Energieverbrauch in Großgießereien erfolgreich steuern
Von Caren Möhrke, Düsseldorf
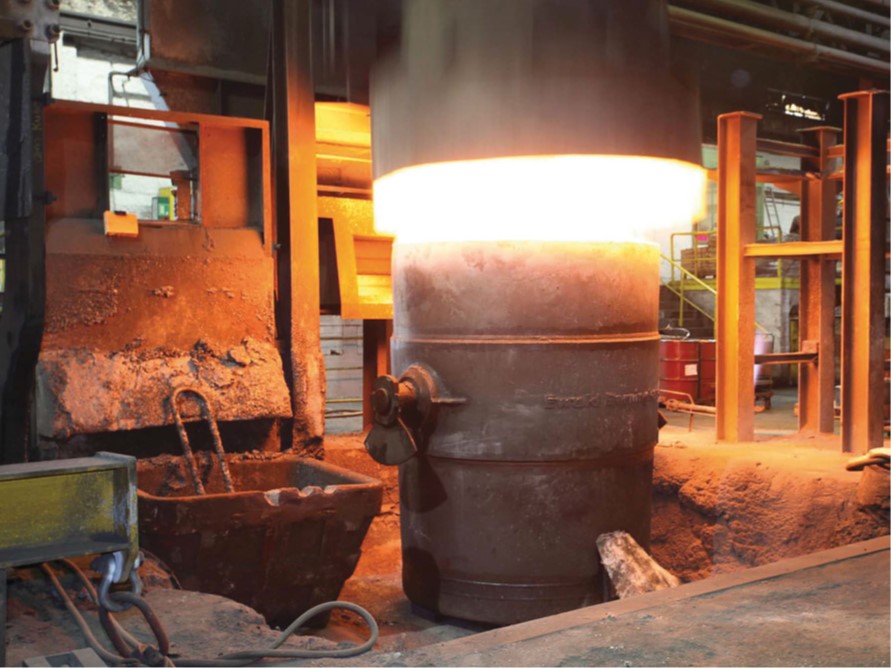
Magnesiumbehandlung in der Friedrich Wilhelms-Hütte mit Tauchpfanne und Tauchglocke unter effizienter Nutzung der Pfannenrestwärme.
Erschienen in GIESSEREI 03/2013
Angesichts der anhaltenden Energiepreisdiskussion und den Herausforderungen im Zusammenhang mit der Energiewende müssen gerade energieintensive Produktionsbetriebe ihre Verbräuche optimieren. Das Bundesministerium für Umwelt, Naturschutz und Reaktorsicherheit (BMU) hat daher unter dem Motto „Best for Production“ bei der Friedrich Wilhelms-Hütte in Mülheim an der Ruhr ein Projekt mit Modellcharakter für eine energieoptimale Produktion in Großgießereien gefördert.
Sollen Abläufe und Prozesse in Produktionsbetrieben verbessert und Potentiale in der Lieferkette effizienter genutzt werden, so stehen üblicherweise Faktoren wie Anlagenkapazität, Materialverfügbarkeit und personelle Ressourcen im Fokus. In energieintensiven Betrieben, wie beispielsweise Gießereien, reicht dies jedoch nicht aus. Hier ist eine intelligente Steuerung des hohen Energieverbrauchs eine weitere, wenn nicht die entscheidende Einflussgröße, um bei Schonung der Ressourcen die Produktivität zu steigern und damit mehr Wettbewerbsfähigkeit zu gewinnen.
