Ressourceneffiziente Gießtechniken beim Zinkdruckgießen
Von Sabina Grund, Düsseldorf
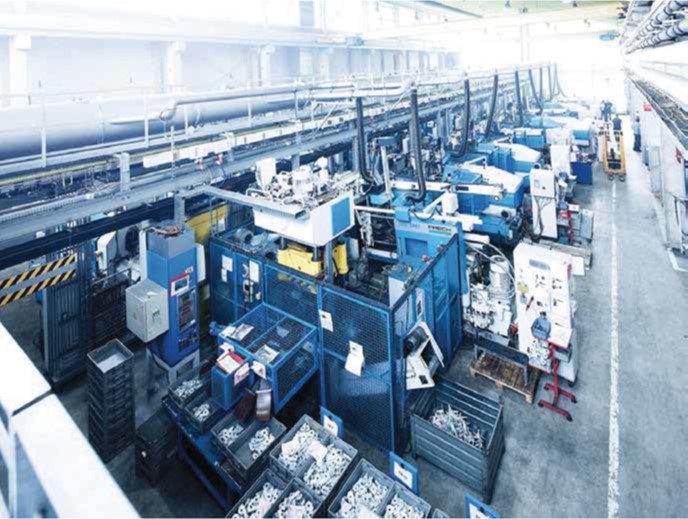
Zinkdruckgießerei der Adolf Föhl GmbH & Co. KG.
Erschienen in GIESSEREI 09/2016
Ressourcen- und energieeffizient zu arbeiten, ist für Gießereien seit jeher eine Selbstverständlichkeit. Sowohl Ressourcen als auch Energie sind immer auch mit Kosten verbunden, sodass es vor allem wirtschaftliche Gründe dafür gibt, weder das eine noch das andere unbedacht oder gar verschwenderisch einzusetzen. Wenn aber heute verstärkt die Frage gestellt wird, ob es nicht noch effizienter geht, ob nicht auch lange bewährte Technologien doch noch Raum für weitere Optimierungen bieten oder ob es möglich ist, mit ganz neuen Technologien zu arbeiten, so liegt das an der Erkenntnis, dass in unserer globalen und vernetzten Welt ein „sehr gut“ noch immer nicht gut genug ist. Die wachsende Weltbevölkerung, der steigende Lebensstandard in den aufstrebenden Regionen der Erde und die Notwendigkeit, nicht nur regional, sondern international wettbewerbsfähige Angebote vorlegen zu können, zwingen uns dazu, vieles neu zu denken und technische Herausforderungen zu meistern. Am Beispiel des angussarmen und angussfreien Zinkdruckgusses lässt sich zeigen, wie so eine kleine technische Revolution in der Umsetzung aussehen kann.
Zinkdruckguss
Bauteile aus Zinkdruckguss sind Hightech-Produkte, die für unterschiedlichste Einsatzzwecke in vielen Bereichen des täglichen Lebens eingesetzt werden, z. B. im Automobil-, Maschinen- und Apparatebau, in der Elektrotechnik und Elektronik sowie im Bauwesen. In der Praxis haben sich vor allem die Legierungen ZL 0400, ZL 0410 und ZL 0430 durchgesetzt. Ihre Basis bildet Feinzink mit einer Reinheit von 99,995 % Zink. Aluminium, Kupfer und Magnesium sind weitere Bestandteile, die erheblich das Eigenschaftsprofil der Legierungen beeinflussen. Gleichzeitig reduziert Aluminium bei Temperaturen unterhalb von 450 °C die Reaktivität eisenhaltiger Materialien im Kontakt mit der flüssigen Schmelze drastisch. Dadurch sind alle Zink-Aluminium-Legierungen im schnellen und hochproduktiven Warmkammerdruckgießverfahren verarbeitbar. Im Druckgießverfahren werden Gussteile aus Aluminium-, Magnesium- und Zinklegierungen hergestellt, die in großen Stückzahlen benötigt werden. Bei diesem Gießverfahren wird die Schmelze nicht direkt in den Formhohlraum gegossen, sondern zunächst in die Gießkammer einer Druckgießmaschine gefüllt und von dort mittels Kolben über einen oder mehrere Kanäle in den Formhohlraum gepresst [5]. Das Warmkammerverfahren hat den Vorteil, dass eine Oxidation der Schmelze verhindert wird.
