Energieeffizienz professionell managen
Von Wolfgang Kallmeyer, Köln, Und Detlef Rissenbeck, Menden
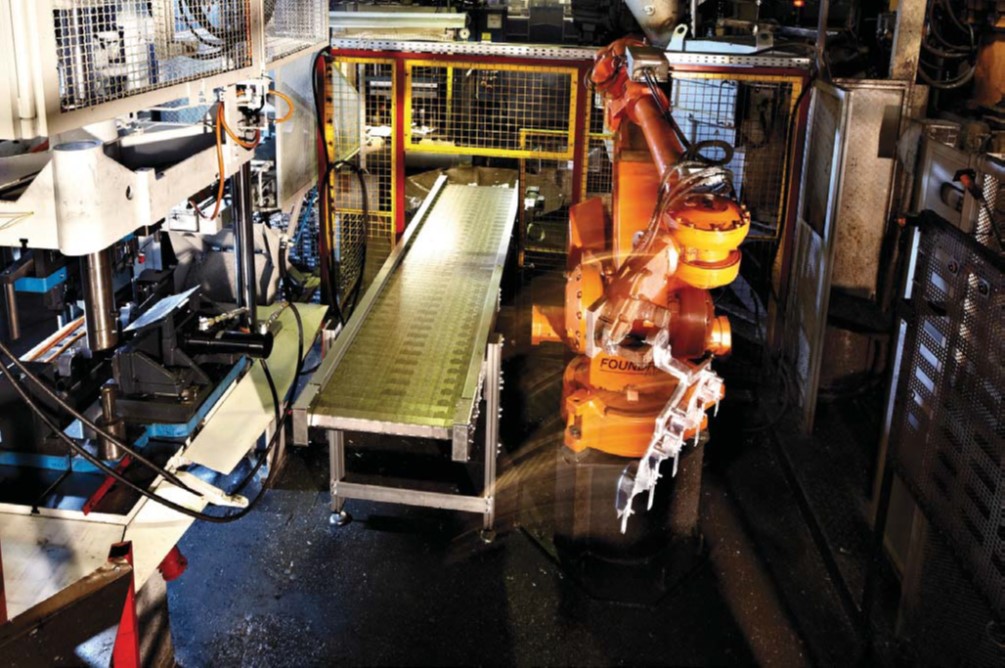
Erschienen in GIESSEREI 09/2013
Mit über einer Million Zertifikaten ist das Qualitätsmanagementsystem nach ISO 9001 bereits ein Klassiker, der sich als anerkannter Standard weltweit durchgesetzt hat. Seit Dezember 2011 gibt es die ISO 50001 als Zertifizierungsstandard für Energiemanagementsysteme. Immer mehr Gießereien setzen auf diese Zertifizierung.
Seit Dezember 2011 gibt es die ISO 50001 als Zertifizierungsstandard für ein Energiemanagementsystem. Der Vorläufer, die Europäische Norm EN 16001 aus dem Jahre 2009, wurde im April 2012 zugunsten der internationalen ISO-Norm zurückgezogen.
Kern des Energiemanagementsystems nach ISO 50001 ist der Begriff „energiebezogene Leistung“. Was erhalten wir für 1 kWh Strom, Gas oder sonstige Energieträgern an Gütern oder Werten. Mit weniger Energie das Gleiche oder mehr zu erreichen, zu produzieren, das bedeutet Energieeffizienz.
Der Energieeinsatz ist auch in Umweltmanagementsystemen immer einer der Umweltaspekte gewesen, aber nur einer unter vielen. Das führte in der Vergangenheit dazu, dass man sich auf die Umweltauswirkungen auf der Output-Seite, wie Abfall, Abwasser, Emissionen etc. fokussierte. Die Input-Seite mit den Material- und Energieverbräuchen führte da eher ein Schattendasein (Bild 1).
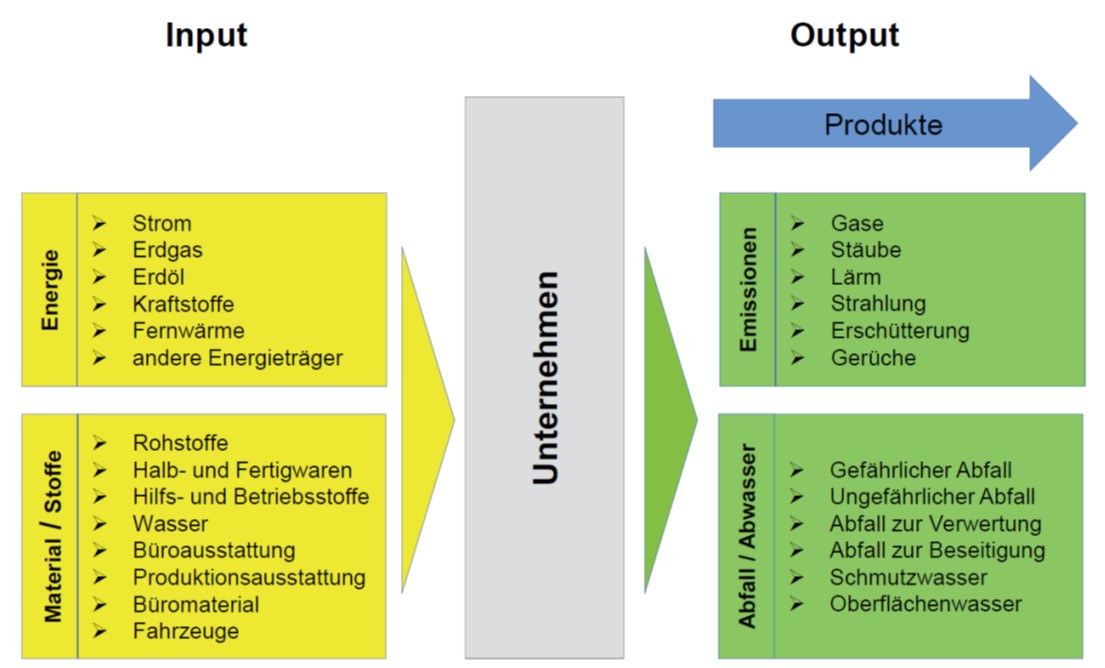
Lastmanagement bei Silbitz Guss
Dabei steuert die Input-Seite die Output-Seite. Weniger Energieverbrauch erzeugt weniger Klimagase, zumindest noch so lange, wie die meiste Energie durch Verbrennen von Gas, Kohle, Öl etc. gewonnen wird. Jedes Kraftwerk, was nicht benötigt wird, erzeugt seinerseits keine Umweltauswirkungen, bis hin zur Gewinnung der Energieträger selber.
Ähnliches gilt für den Materialeinsatz. Je weniger Materialeinsatz an Rohstoffen, Hilfs- und Betriebsstoffen, Wasser, etc. wir für ein gutes Produkt benötigen, umso weniger Abfall-, Abwasser und Emissionen werden erzeugt. Auch hier ist Materialeffizienz der Schlüssel für eine nachhaltige Produktion.
