Absaugtechnik hilft Energiekosten sparen
Von Katrin Herbes, Velen
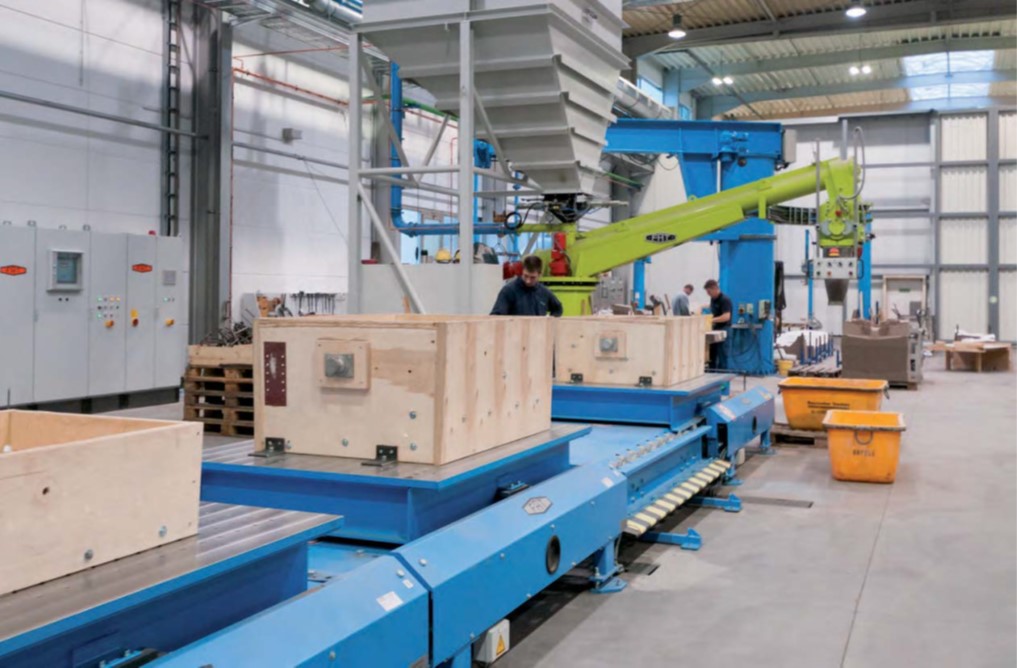
Die Zahl der gefertigten Formen konnte bei Grunewald durch das Pep-Set-Verfahren erheblich gesteigert werden.
Erschienen in GIESSEREI 10/2014
Hoher Kostendruck, kurze Lieferzeiten, hohe Qualitätsansprüche: die Anforderungen an Gießereien im globalen Wettbewerb sind hoch. Dem hat die Grunewald GmbH & Co. KG, Bocholt, pünktlich zum 50-jährigen Bestehen im vergangenen Jahr Rechnung getragen. Mit einer neuen Halle und hochmoderner Verfahrenstechnik in der Formerei und Sandregenerierung hat sie ihre Kapazitäten im Gussbereich erheblich erweitert. Das energiesparende raumlufttechnische Konzept hierfür hat die Teka Absaug- und Entsorgungstechnologie, Velen, entwickelt.
Der Gussbereich ist neben dem Werkzeug- und dem Komponentenbau das dritte große Standbein des internationalen Unternehmens, das an sechs Standorten in Bocholt, Irxleben und Detroit, USA, 240 Mitarbeiter beschäftigt. Einen Namen gemacht hat sich Grunewald als einer der europaweit führenden Hersteller von dünnwandigen Aluminiumstrukturteilen für den Automobilbereich, die Halbleiterindustrie und den Maschinenbau sowie für die schnelle Produktion von Prototypen und Kleinserien.