Erkenntnisse und Ergebnisse
Diese Erkenntnis war grundlegend für das Projekt „Best for Production“, welches die Friedrich Wilhelms-Hütte Eisenguss GmbH (FWH) im Mai 2011 startete und das vom Bundesumweltministerium mit rund 290 000 Euro aus dem Umweltinnovationsprogramm gefördert wurde. In Zusammenarbeit mit dem FWH-Partner PSI Metals aus Würselen, einem Anbieter von Soft warelösungen für das Produktionsmanagement in der Metallindustrie, wurde erstmals ein IT-basiertes Fertigungsleitsystem (FLS) implementiert, das als relevantes Zielkriterium auch und vor allem die Energieeffizienz definiert. „Wir gehen davon aus, dass wir die Erwartungen bei der Optimierung der Energieeffizienz sogar bertreffen“, so Dr. Georg Stierle, kaufmännischer Geschäftsführer der FWH. Das angestrebte Einsparvolumen lag bei 1,5 Mio. KWh elektrischem Strom pro Jahr, was 850 t weniger CO2-Ausstoß bedeutet. Hinzu kommen 60 000 m3 Gas pro Jahr „Auch die geplante Produktivitätssteigerung von 10 % werden wir wohl übertreffen.“ (Bild 1)
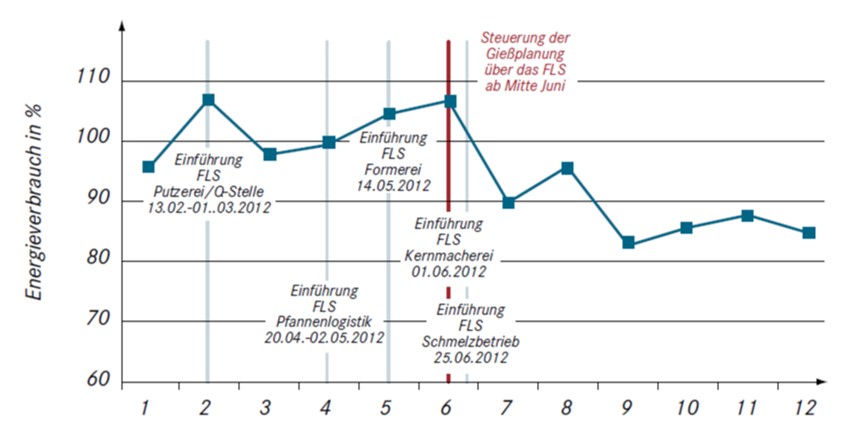
Seit Juli 2012 arbeitet die Gießerei mit allen Betrieben auf der Basis der innovativen Fertigungssteuerung von PSI. Das Projekt dürfte auch für andere Großgießereien von großem Interesse sein, denn das Vorhaben wurde nach den Prinzipien der sogenannten Green IT durchgeführt, bei der mithilfe von Informationstechnologien Ressoucen und CO2 eingespart werden. Wie das Beispiel FWH zeigt, kann Green IT die Energiebilanz in Gießereien verbessern und zu höherer Produktivität und kürzeren Durchlaufzeiten führen. Zusätzliche Effekte können sich aus der Optimierung der Rohstoff-/Materialeffizienz, bei Wartung und Reparaturen sowie durch die Flexibilisierung des Energieeinkaufs ergeben.
Eine starke Zusammenarbeit
Die in Mülheim an der Ruhr ansässige FWH ist eine traditionsreiche Eisengroßgießerei, die Produkte im Gewichtsbereich von 8 bis 160 t fertigt. Fortschritt wird hier groß geschrieben, so kommen beispielsweise Maschinenträger und Rotornaben der 5-MWKlasse für Offshore-Windkraftanlagen von FWH. Wichtigster Partner bei dem Projekt war PSI Metals. Die Spezialisten des Unternehmens hatten im Vorfeld auf der Grundlage einer Ist-Analyse ein Konzept für ein Fertigungsleitsystem und die Betriebsdatenerfassung erstellt, das sie nun innerhalb von 13 Monaten in der FWH erfolgreich implementierten. Zudem stand das Institut für Fabrikbetrieb und -automatisierung der Fraun hofer Gesellschaft in Magdeburg (FFI) für Fragen bei der Energieoptimierung im Schmelzbetrieb als Berater zur Verfügung. Das Projekt führt erstmals den Faktor der Energieeffizienz als relevante Steuerungsgröße in ein Fertigungsleitsystem ein – ein wesentlicher Unterschied und Vorteil im Vergleich mit konventionellen Prozessoptimierungsverfahren.