Nicht noch ein Managementsystem ist das Motto, sondern der Einsatz eines wirksamen Managementsystems, welches sich einem der beiden wichtigsten Stellhebel einer nachhaltigen Produktion bedient, der Energieeffizienz.
Das politische Umfeld
Das Thema Energiemanagement wird in Deutschland stark durch die Politik und seine Vorgaben beeinfl usst. Hintergründe der politischen Einfl ussnahme sind:
- das Nichterreichen von Klimaschutzzielen, zu denen sich Deutschland, Europa und Teile der Welt verpfl ichtet haben (Klimaschutzabkommen von Kyoto),
- die Atomkatastrophe von Fukushima, welche politisch den geplanten Atomausstieg in Deutschland zur Folge hatte und
- die Energiewende mit einer Hinwendung zu den erneuerbaren Energien, welche die Atomkraft und mittelfristig auch einen Teil der fossilen Kraftwerke ersetzen sollen.
Alle diese Ziele sind leichter zu erreichen, wenn der Energieverbrauch in Deutschland reduziert wird, ohne das gewünschte Wachstum dabei zu gefährden. Das noch ungenutzte Potential hinsichtlich Energieeffi zienz wird in Deutschland zurzeit auf ca. 30 % geschätzt.
Um Teile dieses Potentials zu heben, bedient sich die Politik klassischer Mittel wie der Steuer- und Abgabenpolitik. Energieintensive Unternehmen und das produzierende Gewerbe, zu denen auch Gießereien zählen, bekommen zur Verbesserung der internationalen Wettbewerbsfähigkeit vom Staat Hilfen in Form von Erleichterungen bei Steuern und Abgaben. Diese werden aber zunehmend an eigene Anstrengungen zur Energieeffi zienz geknüpft. Um diese Anstrengungen nachzuweisen, wird zurzeit und zukünftig verstärkt von den Unternehmen ein zertifi ziertes Energiemanagementsystem nach ISO 50001 oder eine Umweltvalidierung nach EMAS III (Eco-Management and Audit-Scheme) gefordert.
Die energieintensive Gießerei-Industrie hat die Möglichkeit, eine Vielzahl von energierechtlichen Steuerentlastungen- und -befreiungen und Abgabenbegrenzungen in Anspruch zu nehmen.
Erneuerbare Energiegesetz (EEG)
Unternehmen des produzierenden Gewerbes, welche im internationalen Wettbewerb stehen, können auf Antrag nach § 41 EEG eine Begrenzung der EEG-Umlage in Anspruch nehmen. Voraussetzungen dafür sind, dass der von den Elektrizitätsversorgungsunternehmen bezogene und selbst verbrauchte Strom an einer Abnahmestelle mindestens 1 GWh betragen hat, das Verhältnis der von dem Unternehmen zu tragenden Stromkosten zur Bruttowertschöpfung des Unternehmens mindestens 14 % betragen hat und die EEG-Umlage anteilig an das Unternehmen weitergereicht wurde. Für Unternehmen mit einem Stromverbrauch von größer als 10 GWh ist eine Zertifi zierung nach ISO 50001 oder EMAS III erforderlich. Bei einem Stromverbrauch von mindestens 1 GWh bis 10 GWh pro Jahr müssen diese Unternehmen nur 10 % und bei einem Stromverbrauch über 10 GWh bis 100 GWh pro Jahr nur 1 % der EEG-Umlage bezahlen. Anträge auf Begrenzung der EEG-Umlage können noch für das Jahr 2015 eingereicht werden.
Stromsteuer und Energiesteuergesetz (StromStG, EnergieStG)
Steuerbefreite Prozesse § 51 EnergieStG § 9a StromStG
Energieerzeugnisse, die für die Metallerzeugung und -bearbeitung sowie im Rahmen der Herstellung von Metallerzeugnissen für die Herstellung von Schmiede-, Press-, Zieh- und Stanzteilen, gewalzten Ringen und pulvermetallurgischen Erzeugnissen und zur Oberfl ächenveredlung und Wärmebehandlung verwendet werden, sind von der Energiesteuer befreit. Dies gilt nach § 37 EnergieStG auch für Kohle, die als Heizstoff e für die gerade genannten Prozesse eingesetzt wird.
Steuerermäßigung § 9b StromStG, § 54 EnergieStG
Die Ermäßigungen für Unternehmen des produzierenden Gewerbes können nach § 9b StromStG und § 54 EnergieStG von den Unternehmen in Anspruch genommen werden, deren Steuerlast den Sockelbetrag, der als Selbstbehalt zu verstehen ist, von 1000 Euro übersteigt. Die Ermäßigung beträgt 5,13 Euro/MWh für Strom, 15,34 Euro/1000 l für Heizöl, 1,38 Euro/MWh für Erdgas und 15,15 Euro/1000 kg für Flüssiggas.
Steuerermäßigung § 10 StromStG, § 55 EnergieStG
Unternehmen des produzierenden Gewerbes können auf Antrag nach § 10 StromStG und § 55 EnergieStG die Entlastung in Sonderfällen, den sogenannten "Spitzenausgleich“, in Anspruch nehmen. Dabei wird die nach der Ermäßigung für Unternehmen des produzierenden Gewerbes nach § 9b StromStG und § 54 EnergieStG verbleibende zu zahlende Ökosteuer mit den Entlastungen der Rentenversicherungsbeiträge verrechnet. Der errechnete Wert wird unter Berücksichtigung des Sockelbetrags von 1000 Euro zu 90 % zurückerstattet.
Als Voraussetzung müssen Großunternehmen ab 2015 (über 250 Mitarbeiter oder Jahresumsatz über 50 Mio. Euro) ein Energiemanagementsystem nach ISO 50001
oder eine EMAS-Validierung vorweisen. Kleine und mittlere Unternehmen können anstelle der genannten Managementsysteme ersatzweise Systeme anwenden, die den Anforderungen der DIN EN 16247-1 entsprechen. In den Antragsjahren 2013 und 2014 müssen Unternehmen bereits einen Nachweis darüber erbringen, dass sie mit der Einführung eines der zuvor genannten Systeme begonnen haben.
Des Weiteren ist die Höhe der Erstattung ab dem Antragsjahr 2015 an das Erreichen der Energieeinsparziele der Bundesregierung gekoppelt. Dabei soll das produzierende Gewerbe in Deutschland seine Energieintensität im Vergleich zur jahresdurchschnittlichen Energieintensität des Basisjahre 2007-2012 um ca. 1,3 % pro Jahr verbessern. Nur wenn dieser Zielwert vollständig erreicht wird, folgt eine vollständige Auszahlung des Erstattungsbetrages. Wird der Zielwert nicht mindestens zu 92 % erreicht, erfolgt keine Erstattung. Liegt der Zielerreichungsgrad zwischen 92 und 96 %, werden 60 % ausgezahlt und bei einem Zielerreichungsgrad von 96 bis 100 % werden 80 % des Erstattungsbetrags ausgezahlt (Tabelle 1).
Tabelle 1: Beispielrechnung für eine Gießerei*.
