effizient optimiert. In: Giesserei, Nr. 6, S. 274-278
- Donnerbauer, R. (2012): Stromkosten senken im Gießereibetrieb. In: Giesserei, Nr. 05, S. 51-54