Komplexität beherrschen
In Großgießereien sind Prozesse selten zentral organisiert, sondern werden in altbewährter Manier als einzelne, voneinander isolierte Arbeitsschritte verstanden, die hauptsächlich durch das Know-how der Meister bzw. einzelner Abteilungen gesteuert werden. Ein weiteres typisches Pro blem sind Engpässe in der Verfügbarkeit von Kränen und Gießgruben. Die Folge: Durch äußere wie innere Einflüsse geraten Abläufe leicht ins Stocken, die Produktionskette ist nur selten transparent und es ergeben sich oft Wartezeiten und Leerläufe, die die Ressourcen massiv strapazieren. Optimale Energieeffizienz ist kaum möglich. Ein Gegenentwurf zu diesem Szenario: Ein Fertigungsleitsystem, das als eine wesentliche Steuerungsgröße den Energieverbrauch integriert.
PSI erweiterte ihre Standardmodule und schuf entsprechende Schnittstellen zu den Messsystemen des Energieverbrauches. Das Konzept erwies sich als sinnvolle und richtige Strategie: „Schon während der Umsetzung des Projektes zeigten uns die Zwischenergebnisse, dass wir auf dem richtigen Weg sind“, so Reiner Eschen, technischer Geschäftsführer der FWH. „Die bessere Synchronisation der Prozesse wirkt sich unmittelbar auf die Energieeffizienz und die Produktivität aus.“ Mithilfe des FLS ist nun eine effiziente Planung und Steuerung der Wochengießpläne anhand des Energieverbrauchs möglich: Alle vorgelagerten Prozesse (Formerei, Kernmacherei) sowie alle nachgelagerten Arbeitsschritte (Ausleeren, Putzen, Bearbeiten, Prüfen, Versenden) können auf diese Pläne ausgerichtet und entsprechend koordiniert werden (Bild 2).
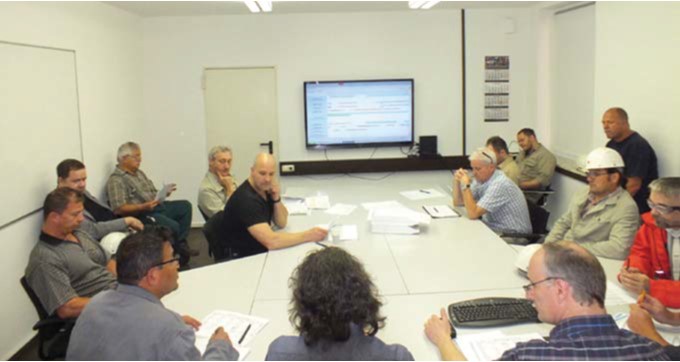
Transparenz schafft Grundlage für Geschäftsstrategie
„Unser Ziel war es, hinsichtlich der Grobund der Feinplanung eine zentral geplante und marktgesteuerte Fließfertigung einzurichten, die schnell und flexibel auf veränderte Bedingungen reagiert und sich vor allem an den Energieverbrauchsvorgaben orientiert“, so Wolfgang Tobias, Leiter des Projektes. „Dies war ein mehrstufiger Prozess und wir mussten schrittweise und Abteilung für Abteilung vorgehen, denn die Etablierung des neuen Systems erfolgte unter Aufrechterhaltung der Fertigung nach alter Methode.“
Um exakter planen zu können, wurde der Bereich Fertigungsplanung und -steuerung gegründet. So ist künftig eine zentrale, transparente und präzise Abstimmung mit einem Vorlauf von 24 h möglich. Wesentlich für den Steuerungsprozess ist die Erfassung der Betriebsdaten, die über die Rückmeldung an den neuen Terminals in der Produktion erfolgt: Den Mitarbeitern werden nicht nur das tägliche Arbeitspensum, sondern auch die Reihenfolge der Arbeitsvorgänge aufgezeigt. Die für die jeweiligen Arbeitsschritte erforderlichen Zeiten, aber auch Störungen werden von dem FLS für die Folgeplanung ausgewertet, eventuelle Engpässe oder Konflikte frühzeitig angezeigt – wie bei einem Frühwarnsystem. Aufgrund der ständigen Erfassung der Ist- Daten erfolgt eine permanente Auswertung dieser Daten durch das System. Daten für die Nachkalkulation sind jederzeit verfügbar. Auf Grundlage dieser Methodik sind fortlaufend Verbesserungen von Arbeitsabläufen und Produkten und damit eine Optimierung der Geschäftsstrategie möglich.