Stromverbrauch | 20 GWh |
Gasverbrauch | 5 GWh |
Koksverbrauch | 30 GWh |
Mitarbeiteranzahl | 250 |
Durchschnittsgehalt | 35 000 Euro p.a. |
Bruttowertschöpfung | 14 % |
EEG Umlage | 5277 ct./kWh |
Benutzungsstundenzahl | 7000 h |
Netzentgelt | 20 % |
Erstattungsgrundlage | Erstattungsbetrag |
§41 EEG (besondere Ausgleichsregelung) | ca. 950 000 Euro |
§ 9b StromStG und § 54 EnergieStG | ca. 109 000 Euro |
§10 StromStG und § 55 EnergieStG (Spitzenausgleich) | ca. 220 000 Euro |
§ 37 EnergieStG Steuerbefreiung von Kohle | ca. 36 000 Euro |
Summe | ca. 1 315 000 Euro |
*Die berechneten Werte sind rein zur Darstellung der Größenordnung der Entlastungseffekte gedacht und daher unverbindlich. |
Die Gießerei und das Energiemanagement
Als Unternehmen, welches im internationalen Wettbewerb steht und die Energiekosten ca. 7 % der Gesamtkosten ausmachen, hat sich die Schött-Druckguß GmbH in Menden auch in der Vergangenheit mit dem Thema Energiekosten bereits auseinandersetzen müssen. Das 1963 gegründete Unternehmen mit ca. 230 Mitarbeitern ist ein privat geführter Mittelständler, wie man ihn häufiger im Sauerland findet. Neben der energieintensiven Gießerei mit Schmelzbetrieb und etlichen Druckgießzellen gibt es die für eine Gießerei klassische Nachbearbeitung (Entgraten, Putzen, Stahlen, etc.) der Gussteile sowie eine gut ausgestattete CNC-Bearbeitung (Bild 2).
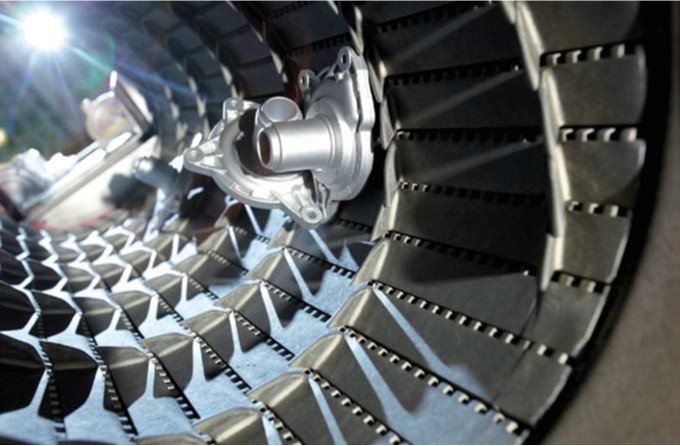
Hauptkunden des Unternehmens sind die Automobilindustrie, Elektroindustrie, Heiztechnik sowie der Maschinen-, Anlagen- und Gerätebau. Das Unternehmen unterhält seit 1998 ein zertifiziertes Qualitätsmanagementsystem nach ISO 9001, welches in 2002 um den automotiven Standard ISO/TS 16949 erweitert wurde. Im Jahre 2004 ließ sich das Unternehmen auch im Umweltmanagement nach ISO 14001 zertifizieren. Im Umgang mit Managementsystemen konnte Schött-Druckguß auf viele Jahre Erfahrung zurückgreifen, was den Aufbau des Energiemanagementsystems (EnMS) positiv beeinflusste.
Natürlich nutzte die Schött-Druckguß GmbH in der Vergangenheit wenn möglich, wie viele andere energieintensiven Unternehmen auch, steuerliche oder abgabentechnische Vorteile. In erster Linie war dies die Steuererstattung im Rahmen des Strom- und Energiesteuergesetzes. Bislang konnte eine Reduzierung der EEG-Umlage, wie es für energieintensive Unternehmen nach dem EEG möglich ist, deshalb nicht erreicht werden, weil der Anteil der Stromkosten an der Bruttowertschöpfung nicht mindestens die erforderlichen 14 % ausmachte. Da die Druckgießerei aber kontinuierlich wächst, ist absehbar auch ein Überschreiten dieser Grenze in naher Zukunft möglich. Die für das EEG notwendige Schwelle des Stromverbrauches von mehr als 10 GWh pro Jahr wird überschritten. In vergleichbarer Größenordnung wie der Stromverbrauch liegt in Summe auch der Verbrauch fossiler Brennstoffe (Erdgas, Erdöl, Kraftstoff, etc.) im Unternehmen.
Unmittelbarer Auslöser für den Beschluss der Geschäftsführung zur Einführung eines Energiemanagementsystems war sicherlich die Änderung des Strom- und Energiesteuergesetzes von 2013, welche ab 2015 für die Erstattung von Steueranteilen ein zertifiziertes Energiemanagementsystem von den Unternehmen fordert sowie die Möglichkeit, von den besonderen Regelungen des EEG zukünftig profitieren zu können. Auch Letzteres setzt ein Zertifikat nach ISO 50001 voraus. Zum anderen war man sich bei Schött-Druckguß bewusst, dass das Thema Energieeffizienz in der Vergangenheit nur sporadisch im Rahmen des bestehenden Umweltmanagementsystems betrachtet worden war. Daraus resultierte die Erkenntnis, dass keine klaren Vorstellungen mehr existierten, welches Effizienzpotential dort noch vorhanden war. Klar war jedoch, dass dies bei einem Kostenanteil von mehr als 7 % für Energie ein lohnendes Thema sein könnte.
Nach einem intensiven Vorgespräch im Hause Schött über das Thema Energiemanagement und dessen Realisierung unter den Rahmenbedingungen bei Schött-Druckguß, wurde im Juli 2012 der Auftrag zur Unterstützung bei der Einführung eines Energiemanagementsystems an die TÜV Rheinland Consulting GmbH (TRC) in Köln erteilt. Ein branchenerfahrener Berater sollte das Team des Unternehmens verstärken und mit seinem Know-how für eine effi ziente Projektabwicklung Sorge tragen. Zu den Voraussetzungen des Projekts gehörte, das Energiemanagementsystem in das bestehende integrierte Managementsystem aus Qualitäts- und Umweltmanagement einzubinden sowie eine Zertifi zierung gemeinsam mit dem Umweltmanagementsystem im April 2013 zu realisieren.
Das Projekt Energiemanagement
Um das Projekt auf den Weg zu bringen, wurde zuerst eine Einführungsveranstaltung im Unternehmen organisiert, um die Führungskräfte der Schött-Druckguß GmbH über die wesentlichen Rahmenbedingungen zu informieren. Die einzelnen Meilensteine des Projektes und deren Inhalte wurden erläutert (Bild 3).