Zinkdruckguss zeichnet sich in der Verarbeitung – bedingt durch die niedrige Schmelztemperatur (380 – 390 °C) – durch sehr kurze Zykluszeiten, sehr lange Formstandzeiten und somit durch eine hohe Wirtschaftlichkeit aus. Seit über 60 Jahren wird Zink in Warmkammerdruckgießmaschinen verarbeitet. Dabei wurde das Verfahren stets weiterentwickelt. Heute werden für das Zinkdruckgießen Maschinen von 20 bis 500 t hydraulischer Schließkraft angeboten. Moderne Gießmaschinen arbeiten mit einem hohen Grad an Automatisierung durch Echtzeitregelung und Visualisierung sowie vernetzt mit Peripheriegeräten. Für das Energiemanagement stehen modernste Methoden und Geräte zur Verfügung.
Eine neue Gießanlage bietet heute ganz nach Kundenwunsch gute Voraussetzungen dafür, auf dem neuesten Stand der Technik höchste Qualitäten zu gießen, aber ganz im Sinne einer Kreislaufwirtschaft, wie sie sich die EU-Kommission vorstellt [1], ist es durchaus auch eine Option, vorhandene Anlagen zu modernisieren und nachzurüsten. Welche Lösung sinnvoller ist, ist dann immer eine Einzelfallbetrachtung und eines gilt nach wie vor: Qualitativ hochwertiger Zinkdruckguss setzt Fachwissen und Erfahrung voraus, das die beste Maschine nicht ersetzen kann.
Der Anguss
Beim Warmkammerdruckgießverfahren wird die Schmelze über einen oder mehrere Kanäle in die Kavitäten, d. h. in den aus Matrize und Kern gebildeten Hohlraum gefüllt. Bei der gleichzeitigen Herstellung mehrerer Gussteile muss das Kanal- bzw. Angusssystem so gestaltet sein, dass die Formteile gleichzeitig und gleichmäßig mit einer Schmelze gleichen Drucks und gleicher Temperatur befüllt werden. Dies führt zu einem oftmals komplexen Angusssystem, das nach dem Erkalten des Metalls vom Gussteil abgetrennt wird. Der Angussanteil kann bis zu 100 % des Teilegewichts ausmachen und wird sortenrein als Neuschrott wieder eingeschmolzen. Das Recycling des Angusses (Neuschrott) ist zwar möglich und üblich, erfordert aber Energie und Arbeitsaufwand. Zudem werden Materialverluste durch Abbrand in Kauf genommen [2].
Um den Energieaufwand für das wiederholte Aufschmelzen des Angussmaterials und die zur Kreislaufführung erforderlichen Arbeitsschritte sowie den damit verbundenen Zeitaufwand zu reduzieren, wurden inzwischen Verfahren entwickelt, die mit minimalen Angüssen oder sogar ganz ohne diese auskommen. Auch wenn es bisher noch nicht möglich ist, alle Zinkdruckgussteile ohne Anguss herzustellen, so sind doch mittlerweile mehrere Techniken mit den ersten Gussteilen in der Serienproduktion im Einsatz [6, 8, 9].
Angussarmer Zinkdruckguss
Am Beispiel einer Gehäuseklappe, die als Abdeckung für eine Kommunikationseinheit verwendet wird, können die Einsparpotenziale des Zinkdruckgusses unter Verwendung eines Heißkanalsystems verdeutlicht werden. Das in diesem Fall verwendete Frech Gating System (FGS) besteht aus temperaturgeregelten Verteilerelementen in der Druckgießform, die durch eine intelligente Verknüpfung mit der Prozess- und Ablaufsteuerung in der Druckgießmaschine verbunden ist [6, 7]. Durch die eingesparten Gießläufe entstehen mehr freie Sprengfläche und Gießvolumen. Dadurch passen deutlich mehr Kavitäten auf die gleiche Maschinengröße. Alternativ kann eine kleinere Gießmaschine zum Einsatz kommen. Im Beispiel der Gehäuseklappe wurde bei der Umstellung von einer Vierfachform mit konventionellem Angusssystem auf eine Sechsfachform mit Heißkanaltechnik das Schussgewicht nahezu gleichgehalten. Das Kreislaufgewicht wurde durch den Einsatz der neuen Technik um 66 % reduziert. Gleichzeitig wurde die Taktzeit von 1,6 auf 0,9 s pro Bauteil und damit um 47 % erheblich gesenkt, da der konventionelle Verteiler nicht gefüllt und abgekühlt werden muss, bevor die Form geöffnet wird. Auf den Einsatz von Überlaufbohnen konnte in diesem Fall verzichtet werden. Auf diese Weise wurde die Energieeffizienz deutlich gesteigert. In Summe wurde bei einem Bedarf von 1 Mio. Bauteilen pro Jahr eine Energieeinsparung von fast 20 000 kWh erzielt und es werden rund 35 000 kg CO2 eingespart, was der Laufleistung eines Pkws der mittleren Oberklasse von 297 000 km entspricht. In einem nächsten Entwicklungsschritt ist es jetzt gelungen, zwei Angussverteiler in eine Form einzubringen. Denkbar ist es, dadurch zwei Formen in einer Form unterzubringen (Bild 1).