„Die Erweiterung der Gießerei auf insgesamt 2800 m2 war ein wichtiger Schritt in Richtung Zukunftssicherung. So konnten wir den gesamten Produktionsprozess an einem Standort bündeln und neu strukturieren“, schildert Ulrich Grunewald, der das Familienunternehmen gemeinsam mit Vater Christian und Bruder Philipp leitet. Technisch geht Grunewald neue Wege und hat den Prozess der Formherstellung und Sandregenerierung auf eine hochmoderne Grundlage gestellt.
Exklusive Mischung beim Pep-Set-Verfahren
In der Formerei erfolgt die Bindung des mit Harzsystemen ausgehärteten Quarzsandes nach dem in Deutschland noch selten angewandten Pep-Set-Verfahren. Dabei kommt eine Mischung zum Einsatz, die der Spezialchemikalienhersteller ASK Chemicals, Hilden, zurzeit exklusiv für Grunewald herstellt. Das Ergebnis: eine noch bessere Qualität der fertigen Aluminiumgussteile sowie eine höhere Produktivität bei der Formherstellung. „Wir erhalten einen fast fließfähigen Sand, der bei der Verarbeitung kaum Klebewirkung zeigt. Hierdurch ist die Oberfläche der Gussteile viel glatter als bisher“, schwärmt Gießereileiter Harald Dieckhues. Auf eine Nachbearbeitung kann fast völlig verzichtet werden. Ein weiterer Vorteil: Dank der erhöhten Bindekraft des Gemischs ist die Endfestigkeit der Formen schneller erreicht, wodurch die Zahl der pro Stunde hergestellten Formen erheblich gestiegen ist.
Die neue Sandaufbereitungsanlage arbeitet besonders ressourcenschonend und kostensparend. Sie verfügt neben der mechanischen nun auch über eine thermische Regenerierungsstufe, die den Sand während eines Brennprozesses in einem etwa 700 °C heißen Ofen vom Binder trennt (Bild 1). Der Großteil des Sandes steht mit höchster Qualität wieder zur Verfügung. Statt bisher bis zu 40 % Ausschuss pro Tonne müssen nur noch rund 10 % durch Neusand ersetzt werden (Bild 2). „Dies schont die Umwelt und den Geldbeutel, da die Kosten für Entsorgung und Neuanschaffung erheblich gesenkt werden“, betont Ulrich Grunewald.
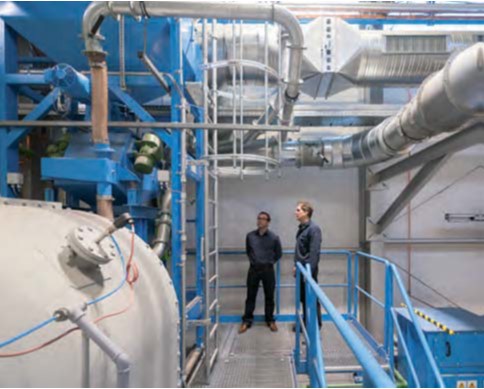
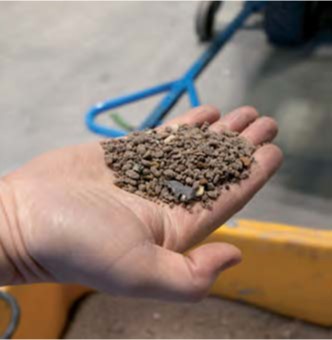
Individuell zugeschnittenes raumlufttechnisches Konzept
Auf zukunftsweisende Technik setzt das Unternehmen auch, was den Bereich der Absaugtechnik angeht. Bei der Entscheidung für die Teka Absaug- und Entsorgungstechnologie aus dem westfälischen Velen spielten mehrere Faktoren eine SPEKTRUM Rolle: „Den Ausschlag hat gegeben, dass wir ein individuell auf die Gegebenheiten bei Grunewald zugeschnittenes raumlufttechnisches Konzept erhalten haben, das nicht nur unsere Mitarbeiter schützt, sondern sich auch als besonders energieeffizient erweist“, erklärt er weiter.