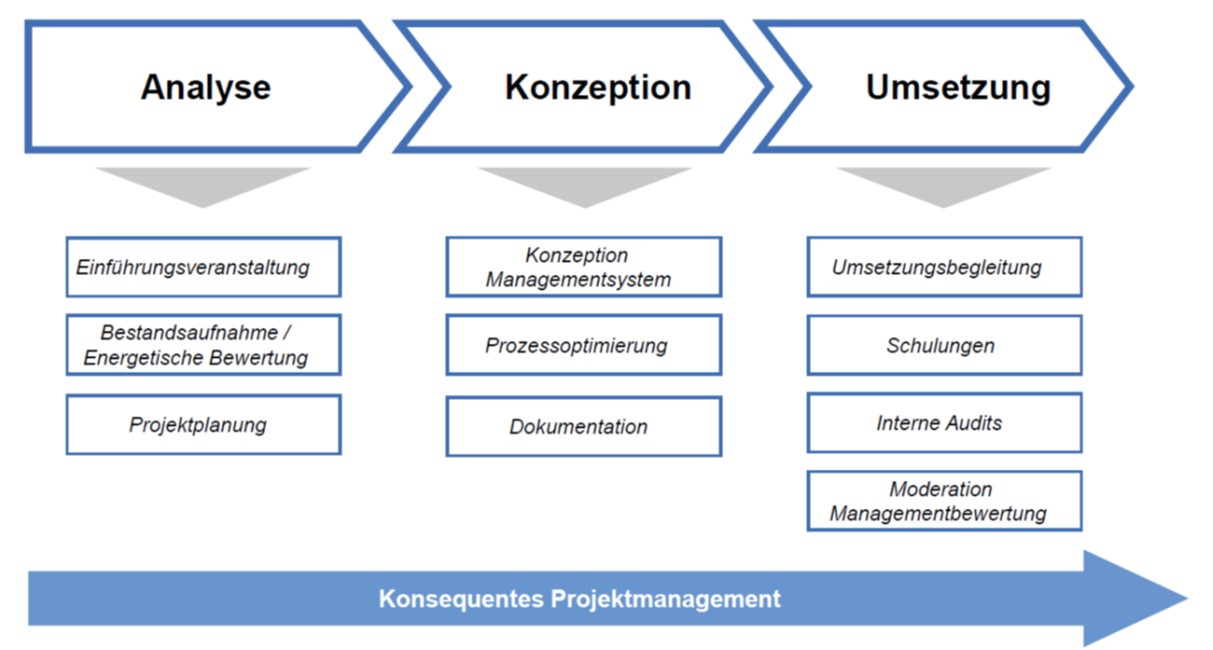
Wesentliche organisatorische Rahmenbedingungen des Projektes, wie z. B. das Kernteam, wurden festgelegt. Es setzte sich aus fünf Personen zusammen: aus dem kaufm. Leiter, dem Betriebsleiter, dem Qualitäts- und Umweltmanagementbeauftragten und dem Berater der TRC. Seitens der Geschäftsführung wurde dem Umweltmanagementbeauftragten in Personalunion auch das Amt des Energiemanagementbeauftragten übertragen. Damit war sichergestellt, dass die vielen Schnittstellen der Umwelt- und Energiemanagementsysteme aus einer Hand betreut wurden und unnötige Reibungsverluste erst gar nicht entstehen konnten.
Im Team wurde der Ablauf der Bestandsaufnahme und die erste energetische Bewertung detailliert erläutert und diskutiert. Die Bestandsaufnahme sollte Klarheit in vier Fragen bringen:
- Was ist von dem bestehenden integrierten Managementsystem für das Energiemanagementsystem nutzbar? Unnötiger Aufwand und Doppelarbeit sollten auf jeden Fall vermieden werden.
- An welchen Stellen der bestehenden Systemdokumentation können notwendige Inhalte des Energiemanagements integriert oder angedockt werden? Dabei sollte die Prämisse einer schlanken Dokumentation auch weiterhin berücksichtigt werden.
- Wie ist der Status der Energieeffi zienz bezüglich infrastruktureller und produktionstechnischer Einrichtungen zu bewerten? Wo sind Energieeinsparpotentiale zu erkennen und wie lassen sie sich realisieren?
- Welche Daten benötigt das Unternehmen, um eine erste energetische Bewertung durchführen zu können? Wie können diese Daten in kurzer Zeit erhoben werden?
Die Bestandsaufnahme
Die Erfassung und Auswertung des Status quo bei Schött-Druckguß zählte ohne jeden Zweifel zu den aufwendigsten Teilen des Gesamtprojekts.
Die Bestandsaufnahme gliedert sich in zwei Teile
- die Bestandsaufnahme zum Managementsystem und
- die Bestandsaufnahme zu den Energieaspekten des Unternehmens.
Die Bestandsaufnahme zum Managementsystem bestand aus einer Prüfung der bestehenden Systemdokumentation im Hinblick auf Struktur und Anknüpfungspunkte für das Energiemanagementsystem. ISO-basierende Managementsysteme haben in den sogenannten systemrelevanten Forderungen vergleichbare Inhalte, die es nahelegen, diese miteinander integrativ zu verbinden. Das spart Aufwand bei der Erstellung und Pfl ege der Dokumentation (Bild 4).
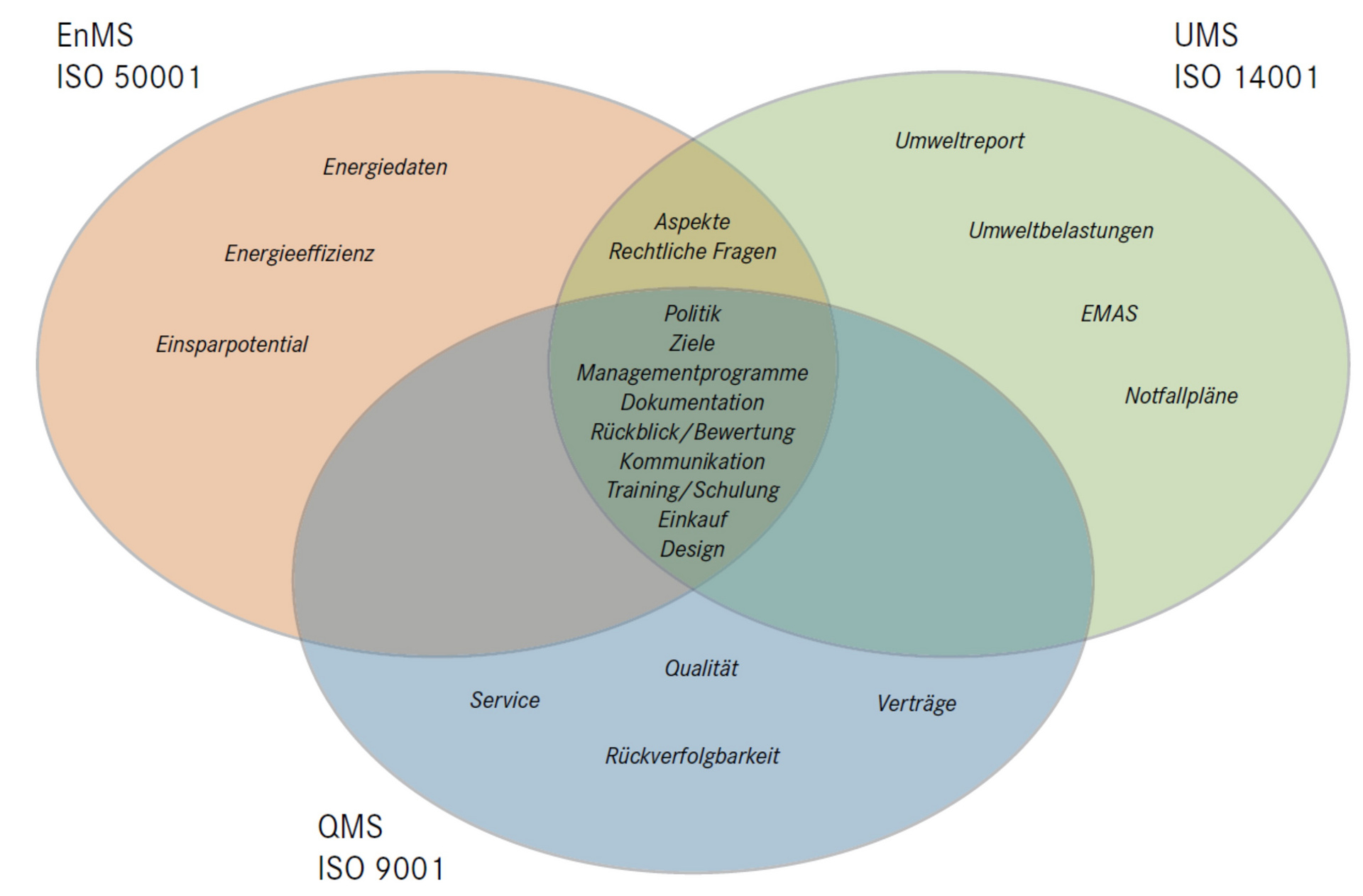
Das Ergebnis war eine Identifi kation von Handbuchkapiteln und Verfahrensanweisungen, die um die Belange des EnMS erweitert werden mussten. Außerdem wurden vier Verfahrensanweisungen identifi ziert, welche für das EnMS neu erstellt werden mussten.
