Energieeffiziente Gattierung und Einfluss der Chargenzusammensetzung auf die Energieeffizienz
Größter Energiebedarf entsteht bei Gießereien im Fertigungsbereich „Schmelzbetrieb“, wobei der Energieverbrauch bei unterschiedlichen Metallen vom Typ des verwendeten Ofens abhängt.
In der Gießerei hat der Schmelzbetrieb Vorgaben zu erfüllen, damit eine optimale Gussteilproduktion gewährleistet wird. Das Gießmetall soll mit einer definierten chemischen Zusammensetzung für den Guss bereitgestellt werden, da diese Zusammensetzung eine entscheidende Voraussetzung für die Erzielung optimaler Eigenschaften im Gussstück sind. Entscheidend für die Schmelze ist ein hoher Gleichmäßigkeitsgrad, um die geforderten hohen Werkstoffanforderungen zu erfüllen. Nebenbedingungen sind dabei, dass diese Bereitstellung auch energieeffizient und gleichzeitig kostengünstig geschieht.
Vor allem durch Automatisierung hat sich die Gießerei seit dem Jahr 1985 deutlich weiterentwickelt, was zu einer Erhöhung der Energieeffizienz von 740 kWh auf 520 kWh je Tonne Flüssigeisen geführt hat. Gleichzeitig werden dadurch auch Emissionen im Allgemeinen reduziert und vorhandene Ressourcen optimal genutzt. Konkret manifestiert sich die Automatisierung von modernen Schmelzbetrieben z. B. im Bereich der Gattierungs- und Chargiervorgänge sowie im Schmelzbereich. Ein übergeordnetes Prozessleitsystem überwacht dabei den gesamten Schmelzprozess und sorgt dafür, dass Lüfter und Absaugen betriebsoptimiert arbeiten. Jedoch bleibt die IT-Unterstützung des Schmelzprozesses im Gegensatz zu anderen Fertigungsbereichen noch weit hinter den Möglichkeiten zurück.
Der Vorteil einer durchgängigen Materialwirtschaft ist, dass alle Einsatzmaterialien sowie Schrotte und Kreislaufmaterialien erfasst werden und chargenweise zugeordnet werden können. Die Parameter der Einsatzmaterialien, z. B. Kohlenstoffgehalt beim Koks, können gespeichert werden. Ferner wird für bestimmte Gattierungen ein kostengünstigster Materialeinsatz gewählt. Dabei kann eine zielgerichtete Gattierung und Nachgattierung sowohl den Materialeinsatz als auch den Energiebedarf durch Verkürzung der Schmelzzeiten und Steigerung der der Schmelzkapazität optimieren. Gleichzeitig werden im Zusammenspiel mit einem Lastmanagementsystem Lastspitzen und damit zu hohe Arbeitspreise gezielt vermieden.
Typische Einflussfaktoren auf die Einsatzstoffe bei Kupolöfen sind beispielsweise:
- Qualität, Gewicht und Zugabemengen des Schrottes
- Qualität, Feuchtigkeit, Zugabemengen und Feinheit des Kokses
- Verunreinigungen im Kalk
- Qualität des Roheisens
- Qualität des internen und externen Kreislaufmaterials
- Verunreinigungen beim Kiesel
- Qualität des Aufkohlungsmittels oder Anthrazits
Entscheidend für den Energiebedarf einer Gusseisenschmelze sind die Einsatzstoffe. Für das Erschmelzen von Gusseisen mit Kugelgraphit fällt unter optimalen Bedingungen ein Energiebedarf von 369 kWh/t an, wohingegen sich der Energiebedarf durch Einsatz von Stahlschrott, Substitution von SiC anstatt FeSi und Einsatz von Kreislaufmaterial auf 392 kWh/t erhöht.
Untersuchungen ergaben, dass Gusseisenschmelzen bei 1480 °C einen Eintrag von ungefähr 385 kWh/t benötigen, was bei einem optimalen Ofenwirkungsgrad von 75 Prozent 513 kWh/h bedeutet.