Die Kernfrage, der sich die Ingenieure bei Teka stellen mussten, lautete: Wie lässt sich die verschmutzte Luft zuverlässig aus der Halle schaffen, ohne die Heizund Prozesswärme ungenutzt zu lassen? Zu berücksichtigen war, dass in der Formerei und bei der mechanischen und thermischen Regenerierung mit Staub bzw. einem Staub-/Gasgemisch unterschiedliche gesundheitsgefährdende Schadstoffe entstehen, die getrennt voneinander abgesaugt und verwertet werden mussten. Entschieden hat sich Grunewald für eine Lösung, die auf den Prinzipen der Luftrückführung und der Wärmerückgewinnung basiert.
Große Staubmengen entfernen und filtern
Herzstück des Systems bilden acht Absaug- und Filteranlagen vom Typ ZPF – drei für die thermische Regenerierung und Formerei und fünf für die mechanische Regenerierung (Bild 3). Sie sind platzsparend außerhalb der Halle errichtet und zeichnen sich durch eine hohe Absaugleistung, viel Filterfläche und lange Filterstandzeiten aus.
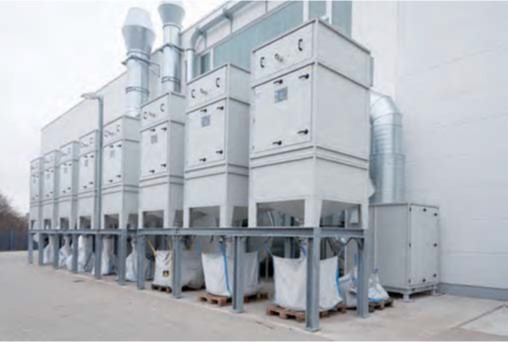
Der Prozess in Kürze: Über zahlreiche Erfassungsstellen wird die belastete Luft nah an der Entstehungsstelle abgesaugt und über Rohrleitungen zu den jeweiligen Filteranlagen geführt (Bild 4).
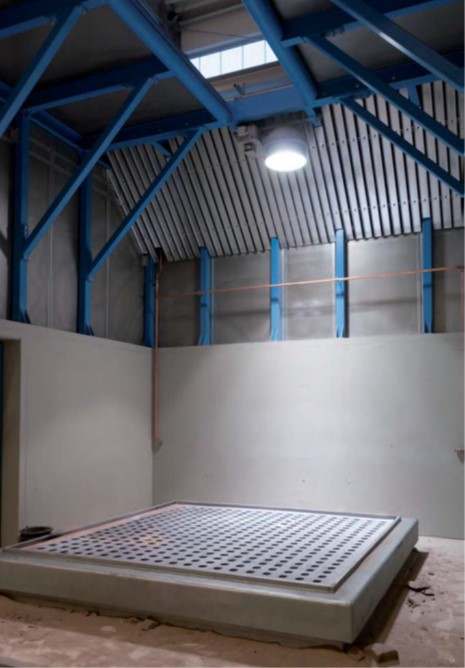
Um abrasivem Verschleiß vorzubeugen, weisen die Stahlrohre eine 3 mm starke Wandung auf. Bei einem Volumenstrom von 15 000 m3/h (thermische Regenerierung und Formerei) bzw. 30 000 m3/h (mechanische Regenerierung und Silos) ist das System in der Lage, große Staubmengen zu entfernen. In den Anlagen durchläuft die verschmutzte Luft einen intensiven Reinigungsprozess. Sie sind jeweils mit neun Patronen á 15,6 m2 Filterfläche ausgestattet (Gesamtfilterfläche von 1120 m² bei 72 Patronen) und lassen sich bei geringem Strom- und Druckluftverbrauch automatisch abreinigen, ohne dass der Betrieb unterbrochen werden muss. Der Reststaub wird in einfach zu entsorgenden Big Bags aufgefangen. Realisiert wird der Anlagenbetrieb mit einer Simatic-Steuerung von Siemens. Die Bedienung und Visualisierung der Filteranlagen erfolgt über Touch Panels (Bild 5).