Im zweiten Schritt wurden die Energieaspekte ermittelt. Dazu sammelte der TÜV-Berater mit Unterstützung der Schött-Mitarbeiter verlässliche, konkrete Daten aus allen Betriebsbereichen. Von wesentlichem Interesse waren die eingesetzten Energieträger (Strom, Gas, etc.) und deren vom Versorger bezogenen Mengen. Wie verteilen sich die Energieströme im Unternehmen und für welche betrieblichen Zwecke werden sie verwendet? Wie ist die quantitative Erfassung von Teilströmen möglich oder bereits realisiert? Eine der wesentlichen Voraussetzungen für ein funktionsfähiges betriebliches Energiemanagementsystem ist die Erfassung einzelner Energieverbräuche über Zähler. Der alte Leitsatz des Qualitätspapstes Edwards Deming „Was Du nicht messen kannst, kannst Du auch nicht steuern“ gilt ganz besonders für das Energiemanagement. Neben der Erfassung von absoluten Energieverbräuchen wurde auch die Erfassung betrieblicher Teilleistungen ermittelt, welche mit dem Energieeinsatz erzeugt wurden.
Auf Fragen wie: Wie viel kWh Strom braucht man, um 1 m3 Druckluft zu erzeugen? oder wie viel m3 Gas benötigt ein Schmelzofen für 1 t flüssiges Aluminium? muss ein Energiemanagementsystem jederzeit verlässliche Antworten geben können.
Der schwierigste Punkt einer jeder Bestandsaufnahme zum Energiemanagement ist die Beantwortung der Frage: Wo ist der Energieaufwand bezogen auf die betriebliche Leistung gerechtfertigt und wo kann man etwas verbessern? Im Grundsatz geht man dabei von fünf verschiedenen Varianten zur Optimierung aus:
- technisches Einsparpotential (Einsatz energieeffizienter Technologie),
- prozessuales Einsparpotential (energetisch optimierte Herstellungsprozesse),
- organisatorisches Einsparpotential (Verminderung von Verschwendung),
- Nutzung von Wärmerückgewinnung und
- Vermeidung von Wärmeverlusten durch Isolierung (z. B. Gebäude, Öfen).
Das Ergebnis des zweiten Teiles der Bestandsaufnahme ergab im Bereich der Energieerfassung ein tragfähiges Gerüst von betrieblichen Zählern für Strom (35 Zähler) und Gas (6 Zähler), welche wöchentlich zu einem Stichtermin manuell erfasst und in einer Tabelle dokumentiert wurden. Damit war für die wesentlichen Produktionsbereiche bereits eine Transparenz über den Energieeinsatz gegeben. Die Daten wurden in der Vergangenheit aber nicht zur Bildung von Energiekennzahlen, die eine Bewertung der energiebezogenen Leistung ermöglichten, herangezogen. Die dafür notwendigen Zahlen zur betrieblichen Leistung, ob „Tonne Schmelze“ oder „gegossene Tonnage“ wurden im BDE-System (Betriebsdatenerfassung) erfasst. Um geeignete Energiekennzahlen zu bilden, mussten die beiden Datenströme miteinander verknüpft werden.
Die Ermittlung von Potentialen zur energetischen Optimierung wurde in diesem Stadium des Projektes noch ohne nähere Betrachtung von Randbedingungen zur Realisierung oder wirtschaftlichen Betrachtungsweisen rein qualitativ durchgeführt. Folgende Potentiale haben sich auf den ersten Blick ergeben:
- Abwärmenutzung des Schmelzbetriebes,
- Austausch von ineffizienten Beleuchtungskörpern in der Produktion,
- Austausch von veralteten Heizsystemen (Gasstrahler) in der Produktion,
- Optimierung des Druckluftnetzes (Leitungsverluste),
- verbesserte Wärmedämmung in Teilen der älteren Gebäudesubstanz und
- Reduzierung von Verschwendung an vielen Stellen.
Diese ersten Hinweise auf potentielle Energieeffizienzmaßnahmen wurden im Rahmen der energetischen Bewertung weiter verfolgt.
Die energetische Bewertung
Die energetische (Erst-)Bewertung (Bild 5) ist eines der zentralen Themen für das aufzubauende EnMS.