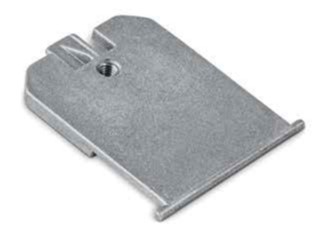
Bild 1: Gehäuseklappe: Durch den serienmäßigen Einsatz eines Heißkanalsystems (FGS) wurden erhebliche Energieeinsparungen realisiert sowie die Taktzeit nahezu halbiert und in Summe die Wirtschaftlichkeit des Verfahrens deutlich gesteigert.
Durch den Einsatz der Heißkanaltechnik kann so die Wirtschaftlichkeit des Zinkdruckgießverfahrens gesteigert werden. Es wird wettbewerbsfähiger und neue Einsatzbereiche können erschlossen werden. Welche Gussstücke sich zur Umsetzung beim angussarmen Zinkdruckgießen eignen, hängt von mehreren Faktoren ab.
Angussfreier Zinkdruckguss
Eine Weiterentwicklung zum angusslosen Gießen wird heute durch die, von der Ferro facta GmbH, Allendorf, zusammen mit der Adolf Föhl GmbH & Co. KG, Rudersberg, entwickelte Heißkanaldüse umgesetzt. Dabei wird die Schmelze durch die für das Zinkdruckgießen neu entwickelte Heißkanaldüse direkt auf das Teil eingespeist [8]. So können Zinkdruckgussteile ganz ohne Verteiler gegossen werden. Durch den Wegfall des kompletten Gießlaufs wird die Porosität des Bauteils weiter reduziert. Trotz geringer Wandstärken von 0,9 mm wird ein sehr geringer Porenanteil von nur ca. 2,3 % erzielt. Außerdem können durch den Einsatz der Heißkanaldüse komplexe Geometrien gegossen werden, die durch konventionelle Anbindungen bisher nicht herstellbar waren. Eine Mehrfachauslegung wird durch die Verwendung von einer Heißkanaldüse für jedes einzelne Bauteil ermöglicht. Zudem kann durch die Verwendung von zwei oder mehr Düsen für ein Bauteil mehr Material direkt in das Werkzeug eingebracht werden. Hierdurch erreicht man ein gleichmäßiges Abkühlverhalten des Bauteils und vermeidet Schwindungslunker und Spannungen.
Die Positionierung der Heißkanaldüse auf dem Bauteil erlaubt eine punktuelle Einspeisung des Materials. Dadurch ergibt sich ähnlich wie beim Punktanguss beim Kunststoffspritzgießen eine Vereinfachung, sodass Fließwege und Distanzen des Materials im Werkzeug gleichmäßig und kurz gehalten werden können. Entsprechend sind runde Bauteile prädestiniert, da keine Abflachung für einen etwaigen Anschnitt des Angussverteilersystems benötigt wird und darüber hinaus die Distanzen für den Materialweg im Werkzeug (nahe dem Mittelpunkt des Bauteils) verkürzt werden. Der Materialweg im Werkzeug entspricht dann nicht dem Durchmesser des Bauteils, sondern dem Radius.
Ist die optimale Angussposition gefunden, so ergeben sich weitere Vorteile durch die Reduktion der Sprengfläche der benötigten Schließkraft. Durch den Wegfall des Angussverteilersystems kann der entstehende Platz für zusätzliche Kavitäten genutzt werden. Zudem ergibt sich die Möglichkeit, bei gleicher Auslegung auf die nächstkleinere Maschine mit geringerer Schließkraft und kürzeren Zyklusgeschwindigkeiten zu wechseln (Bild 2).