In der Praxis sollte sich aufgrund längerer Warmhaltezeiten und weitere Verzögerungen in den Prozessschritten zum Abgießen ein Energiebedarf von etwa 600 kWh/t zeigen. Praxiswerte in der Gießerei-Industrie zeigen deutlich die Vorteile von Induktionsöfen mit größerem Ofenfassungsvermögen:#
So braucht in der Praxis 2t/3t/4t 550 kWh/590 kWh/680 kWh pro Tonne Flüssigeisen. Einsatzstoffe in Induktionsöfen sind Stahlschrott, Roheisen, Gussbruch, Späne und Kreislaufmaterial. Zusätzlich als Zuschlagsstoffe werden Siliziumcarbid, Kohle, Ferrosilizium und andere Ferrolegierungen wie Ferromangan und Ferrochrom eingesetzt.
Um die Schmelzequalität hoch zu halten, sollten die Einsatzstoffe möglichst wasser-, öl- und rostfrei sowie frei von schädlichen Begleitelementen und nichtmetallischen Beschichtungen sein.
Mit in die Betrachtung aufgenommen werden muss auch die Qualität der Einsatzmaterialien, um einen Anstieg des Abbrandes und der Schlackenmenge zu verhindern. Die Kenntnis über die genaue Chargenzusammensetzung auf Basis von Analysenwerten der Einsatzstoffe, das Wissen um die genaue Dosierung der Einsatzstoffe und der entsprechenden Legierungszuschläge, einschließlich der Korrekturen zwischen Soll- und Ist-Gewicht, sind Grundvoraussetzung für das Vermeiden von Zeit- und Energieverschwendung im Schmelzbetrieb.
Das Chargieren von trockenem und sauberem Einsatzmaterial macht sich im Energiebedarf bemerkbar. Für das Verschlacken von Sand, der an nicht gestrahltem Kreislaufmaterial haftet, wird eine spezifische Energie von ca. 500 kWh/t verbraucht. Das entspricht in etwa der Energie, die zum Schmelzen von Eisen benötigt wird. Auch verrostete Einsatzmaterialien sollten vermieden werden, denn der Einsatz deren Einsatz erhöht den Energiebedarf. Insgesamt erfordert die Verwendung von verrostetem Schrott die zwei bis dreifache Zeit zum Schmelzen und einen 40 bis 60 Prozent höheren Energieaufwand.
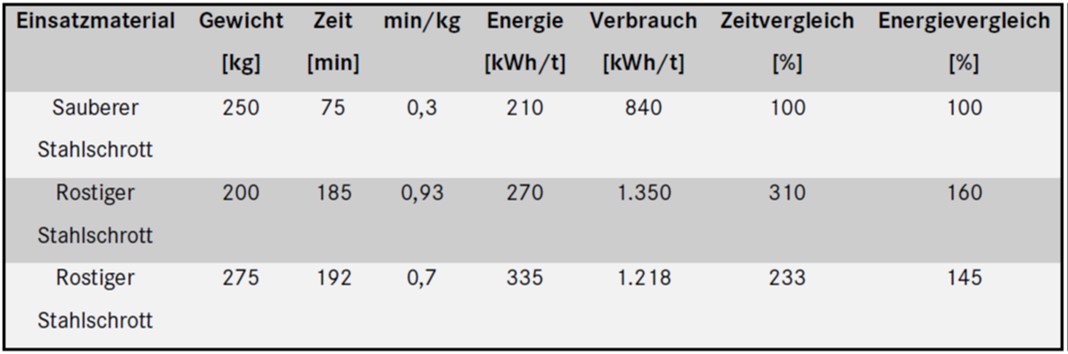
Die Packungsdichte der Einsatzmaterialien beim Schmelzen in einen elektrisch betriebenen Schmelzofen hat einen signifikanten Einfluss auf den Energiebedarf für das Erschmelzen dieser Einsatzmaterialien. So hat die Packungsdichte des Chargiergutes einen Einfluss auf die elektromagnetische Ankopplung und damit auf die elektrische Leistungsaufnahme des Einsatzmaterials.
Durch die Zerkleinerung des Einsatzmaterials wird zusätzlich die Beschickung erleichtert und die Gefahr einer Brückenbildung im Schmelzofen reduziert. Daraus ergeben sich in Abhängigkeit von der Leistungsaufnahme unterschiedliche Chargierzeiten und in der Folge unterschiedliche Energiebedarfswerte.