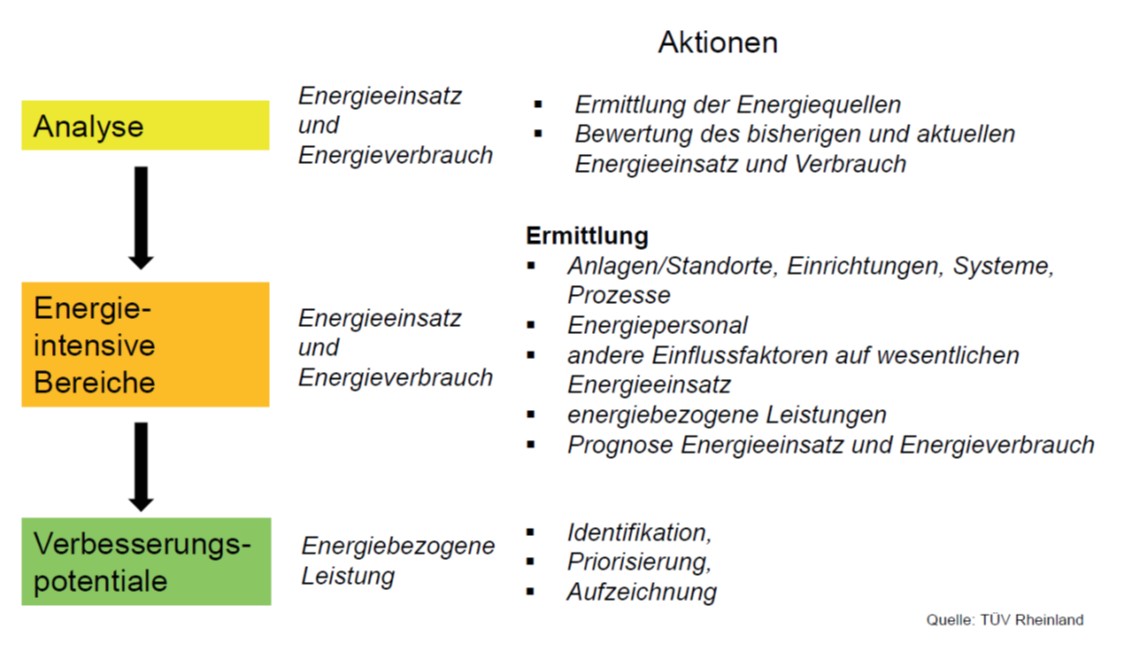
Sie setzt sich zusammen aus der
- Erfassung aller Energieverbraucher,
- Gliederung des Unternehmens in Verbrauchsbereiche mit eigener abgrenzbarer Wertschöpfung,
- Bewertung der Energieaspekte hinsichtlich ihrer Wertigkeit,
- Festlegung einer Baseline (Ausgangspunkt) als Messlatte für zukünftiger Verbesserung und
- Bildung von Energiekennzahlen zur Bewertung der energetischen Leistung für die definierten Verbrauchsbereiche.
Im ersten Schritt ist eine umfassende Erfassung aller energieverbrauchenden Maschinen, Anlagen und Einrichtungen des Unternehmens notwendig. Diese Liste wurde durch Mitarbeiter von Schött-Druckguß nach Vorgaben des Beraters erstellt. Für Strom- und Gasverbraucher wurden getrennte Listen erstellt. Im Strombereich wurden alle Aggregate mit einem Anschlusswert ab 1 KW und größer erfasst, im Gasbereiche alle Verbraucher. In Summe ergaben sich mehr als 500 Positionen. Zu jeder Position wurden dann spezifische Informationen mit Aussagefähigkeit bezüglich Energieeffizienz gesammelt. Neben dem Alter des Equipments wurden Daten wie Anschlusswert/Leistung, jährliche Betriebsstunden, Energieverbrauchsmessung, Energieeffizienzklasse/Wirkungsgrad, Möglichkeit zur Abwärmenutzung sowie weitere Informationen erfasst.
Darüber hinaus wurden zusätzliche infrastrukturelle Informationen mit Bedeutung für das EnMS erstellt oder aktualisiert:
- Bestandsplan Stromleitungsverlauf,
- Bestandsplan Druckluftnetz,
- Bestandsplan Gasnetz,
- Beleuchtungskataster und
- Energiezählerplan (Strom/Gas).
Diese Bestandspläne wurden so detailliert ausgearbeitet, dass der Weg von der Einspeisung bis zu den Großverbrauchern nachvollziehbar wurde. Das Beleuchtungskataster enthielt Information über Beleuchtungstyp, Anzahl, Anschlusswert, Energieeffizienzklasse, jährliche Nutzungsdauer etc., die notwendig waren, um eine Beurteilung über deren Energieeffizienz zu ermöglichen. Gleichzeitig wurden die Belange des Arbeitsschutzes hinsichtlich Beleuchtungsstärke darin berücksichtigt. Diese Aufgaben wurden weitgehend von den Mitarbeitern von Schött-Druckguß aufgrund ihrer speziellen Betriebskenntnisse durchgeführt.
Um eine Gliederung des Unternehmens in Energieverbrauchsbereiche vornehmen zu können, ist es notwendig, Energiedaten aus der letzten Abrechnungsperiode des Energieversorgers auf die wesentlichen Energieverbraucher im Unternehmen runterzubrechen. Bei Schött-Druckguß waren die bereits vorhandenen 41 betrieblichen Zähler da sehr hilfreich. Damit waren die Gasverbräuche aller Schmelzöfen für das Jahr 2012 bereits erfasst, welche in Summe ca. 90 % des gesamten Gasverbrauches von Schött-Druckguß ausmachten. Der Rest entfiel auf Heiz- und Sanitärzwecke durch mehrere Verbraucher, die aber keine eigene Messung hatten. Auch im elektrischen Bereich konnte über die bestehende Zählerstruktur ca. 90 % des Stroms Endverbrauchern zugeordnet werden. Zum Teil fasten diese Messungen aber Betriebsbereiche/Anlagen zusammen, in denen mehrere Einzelverbraucher oder Haustechnik wie Beleuchtung gemeinsam erfasst wurden. Damit war eine saubere Trennung von betrieblichem Strom für die Produktion und infrastrukturellem Strom z. B. für Beleuchtung, Krananlagen, etc. nicht immer gegeben. Anhand der Liste „Energieverbraucher Strom“ konnte aber über die Anschlusswerte und die Betriebsnutzungszeiten ein Schlüssel erstellt werden, welcher eine Aufteilung dieser Sammelmessung ermöglichte.
Damit waren die Voraussetzungen geschaffen, eine für das EnMS nutzbare Aufteilung des Unternehmens in Verbrauchsbereiche vorzunehmen. Bei der Einführung eines EnMS wird sich da niemals der Idealzustand sofort herstellen lassen. Zu berücksichtigen sind dabei immer der Stand der Messbarkeit von Energieverbrauchern und der zugehörigen betrieblichen Leistung. Bisherige betriebliche Gliederungen von Schött-Druckguß, wie Schmelzbetrieb, Gießerei, CNC-Fertigung etc. wurden erst einmal übernommen. Die gemessenen und auf rechnerischem Wege ermittelten Energieverbräuche des Jahres 2012 wurden diesen Verbrauchsbereichen unter Angabe des Verbrauchers zugeordnet, getrennt nach Strom und Gas. Die Daten zum Energieeinsatz und zum Verbrauch an Strom und Gas wurden dann in Energieflussbildern, sogenannten Sankey-Diagrammen, graphisch ausgewertet (Bild 6).