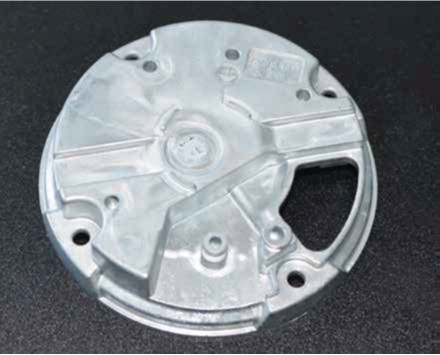
Bild 2: Flansch als Motorabdeckung zur effizienten Gestaltung des Luftstroms, angussfrei gegossen mit neu entwickelter Heißkanaldüse für das Zinkdruckgießen.
Dünnwand- und Schaumgießen
Bereits länger am Markt sind Entwicklungen, die auf die Reduzierung des Gussteilgewichts unter Beibehaltung mechanischer oder optischer Eigenschaften abzielen und so zur Steigerung der Ressourceneffizienz beim Zinkdruckgießen beitragen. bzw. mit denen das Zinkdruckgießen zur Ressourceneffizienz von Autos beiträgt.
Ausgehend von den bewährten Zinkdruckgusslegierungen gibt es heute Weiterentwicklungen der Legierungen und des Gießverfahrens. Die Reduktion des Gussteilgewichts ohne eine wesentliche Veränderung der Werkstoffeigenschaften ist dabei vor allem für die Automobilindustrie von besonderem Interesse. Grundsätzlich werden dabei zwei Wege beschritten:
- Beim Gießen von Zinkschaum im Zinkdruckgießverfahren kann eine Material- und damit auch eine Gewichtsersparnis von über 50 % erzielt werden. Während das Gussteilinnere gewollte Poren enthält, weist das Teil außen eine geschlossene, polier- und galvanisierbare Oberfläche auf [3].
- Durch die Anpassungen der Legierungszusammensetzung unter anderem durch die Verwendung kornfeinender Elemente wurde das Fließ- und Formfüllvermögen so optimiert, dass insbesondere bei sehr dünnwandigen Bauteilen (serienmäßig bis 0,3 mm) oder hohen Oberflächenansprüchen höchste Qualitätsanforderungen verwirklicht werden können [4].
Fazit
Zinkdruckguss hat sich seit Jahrzehnten in vielen Anwendungsfeldern etabliert. Bedingt durch die niedrige Schmelztemperatur und die damit verbundenen sehr kurzen Zykluszeiten bei gleichzeitig langen Formstandzeiten weist das Verfahren eine gute Wirtschaftlichkeit auf. Gute mechanische Werkstoffkennwerte, eine hohe Oberflächenqualität und der endkonturnahe Guss runden das positive Bild ab. Weiterentwicklungen der bewährten Legierungen haben das Dünnwandgießen in Zink heute salonfähig gemacht, sodass die Branche bei gleicher oder sogar steigender Tonnage eine überproportional gestiegene Anzahl an Gussteilen herstellt.
Die jetzt zur Serienreife gebrachten Entwicklungen für das Zinkdruckgießen unter Einsatz von Heißkanal- und Heißdüsensystemen haben die Energieeffizienz des Verfahrens sowie dessen Wirtschaftlichkeit nochmals deutlich gesteigert. Zinkdruckguss wird so noch wettbewerbsfähiger. Neue Einsatzbereiche können erschlossen werden.
Literatur
[1] www.foehl.de/de/techno logien #section-119, abgerufen am 03.08.2016, Adolf Föhl GmbH + Co KG. Techno logien, Rudersberg
[2] www.google.com/patents/EP1201335A1?cl=de, abgerufen am 03.08.2016, Oskar Frech GmbH & Co., Schorndorf
[3] Seiler, R.: Zincopor - galvanisierbarer Zinkschaum. Oberflächentage 2013, Dresden.
[4] IZA, I. Z. (2013). Ultra thin zinc die casting alloys.
[5] www.kug.bdguss.de/giessverfahren_inhalte/druckguss, abgerufen am 03.08.2016, Konstruieren und Gießen, Bundesverband der Deutschen Gießerei-Industrie, Düsseldorf.
[6] www.frech.com/fileadmin/content/Documents/Prospekte/ProspektFGS.pdf, abgerufen am 03.08 2016, Oskar Frech GmbH & Co. KG, Schorndorf. [7] 6. Zinkdruckgusswettbewerb: Preisträger ausgezeichnet. Pressemitteilung Initiative Zink, Düsseldorf, 2016.
[8] www.foehl.de/de/techno logien#section-119, abgerufen am 03.08.2016, Adolf Föhl GmbH + Co KG. Technologien, Rudersberg
[9] Seiler, R.: Sprue reduced zinc-high pressure die casting with hotcast: a field report. International Zinc Die Casting Conference, Brescia, Italy, 2016.