Tests wurden an einer Schmelzanlage mit einem Fassungsvermögen von 10 Tonnen und einer Nennleistung von 8.000 kW bei 250 Hz durchgeführt. Der leere Ofen wurde mit einer festgelegten Charge aus Roheisen, Gussbruch und Kreislaufmaterial einmal gefüllt. Dann wurde ohne Nachchargieren bis auf eine Temperatur von 1.380 °C aufgeschmolzen und der Energiebedarf ermittelt. Durch unterschiedliche Abmessungen des Kreislaufmaterials und des Stahlschrottes ergaben sich Packungsdichten im Bereich von 2 t/m³ bis 2,7 t/m³.
Der Einfluss der Packungsdichte ist in Abbildung 3 festgehalten. Die Ergebnisse der Untersuchungen zeigen, dass bei einer Abnahme der Packungsdichte von 2,5 t/m³ auf 2,0 t/m³ der Energiebedarf um etwa 25 kWh zunimmt.
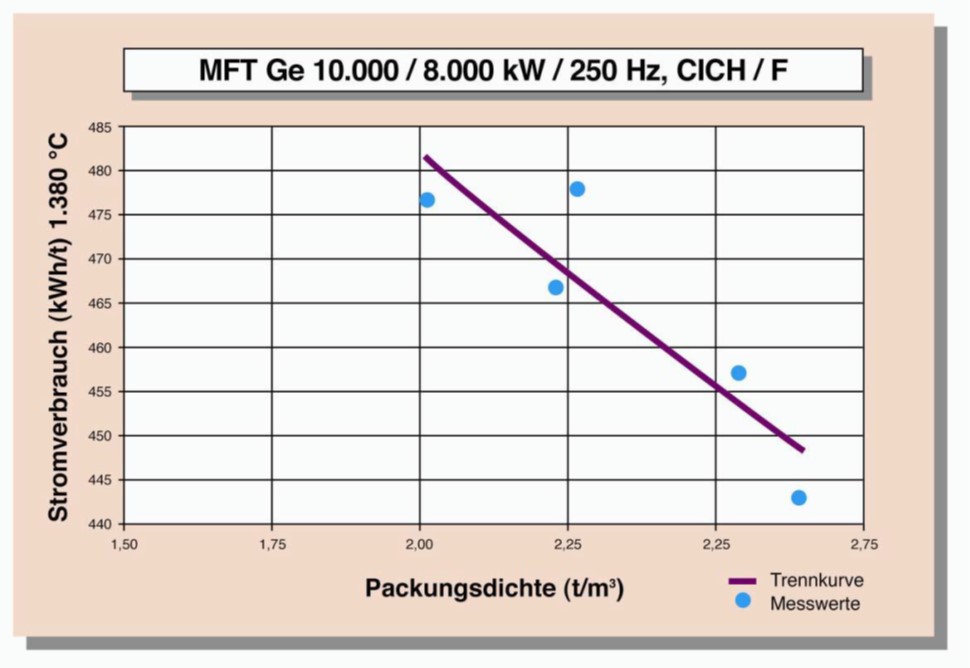
Die Stückigkeit ist auf eine möglichst hohe Schüttdichte einzustellen und der Ofengröße anzupassen: Maximale Kantenlänge gleich 0,5- bis 0,7-facher Tiegelinnendurchmesser. Eine Studie untersuchte ausführlich die Wahl der Chargierungsparameter (gebündelter und loser Stahl sowie gesäuberter Schrott und verschmutzter Schrott) auf den Energiebedarf und die Schmelzzeit in der Produktion von Kugelgraphit-gusseisenlegierungen, um Einflüsse zu identifizieren und die beiden Parameter zu optimieren. Dabei durfte der Input der einzelnen Komponenten 50 Prozent nicht überschreiten.
Ergebnis war, dass bei 50 Prozent gebündeltem Stahl und 50 Prozent gesäubertem Schrott sowohl der Energiebedarf als auch die Schmelzdauer am niedrigsten lag, wohingegen im entgegengesetzten Fall der Energiebedarf am höchsten und die Einschmelzzeit doppelt so lange benötigte.
Die Art und Weise der Zugabe von Aufkohlungsmittel hat Einfluss auf den Energiebedarf. Es sollte darauf geachtet werden, dass der Kohlenstoffgehalt der sich bildenden Schmelze nicht unnötig ansteigt.