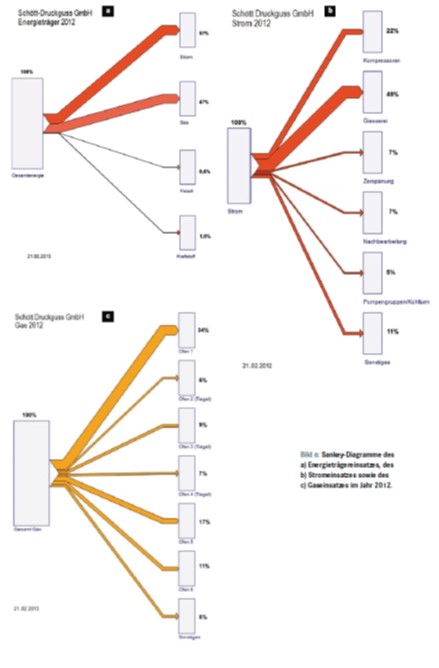
Das Ergebnis zeigte bereits die Handlungsschwerpunkte für die Differenzierung der Verbrauchsbereiche auf. Im Gasbereich konnten die Verbrauchsbereiche auf die beiden Hauptgruppen Schmelzbetrieb und Heizung begrenzt bleiben. Im Bereich Schmelzbetrieb bildete jeder Schmelzofen eine eigene Untergruppe, dem auch über die erzeugte Menge an Schmelze eine betriebliche Leistung klar zugeordnet werden konnte. Auf eine weitere Unterteilung der Hauptgruppe Heizung wurde aufgrund des geringen Gesamtverbrauches aufs erste verzichtet.
Auch die Aufteilung des Stromverbrauches in Verbrauchsbereiche konnte aus dem Sankey-Diagramm abgelesen werden. Ca. drei Viertel des Stromeinsatzes gingen in die Druckgießerei und die Drucklufterzeugung. Die Bereiche Zerspanung, Nachbearbeitung, Pumpengruppe/Kühlturm sowie Sonstiges sind da eher von untergeordneter Bedeutung. Im Hinblick auf mögliche Verbrauchsbereiche wurden die Hauptgruppen Drucklufterzeugung und Gießerei in weitere Untergruppen aufgeteilt. Im Bereich der Drucklufterzeugung wurde bis auf die fünf einzelnen Kompressoren runtergebrochen. In der Gießerei bildeten die einzelnen Druckgießzellen und Pressengruppen die kleinste Einheit. Die restlichen vier Hauptgruppen sollten vorerst noch nicht weiter aufgeteilt werden.
Da differenzierte Energiedaten aus der Vergangenheit nur für das Jahr 2011 und 2012 vorhanden waren, wurden als energetische Ausgangsbasis die Daten des Jahres 2012 ausgewählt. Die betrieblichen Leistungsdaten wurden für dieses Jahr dem BDE-System entnommen.
An diesem Punkt war die Sammlung und Analyse von Daten soweit gediehen, dass eine erste energetische Bewertung vorgenommen werden konnte. Eines der wesentlichen Ergebnisse der Bewertung ist das Erkennen von Optimierungspotential, aus dem sich Ziele für das Energiemanagementsystem ableiten lassen. Dazu war es notwendig, messbare Kriterien aufzustellen, anhand der eine energetische Bewertung vorgenommen werden konnte. Im Team wurden vier Kriterien dafür ausgewählt:
- die Bedeutung des Energieverbrauches als Anteil am Strom-/Gasgesamtverbrauch des einzelnen Verbrauchsbereiches,
- das prozentuale Einsparpotential, bezogen auf den jeweiligen Verbrauchsbereich,
- die Schwierigkeit der Umsetzbarkeit im Hinblick darauf, wie stark der (Produktions-) Prozess und die Qualität davon betroffen sind und
- die Kosten (Investitionen), die notwendig sind, die Optimierungsmaßnahmen durchzuführen.
Das Ganze wurde nach der Systematik einer ABC-Analyse (hoch, mittel, gering) bewertet (Bild 7).
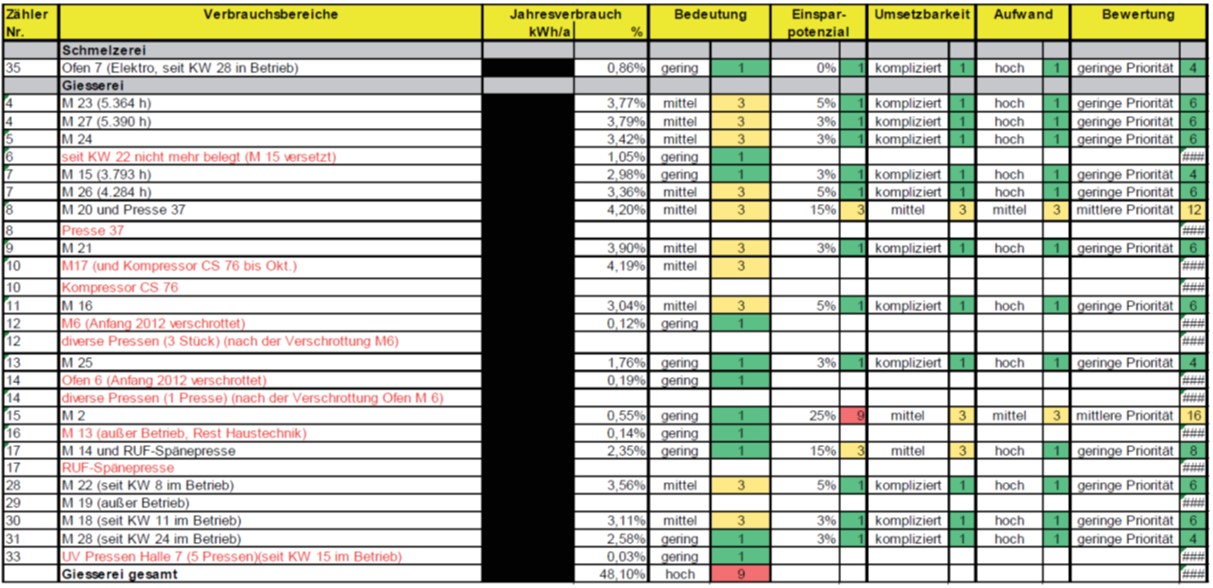
Baseline und Energiecontrolling
Um den Energieverbrauch zukünftig überwachen zu können, wurde ein Energiecontrollingsystem eingerichtet. Auf Basis der wöchentlichen Messung der Strom- und Gasverbräuche und der in diesem Zeitraum erzeugten Produktionsmengen wurden für die einzelnen Verbrauchsbereiche Kennzahlen gebildet. Die Kennzahlen dieser sogenannten „Energy Baseline“ das Jahres 2012 waren z. B. die Schmelzemenge Ofen 1 in Bezug zum Gasverbrauch des Ofens oder der Stromverbrauch der Druckgießzelle 17 in Bezug zur erzeugten Bruttodruckgussmenge. Alle Baseline-Werte basierten auf dem Jahresmittelwert, um temporäre Ereignisse statistisch auszugleichen. Denen gegenüber wurde der aktuelle Ist-Wert der Woche gestellt. Die Differenz zwischen Soll und Ist wurde über Toleranzbereiche (in % der Abweichung vom Soll-Wert) bewertet, die nach dem Ampelsystem gekennzeichnet wurden:
- Grüner Toleranzbereich – Der Energieverbrauch entspricht den Erwartungen.
- Gelber Toleranzbereich – Der Energieverbrauch über- oder unterschreitet den Planverbrauch geringfügig. Die Abweichung ist bezüglich einer Trendbetrachtung näher zu überwachen.