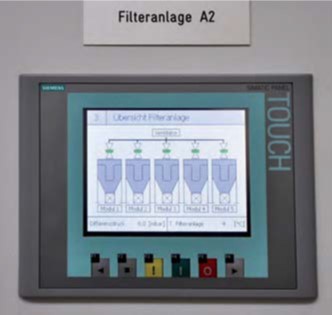
Saubere Luft ohne Wärmeverlust
Nach dem Filterprozess wird die von Stäuben gereinigte und bereits erwärmte Luft aus der mechanischen Regenerierung und den Sandsilos über eine Rohrleitung mit Ausblasgittern zu 100 % in die Halle zurückgeführt. Möglich wird dies vor allem durch den hohen Stand der Filtertechnik: Das System ist mit Patronen ausgestattet, die der Staubklasse M entsprechen. Sie sind gemäß DIN EN 60335-2-69 für Stäube mit einem Arbeitsplatzgrenzwert ≥ 0,1 mg/m3 Luft geeignet, der weit unter den in Gießereien geltenden Grenzwerten liegt.
Darüber hinaus scheiden sie selbst feine Stäube in einer Größenordnung von 0,2 bis 2 μm (Prüfstaub 200 mg/m3 Quarzstaub) zu mehr als 99,9 % ab. Die Arbeitsplatzgrenzwerte für Emissionen in Gießereien werden so in der Regel bei weitem unterschritten – die emittierte Luft ist meist reiner als die zugeführte Umgebungsluft. Zugleich wird die vorhandene Wärme optimal genutzt. Auf Belüftungsanlagen, die Frischluft in den Raum tragen und erhitzen, kann verzichtet werden. Das spart vor allem im Winter Energie und schont die Umwelt. Im Sommer kann die Abluft nach draußen geleitet werden. „Die Energiekosten schnellen immer weiter nach oben. In dieser Situation die erwärmte Luft in den kalten Monaten ungenutzt nach draußen zu blasen, wäre Verschwendung pur“, konstatiert Ulrich Grunewald.
Bei Verbrennungsprozessen in der thermischen Regenerierung entstehen neben Stäuben auch Gase. Anders als bei der mechanischen Regenerierung muss die abgesaugte Luft daher nach außen geleitet und Frischluft zugeführt werden. Mit Hilfe eines Kreuzwärmetauschers kann vor allem die Abwärme des Ofens genutzt werden, um die Luft auf 35 °C zu erhitzen und über eine Rohrleitung gleichmäßig in der Halle zu verteilen. Der Kreuzwärmetauscher weist bei einer angenommenen mittleren Außentemperatur von 10 °C im Jahr einen Wirkungsgrad von 57,8 % und eine Heizleistung von 227 kW auf.
Fazit
„Nach unseren Berechnungen haben sich die Investitionen in das Absaugsystem in knapp acht Jahren amortisiert“, rechnet Ulrich Grunewald vor. Hinzu kommt: In der Regel steigt die Temperatur in der Halle so stark an, dass die Heizungsanlage nach unten reguliert oder sogar ganz ausgeschaltet werden kann, was die Kosten weiter reduziert. Zusätzliche Einsparpotenziale bieten Frequenzumrichter, die im Bereich der Filter und des Wärmetauschers angebracht sind.
Das Ergebnis: Das Absaugsystem entfernt Stäube und gasförmige Stoffe aus der Halle. Gleichzeitig ist es durch die optimale Ausschöpfung der vorhandenen Wärme in erheblichem Maße möglich, Energie einzusparen und die CO2-Belastung zu senken. Ulrich Grunewald ist von dem Ergebnis begeistert: „Der moderne Arbeitsschutz kommt nicht nur unseren Mitarbeitern und der Umwelt zugute, sondern wirkt sich auch positiv auf die Energiebilanz im Unternehmen aus.“
Katrin Herbers, Marketing, Teka Absaugund Entsorgungstechnologie GmbH, Velen