Schritt für Schritt zur neuen Struktur
Angesichts der Komplexität der Systemumstellung hat sich ein schrittweises Vorgehen bewährt. Interessanterweise wurde zunächst die Putzerei umstrukturiert, also eine Abteilung am Ende der Fertigung. Da es dort besonders vielfältige Arbeitsschritte gibt und zudem die Kran- und Platzverfügbarkeit eine große Rolle spielt, waren gleich zu Beginn eine konsequente Neugestaltung der Abläufe und eine räumliche Neuordnung wichtig.
Die Systemumstellung in der Putzerei diente als Modell im Gesamtprojekt. Sie lieferte Erfahrungswerte und Erkenntnisse, von denen in der Folge andere Abteilungen profitierten.
„Der Gesamtprozess war mit einem hohen Arbeitsaufwand verbunden und hat uns allen viel abverlangt“, gesteht Tobias ein. Die gesamte Fertigungskette war von einer Neuorganisation betroffen, eingespielte betriebsinterne Strukturen wurden verändert (Bild 3). Die reibungslose Implementierung kann durch Schulungen unterstützt werden. PSI Metals führte deshalb entsprechende Kurse für Abteilungsleiter, Meister, Vorarbeiter und Mitarbeiter durch. Hierbei mussten bei der Belegschaft Widerstände gegen die Umstellung auf einen computergesteuerten Durchlauf sowie Berührungsängste mit der neuen Technik überwunden werden.
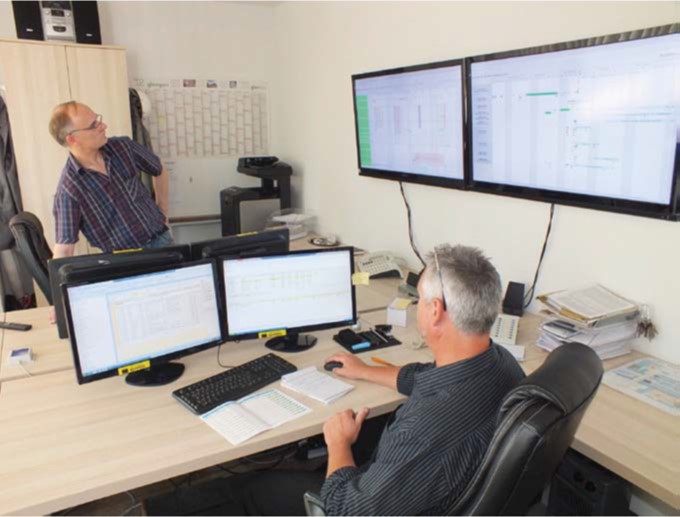
Nebenwirkungen und Chancen
Eine wesentliche Verbesserung wird konsequenterweise auch bei den Durchlaufzeiten einzelner Produkte erzielt. Dies wurde bereits in der Erprobungs- und Testphase des neuen Systems deutlich: Ein gegossener Maschinenträger für Windkraftanlagen wurde zunächst gemäß der alten Vorgehensweise geplant und dann auf das neue System umgestellt. Die Durchlaufzeit konnte um 20 % verbessert werden; theoretisch hatte man hier nur mit 10 % Optimierung gerechnet. Mit dem transparenten Überblick über das Arbeitspensum und die hierfür erforderliche Zeit schafft das System auch Vorteile für die Mitarbeiter: Sie können sich jetzt besser auf die Arbeit einstellen und haben weniger Extraschichten am Wochenende.
Das „Best for Production“-Projekt der FWH kann auch für andere Großgießereibetriebe Modellcharakter haben. Denn intelligente Green IT ermöglicht eine ressourcenschonende Produktion und eröffnet der Branche die Chance, ganz neu über die Vernetzung im Sinne sogenannter Smart Grids nachzudenken. In Smart Grids können Energieströme dank moderner Informations- und Telekommunikationstechnik sowie Mess-, Steuer- und Regeltechnik sehr viel differenzierter als bisher gesteuert werden. „Ein zukunftsweisendes Projekt“, meint Dr. Stierle und fügt hinzu: „Im wahrsten Sinne des Wortes Best for Production.“
Dr. Caren Möhrke, Marketing Services, Düsseldorf