- Roter Toleranzbereich – Der Energieverbrauch entspricht überhaupt nicht den Erwartungen, eine unverzügliche Ursachenanalyse ist durchzuführen und Korrekturmaßnahmen sind einzuleiten.
Energiecontrolling und Baseline bilden in ihrem Zusammenspiel die Basis für die Energieeffizienzsteigerung. Ausgehend von der Baseline werden über Energieeffizienzmaßnahmen Einsparpotentiale realisiert, welche zum Prozess der kontinuierlichen Verbesserung (KVP) führen, der von anderen Managementsystemen bekannt ist.
Ergänzung der Systemdokumentation
Parallel mit der energetischen Bewertung wurde die bestehende Systemdokumentation um die Anforderungen des EnMS, gemäß den Feststellungen der Bestandsaufnahme, ergänzt. Dazu wurden Kompetenzteams gebildet, die unter der Moderation des TÜV-Beraters diese Aufgabe übernahmen.
Die Ergänzung der Systemdokumentation hatte drei wesentliche Inhalte:
- Ergänzen von bestehenden Verfahrensanweisungen aus dem Qualitäts- und Umweltmanagementsystem,
- Erstellen von neuen Verfahrensanweisungen mit Inhalten, welche nur das Energiemanagementsystem betreffen sowie
- Ergänzen des bestehenden Handbuches zum integrierten Managementsystem um energierelevante Inhalte.
Das Ergänzen bestehender Verfahren (insgesamt 10 Stück) bezog sich in der Regel auf systemrelevante Verfahren, wie interne Audits, Dokumenten- und Aufzeichnungslenkung, Rechtsvorschriften zum Energierecht, Beschaffung unter Energiegesichtspunkten sowie weitere Verfahren. An neuen Regelungen für das Energiemanagementsystem wurden benötigt: Verfahren zur Festlegung von Themen, wie der energetischen Bewertung, dem Energiecontrolling, der Energieplanung und -beschaffung sowie der Abwicklung von Investitionsvorhaben unter der Prämisse einer Energieeffizienzanalyse.
Mit der Erweiterung des Handbuches wurde auch eine Ergänzung der Qualitätsund Umweltpolitik durchgeführt. Wesentliche neue Aussagen zum Energiemanagement waren die Verpflichtung zur Verbesserung der energetischen Leistung, das Erreichen der Energieziele sowie der Erwerb von energieeffizienten Gütern.
Implementierung des EnMS
Die Einführung des Energiemanagementsystems bei Schött-Druckguß erfolgte in mehreren Schritten. Zunächst wurden aus der Energiepolitik, der energetischen Bewertung und aus den Erfahrungen des Projektes Ziele für das EnMS definiert. Neben dem strategischen Ziel der messbaren Steigerung der Energieeffizienz des Unternehmens im Rahmen einer 3-Jahres-Planung waren wesentliche Einzelziele:
- Anschaffen von energieeffizienten Motoren, Pumpen und Antrieben bei Neubeschaffung und Austausch,
- Erhöhen der Energieverbrauchstransparenz durch Installation weiterer Messstellen,
- Umstellen ausgewählter Messstellen auf eine Online-Erfassung und
- Steigerung der Abwärmenutzung im Schmelzbetrieb.
Dann wurden die betrieblichen Führungskräfte mittels mehrerer Einführungsworkshops über das neue Energiemanagementsystem informiert. Die Umsetzung der Verfahren und Regelungen des neuen EnMS in die betriebliche Praxis erfolgte im Rahmen einer Unterweisungskampagne durch die betrieblichen Führungskräfte mit Unterstützung des Projektteams. Besonderer Schwerpunkt war hier die Bewusstseinsbildung bei allen Mitarbeitern, dass jeder zur Energieeffizienz betragen kann und dass gerade die Vermeidung von Energieverschwendung eine Aufgabe eines jeden einzelnen Mitarbeiters ist.
Zur Unterstützung des Energiemanagementbeauftragten setzte die Geschäftsführung ein Energieteam ein. Es setzte sich aus betrieblichen Führungskräften zusammen, welche in ihrem Verantwortungsbereich bedeutenden Einfluss auf die energetische Leistung des Unternehmens haben. Die Aufgaben des Energieteams sind im Wesentlichen Mitwirkung beim Energiecontrolling, Umsetzungskontrolle von Maßnahmen und Zielen sowie die Identifizierung von weiteren Potentialen zur Energieeffizienzsteigerung.
Die Geschäftsführung setzte Anfang März 2013 das Energiemanagementsystem im erweiterten Managementhandbuch in Kraft und machte es damit für alle Mitarbeiter von Schött-Druckguß verbindlich.
Die Generalprobe war das im März 2013 durch die Beratungsgesellschaft durchgeführte erste interne Audit zum EnMS. Dabei wurde der Managementbeauftragte als Co-Auditor eingebunden. Die Ergebnisse des Audits wurden vom Auditorenteam in einem Auditbericht zusammengefasst. Wie bei einem neuen System zu erwarten, entsprach noch nicht alles den Normenforderungen. Es gab diverse Auditfeststellungen, welche mit Abstellmaßnahmen und Verantwortlichkeit in einem Maßnahmenplan niedergelegt wurden, der vor der Zertifizierung abgearbeitet wurde.
Aus den Ergebnissen des Bestandsaufnahmeberichts sowie dem internen Audits und daraus abgeleiteten Maßnahmen erstellte die Geschäftsführung eine erste Managementbewertung für das Energiemanagementsystem.
Der Erfolg und der Ertrag
So vorbereitet stand bei Schött-Druckguß einer Zertifizierung des neuen Energiemanagementsystems nichts mehr im Wege. Ein externes Zertifizierungsunternehmen führte Mitte März 2013 das Stufe 1-Audit (Nachweis der Zertifizierfähigkeit) durch, dessen Ergebnis zu Maßnahmen führte, welche bis zum Stufe 2-Audit abgearbeitet wurden. Ende April 2013 wurde das Stufe 2-Audit mit Erfolg durchgeführt. Schött-Druckguß besitzt nun ein zertifiziertes Energiemanagementsystem nach DIN EN ISO 50001:2011.
Aber das Zertifikat an sich und die damit verbundenen Möglichkeiten, auch zukünftig steuerliche oder umlagenbezogene Vergünstigungen zu erhalten, waren nicht der einzige Gewinn, den das Unternehmen am Ende des Projektes aus der Einführung des EnMS ziehen konnte. Die durch das neue Energiecontrolling gewonnene Transparenz über den Energieeinsatz im Unternehmen überzeugte die Führung des Unternehmens schnell davon, dass hier noch wesentliche Potentiale zur Steigerung der Wirtschaftlichkeit des Unternehmens liegen. Energie- und Kosteneffizienz sind zwei Seiten derselben Medaille – und ein gelebtes Energiemanagementsystem ist ein aktives Kostensenkungsprogramm mit Zukunft.
Dr.-Ing. Wolfgang Kallmeyer, Senior-Berater der TÜV Rheinland Consulting GmbH, Köln; Dipl.-Ing. Detlef Rissenbeck, Betriebsleiter der Schött-Druckguß GmbH, Menden.