Durchgeführten Untersuchungen zufolge ergibt sich ein deutlicher Mehrverbrauch an Energie, wenn das Aufkohlungsmittel nicht am Anfang des Schmelzvorganges zusammen mit den metallischen Einsatzstoffen eingesetzt wird, sondern erst nach dem Aufschmelzen in das flüssige Bad eingebracht wird.
Erfahrungen aus Versuchsreihen gehen davon aus, dass im letzteren Fall ca. 1 bis 2 kWh/kg Kohlungsmittel zusätzlich erforderlich sind. Bei einer Zugabe von 2 Prozent Aufkohlungsmittel sind etwa 40 kWh/t Eisen an Mehrverbrauch an Energie zu erwarten. Ansonsten kann dies zu einem unnötigen Tiegelverschleiß führen. Es wird daher empfohlen, die Dosierung des Aufkohlungsmittels gemeinsam mit der Charge vorzunehmen.
Typische Einflussfaktoren auf die Gattierung bei Kupolöfen sind beispielsweise:
- Genauigkeit der Wiegevorrichtung
- Genaues Einsatzverhältnis der Komponenten
- Energieeffiziente Gattierungsanweisung und genaue Bezeichnung der Einsatzstoffe (Verwechslungen ausschließen)
Wichtig für eine energieeffiziente Gattierung ist die richtige Lagerung der Einsatzmaterialien. In einigen Gießereien wird z. B. der Koks nicht vor Witterungseinflüssen (Regen, Schnee, Eis) geschützt, so dass sich der Feuchtigkeitsgehalt im Koks erhöht. Dadurch kann es zu einer Veränderung seiner Eigenschaften kommen (Kleben, Verringerung des Brennwerts etc.). Normalerweise variiert der Wassergehalt von Koks je nach Lagerbedingungen zwischen 0 und 15%.
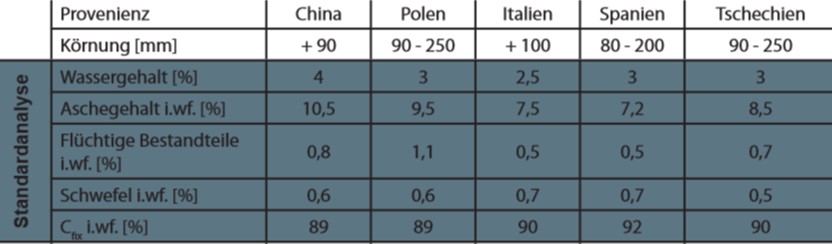
Diese Menge an Wasser im Koks verdampft im Kupolofen und wird mit dem Abgas ausgeführt. Einerseits ist dieser Vorgang nutzlos für den Schmelzprozess an sich, andererseits führt dies zu erhöhtem Energiebedarf. Wenn Koks an einem trockenen Ort gelagert wird, kann dieser zusätzliche Energiebedarf vermieden werden.
Aus Untersuchungen in Gießereien kann ein durchschnittlicher Wert für die Reduktion des Koksverbrauchs um 0,5 Prozent von der gesamten Einsatzmenge angenommen werden, wenn Überdachungen gebaut werden.
Zur sachgemäßen Lagerung von Einsatzmaterialien sollten folgende Hinweise beachtet werden:
- Schon bei der Anlieferung und beim Transport sollten die Einsatzmaterialien geschützt sein, z. B. dadurch dass das Transportfahrzeug bis in die überdachte Lagerhalle fahren kann
- Getrennte Lagerung für unterschiedliche Materialien und Metalltypen in separaten Bunkern oder Containern
- Ein betonierter Schrottplatz verhindert das Mitführen von Erde, Schmutz und Wasser
- Überdachte Lagerplätze oder zeltartige Abdeckungen bauen (eine Dachkonstruktion über dem Lagerbereich kann Regenwasser fernhalten und Staubemissionen zurückhalten)
- Füllhöhen im Vorratsbunker sollten nicht zu groß sein und die Wände keine zu starke Neigung aufweisen (z. B. bei Koks kann es sonst zum Zerdrücken durch das Eigengewicht kommen kann)
- Kontrollierte Zusammensetzung des Beschickungsmaterials
- Trockene Einsatzmaterialien (vor allem z. B. beim Koks) garantieren
Die Gattierungsberechnung sollte sich an folgenden Schritten orientieren:
- Festlegung der Soll-Analyse z. B. mit Werten für den Kohlenstoffgehalt
- Auswahl des metallischen Einsatzes für die Charge, z. B. Kreislaufmaterial, Stahlschrott und Roheisen mit Bestimmung der Eisenbegleiter der einzelnen Einsatzstoffe
- Daraus werden dann die Prozentanteile der Einsatzstoffe in der Charge festgelegt, wobei eine Berücksichtigung des Abbrandes vorgenommen werden sollte
- Korrekturzugabe für einzelne Eisenbegleiter
- Berücksichtigung der Aufkohlung und Aufschwefelung im Kupolofen durch den Koks
Die optimale Gattierungsfolge ist in nachfolgender Abbildung dargestellt:
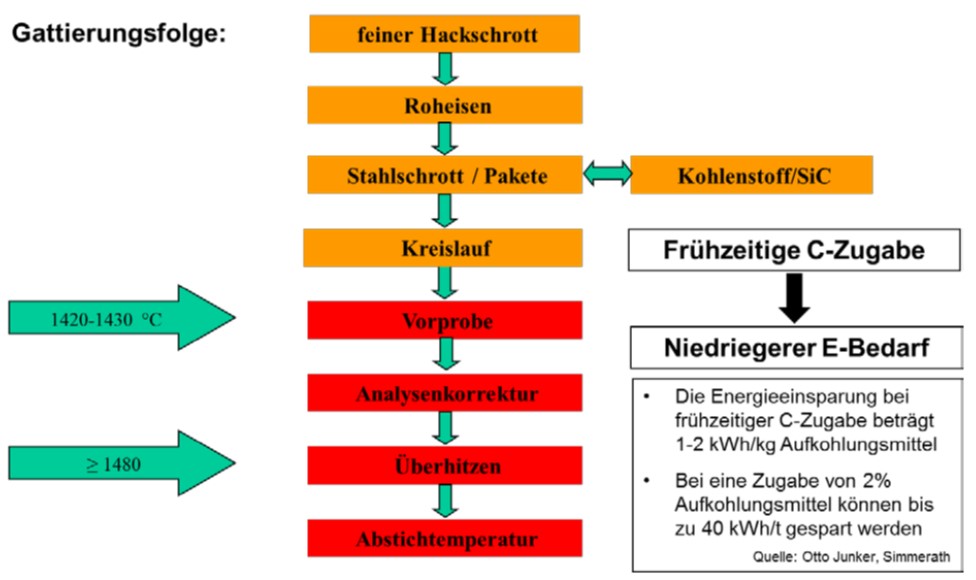
Diese Seite als PDF downloaden.
Informationsquellen
- Bembenek, K. (2013): Rechnergestützte Schmelzeführung und Gattierungsoptimierung. In: Giesserei, Nr. 5, S. 70-73 Dötsch, E. (2001): Energiesparendes und umweltschonende Schmelzen von Gusseisen im Induktionsofen. In: Giesserei 2001, Nr. 10, S. 25-29.
- Dötsch, E. (2009): Induktives Schmelzen und Warmhalten – Grundlagen, Anlagenaufbau, Verfahrenstechnik, Essen 2009
- Forschungsprojekt Foundrybench (2012): Best Practice Beispiel 26 - Dry cupola coke, www.foundrybench.fi
- Forschungsprojekt Foundrybench (2012): Best Practice Beispiel 27 - Furnace charging I, www.foundrybench.fi
- Forschungsprojekt Foundrybench (2012): Best Practice Beispiel 28 - Furnace charging II, www.foundrybench.fi
- Forschungsprojekt Foundrybench (2012): Best Practice Beispiel 29 - Furnace charging III, www.foundrybench.fi
- Ravichandran, S.; Alagumurthi, N.; Palaniradja, K. (2012): Optimization of raw material charge mix in induction furnace for energy conservation in doundry industry. In: International Foundry Research, Nr. 4, S. 10-17
- Umweltbundesamt (2004): Merkblatt über Beste Verfügbare Techniken in der Gießereiindustrie, Abruf Mai 2013
- VDG Akademie (2007): Qualifizierungslehrgang – Schmelzbetrieb in Eisengießereien, Düsseldorf 2007.
- VDG Merkblatt R 80 (2008): Gießereikoks, Abruf Mai 2013